Методика поверки «СТЕНДЫ АВТОДИАГНОСТИЧЕСКИЕ ИЗМЕРИТЕЛЬНЫЕ РОЛИКОВЫЕ МНОГОФУНКЦИОНАЛЬНЫЕ X-ROAD» (МП АПМ 62-15)
УТВЕРЖДАЮ директор
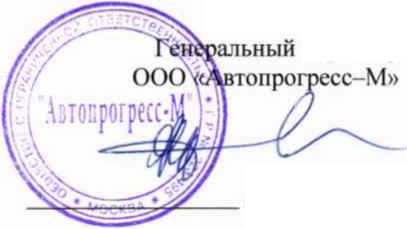
А. С. Никитин
« /J »________________2015 г.
СТЕНДЫ АВТОДИАГНОСТИЧЕСКИЕ ИЗМЕРИТЕЛЬНЫЕ РОЛИКОВЫЕ МНОГОФУНКЦИОНАЛЬНЫЕ X-ROADМЕТОДИКА ПОВЕРКИ
МП АПМ 62-15
гGBIQSг. Москва
2015 г.
Настоящая методика поверки распространяется на стенды автодиагностические измерительные роликовые многофункциональные x-road, производства «Durr Assembly Products GmbH», Германия и «Schenck Shanghai Machinery Co.Ltd» КНР (далее - стенды) и устанавливает методику их первичной и периодической поверки.
Интервал между периодическими поверками -1 год.
1. Операции поверки
При проведении поверки должны выполняться операции, указанные в таблице 1.
Таблица 1
Наименование этапа поверки |
№ пункта документа по поверке | |
1 |
Внешний осмотр, проверка маркировки и комплектности |
7.1 |
2 |
Опробование, проверка работоспособности функциональных режимов и диапазонов измерений:
|
7.2 |
3 |
Определение средних диаметров ходовых роликов |
7.3 |
4 |
Идентификация программного обеспечения |
7.4 |
5 |
Определение метрологических характеристик |
7.5 |
5.1 |
Определение приведенной погрешности измерений тангенциальной составляющей силы, прикладываемой к поверхности ходовых роликов |
7.5.1 |
5.2 |
Определение приведённой погрешности измерений усилий, прикладываемых к органам управления тормозными системами |
7.5.2 |
5.3 |
Определение абсолютной погрешности измерений скорости движения автомобиля |
7.5.3 |
2. Средства поверки
При проведении поверки должны применяться эталоны и вспомогательные средства, приведенные в таблице 2.
Таблица 1
№ пункта документа по поверке |
Наименование эталонов, вспомогательных средств поверки и их основные метрологические и технические характеристики |
7.3 |
Рулетка измерительная металлическая (0-^-5000) мм, кл 3, ГОСТ 7502-98 |
7.5.1 |
Датчик крутящего момента силы, тип Т4А (per. № 50770-12), ±1 кН-м, ПГ ±0,1 % |
7.5.2 |
Весы неавтоматического действия по ГОСТ OIML R 76-1-2011, (per. № 59261-14), КТ «высокий», max <20 кг, погрешность измерений не более ±1 г |
7.5.3 |
Тахометр электронный, тип АТТ 6000 (per. № 27264-11), (5 - 99999) мин'1; ПГ ±0,1 %±1 |
Допускается применять другие средства поверки, обеспечивающие определение метрологических характеристик с точностью, удовлетворяющей требованиям настоящей методике поверки.
3. Требования к квалификации поверителейК проведению поверки допускаются лица, изучившие эксплуатационные документы на стенды автодиагностические измерительные роликовые многофункциональные x-road, имеющие достаточные знания и опыт работы с ними.
4. Требования безопасности-
4.1. Перед проведением поверки следует изучить техническое описание и инструкцию по эксплуатации на поверяемый стенд и приборы, применяемые при поверке.
-
4.2. К поверке допускаются лица, прошедшие инструктаж по технике безопасности при работе на электроустановках.
-
4.3. Перед проведением поверки должны быть выполнены следующие работы:
-
- все детали стенда и средств поверки должны быть очищены от пыли и грязи;
-
- поверяемый стенд и приборы, участвующие в поверке должны быть заземлены.
При проведении поверки должны соблюдаться следующие нормальные условия измерений:
-
- температура окружающей среды, °C 20±5;
-
- относительная влажность воздуха, % не более (60±20);
-
- атмосферное давление, кПа (мм рт. ст.) 84,0106,7 (630..800).
