Методика поверки «МАНОМЕТРЫ ГРУЗОПОРШНЕВЫЕ СЕРИИ Р ПРОГРАММА ИСПЫТАНИЙ В ЦЕЛЯХ УТВЕЖДЕНИЯ ТИПА» (Код не указан!)
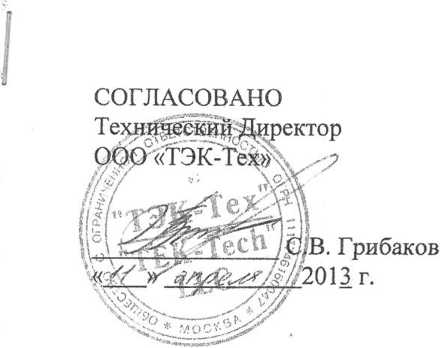
УТВЕРЖДАЮ
Руководитель ГЦИ СИ -
Зам.генералыюго директора
- Москва»
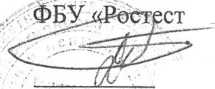
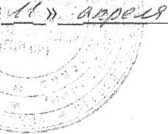
__А.С. Евдокимов 2013 г.
ПРОГРАММА ИСПЫТАНИЙ
В ЦЕЛЯХ УТВЕЖДЕНИЯ ТИПА
г. Москва
2013 г.
Настоящая программа предназначена для проведения испытаний в целях утверждения типа манометров грузопоршневых серии Р модификаций ЗОхх, 31хх, 32хх, 38хх серийного производства, изготовленных фирмой «Fluke Corporation», США (торговая марка Pressurements).
Манометры грузопоршневые серии Р (далее по тексту - манометры) предназначены для измерения и воспроизведения избыточного давления при поверки и калибровки эталонов давления в диапазоне до 250 МПа.
На испытания в целях утверждения типа представлены по одному образцу манометров Р3015 и Р3124. По результатам испытаний представленных образцов принимается решение о распространении результатов на весь тип манометров грузопоршневых серии Р.
Испытания проведены на испытательной базе ГЦИ СИ ФБУ «Ростест - Москва» и Fluke Corporation (США).
2 СОДЕРЖАНИЕ И ОБЪЁМ ИСПЫТАНИЙ-
2.1 Состав и рекомендуемая последовательность проведения испытаний должны соответствовать таблице 1.
Таблица 1
№№ п/п |
Наименование этапа испытаний |
Ссылка на пункт методики испытаний |
Сведения об эталонах и испытательном оборудование для проведения испытаний |
1 |
2 |
3 |
4 |
1 |
Оценка полноты и правильности выражения метрологических и технических характеристик средства измерений в представленной заявителем технической документации |
Рассматривают рациональность выбора нормируемых метрологических характеристик и проверяют соответствие метрологических характеристик требованиям п. 6.2.4. МИ 3290-2010 | |
2 |
Проверка внешнего вида, комплектности, маркировки и упаковки |
4.1 |
Визуально, сличение с технической документацией. |
3 |
Проверка соответствия габаритных размеров и массы |
4.2 |
Рулетка измерительная металлическая (0.. .5000) мм 2 класса; Весы электронные LP-12000S с наибольшим пределом взвешивания 12 кг 3 разряда по ГОСТ 29329-92. |
4 |
Проверка на герметичность |
4.3 |
Секундомер механический СОСпр, диапазон измерений (0...30)мин, ПГ 1с; Микроскоп отсчетный МПБ-3 с пределом измерений 6 мм, ц.д. 0,05 мм |
1 |
2 |
3 |
4 |
5 |
Определение основных метрологических характеристик |
4.4 |
Рабочий эталон ВЭТ 23-3-03 с ИПС МП-600 №13 с диапазоном измерений от 1,25 до 60 МПа, КТ 0,005; Манометр грузопоршневой СРВ5000 диапазон измерений (0,04... 10) МПа, КТ 0,005; Весы электронные ВР221 с наибольшим пределом взвешивания 220 г специального класса; Весы электронные LP-1200S с наибольшим пределом взвешивания 1,2 кг специального класса; Весы электронные LP-6200S с наибольшим пределом взвешивания 6,2 кг специального класса; Секундомер механический СОСпр, диапазон измерений (0...30)мин, ПГ 1с; Микроскоп отсчетный МПБ-3 с пределом измерений 6 мм, ц.д. 0,05 мм; Термогигрометр «ИВА-6Н», диапазон отн. влажности (0...98) %, ПГ ± 3 %; диапазон температур (0... 60) °C, ПГ±0,5 °C; Барометр БРС-1М-3, диапазон измерений (5...1100) гПа, ПГ ± 20 Па |
6 |
Испытания в упаковке на воздействие повышенной (пониженной) температуры окружающего воздуха, соответствующей условиям хранения |
4.5 |
Климатическая камера PSL-4GM с диапазонами измерения температуры (-50... +90) °C, с ПГ ± 2 °C и относительной влажности (10 ... 100)%, ПГ±3 %. Эталонные СИ по п.4.4 настоящей программы. |
7 |
Испытания на воздействия повышенной влажности |
4.6 |
