Методика поверки «СТАНКИ БАЛАНСИРОВОЧНЫЕ ВИБРОИЗМЕРИТЕЛЬНЫЕ СЕРИИ ВМВ» (МП ВМВ ХХХХХ.000.000 )
ОБЩЕСТВО С ОГРАНИЧЕННОЙ ОТВЕТСТВЕННОСТЬЮ
«ДИАМЕХ 2000»
УТВЕРЖДАЮ
Генеральный директор
ООО «ДИАМЕХ 2000»
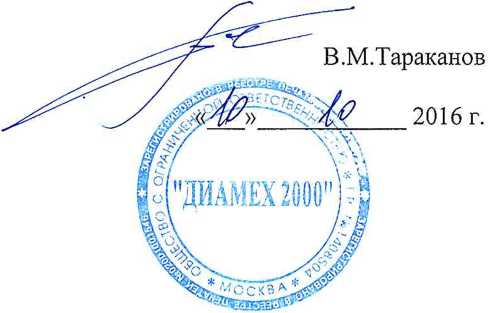
УТВЕРЖДАЮ Заместитель директора оизводственной метрологии ь * о < ч-»• Д'-
ФГУП «ВНИИМС»
7
Н.В. Иванникова
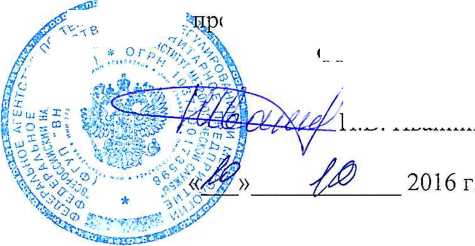
ВМВ ХХХХХ.000.000 МП
Москва 2016 г.
СТАНКИ БАЛАНСИРОВОЧНЫЕ ВИБРОИЗМЕРИТЕЛЬНЫЕ СЕРИИ ВМВ МЕТОДИКА ПОВЕРКИ
Настоящая методика поверки распространяется на станки балансировочные виброизмерительные серии ВМВ (далее - станки) и устанавливает методику их первичной поверки на стадии до ввода в эксплуатацию, первичной поверки после ремонта и периодической поверки.
Интервал меду поверками - 3 года.
Поверка станка проводится в два этапа. Первый этап - поверка измерительной системы при помощи вибрационной поверочной установки. Второй этап - поверка станка при помощи измерительной системы и контрольных грузов.
Допускается проводить поверку станка только при помощи контрольных грузов, которые предварительно должны быть взвешены на весах неавтоматического действия по ГОСТ 8.021-2015 высокого класса точности.
-
1 Поверка измерительной системы
1.1 Операции поверки
-
1.1.1 При проведении первичной и периодической поверок измерительной системы (далее системы) выполняют операции, указанные в таблице 1.1.
Таблица 1.1
Наименование операции |
Номер пункта |
Проведение операции при поверке | |
первичной |
периодической | ||
1 |
2 |
3 |
4 |
Внешний осмотр |
1.7.1 |
да |
да |
Опробование |
1.7.2 |
да |
да |
Проверка погрешности измерений амплитуды виброперемещения |
1.7.3 |
да |
да |
Проверка неравномерности амплитудно-частотной характеристики (АЧХ) |
1.7.4 |
да |
да |
1.2 Средства поверки
-
1.2.1 При проведении поверки должны применяться средства, указанные в таблице 2.
Таблица 1.2
Номер пункта |
Наименование средства поверки и его технические характеристики |
1 |
- |
1.7.1 |
- |
1.7.2 |
- |
1.7.3 и 1.7.4 |
Установка вибрационная поверочная 2-го разряда по ГОСТ Р 8.800-2012 |
-
1.2.1 Допускается применять другие средства поверки, удовлетворяющие требованиям настоящей методики по значениям допустимой погрешности.
1.3 Требования к квалификации поверителей
-
1.3.1 К поверке допускаются лица, аттестованные по месту работы в соответствии с правилами ПР 50.2.012-94, прошедшие обучение и имеющие свидетельство и аттестат поверителя.
1.4 Требования безопасности
-
1.4.1 Перед проведением поверки измерительная система должна быть подготовлена к работе в соответствии с руководством по эксплуатации.