Перед проведением поверки должны быть выполнены следующие подготовительные работы:
-
- проверить наличие действующих свидетельств о поверке на средства поверки;
-
- стенд должен быть установлен в соответствии с инструкцией по установке изготовителя;
-
- стенд и средства поверки привести в рабочее состояние в соответствии с их эксплуатационной документацией;
-
- стенд и средства поверки должны быть выдержан в испытательном помещении не менее 1ч;
-
- для поверяемого образца стенда должна быть выполнена процедура автокалибровки измерительных датчиков согласно подразделу «Калибровочный режим» руководства по эксплуатации стенда. Автокалибровка осуществляется в следующей последовательности:
-
• передний левый узел асинхронного двигателя с ходовыми роликами;
-
• передний правый узел асинхронного двигателя с ходовыми роликами;
-
• задний левый узел асинхронного двигателя с ходовыми роликами;
-
• задний правый узел асинхронного двигателя с ходовыми роликами.
Стенд считается готовым к проведению поверки, если все четыре графических зависимости, полученные по результатам проведенной автокалибровки линейны во всем измерительном диапазоне и близки друг к другу по абсолютным величинам.
-
7. Проведение поверки
При внешнем осмотре должно быть установлено соответствие стенда следующим требованиям:
-
- наличие маркировки (наименование или товарный знак фирмы-изготовителя, тип и заводской номер);
-
- комплектность стенда должна соответствовать руководству по эксплуатации;
-
- отсутствие механических повреждений и коррозии корпуса, рабочих поверхностей ходовых роликов, и других конструктивных элементов стенда;
-
- отсутствие механических повреждений и загрязнений сигнальных индикаторов, экрана дисплея, а также других повреждений, затрудняющих отсчет показаний и влияющих на их точность;
-
- наличие четких надписей и отметок на органах управления.
-
7.2. Опробование, проверка работоспособности функциональных режимов и диапазонов измерений: тормозной силы, усилий, прикладываемых к органам управления тормозными системами, скорости движения.
При опробовании должно быть установлено соответствие стенда следующим требованиям:
-
- работоспособность всех функциональных режимов;
-
- диапазоны измерений: тангенциальной составляющей силы, прикладываемой к поверхности ходовых роликов, усилий, прикладываемых к органам управления тормозными системами, скорости движения должны соответствовать эксплуатационной документации на стенд.
Определение средних диаметров ходовых роликов осуществляется в следующей последовательности:
-
- отметить точки измерений на поверхности роликов фломастером. Для этого фломастер на выбранной точке фиксируется посредством штатива с магнитным держателем. Ролик медленно вращается вручную, так чтобы фломастер вёл одну линию вокруг окружности ролика;
-
- измерить с помощью рулетки измерительной металлической диаметры dl, d2 и d3. Измерения проводятся рулеткой на двух ходовых роликах по одному из каждой пары. Точки, в которых по длине ролика, следует измерять длины окружностей и рассчитывать диаметры dl, d2 и d3, выбираются в соответствии с рис. 1. Результаты измерений диаметров dl, d2 и d3 для каждого ходового ролика заносятся в протокол поверки.
/
•ХЗ |
S’ | ||
J -0,25 i >.51 | |||
Z, 0,751 | |||
Рис. 1.
Точки измерений для di, d2 и d3
рассчитать для каждого исследуемого ролика эффективный диаметр ролика deff и средний диаметр ролика dm согласно следующим уравнениям:
<7cff = 0,1 d\ + 0,8 di +0,1 di
dm — deff - Vrau (mm)
где: rrau - высота неровностей профиля (за величину высоты
неровностей профиля принимается удвоенная усредненная высота неровностей профиля)
Высота неровностей профиля указывается в технической документации на стенд и зависит от наличия покрытия и характеристик материала покрытия ходовых роликов.
7.4. Идентификация программного обеспеченияИдентификационные данные программного обеспечения (далее - ПО) должны соответствовать данным, приведённым в таблице 3
Таблица 3.
Идентификационное наименование программного обеспечения |
x-line |
Номер версии (идентификационный номер) программного обеспечения, не ниже |
3.1.0.0 |
Идентификационные данные ПО могут быть получены следующим путем:
-
- включить ПК или программируемый контроллер (SPS) стенда;
-
- запустить ПО «х-Ипе»;
-
- выбрать вкладку главного меню «Help» и далее во всплывшем меню выбрать пункт «Info about eabappOl»;
-
- на экран будет выведена информация о наименование и номер версии ПО.