Эталонные СИ по п.4.4 настоящей программы; Испытательное оборудование по п.4.6 настоящей программы. |
8 |
Испытания в упаковке на воздействие механикодинамических нагрузок, соответствующих условиям транспортирования |
4.7 |
Установка вибрационная испытательная DSC-8/PA2000/L721 с диапазоном частот от 55 до 5000 Гц и амплитудой от 0 до 7,5 мм Эталонные СИ по п.4.4 настоящей программы. |
9 |
Проверка возможности проведения поверки в соответствии с проектом НД на методику поверки |
4.8 |
Эталонные СИ по п.4.4 настоящей программы. Г |
10 |
Определение интервала между поверками |
Раздел 5 |
интервал между поверками рассчитывается в соответствии с РМГ 74-2004 |
И |
Анализ конструкции СИ |
Раздел 6 |
визуально |
-
3.1 При проведении испытаний в целях утверждения типа приборы должны быть установлены в рабочее положение с соблюдением требований безопасности изложенных в руководстве по эксплуатации.
Испытания в целях утверждения типа, если их условия не оговариваются при описании отдельных методов испытаний, следует проводить при следующих условиях:
-
- температура окружающего воздуха от 18 до 28 °C;
-
- относительная влажность от 30 до 80 %;
-
- атмосферное давление от 84 до 106,7 кПа;
-
- вибрация, тряска, удары, магнитные поля, кроме земного, влияющие на работу приборов, должны отсутствовать.
-
3.2 Требования безопасности.
Перед испытаниями в целях утверждения типа проводится проверка соблюдения условий испытаний и выполнения требований безопасности, установленных в эксплуатационной документации на средства измерений, испытательное оборудование и вспомогательную аппаратуру.
-
3.3 Требования к квалификации персонала.
К испытаниям допускаются лица, аттестованные в качестве испытателей, прошедшие инструктаж по технике безопасности, изучившие техническую документацию на средства измерений, испытательное оборудование, вспомогательную аппаратуру и настоящую программу испытаний.
4 МЕТОДЫ (МЕТОДИКА) ИСПЫТАНИЙ-
4.1 Проверка внешнего вида, комплектности, маркировки и упаковки.
Проверка внешнего вида, комплектности, маркировки и упаковки проверяется визуальным контролем.
При внешнем осмотре должно быть установлено:
-
- отсутствие механических повреждений корпуса и измерительной поршневой системы; поршень должен свободно, без затираний, вращаться в цилиндре и перемещаться вдоль оси цилиндра
-
- соответствие маркировки манометра, измерительных поршневых систем и грузов требованиям документации фирмы;
-
- соответствие маркировки транспортной тары требованиям ГОСТ 14192-96.
-
4.2 Проверка габаритных размеров и массы.
Проверка габаритных размеров манометра производится измерением с погрешностью не более 1 мм.
Массу манометра определяют взвешиванием на весах с погрешностью не более 0,1 кг.
-
4.3 Проверка на герметичность.
Проверку герметичности манометров положительного и отрицательного давления проверяют на верхнем пределе измерений положительного избыточного давления.
При указанном давлении манометр выдерживают 5 минут. Манометр считается герметичным, если изменение давления не наблюдается при скорости опускания поршня, не более 2 мм/мин (для пневматических манометров с ВПИ от 1 до 7 МПа) и 1,5 мм/мин (для гидравлических манометров с ВПИ свыше 6 МПа).
-
4.4 Определение основных метрологических характеристик.
-
4.4.1 Определение продолжительности свободного вращения поршня.
-
Продолжительность свободного вращения поршня определяют при помощи секундомера при установке поршня поверяемого манометра в рабочее положение.
Поршень манометра нагружают грузами, создавая давление равное 20% верхнего предела измерений, и приводят во вращение по ходу часовой стрелки.