1.5 Условия проведения поверки
1.5.1 При проведении поверки должны быть соблюдены следующие условия:
|
25 ±10 °C 60 ±20% 101 ±4 кПа |
- напряжение источника питания должно соответствовать значению, указанному в технической документации на систему
1.6 Подготовка к проведению поверки
-
1.6.1 При подготовке к проведению поверки должно быть установлено соответствие системы следующим требованиям:
-
- отсутствие механических повреждений корпусов составных частей системы, соединительных кабелей и электрических разъемов;
-
- резьбовые части электрических разъемов не должны иметь видимых повреждений;
-
1.6.2 В случае несоответствия системы вышеуказанным требованиям, она считается непригодной к применению, а ее поверка не производится до устранения выявленных несоответствий.
-
1.6.3 Приборы, используемые при проверке, должны быть прогреты и подготовлены к работе в соответствии с требованиями эксплуатационной документации.
-
1.7 Проведение поверки
1.7.1 Внешний осмотр
-
1.7.1.1 При внешнем осмотре устанавливают соответствие комплектности и маркировки требованиям эксплуатационной документации, а также отсутствие механических повреждений корпусов составных частей системы, соединительных кабелей и разъемов.
1.7.2 Опробование
-
1.7.2.1 Проверяют работоспособность системы в соответствии с эксплуатационной документацией
-
1.7.2.2 Проверяют идентификационные данные программного обеспечения (ПО): идентификационное наименование ПО, номер версии (идентификационный номер) ПО.
1.7.3 Проверка относительной погрешности измерения амплитуды виброперемещения
-
1.7.3.1 Проверку проводят с использованием эталонной вибрационной установки, на которой задают значения амплитуды виброперемещения: 0,1; 0,5; 1; 5; 10; 40; 80 и 100 мкм (Si зад.) на частоте 40 Гц.
Примечание - По согласованию с пользователем проверка по п.1.7.3.1 может осуществляться на любой частоте (в диапазоне 5...40 Гц), отличной от значения базовой частоты 40 Гц (2400 об/мин). В этом случае следует руководствоваться ГОСТ ИСО 1940-1 -2007 (п.5.3), согласно которому для однотипных роторов с уменьшением частоты балансировки допустимое значение остаточного удельного дисбаланса пропорционально возрастает в 2400/п раз (где п - частота вращения ротора, об/мин). При осуществлении поверки на выбранной частоте минимальное значение амплитуды виброперемещения, создаваемой вибрационной установкой, также необходимо увеличивать в 2400/п раз, а задаваемые значения амплитуды виброперемещения выбирать в соответствии с таблицей 1.3.
Таблица 1.3 Задаваемые значения амплитуды виброперемещения в зависимости от
базовой частоты вращения ротора
Базовая частота, Гц (об/мин) |
Задаваемые значения амплитуды виброперемещения, мкм |
5 (300) |
0,8; 1; 5; 10; 40; 80; 100 |
10 (600) |
0,4; 1; 5; 10; 40; 80; 100 |
15 (900) |
0,27; 0,5; 1; 5; 10; 40; 80; 100 |
20 (1200) |
0,2; 0,5; 1; 5; 10; 40; 80; 100 |
30 (1800) |
0,13; 0,5; 1; 5; 10; 40; 80; 100 |
40 (2400) |
0,1; 0,5; 1; 5; 10; 40; 80; 100 |
-
1.7.3.2 Измеренные значения амплитуды виброперемещения (Si изм.) считывают на дисплее блока отображения информации измерительной системы.
-
1.7.3.3 Значения основной относительной погрешности измерений амплитуды виброперемещения определяют по формуле:
где:
S, зад “ значение амплитуды виброперемещения, задаваемое на вибрационной установке;
Si изм ~ значение амплитуды виброперемещения, считанное на дисплее блока отображения информации
-
1.7.3.4 Полученные значения относительной погрешности на выбранной базовой частоте не должны превышать ± 10 %.
1.7.4 Проверка неравномерности амплитудно-частотной характеристики (АЧХ)
-
1.7.4.1 Измерения проводят при помощи эталонной вибрационной установки относительно базовой частоты 40 Гц. Задают на вибростенде значение виброперемещения равное 40 мкм на частотах 5; 10; 15; 20; 30; 40 Гц.
-
1.7.4.2 Сохраняя установленный уровень виброперемещения, изменяют частоту, а измеренные значения амплитуды виброперемещения (Si изм.) считывают на дисплее блока отображения информации измерительной системы.
Примечание - Если измерения по п. 1.7.3 проводились на базовой частоте, отличной от 40 Гц, то проверку неравномерности АЧХ осуществляют относительно значения базовой частоты, выбранного в соответствии с таблицей 1.3.
