Методика поверки «Шаблоны универсальные модели ПШ00316А» (МП 203-18-2016)
ФГУП «ВСЕРОССИЙСКИЙ НАУЧНО-ИССЛЕДОВАТЕЛЬСКИЙ ИНСТИТУТ МЕТРОЛОГИЧЕСКОЙ СЛУЖБЫ»
ФГУП «вниимс»
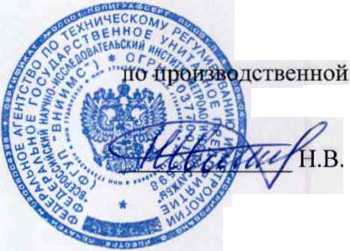
«07» ноября 2016 г.
УТВЕРЖДАЮ Зам. директора метрологии ФГУП «ВНИИМС»
Шаблоны универсальные модели ПШ00316А МЕТОДИКА ПОВЕРКИ МП 203-18-2016МОСКВА, 2016
Настоящая методика поверки распространяется на шаблоны универсальные модели ПШ00316А (далее по тексту - шаблоны), выпускаемые по ТУ 3936-011-30903142-2015 «Шаблоны универсальные модели ПШ00316А. Технические условия», изготавливаемые ООО «Армада», г. Киров и устанавливает методы и средства их первичной и периодической поверок.
Интервал между поверками 1 год.
1. ОПЕРАЦИИ И СРЕДСТВА ПОВЕРКИ1.1. При проведении поверки должны быть выполнены операции и применены средства поверки, указанные в таблице 1.
Таблица 1
Наименование операции |
Номер пункта методики поверки |
Средства поверки |
Проведение операции при | |
первичной поверке |
периоди ческой поверке | |||
Внешний осмотр |
5.1. |
Визуально |
да |
да |
Опробование |
5.2. |
Визуально |
да |
да |
Определение шероховатости рабочих и измерительных поверхностей |
5.3. |
Образцы шероховатости поверхности с параметрами Ra =0,8 мкм, Ra =1,6 мкм по ГОСТ 9378-93; профилометр-профилограф контактный по ГОСТ 19300-86 |
да |
нет |
Определение угла между рабочими поверхностями для контроля взаимного расположения остряка и рамного рельса |
5.4. |
Угломер типа 1-5 по ГОСТ 5378-88 |
да |
нет |
Определение отклонения от прямолинейности рабочих и измерительных поверхностей |
5.5. |
Линейка ЛД-1-320 по ГОСТ 8026-92, щупы 0,03 мм и 0,05 мм по ТУ 2-034-0221197-011-91, образец просвета из концевых мер длины 3 класса точности по ГОСТ 9038-90 и плоской стеклянной пластины диаметром 60 мм с отклонением от плоскостности не более 0,09 мкм |
да |
да |
Определение абсолютной погрешности при измерении стыковых рельсовых зазоров |
5.6. |
Штангенциркуль ШЦ-1-150-0,1 по ГОСТ 166-89 |
да |
да |
Определение абсолютной погрешности при измерении глубины поверхностных дефектов, горизонтальных и вертикальных ступенек |
5.7. |
Меры длины концевые плоскопараллельные 10 и 15 мм, класс точности 3 по ГОСТ 9038-90, плита поверочная 1-1-400x400 по ГОСТ 10905-86, микроскоп видеоизмерительный |
да |
да |
рельсовых стыков |
ММ320 с диапазоном измерений 200x100 мм (per. № 39844-13) | |||
Определение абсолютной погрешности при измерении протяженности поверхностных дефектов и расположения болтовых отверстий |
5.8. |
Линейка измерительная металлическая с верхним пределом диапазона измерений 300 мм по ГОСТ 427-75; микроскоп видеоизмерительный ММ320 с диапазоном измерений 200x100 мм (per. № 39844-13) |
да |
да |
Примечание: Допускается применение аналогичных средств поверки, не приведенных в перечне, но обеспечивающих определение метрологических характеристик поверяемых средств измерений с требуемой точностью.