За продолжительность свободного вращения поршня принимают интервал времени от момента, соответствующего начальной частоте его вращения, равной (120±10) об/мин, до полной остановки поршня. Начальную частоту вращения определяют подсчетом числа оборотов за 10 с. Для удобства подсчета между грузами следует положить полоску бумаги.
Продолжительность свободного вращения поршня приведенная к температуре 20 °C, должна быть не меньше 4 минут для ВПИ до 6 МПа и 6 минут для ВПИ свыше 6 МПа. Если температура манометра в момент измерений отличается от 20 °C, то значения продолжительности вращения необходимо привести к температуре 20 °C пересчетом по формуле
Л
Т20= Т ,
Л20
где Т20 - приведенное значение продолжительности вращения, с;
т - подсчитанное значение продолжительности вращения, с;
ц - значение динамической вязкости рабочей жидкости при измерении, Пах; т|20 - значение динамической вязкости рабочей жидкости при измерении при температуре 20 °C, Пах.
-
4.4.2 Определение скорости опускания.
Скорость опускания поршня определяют при нагрузке, соответствующей верхнему пределу измерений поверяемого манометра. При этом запорный вентиль должен быть перекрыт, а частота вращения поршня с грузами должна быть не менее 30 об/мин.
Для определения скорости опускания поршня измеряют расстояние, на которое переместился поршень за некоторый промежуток времени. Расстояние измеряют микроскопом или индикатором, интервал времени опускания поршня отсчитывают по секундомеру.
Скорость опускания поршня, приведенная к температуре 20 °C, должна быть не более 2 мм/мин (для пневматических манометров с ВПИ от 1 до 7 МПа) и 1,5 мм/мин (для гидравлических манометров с ВПИ свыше 6 МПа).
Если температура в момент измерений отличается от 20 °C, то значение скорости опускания необходимо привести к температуре 20 °C, пересчитав по формуле
П
V20= V •-------,
П20
где V20 - приведенное значение скорости опускания, мм/мин;
v - измеренное значение скорости опускания, мм/мин.
-
4.4.3 Определение порога реагирования
Порог реагирования определяют при последнем уравновешивании, т.е. при давлении, соответствующему верхнему пределу измерений манометра. При окончании уравновешивания поршень поверяемого манометра дополнительно нагружают гирями, масса которых не превышает 0,15Пов mmax (где штах - масса грузов поверяемого манометра, соответствующая верхнему пределу измерений).
Результат проверки порога реагирования считают положительным, если при помещении добавочных гирь равновесие поршней нарушается.
-
4.4.4 Определение приведенной площади поршня.
-
4.4.4.1 Приведенную площадь поршня определяют методом сличения поверяемого манометра с эталонным манометром.
-
Прямое уравновешивание с предварительным уравновешиванием масс поршней с грузоприемными устройствами и помещенных на них грузов. При условии предварительного уравновешивания нет необходимости торцы поршней располагать в одной горизонтальной плоскости.
-
4.4.4.2 При определении приведенной площади поршня должны быть выполнены следующие требования.
Поршни рабочего эталона и поверяемого манометра должны быть установлены в рабочее положение.
Взаимное положение поршней следует контролировать во время их равновесия устройством для наблюдения за положением равновесия поршней с погрешностью, не превышающей чувствительность отсчетного устройства эталонного манометра.
Измерения следует проводить при давлениях, возрастающих до верхнего предела измерений. Число точек давления должно быть не менее 9.
Погрешность определения действительных значений масс поршня с грузоприемным устройством и грузов поверяемого манометра при определении приведенной площади поршня не должны превышать 0,1 5ПОв.
Примечания:
-
1 При отклонении действительных значений массы груздв от номинальных значений, не превышающем значения допускаемой погрешности определения массы (т.е. 0,1 6Пов), в протокол поверки записывают их номинальную массу. В противном случае учитывают действительное значение массы грузов.
-
2 При определении метрологических характеристик не допускается:
-снимать грузы с манометра, верхние пределы измерений которых превышают 0,6 МПа, когда поршень находится в крайнем верхнем положении
-открывать вентиль устройства для создания давления, предназначенный для отключения поверяемого манометра, если давление в прессовой части превышает сумму значений давлений грузов, находящихся на грузоприемном устройстве.