-
7.5.1. Определение приведенной погрешности измерений тангенциальной составляющей силы, прикладываемой к поверхности ходовых роликов.
Определение приведенной погрешности измерений тангенциальной составляющей силы, прикладываемой к поверхности ходовых роликов в ходе проведения поверки проводится последовательно на каждом из четырех ходовых роликов.
При определении приведенной погрешности измерений тангенциальной составляющей силы, прикладываемой к поверхности ходовых роликов необходимо:
- используя экранное меню Рис. 2, выбрать калибровочную функцию «Калиб. усил. торм. 4 двиг.». Выбор режима осуществляется при помощи кнопки [Т1], а активация режима - кнопки [Т2] (нижние кнопки правых функциональных клавиш на мониторе);
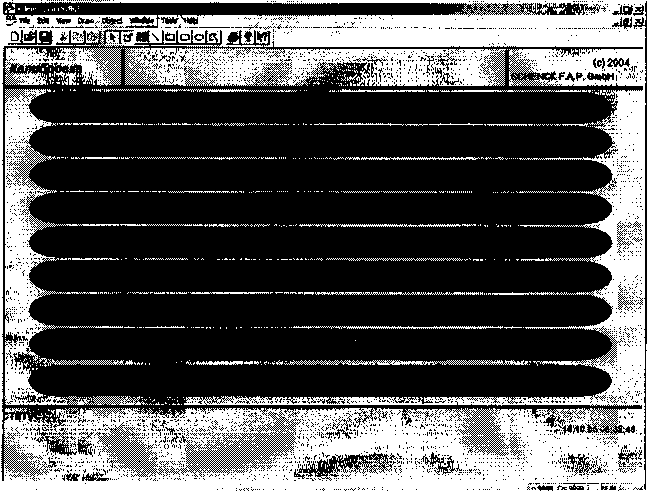
Рис. 2 Экранное меню «Калибровка»
перед испытаниями убедитесь, что стенд находятся в выключенном состоянии. В этом случае кодовый выключатель «Ролики укрыты» находится в положении «О»;
после выбора этой функции в диалоговом окне «Главное меню выбора калибровки» на мониторе открывается диалоговое окно «Выбор двигателя» (Рис. 3);
ш «и он* смм «ым н* ъ* eaii . • . |
j г-ли | |
ВЫБР.ДВИГ. |
Цвиг. Спер.Спр.

Цдин. выбор
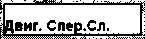
|двиг. Сзад.Сл
gQ
мм
Рис. 3. Выбор двигателя при поверке.
для выбора калибруемого двигателя используется соответствующая функциональная кнопка на мониторе;
следующее диалоговое окно на мониторе системы управления предлагает оператору установить измерительное устройство с датчиком крутящего момента силы. Внешний вид измерительного устройства с датчиком крутящего момента силы и набор калибровочных приспособлений приведен на рисунке 4;
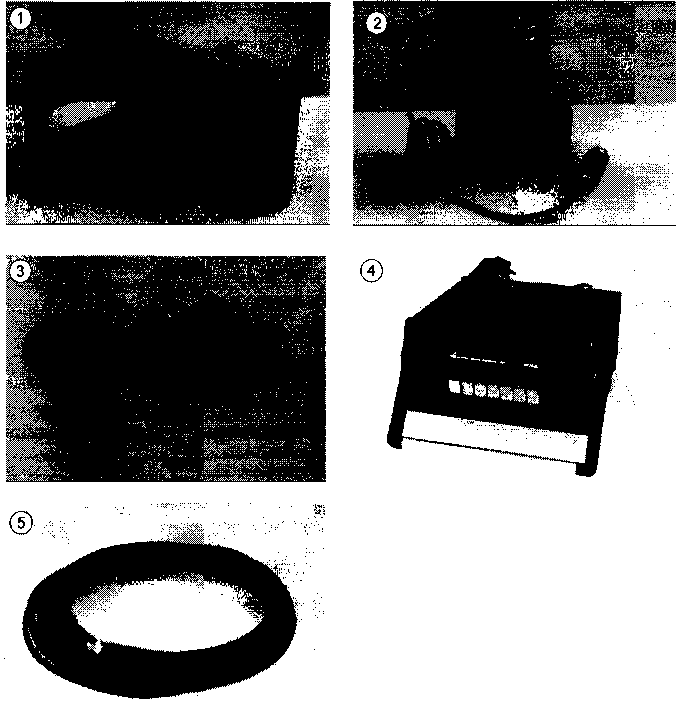
Рис. 4. Компоненты измерительного устройства и калибровочных приспособлений
-
1. держатель;
-
2. адаптер с датчиком крутящего момента силы;
-
3. соединительный элемент со стопорной шайбой;
-
4. измерительный усилитель;
-
5. соединительный кабель;
- установить датчик крутящего момента силы на поверяемый двигатель стенда, используя калибровочные приспособления, как показано на рисунках 4 - 6 в следующей последовательности:
• снять защитную крышку ременной передачи между двигателем и 1-м роликом;
• установить на вал двигателя адаптер с датчиком крутящего момента
силы (Рис. 5);
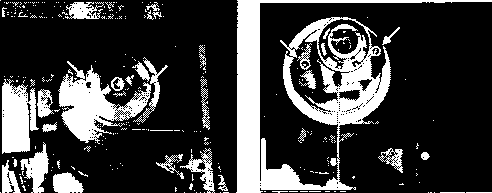
Рис. 5: Установка адаптера с датчиком крутящего момента силы.
