Методика поверки «Комплексы измерительные диагностические тормозной системы и подвески автотранспортных средств VTEQ» (МП 06/004-12)
Государственная система обеспечения единства измерений
УТВЕРЖДАЮ
Заместитель руководителя ГЦИ СИ ФБУ «ЦСМ Московской области»
Директор
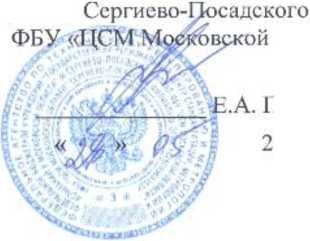
филиала
области»
Комплексы измерительные диагностические тормозной системы и подвески автотранспорт ных средств VTEQ
МЕТОДИКА ПОВЕРКИ МП 06/004-12Настоящая методика поверки распространяется на комплексы измерительные диагностические тормозной системы и подвески автотранспортных средств VTEQ (далее -комплексы) модификаций VTEQ 3000, VTEQ 3014, VTEQ 3080, VTEQ 7000, входящие в их состав стенды тормозные роликовые исполнений (моделей) BRAK 1000, BRAK 2000, BRAK 2080, BRAK 3000, BRAK 3011, BRAK 3014, BRAK 3080, BRAK 6000, BRAK 7000, стенды диагностирования подвески исполнений (моделей) EUSAMA 3000, EUSAMA 3012, EUSAMA 3013 и стенды бокового увода колес исполнений (моделей) SLIP 3000, SLIP 7000 (далее - стенды), и устанавливает методику их первичной и периодической поверки.
Рекомендуемый межповерочный интервал - один год.
1 Операции и средства поверкиПри проведении поверки проводят операции, указанные в таблице 1, и должны использоваться средства поверки, указанные в таблице 2.
Таблица 1. Операции поверки.
№ п/п |
Операции поверки |
Номер пункта методики поверки |
Проведение операций при поверке | |
первичной (внеочередной) |
периодической | |||
1 |
Внешний осмотр |
5.1 |
+ |
+ |
2 |
Определение идентификационных данных программного обеспечения |
5.2 |
+ |
+ |
3 |
Опробование |
5.3 |
+ |
+ |
4 |
Определение метрологических характеристик |
5.4 | ||
4.1 |
Определение погрешности измерений тормозной силы |
5.4.1 |
+ |
+ |
4.2 |
Определение погрешности измерений массы автотранспортного средства |
5.4.2 |
+ |
+ |
4.3 |
Определение погрешности измерений перемещений платформы стенда бокового увода колес |
5.4.3 |
+ |
+ |
При несоответствии характеристик поверяемого стенда установленным требованиям по любому из пунктов таблицы 1 его к дальнейшей поверке не допускают и последующие операции не проводят, за исключением оформления результатов по п. 6.
Таблица 2. Средства поверки.
№ п/п методики поверки |
Наименование средства измерения |
Метрологические характеристики |
5.4.1 |
Калибровочные приспособления (рычаги с грузами) из комплекта поставки, аттестованные в установленном порядке (приложение 1). Линейка поверочная типа ШП или ШД по ГОСТ 8026-92. Штангенциркуль ШЦ-1 по ГОСТ 166-89. |
Диапазон воспроизведения силы (0-6) кН, погрешность ±1 % для стендов моделей BRAK 1000, BRAK 2000, BRAK 2080, BRAK 3000, BRAK 3011, BRAK 3014, BRAK 3080. Диапазон воспроизведения силы (0-40) кН, погрешность ±1 % для стендов моделей BRAK 6000, BRAK 7000. Длина 400 или 630 мм, класс точности 2. Диапазон измерений (0-125) мм, цена деления 0,1 мм, с глубиномером. |
5.4.2 |
Гири эталонные по ГОСТ 7328-2001. |
4 разряда (класс точности М1), масса 10 кг 1 шт., масса 20 кг 20 шт., масса 500 кг 6 шт., масса 1000 кг 6 шт. |
5.4.3 |
Меры длины концевые плоскопараллельные. Набор принадлежностей к плоскопараллельным концевым мерам длины ПК-1 по ГОСТ 4119-76. |
ГОСТ 9038-90, набор №2, класс точности 4. Державка 80 мм с плоскопараллельными боковиками 10 мм. |
Примечания:
-
1) Допускается применять другие средства поверки, метрологические и технические характеристики которых не хуже приведенных в таблице 2.