Для уравновешивания поршней на грузоприемные устройства поверяемого манометра и рабочего эталона помещают грузы соответствующей массы, необходимой для создания требуемого значения давления. При помощи устройства для создания давления поршни устанавливают в рабочее положение, а затем приводят их во вращение с частотой не менее 30 об/мин. Если при этом равновесие поршней отсутствует, то поднимающийся поршень дополнительно нагружают гирями общего назначения до достижения равновесия.
Равновесие считают достигнутым, если не наблюдается изменение положения поршней относительно друг друга, т.е. скорость их опускания одинакова.
При определении приведенной площади поршня с предварительным уравновешиванием перед началом измерений проводят предварительное уравновешивание поршней эталонного и поверяемого манометров путем накладывания тарировочных грузов, которые затем не снимают с грузоприемных устройств.
Суммарные массы поршней с грузоприемными устройствами и грузов, помещенных при предварительном уравновешивании, при определении приведенной площади не измеряют и не учитывают.
Отношение масс А; при каждом отдельном уравновешивании поршней определяют по формуле
ПЗпов ri Qi Aj= ------------'
ГПэ ri
а среднее отношение масс А - по формуле
п
S ГПпов ri ' Qi
i=l
А = ----------
n
Zj Шэ ri
i=l
где тэ п и mn0B п - действительная масса грузов и гирь при i-м уравновешивании, нагружаемых на эталонный и поверяемый манометры соответственно, кг;
qi - поправочный коэффициент, учитывающий влияние температуры и
деформации на показания манометров, определяемый по формуле:
Ц; — 1 + (ОЦэ + С^2э)’^э1 20 С) — (Щпов + С^2пов)’(^пов4— 20 С)+(РЭ — рпов)'Р| ?
Г
где сс1э и а2э - температурные коэффициенты линейного расширения материалов цилиндра и поршня эталонного манометра, °C'1;
аыов и а2пов - температурные коэффициенты линейного расширения материалов цилиндра и поршня поверяемого манометра, °C’1;
tnoei и t3i - температура поверяемого и эталонного манометров соответственно при i-м уравновешивании, °C'1;
Pi - номинальное давление при i-м уравновешивании;
Рэ и рпов - коэффициенты деформации поршня и цилиндра от давления эталонного и поверяемого манометров соответственно, Па’1.
Коэффициент деформации р вычисляют по формуле
1 Е1 R2+r2
р= ---- [ 3И1-1 + — (------- + ц) ],
2Ei Е R2-?
где Е и Ei - модули упругости материалов цилиндра и поршня (модуль Юнга), Па ц и pi - коэффициенты поперечного сжатия материала цилиндра и поршня (коэффициент Пуассона);
R - внешний радиус цилиндра, м;
г - внутренний радиус цилиндра, принимаемый равным радиусу поршня, м.
Для манометров с поршнями и цилиндрами, изготовленными из одного материала эта формула принимает вид:
1 г2
Р = — ( 2М- +-------) ,
Е R2-r2
Поправочным коэффициентом q; пренебрегают, если его значение не превышает 10% предела допускаемой погрешности поверяемого манометра.
Приведенную площадь поверяемого манометра F определяют по формуле
F = F3 ’ А
где F3 - значение приведенной площади эталонного манометра, м2.
Для оценки точности полученных значений приведенной площади поршня высчитывают среднее квадратическое отклонение Sf результата определения приведенной площади поршня в последовательности, приведенной ниже.
При каждом значении давления определяют разность отношений масс 8 по формуле
8 = А{ - А
Среднее квадратическое отклонение определяют по формуле
п
S32i=i sF = -V (----------) Г
п- 1
Среднее квадратическое отклонение результата определения приведенной площади поршня не должно превышать 0,0014% номинального значения приведенной площади поршня для манометра класса точности 0,008 и 0,0026% - для манометра класса точности 0,015.
-
4.4.6 Проверка соответствия действительных значений массы грузов расчетным или номинальным значениям.
Масса грузов и масса поршня с грузоприемным устройством должны быть подогнаны в зависимости от назначения под номинальное значение массы или под номинальное значение давления.
Отклонение действительных значений массы поршня с грузоприемным устройством и массы каждого груза, подогнанных под номинальное значение массы, от номинальных значений массы недолжно превышать 0,26ПОВ.
Масса поршня с грузоприемным устройством и масса каждого груза, подогнанных под номинальное значение давления, должны быть рассчитаны с учетом полученного нового значения приведенной площади поршня по формулам, приведенным в ГОСТ 8291-83.