-
1.7.4.3 Значения неравномерности АЧХ вычисляют по формуле:
° баз 1 лл
(%) (2)
Где Si изм - значение амплитуды виброперемещения на Гой частоте, считанное на дисплее блока отображения информации;
Sscb - значение амплитуды виброперемещения на базовой частоте, считанное на дисплее блока отображения информации
-
1.7.4.4 Полученные значения неравномерности АЧХ относительно выбранной базовой частоты не должны превышать ± 12 %.
2 Поверка станка
-
2.1 Операции поверки
-
2.1.1 При проведении первичной и периодической поверок станка балансировочного виброизмерительного серии ВМВ (далее - станка) выполняют операции, указанные в таблице 2.1.
-
Таблица 2.1
Наименование операции |
Номер пункта |
Проведение операции при поверке | |
первичной |
периодической | ||
1 |
2 |
3 |
4 |
Внешний осмотр |
2.7.1 |
да |
да |
Опробование |
2.7.2 |
да |
Да |
Проверка основной относительной погрешности станка |
2.7.3 |
да |
да |
Проверка неравномерности амплитудно-частотной характеристики (АЧХ) станка |
2.7.4 |
да |
да |
2.2 Средства поверки
-
2.2.1 При проведении поверки должны применяться средства, указанные в таблице 2.2.
Таблица 2.2
Номер пункта |
Наименование средства поверки и его технические характеристики |
1 |
- |
2.7.1 |
- |
2.7.2 |
- |
2.7.3 и 2.7.4 |
Контрольные грузы от 0,01 до 100 г. |
2.3 Требования к квалификации поверителей
-
2.3.1 К поверке допускаются лица, аттестованные по месту работы в соответствии с правилами ПР 50.2.012-94, прошедшие обучение и имеющие свидетельство и аттестат поверителя.
2.4 Требования безопасности
-
2.4.1 Перед проведением поверки станок должен быть подготовлен к работе в соответствии с руководством по эксплуатации.
2.5 Условия проведения поверки
2.5.1 При проведении поверки должны быть соблюдены следующие условия:
|
25 ±10 °C 60 ±20% 101 ±4 кПа |
напряжение источника питания должно
соответствовать значению, указанному в технической документации на систему
2.6 Подготовка к проведению поверки
-
2.6.1 При подготовке к проведению поверки должно быть установлено соответствие станка следующим требованиям:
-
- отсутствие механических повреждений корпусов составных частей станка, соединительных кабелей и электрических разъемов;
-
- резьбовые части электрических разъемов не должны иметь видимых повреждений;
-
2.6.2 В случае несоответствия станка хотя бы одному из выше указанных требований, он считается непригодным к применению, поверка не производится до устранения выявленных замечаний.
-
2.6.3 Все приборы должны быть прогреты и подготовлены к работе в соответствии со своим руководством по эксплуатации.
-
2.6.4 Выполняют операции, изложенные в разделе 6 Руководства по эксплуатации на станок. Выполняют:
-
- регулировку горизонтального положения опорных стоек;
-
- выбор контрольного ротора, значение массы которого должно находиться в нижней трети диапазона грузоподъемности станка;
-
- установку контрольного ротора на опорные ролики;
-
- установку на контрольном роторе светочувствительной метки;
-
- ввод в измерительную систему параметров контрольного ротора;
- выбор и подготовку контрольных грузов mid зад., массы которых увязаны с параметрами выбранного контрольного ротора и в процессе поверки обеспечивают создание ряда значений искусственного удельного дисбаланса (е i. зад.): е i. зад. ~ 3 е регл 5 е регл 10 е регл 20 © регл 50 е регл 100 е per., 200 е регл где е per. - паспортное значение минимального достижимого остаточного удельного дисбаланса, мкм (г*мм/кг)
Примечание - Поверка станка осуществляется при скорости воздушного потока не более 0,1 м/с.
-
2.7 Проведение поверки
2.7.1 Внешний осмотр
-
2.7.1 При внешнем осмотре устанавливают соответствие комплектности и маркировки требованиям эксплуатационной документации, а также отсутствие механических повреждений корпусов составных частей станка, соединительных кабелей и разъемов.
2.7.2 Опробование
-
2.7.2.1 Осуществляют пуск станка, устанавливают выбранную частоту вращения контрольного ротора - 40 Гц (2400 об/мин).