-
• установить на адаптер соединительный элемент;
-
• установить на соединительный элемент держатель и болтами привернуть его к несущей раме (Рис. 6);
Рис. 6. Установка соединительного элемента, установка и крепеж держателя
• зафиксировать держатель со стопорной шайбой и затянуть болты (Рис. 7);
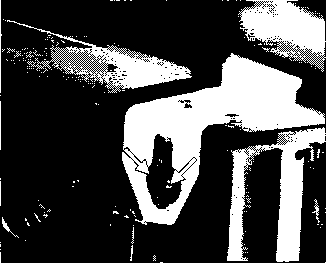
Рис. 7: Установка стопорной шайбы
-
• при помощи соединительного кабеля подключить датчик измерения крутящего момента к измерительному усилителю;
-
• с помощью соединительного кабеля подключить измерительный усилитель к последовательному интерфейсу стенда (окно меню «Электросхема»);
-
• включить и обнулить измерительный усилитель.
используя экран монитора приборной стойки стенда считать показания измеренных величин тангенциальной составляющей силы, прикладываемой к поверхности ходовых роликов, в заданных точках диапазона измерений. Конкретные значения величин тангенциальной составляющей силы, прикладываемой к поверхности ходовых роликов, выбираются заранее, программно. Эти значения принимаются за действительные значения поверяемой величины Рдейст при расчетах пределов допускаемой приведенной погрешности измерений тангенциальной составляющей силы, прикладываемой к поверхности ходовых роликов.
рассчитать измеренные величины тангенциальной составляющей силы, прикладываемой к поверхности ходовых роликов в соответствии с выражением:
Fh3m= М i(g) /г
где: М - момент на валу асинхронного двигателя, измеренный с
помощью датчика крутящего момента Т4А (или аналогичного), Н м;
i(g) - передаточное число зубчато-ремённого соединения двигателя ходовых роликов (указано в эксплуатационной документации на каждый стенд);
г - радиус ходового ролика в единицах - м;
FH3m - тангенциальная составляющая силы на поверхности ходового ролика, Н.
-
- выполнить в каждой выбранной точке диапазона измерений не менее пяти измерений;
-
- в каждой точке рассчитать приведенную погрешность измерений тангенциальной составляющей силы, прикладываемой к поверхности ходовых роликов по формулам (в зависимости от модификации):
A. =FH3M -Рдейст х100Го/о1 или д =5^!_^Lx100[%1
1 3000 L J 1 3700 L J
или
Д = £изм -рДейс£х100Го/о1 или Д = FH3M 'РДейст х100Го/1
‘ 4000 1 J ’ 4500 1 J
или
Д = go» - Рдейст х J 00 го/о] или д ризм -Рдейс-г, у j Q() Го/1
1 6000 L J 1 10000 L J
или
Д = Fh3m ~Рдейст х100Го/о1
1 25000 L J
-
- за окончательный результат приведенной погрешности измерений тангенциальной составляющей силы принять наибольшее значение результатов всех расчетов;
-
- после завершения испытаний на выбранном блоке ходовых роликов перед проведением операций поверки на следующем блоке ходовых роликов стенда, снять измерительное устройство с датчиком крутящего момента силы с поверенного блока ходовых роликов;
-
- провести процедуру поверки для остальных блоков ходовых роликов стенда в последовательности указанной в пункте 6 настоящей методики поверки.