2. ТРЕБОВАНИЯ БЕЗОПАСНОСТИПри проведении поверки шаблонов должны соблюдаться следующие требования:
-
- при подготовке к проведению поверки должны быть соблюдены требования пожарной безопасности при работе с легковоспламеняющимися жидкостями, к которым относится бензин, используемый для промывки;
-
- бензин хранят в металлической посуде, плотно закрытой металлической крышкой, в количестве не более однодневной нормы, требуемой для промывки;
-
- промывку проводят в резиновых технических перчатках типа II по ГОСТ 20010-93.
-
3.1. Всю поверку шаблонов, следует проводить в нормальных условиях применения приборов:
-
- температура окружающего воздуха, °C (20 ± 5)
-
- относительная влажность окружающего воздуха при температуре 25 °C не более 80%.
Перед проведением поверки должны быть выполнены следующие подготовительные работы:
- шаблоны и средства измерений должны быть подготовлены к работе в соответствии с технической документацией на них;
-
- шаблоны должны быть выдержаны в помещении, где проводят поверку не менее 1 часа.
-
5.1. При внешнем осмотре по п. 5.1. (далее нумерация согласно таблицы 1) должно быть установлено:
-
- отсутствие на рабочих и измерительных поверхностях шаблона дефектов влияющих на эксплуатационные качества;
-
- отчетливость и правильность оцифровки штрихов шкал;
-
- поверхности, на которые нанесены шкалы, должны быть матовыми;
-
- на каждом шаблоне должны быть нанесены: товарный знак предприятия-изготовителя, порядковый заводской номер, модель шаблона.
-
- штрихи на шкале «В», соответствующие отметкам 96, 130 и 220 мм и определяющие расположение болтовых отверстий в рельсах типов Р65, Р65К, Р75, должны иметь отличительный условный знак «V», а штрихи - 66, 140 и 150 мм, определяющие расположение болтовых отверстий в рельсах типов Р50, - знак «о».
Шаблон считается прошедшим поверку, если он удовлетворяет всем вышеперечисленным требованиям.
-
5.2. Опробование.
В рабочем положении измерительный рычаг не должен перемещаться под действием собственного веса.
Шаблон считается прошедшим поверку, если он удовлетворяет вышеперечисленному требованию.
-
5.3. Шероховатость измерительных поверхностей шаблонов проверяют визуально сравнением с образцами шероховатости.
Шероховатость Ra измерительной поверхности измерительного стержня и рабочих поверхностей для контроля взаимного расположения остряка и рамного рельса должна быть не более 0,8 мкм, а остальных рабочих поверхностей не более 1,6 мкм по ГОСТ 2789-73.
При возникновении спорных вопросов шероховатость поверхности определяют профилометром степени точности 2 по ГОСТ 19300-86.
-
5.4. Угол между рабочими поверхностями для контроля взаимного расположения остряка и рамного рельса определяют с помощью угломера. Измерение угла производят дважды. За результат измерений принимают среднеарифметическое значение.
Угол между рабочими поверхностями для контроля взаимного расположения остряка и рамного рельса должен быть 120°±20'
-
5.5. Отклонения от прямолинейности рабочих поверхностей для контроля взаимного расположения остряка и рамного рельса проверяют при помощи лекальной линейки с двусторонним скосом. Ребро лекальной линейки устанавливают на рабочую поверхность параллельно длинному ребру контролируемой поверхности и определяют величину зазора, если таковой имеется, с помощью щупа.
Щуп толщиной 0,03 мм не должен проходить в имеющийся зазор.
Зазор длиной менее 10 мм определяют визуально сравнением с образцом просвета. Для получения «образца просвета» к рабочей поверхности плоской стеклянной пластины нижней притирают параллельно друг к другу плоскопараллельные концевые меры длины, разность номинальных длин которых равна 0,03 мм. Две одинаковые концевые меры большей длины притираются по краям, а концевую меру меньшей длины между ними. При наложении ребра лекальной линейки на концевые меры длины в направлении, параллельном их короткому ребру получается «образец просвета».
Просвет между лекальной линейкой и контролируемой поверхностью не должен превышать просвета на «образце просвета».
Отклонения от прямолинейности рабочих поверхностей для контроля протяженности поверхностных дефектов элементов рельсовых и стрелочных переводов проверяют лекальной линейкой. Ребро поверочной линейки устанавливают на рабочую поверхность параллельно длинному ребру контролируемой поверхности и определяют величину зазора, если таковой имеется, с помощью щупа.