Отклонение действительных значений массы поршня с грузоприемным устройством и массы каждого груза от расчетных значений не должно превышать 0,26Пов-
Действительные значения массы грузов, поршня с грузоприемным устройством и дополнительных грузов проверяют взвешиванием на образцовых весах с применением образцовых гирь по методике, изложенной в ГОСТ 8291-83.
-
4.5 Испытания в упаковке на воздействие повышенной (пониженной) температуры окружающего воздуха, соответствующей условиям хранения.
-
4.5.1 Прибор в упаковке помещают в климатическую камеру при температуре указанной в разделе 3 настоящей программы, повышают температуру в камере до плюс 50°С, с отклонением ±3 °C, выдерживают его при этой температуре не менее 6 часов, затем понижают температуру в камере до значения указанного в разделе 3 настоящей программы и после выдержки при этой температуре не менее 12 часов определяют основные метрологические характеристики по п.4.4 настоящей программы.
-
4.5.2 Прибор в упаковке помещают в климатическую камеру при температуре указанной в разделе 3 настоящей программы, понижают температуру в камере до минус 10 °C, с отклонением ±3 °C, выдерживают прибор при этой температуре не менее 6 часов, затем повышают температуру в камере до значения указанного в разделе 3 настоящей программы и после выдержки при этой температуре не менее 12 часов определяют основные метрологические характеристики по п.4.4 настоящей программы.
-
Прибор считается выдержавшим испытание, если после окончания испытаний отсутствуют механические повреждения, а значения основных метрологических характеристики соответствуют заявленным.
-
4.6 Испытания на воздействие повышенной влажности окружающего воздуха.
Прибор помещают в камеру влажности при температуре указанной в разделе 3 настоящей программы, повышают температуру в камере до +30 °C, с отклонением ±3 °C, выдерживают прибор при этой температуре не менее 2 часов, затем повышают относительную влажность до 80 % и выдерживают в течение 48 часов. После окончания испытаний прибор выдерживают в нормальных условиях не менее 6 часов и определяют основные метрологические характеристики по п.4.4 настоящей программы.
Прибор считается выдержавшим испытание, если после окончания испытаний значения основных метрологических характеристики соответствуют заявленным, на его внешних и внутренних деталях не обнаружено следов коррозии, отслаивания и повреждения защитного покрытия.
-
4.7 Испытания в упаковке на воздействие механико-динамических нагрузок, соответствующих условиям транспортирования.
Испытание на воздействия механико-динамических нагрузок производят в течение 2 часов на стенде, создающем тряску в вертикальном направлении с частотой 120 ударов в минуту. Прибор в упаковке укрепляют на стенде без наружной амортизации в положении, определенном надписью «ВВЕРХ». После снятия прибора со стенда определяют его основную погрешность по п.4.4 настоящей программы.
Прибор считается выдержавшим испытания, если после окончания испытаний отсутствуют механические повреждения, а значения основных метрологических характеристик соответствуют заявленным.
-
4.8 Проверка возможности проведения поверки в соответствии с проектом НД на методику поверки.
В ходе проведения испытаний в целях утверждения типа калибраторов должна быть опробована МИ 2429-97 «ГСИ. Манометры грузопоршневые. Метрологические и технические характеристики. Виды метрологического контроля» (MP МОЗМ №110). После чего выносится решение о возможности ее применения.
5 ОПРЕДЕЛЕНИЕ ИНТЕРВАЛА МЕЖДУ ПОВЕРКАМИРекомендованный интервал между поверками рассчитывается в соответствии с РМГ 74-2004 «ГСИ. Методы определения межповерочных и межкалибровочных интервалов средств измерений», с учетом показателей надежности, испытуемого прибора, исходя из риска их использования с погрешностью, превышающей допускаемую, и с учетом данных по результатам периодической поверки отечественных и зарубежных аналогов. Результаты расчета интервала между поверками заносят в протокол.
6 АНАЛИЗ КОНСТРУКЦИИ СРЕДСТВА ИЗМЕРЕНИЙПроводится анализ конструкции манометров грузопоршневых серии Р. Проверяется соответствие манометров документации фирмы. Результаты заносят в протокол.
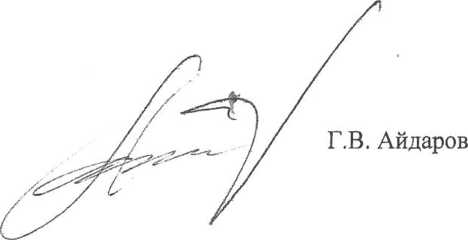
Начальник лаборатории поверки и испытаний СИ давления и вакуума
10