Примечания:
1 По согласованию с пользователем настоящая проверка может осуществляться на любой частоте (в диапазоне 5...40 Гц), отличной от значения базовой частоты по п.2.7.2.1. В этом случае в соответствии с ГОСТ ИСО 1940-1 - 2007 (п.5.3) с уменьшением базовой частоты допустимое значение остаточного удельного дисбаланса для контрольной плоскости пропорционально возрастает в 2400/п раз и задается в соответствии с таблицей 2.3.
Таблица 2.3 Минимально допустимые значения остаточного удельного дисбаланса в зависимости от базовой частоты вращения ротора
Базовая частота, Гц (об/мин) |
Минимальное допустимое значение остаточного удельного дисбаланса е реГф, мкм |
5 (300) |
0,4 |
10 (600) |
0,2 |
15 (900) |
0,13 |
20 (1200) |
0,1 |
30 (1800) |
0,067 |
40 (2400) |
0,05 |
2 Массы контрольных грузов, обеспечивающих создание ряда значений удельного дисбаланса, приведенного в п.2.6.4, выбираются в соответствии с таблицами 2.4...2.6, составленных с учетом требований примечания 1 (п.2.7.2.1).
Таблица 2.4 Значения масс контрольных грузов на базовой частоте 40 Гц
Модель контрольного ротора |
Масса контрольного ротора, кг |
Масса условного груза, соответствующего минимальному достижимому остаточному удельному дисбалансу е рег, г |
Ряд значений массы контрольных грузов m id зад.5 г для создания удельного дисбаланса по п.2.6.4 |
РКД 005 |
5 |
0,006 |
0,02; 0,03; 0,06; 0,12; 0,3; 0,6; 1,2 |
РКД016 |
16 |
0,012 |
0,04; 0,06; 0,12; 0,24; 0,6; 1,2; 2,4 |
РКД 050 |
50 |
0,028 |
0,08; 0,14; 0,28; 0,56; 1,4; 2,8; 5,6 |
РКД 160 |
160 |
0,064 |
0,2; 0,32; 0,64; 1,28; 3,2; 6,4; 12,8 |
РКД 500 |
500 |
0,132 |
0,4; 0,67; 1,32; 2,64; 6,6; 13,2; 26,4 |
Таблица 2.5 Значения масс контрольных грузов на базовой частоте 15 Гц
Модель контрольного ротора |
Масса контрольного ротора, кг |
Масса условного груза, соответствующего минимальному достижимому остаточному удельному дисбалансу е рег, г |
Ряд значений массы контрольных грузов m id зад., г для создания удельного дисбаланса по п.2.6.4 |
РКД 005 |
5 |
0,006 |
0,048; 0,08; 0,16; 0,32; 0,8; 1,6; 3,2 |
РКД 016 |
16 |
0,012 |
0,096; 0,16; 0,32; 0,64; 1,6; 3,2; 6,4 |
РКД 050 |
50 |
0,028 |
0,22; 0,37; 0,75; 1,5; 3,73; 7,47; 14,9 |
РКД 160 |
160 |
0,064 |
0,51; 0,85; 1,7; 3,4; 8,5; 17,1; 34,1 |
РКД 500 |
500 |
0,132 |
1,06; 1,76; 3,52; 7,04; 17,6; 35,2; 70,4 |
Таблица 2.6 Значения масс контрольных грузов на базовой частоте 10 Гц
Модель контрольного ротора |
Масса контрольного ротора, кг |
Масса условного груза, соответствующего минимальному достижимому остаточному удельному дисбалансу е рег, г |
Ряд значений массы контрольных грузов m к! зад., г для создания удельного дисбаланса по п.2.6.4 |
РКД 005 |
5 |
0,006 |
0,07; 0,12; 0,24; 0,48; 1,2; 2,4; 4,8 |
РКД 016 |
16 |
0,012 |
0,16; 0,24; 0,48; 0,96; 2,4; 4,8; 9,6 |
РКД 050 |
50 |
0,028 |
0,34; 0,56; 1,1; 2,24; 5,6; 11,2; 22,4 |
РКД 160 |
160 |
0,064 |
0,77; 1,28; 2,56; 5,12; 12,8; 25,6; 51,2 |
РКД 500 |
500 |
0,132 |
1,58; 2,64; 5,28; 10,56; 26,4; 52,8; 105,6 |
-
3 При осуществлении поверки станка в условиях пользователя вследствие возможного разброса параметров измерительной системы, механических узлов станка, воздействия внешних факторов и т.п. возможен разброс значений точности станка, в результате чего, нижний предел диапазона измерений удельного дисбаланса может превысить заявленное значение 0,05 мкм. В этом случае, а также в других случаях изменения точности станка (как в сторону уменьшения, так и в сторону увеличения) по согласованию с пользователем допускается осуществлять его поверку в диапазоне измерений с зафиксированным значением нижнего предела диапазона измерений удельного дисбаланса и соответствующих значений массы контрольных грузов.