-
2) Все средства измерений должны быть исправны и поверены.
К поверке комплексов допускают лиц, аттестованных на право поверки средств измерений механических и линейных измерений и изучивших эксплуатационную документацию на комплексы.
Поверитель должен пройти инструктаж по технике безопасности и иметь удостоверение на право работы в электроустановках с напряжением до 1000 В с группой допуска не ниже III.
3 Требования безопасностиПри проведении поверки должны быть соблюдены требования ГОСТ 12.3.019-80, ПОТ РМ-016-2001 РД 153-34.0-03.150-00 «Межотраслевые правила по охране труда (правила безопасности) при эксплуатации электроустановок».
Так же должны быть обеспечены требования безопасности, указанные в эксплуатационных документах на средства поверки и комплексы.
4 Условия поверки и подготовка к ней-
4.1 При проведении поверки должны соблюдаться следующие условия:
-
- температура окружающей среды, °С 10-30;
-
- относительная влажность воздуха, % 30-80;
-
- атмосферное давление, кПа 85-105.
-
4.2 Средства поверки подготавливают к работе согласно указаниям, приведенным в соответствующих эксплуатационных документах.
-
5.1 Внешний осмотр
При проведении внешнего осмотра должно быть установлено соответствие поверяемого комплекса следующим требованиям:
-
- комплектность в соответствии с эксплуатационной документацией;
-
- отсутствие коррозии, механических повреждений и других дефектов, нарушающих работу стендов и аппаратуры комплекса;
-
- наличие маркировки и заводских номеров на стендах и измерительном блоке (консоли контроллера) комплекса и их соответствие эксплуатационной документации.
-
5.2 Определение идентификационных данных программного обеспечения
Перед поверкой необходимо выполнить проверку идентификационных данных программного обеспечения (ПО) комплекса: идентификационного наименования, номера версии и контрольной суммы ПО.
Алгоритм проверки идентификационного наименования, версии и контрольной суммы ПО при поверке:
1. Включите комплекс согласно эксплуатационной документации.
3»ят
VTEQWm
2. Для значка программы VTEQWin
на рабочем столе дисплея персонального компьютера по правой кнопке мыши вызовите пункт меню «Свойства». На экране отобразится окно с идентификационным наименованием ПО.
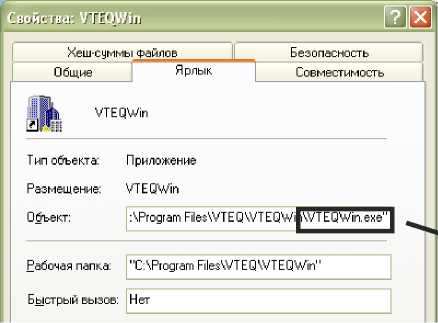
Идентификационное наименование
Рисунок 1. Окно «Свойства» с идентификационным наименованием программы VTEQWin
3. Запустите программу VTEQWin, на экране будет отображаться рабочее окно программы VTEQWin с номером версии и контрольной суммой ПО (рис. 2).