Приведенная погрешность измерений тангенциальной составляющей силы, прикладываемой к поверхности ходовых роликов не должна превышать ±1,0%.
В качестве альтернативы может использоваться датчик крутящего момента T10F (или аналогичный), который устанавливается на ходовом ролике.
-
7.5.2. Определение приведённой погрешности измерений усилий, прикладываемых к органам управления тормозными системами.
-
7.5.2.1. Определение приведённой погрешности измерений усилий, прикладываемых к органам управления ножной тормозной системой.
-
При определении приведенной погрешности измерений усилий, прикладываемых к органам управления ножной тормозной системой, датчик усилия установить в силонажимное приспособление. Внешний вид приспособления с установленным датчиком и грузами контрольными приведены на Рисунке 8. Поверка осуществляется с помощью весов не автоматического действия по ГОСТ OIML R 76-1-2011, класс точности высокий, Мтах <20 кг, погрешность измерений не более ±1 г и грузов контрольных из комплекта поставки в следующей последовательности:
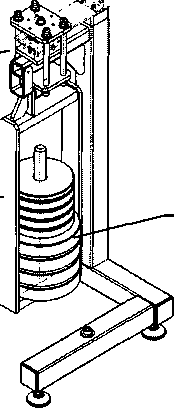
Рис. 8. Поверка силоизмерительного датчика. (1 - датчик усилия; 2 - силонажимное приспособление; 3 - контрольные грузы)
выполнить юстировку точки нуля на измерительном усилителе устройства для измерений усилий, прикладываемых к органам управления ножной тормозной системой;
устанавливать на столе держателя силонажимного приспособления (Рис. 8) наборы из грузов контрольных. Массу грузов контрольных (Мдейст) определять путем прямого взвешивания с помощью весов не автоматического действия по ГОСТ OIML R 76-1-2011. В ходе проведения поверки проверяется линейность тензометрического датчика. Результаты измерений заносятся в протокол при нагружении датчика грузами массой от 10 до 100 кг. Сначала устанавливается диск массой 10 кг, затем масса увеличивается с приращением 10 кг. Измерительный усилитель отрегулирован на индикацию прилагаемой массы в килограммах;
в каждой поверяемой точке диапазона измерений выполнить не менее 10 измерений (М ИЗм),
результаты измерений обработать в соответствии с выражением:

z 100 L J
за окончательный результат приведенной погрешности измерений усилий, прикладываемых к органам управления ножной тормозной системой принять наибольшее значение результатов всех расчетов
Результаты поверки устройства для измерений усилий, прикладываемых к органам управления ножной тормозной системой считаются положительными, если приведённая погрешность измерений усилий, прикладываемых к органам управления ножной тормозной системой не превышает величин ±1%.
-
7.5.2.2. Определение приведённой погрешности измерений усилий, прикладываемых к органам управления ручной тормозной системой.
При определении приведенной погрешности измерений усилий, прикладываемых к органам управления ручной тормозной системой датчик усилия установить в силонажимное приспособление. Внешний вид приспособления с установленным датчиком и грузами контрольными приведены на Рисунке 9. Поверка осуществляется с помощью весов не автоматического действия по ГОСТ OIML R 76-1-2011, класс точности высокий, Мтах <20 кг, погрешность измерений не более ±1 г и грузов контрольных из комплекта поставки в следующей последовательности:
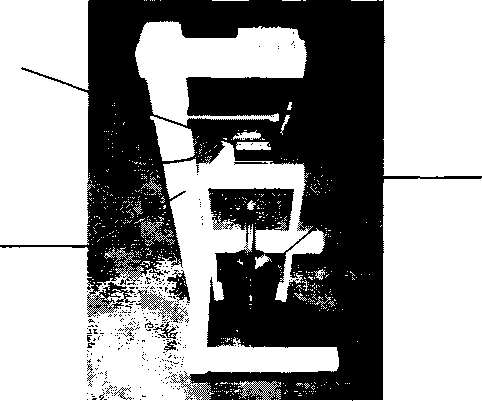
Рисунок 9. Поверка силоизмерительного датчика. (1 - поверяемый датчик; 2 -силонажимное приспособление; 3 - набор контрольных грузов)
выполнить юстировку точки нуля на измерительном усилителе устройства для измерений усилий, прикладываемых к органам управления ручной тормозной системой;
снять защиту с датчика для измерений усилий, прикладываемых к органам управления ручной тормозной системой;
устанавливать на столе держателя силонажимного приспособления (Рис. 9) наборы из грузов контрольных. Массу грузов контрольных (Мдейст) определять путем прямого взвешивания с помощью весов не автоматического действия по ГОСТ OIML R 76-1-2011. В ходе проведения поверки проверяется линейность датчика для измерений усилий, прикладываемых к органам управления ручной тормозной системой. Результаты измерений заносятся в протокол при нагружении датчика устройства для измерений усилий, прикладываемых к органам управления ручной тормозной системой грузами массой от 5 до 50 кг. Сначала устанавливается диск массой 5 кг, затем масса увеличивается с приращением 10 кг. Измерительный усилитель отрегулирован на индикацию прилагаемой массы в килограммах;
в каждой поверяемой точке диапазона измерений выполнить не менее 10 измерений (М изм)?