-
4 Масса контрольного ротора должна находиться в нижней трети диапазона допустимых масс уравновешиваемых роторов (грузоподъемности станка).
-
2.7.2.2 Вызывают искусственный дисбаланс контрольного ротора. Значение внесенного удельного дисбаланса выбирают на уровне 20 ерег, где ерег - паспортное значение минимального достижимого остаточного удельного дисбаланса.
-
2.7.2.3 Устраняют внесенный дисбаланс контрольного ротора путем осуществления стандартной процедуры балансировки. При этом для каждой контрольной плоскости ротора осуществляют проверку значения минимального достижимого остаточного удельного дисбаланса и его соответствия заявленному значению е рег.
-
2.7.2.4 В процессе выполнения операций по п.п. 2.7.2.3 и п.2.7.2.4 измерительной системой станка определяются коэффициенты влияния.
2.7.3 Проверка основной относительной погрешности станка
-
2.7.3.1 Измерительную систему переводят в режим «Калибровка и поверка станка».
-
2.7.3.2 Выбранные значения масс m id зад. (по п.2.7.2.1 Примечание 2) и углов установки контрольных грузов в плоскостях коррекции контрольного ротора вводят в измерительную систему, которая на основании определенных параметров коэффициентов влияния рассчитывает ожидаемые (заданные) значения амплитуды виброперемещения на опорной стойке станка (Si зад.1), соответствующие ряду выбранных масс контрольных грузов (т id зад.1).
-
2.7.3.3 В первой плоскости коррекции искусственно создают дисбаланс контрольного ротора, вызывающий вибрацию опорных стоек станка. Для этого в точке 0° по шкале разметки плоскости коррекции последовательно устанавливают контрольные грузы массой m id зад. 1, обеспечивающие ряд заданных в п.2.6.4 значений удельного дисбаланса.
-
2.7.3.4 После установки каждого из контрольных грузов Hl Ki зад.1 осуществляют пуск станка и на дисплее измерительной системы считывают значения амплитуды виброперемещения (Si изм.1), измеренные на опорной стойке станка, а также значения массы контрольного груза m id изм.1, соответствующие заданным значениям удельного дисбаланса е i зад.
-
2.7.3.5 Вычисляют основную относительную погрешность станка (§Si п) по результатам измерений амплитуды виброперемещения по формуле:
(3)
^isadn
где:
зад п “ заданное (ожидаемое) значение виброперемещения;
S\ изм п “ измеренное значение виброперемещения, соответствующее заданному значению удельного дисбаланса.
n - порядковый номер плоскости коррекции контрольного ротора
-
2.7.3.6 Вычисляют основную относительную погрешность станка по результатам измерений массы контрольного груза (m ki изм. п):
wi __тт?
с _ & измп ki задп gg z%\
(4)
t'nu n \ '
тк1задп
-
2.7.3.7 Изменяют место размещения контрольных грузов в первой плоскости коррекции контрольного ротора, последовательно устанавливая его через 60° по шкале разметки. Повторяют операции по п.п. 2.7.3.3 в каждой новой точке установки контрольных грузов.
Примечание! Допускается сократить число точек контроля, последовательно устанавливая контрольные грузы через 90° по шкале разметки.
-
2.7.8 Повторяют операции п.п. 2.7.3.3...2.7.3.7 для второй плоскости коррекции определяя погрешности измерения 8 Si 2, 8 mi 2 используя формулы п.п.2.7.3.5 и 2.7.3.6.
-
2.7.9 Для каждого положения контрольного груза, отмеченного по шкале разметки, полученные результаты измерений заносят в таблицы 2.7 и 2.8.
-
2.7.10 Результат операции поверки считается положительным, если вычисленные значения основной относительной погрешности для каждой точки измерений по формулам п.п.2.7.3.5 и 2.7.3.6 на выбранной базовой частоте не превышают ± 12 %.