Щуп толщиной 0,05 мм не должен проходить в имеющийся зазор.
Зазор длиной менее 10 мм определяют визуально сравнением с образцом просвета. Для получения «образца просвета» к рабочей поверхности плоской стеклянной пластины нижней притирают параллельно друг к другу плоскопараллельные концевые меры длины, разность номинальных длин которых равна 0,05 мм. Две одинаковые концевые меры большей длины притираются по краям, а концевую меру меньшей длины между ними. При наложении ребра лекальной линейки на концевые меры длины в направлении, параллельном их короткому ребру получается «образец просвета».
Просвет между лекальной линейкой и контролируемой поверхностью не должен превышать просвета на «образце просвета».
-
5.6. Определение абсолютной погрешности при измерении стыковых рельсовых зазоров.
Определение абсолютной погрешности шаблона при измерении стыковых рельсовых зазоров производят с помощью штангенциркуля ШЦ-1-150-0,1 по ГОСТ 166-89.
Абсолютную погрешность шаблона проверяют в точках «5», «30» и «50» мм шкалы.
Штангенциркуль устанавливают на размер, соответствующий контролируемому. Фиксируют положение подвижной губки стопорным винтом. Помещают шаблон между губками штангенциркуля и снимают показания по шкале шаблона 3-5 раз.
Разность между показаниями штангенциркуля и шаблона не должна превышать пределов допускаемой абсолютной погрешности ±0,5 мм.
-
5.7. Определение абсолютной погрешности при измерении глубины поверхностных дефектов и стрелочных переводов, горизонтальных и вертикальных ступенек рельсовых стыков проводят с помощью концевых мер длиной 10 мм и 15 мм и поверочной плиты. Шаблон вертикально устанавливают рабочей поверхностью на поверочную плиту, опускают измерительный наконечник до касания с плитой и снимают показания по шкале «Б» 3-5 раза. Затем устанавливают на поверочной плите две концевые меры длиной 10 мм параллельно друг другу на расстоянии 180 - 200 мм. Шаблон устанавливают рабочей поверхностью на концевые меры и опускают измерительный наконечник до касания с плитой. Снимают показания по шкале «Б» и указательному штриху 3-5 раза. Повторяют проверку с использованием концевых мер длиной 15 мм.
Несовпадение штриха указателя и штрихов шкалы «0», «10» и «15» должно быть не более 1/4 цены деления шкалы «Б», что не превышает пределов допускаемой абсолютной погрешности ±0,25 мм.
При возникновении спорных вопросов несовпадение штриха указателя и штрихов шкалы измеряют при помощи микроскопа.
-
5.8. Определение абсолютной погрешности при измерении протяженности поверхностных дефектов и расположения болтовых отверстий проводят с помощью измерительной линейки. Накладывают линейку на шкалу «В» шаблона так, чтобы нулевой штрих линейки совпал с кромкой шаблона, расположенной справа от начального штриха шкалы «В». Сопоставляют штрихи линейки с соответствующими штрихами шкалы «В» шаблона во всем ее диапазоне, а также в точках 66, 96, 130, 140, 150 и 220 мм.
Несовпадение штрихов не должно превышать пределов допускаемой абсолютной погрешности ±0,25 мм.
При возникновении спорных вопросов несовпадение штрихов линейки с соответствующими штрихами шкалы «В» шаблона во всем ее диапазоне, а также в указанных точках измеряют при помощи микроскопа.
6. ОФОРМЛЕНИЕ РЕЗУЛЬТАТОВ ПОВЕРКИ-
6.1. При положительных результатах поверки оформляется свидетельство о поверке по форме приложения 1 Приказа Минпромторга России № 1815 от 02.07.2015г.
-
6.2. При отрицательных результатах поверки оформляется извещение о непригодности по форме приложения 2 Приказа Минпромторга России № 1815 от 02.07.2015г.
Знак поверки наносится на свидетельство о поверке.
Зам. начальника отдела 203
Испытательного центра ФГУП «ВНИИМС
Ведущий инженер отдела 203
ФГУП «ВНИИМС»
Табачникова
Н.И. Кравченко