результаты измерений обработать в соответствии с выражением:
д = МиЗМ - Мдейст_ 1 о() Г 3
3 50 L J
за окончательный результат приведенной погрешности измерений усилий, прикладываемых к органам управления ручной тормозной системой принять наибольшее значение результатов всех расчетов
Результаты поверки устройства для измерений усилий, прикладываемых к органам управления ручной тормозной системой считаются положительными, если приведенная погрешность измерений усилий, прикладываемых к органам управления ножной тормозной системой не превышает величины ±1%.
7.5.3. Определение абсолютной погрешности измерений скорости движения автомобиля.
Скорость движения автомобиля определяется на основе расчетов диаметра роликов или длины окружности роликов.
Измерение скорости должно проводиться на тех же ходовых роликах, на которых измерялся диаметр. На выбранном для поверки ролике должна иметься маркировка, которая может быть распознана ручным тахометром. При проведении поверки скорость движения автомобиля на роликах устанавливается с клавиатуры управления стендом в диапазоне от О км/ч до 200 км/ч (шаг установки скорости 20 км/ч). Последовательность определения приведенной абсолютной погрешности измерений скорости движения автомобиля на каждой паре ходовых роликов должна быть той же, что и при проведении процедуры поверки силоизмерительной цепи.
Для расчета абсолютной погрешности измерений скорости движения автомобиля необходимо выполнить следующие операции:
-
- включить ходовые ролики стенда с одной из выбранных скоростей движения автомобиля Уизм;
-
- удерживая тахометр вертикально, направит излучатель тахометра на область ролика, где нанесена маркировочная метка. При этом необходимо добиться устойчивых показаний величины оборотов ролика п на дисплее тахометра. Результаты измерений числа оборотов каждой пары ходовых роликов заносятся в протокол поверки;
-
- в каждой выбранной поверяемой точке диапазона, измерения повторить не менее пяти раз;
-
- по результатам измерений числа оборотов ролика п и среднего диаметра ролика dm рассчитать скорость автомобиля Удейств согласно следующей формуле:
Удейств = ЛхбтХПх6х10’5
КМ
ч
- рассчитать абсолютную погрешность измерений скорости движения автомобиля Дг по формуле:
^4 * изм * деист ’
где Уизм - выбранная скорость движения ходовых ролики стенда [км/ч];
Удейст - рассчитанная скорость движения ходовых ролики стенда [км/ч];
За окончательный результат абсолютной погрешности измерений скорости движения автомобиля принять величину наибольшего значения Дг, по обработанным результатам всех выполненных измерений.
Абсолютная погрешность измерений скорости движения автомобиля не должны превышать ±1 км/ч
8. Оформление результатов поверки-
8.1. Результаты поверки оформляются протоколом, составленным в виде сводной таблицы результатов поверки по каждому пункту раздела 7 настоящей методики поверки с указанием предельных числовых значений результатов измерений и их оценки по сравнению с предъявленными требованиями.
-
8.2. При положительных результатах поверки стенд признается годным к применению и на него выдается свидетельство о поверке установленной формы.
Знак поверки наносится на свидетельство о поверке в виде наклейки и (или) поверительного клейма.
-
8.3. При отрицательных результатах поверки, стенд признается непригодным к применению и на него выдается извещение о непригодности установленной формы с указанием основных причин.