Таблица 2.7 (Установка контрольных грузов m Ki зад.1 в плоскости коррекции 1)
Угол установки груза, град. |
* | ||||||
Частота, Гц | |||||||
mxi зад.1, г. | |||||||
тк!изм.1,г. | |||||||
3mi 1, % | |||||||
Si зад.1,мкм | |||||||
Si изм.1, мкм | |||||||
Ssi 1, % |
Таблица 2.8 (Установка контрольных грузов m id зад.2 в плоскости коррекции 2)
Угол установки груза, град. | |||||||
Частота, Гц | |||||||
mid зад.2, г. | |||||||
mid изм.2, г. | |||||||
3mi 2, % | |||||||
Si зад.2, мкм | |||||||
Si изм.2, мкм | |||||||
Ssi 2, % |
Примечание - Значение амплитуды виброперемещения на опорных стойках, значение удельного дисбаланса пропорциональны массе контрольного груза, радиусу его установки и обратно пропорционально массе контрольного ротора. Поскольку радиус установки контрольного груза и масса контрольного ротора являются константами расчет основной относительной погрешности станка выполняется с использованием значений m id изм. и m id зад,.
2.7.4 Проверка неравномерности АЧХ станка
-
2.7.1 В первой плоскости коррекции искусственно создают дисбаланс контрольного ротора. Для этого в точке 0° по шкале разметки плоскости коррекции устанавливают контрольный груз массой m к. зад., создающий удельный дисбаланс, равный 20 ерег.
-
2.7.2 Осуществляют пуск станка и устанавливают частоту вращения ротора - 40 Гц (± 3 %).
-
2.7.3 На дисплее измерительной системы считывают значение массы m изм. (40) установленного на роторе контрольного груза, измеренное при частоте вращений 40 Гц.
-
2.7.4 Меняют угловую скорость вращения ротора последовательно устанавливая частоту вращения из ряда: 5, 10,15,20,25 Гц с погрешностью задания-± 3 %.
-
2.7.5 Для каждого значения частоты вращения ротора на дисплее прибора измерительной системы считывают значение измеренной массы (т ю изм.) установленного на роторе контрольного груза.
-
2.7.6 Повторяют операции п.п. 2.7.1... 2.7.5 для второй плоскости коррекции.
-
2.7.7 Вычисляют неравномерность АЧХ станка относительно базовой частоты 40 Гц по формуле:
где Шизд^о - значение массы контрольного груза, определяемое по блоку отображения информации на базовой частоте 40 Гц;
т ki изм - значение массы контрольного груза, определяемое по блоку отображения информации на Гой частоте
-
2.7.8 Результаты измерений заносят в таблицы 3.1 и 3.2.
Таблица 3.1 (Установка контрольных грузов mid зад.1 в плоскости коррекции 1)
£Гц |
5 |
10 |
15 |
20 |
25 |
40 |
тк зад. 1, г. |
20ткпнп | |||||
mid изм 1.,г. | ||||||
Г,% |
0 |
Таблица 3.2 (Установка контрольных грузов mid зад.2 в плоскости коррекции 2)
f,rit |
5 10 |
15 |
20 |
25 |
40 | |
тк зад. 2, г. |
20 шктт | |||||
т id изм 2., г. | ||||||
У,°/о |
0 |
Примечания:
-
1 Значение амплитуды виброперемещения на опорных стойках, значение удельного дисбаланса пропорциональны массе контрольного груза, радиусу его установки и обратно пропорционально массе контрольного ротора. Поскольку радиус установки контрольного груза и масса контрольного ротора являются константами расчет неравномерности АЧХ станка выполняется с использованием значений m Ki изм. и m Ki зад..
-
2 При изменении базовой частоты расчет неравномерности АЧХ осуществляют с использованием формулы (5) относительно выбранной частоты проверки станка.
-
2.7.9 Результат операции поверки считается положительным, если неравномерность АЧХ станка относительно выбранной базовой частоты не превышает ±15%.
3 Оформление результатов поверки
-
3.1 Положительные результаты поверки станка оформляются «Свидетельством о поверке» по форме, установленной в Приложении 1 ПР50.2.006-94 с нанесением на техническую документацию оттиска поверительного клейма.
-
3.2 Станок, не удовлетворяющий требованиям настоящей методики поверки, к применению не допускается, на него выдается «Извещение о непригодности» по форме Приложения 2 ПР50.2.006-94 с указанием причин.
Начальник отдела 204
ФГУП «ВНИИМС»
Начальник лаборатории 204/3
ФГУП «ВНИИМС»
Испытатель
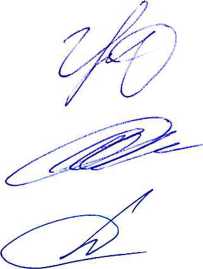
А.Е. Рачковский
А.Г. Волченко
Ю.С. Дикарева
12