Инженер
ООО «Автопрогресс-М»
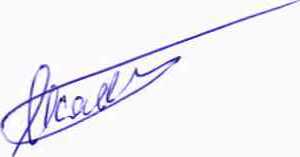
Исаев Е.В.
4. Идентификация программного обеспечения
Идентификационное наименование программного обеспечения | |
Номер версии (идентификационный номер) программного обеспечения, не ниже |
Блок передних ходовых роликов
R (радиус роликов) _______мм
I (передаточное число) _______
Задаваемое значение, Н |
Измеренное значение, Н |
Действительное значение, Н |
Абсолютная погрешность, Н |
Приведенная погрешность, % |
Максимальное значение приведенной погрешности: % | ||||
Пределы допускаемой приведенной погрешности измерений тангенциальной составляющей силы, прикладываемой к поверхности ходовых роликов в соответствии с техническими характеристиками: ± % |
Блок задних ходовых роликов
R (радиус роликов):_______мм
I (передаточное число):_________
Задаваемое значение, Н |
Измеренное значение, Н |
Действительное значение, Н |
Абсолютная погрешность, Н |
Приведенная погрешность, % |
Максимальное значение приведенной погрешности: % | ||||
Пределы допускаемой приведенной погрешности измерений тангенциальной составляющей силы, прикладываемой к поверхности ходовых роликов в соответствии с техническими характеристиками: ± % |
Измерение усилий на органе управления ножной тормозной системой
Задаваемое значение, Н |
Измеренное значение, Н |
Действительное значение, Н |
Абсолютная погрешность, Н |
Приведенная погрешность, % |
Максимальное значение приведенной погрешности: % | ||||
Пределы допускаемой приведенной погрешности измерений усилий на органе управления ножной тормозной системой в соответствии с техническими характеристиками: ± % |
Измерение усилий на органе управления ручной тормозной системой
Задаваемое значение, Н |
Измеренное значение, Н |
Действительное значение, Н |
Абсолютная погрешность, Н |
Приведенная погрешность, % |
Максимальное значение приведенной погрешности: % | ||||
Пределы допускаемой приведенной погрешности измерений усилий на органе управления ручной тормозной системой в соответствии с техническими характеристиками: ± % |
7. Определение абсолютной погрешности измерений скорости движения автомобиля.
Диаметр роликов:______м
Задаваемое значение, об/мин |
Измеренное значение, км/ч |
Действительное значение, км/ч |
Абсолютная погрешность, км/ч |
Максимальное значение абсолютной погрешности: км/ч | |||
Пределы допускаемой абсолютной погрешности измерений скорости движения автомобиля в соответствии с техническими характеристиками ± км/ч |
ПРИЛОЖЕНИЕ (Рекомендуемое)
ПРОТОКОЛ №
Дата и время проведения поверки:
Условия проведения поверки:
1. Внешний осмотр, проверка маркировки и комплектности
Требования |
Результаты поверки |
Наличие маркировки | |
Комплектность | |
Отсутствие механических повреждений и коррозии корпуса, рабочих поверхностей ходовых роликов, и других конструктивных элементов | |
Отсутствие механических повреждений и загрязнений сигнальных индикаторов, экрана дисплея, а также других повреждений, затрудняющих отсчет показаний и влияющих на их точность | |
Наличие четких надписей и отметок на органах управления |
2. Опробование, проверка работоспособности функциональных режимов и диапазонов измерений
Требования |
Результаты поверки |
Работоспособность всех функциональных режимов | |
Диапазоны измерений: тангенциальной составляющей силы, прикладываемой к поверхности ходовых роликов, усилий, прикладываемых к органам управления тормозными системами, скорости движения |
3. Определение средних диаметров ходовых роликов Блок передних ходовых роликов
№ п/ п |
Значение величин, приведенных в технических характеристиках |
Результаты испытаний |
1 |
Средние диаметры ходовых роликов мм | |
2 |
Диаметр ходовых роликов с покрытием мм | |
3 |
Среднее значение радиуса ходовых роликов с покрытием, мм |
Блок задних ходовых роликов
№ п/п |
Значение величин, приведенных в технических характеристиках |
Результаты испытаний |
1 |
Средние диаметры ходовых роликов мм | |
2 |
Диаметр ходовых роликов с покрытием мм | |
3 |
Среднее значение радиуса ходовых роликов с покрытием, мм | |
Диаметр ходовых роликов с покрытием в соответствии с техническими характеристиками: мм |