Контрольная сумма
Номер версии ПО
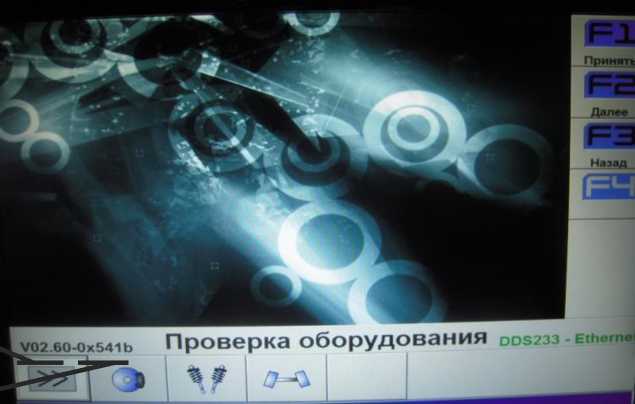
Рисунок 2. Стартовый экран программы VTEQWin с номером версии и контрольной суммой ПО
Идентификационные данные ПО комплекса должны соответствовать таблице 3. Таблица 3. Идентификационные данные программного обеспечения комплекса.
Наименование |
Идентификационное наименование |
Номер версии (идентификационный номер) |
Цифровой идентификатор (контрольная сумма исполняемого кода) |
ПО линий диагностических VTEQ |
VTEQWin |
02.60 |
0x541b |
В случае, если идентификационные данные ПО не соответствуют указанным в табл. 3, для данного комплекса может быть выполнена только его калибровка по настоящей методике поверки.
-
5.3 Опробование
При опробовании должно быть установлено соответствие комплекса следующим требованиям:
- отсутствие сообщений о неисправностях при включении;
- возможность выбора стендов для диагностики.
Далее с использованием автотранспортного средства выполнить проверку работоспособности всех стендов, следуя алгоритму проверки автотранспортного средства на стендах комплекса. В ходе выполнения диагностики на дисплее должны отображаться ход и результаты выполнения тестов.
Комплекс и входящие в его состав стенды должны функционировать в соответствии с эксплуатационной документацией.
-
5.4 Определение метрологических характеристик
-
5.4.1 Определение погрешности измерений тормозной силы.
-
При периодической поверке перед определением погрешности измерений тормозной силы осуществляется проверка величины износа роликов стенда.
Величина износа определяется для каждого ролика стенда с помощью линейки поверочной и штангенциркуля с глубиномером. Поверочная линейка устанавливается на ребро симметрично относительно центра по длине ролика и плотно прижимается к нему рукой. Штангенциркулем измеряется расстояние между линейкой и роликом на одном из краев линейки и в месте наибольшей выработки ролика.
Разность измеренных расстояний для каждого ролика не должна превышать 5 мм.
Погрешность измерений тормозной силы стендов моделей BRAK определяется с помощью калибровочного приспособления (Приложение 1) в ручном режиме измерения тормозной силы поочередно для левого и правого тормозных роликов (рис. 3).
Индикатор канала
Индикатор канала измерения тормозной силы левого ролика
измерения
тормозной силы
левого ролика
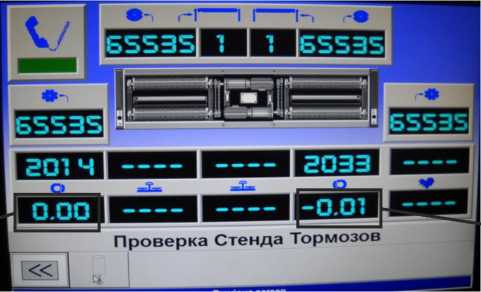
Индикатор канала
Индикатор канала измерения тормозной силы правого ролика
Рисунок 3. Экран программы теста тормозов
измерения
тормозной силы
правого ролика
Определение погрешности измерений проводить в следующей последовательности:

из стартового экрана программы VTEQWin (рис. 2) вызовите кнопкой
программу теста тормозов (рис. 3);
- установите рычаг длинным плечом по ходу диагностируемых автомобилей на любой ролик стенда:
-
a) для стендов моделей BRAK 1000, BRAK 2000, BRAK 2080, BRAK 3000, BRAK 3011, BRAK 3014, BRAK 3080 в соответствии с рис. 4а (для обеспечения доступа к местам установки силоизмерительного рычага снимите крышку со стенда). Регулировкой болта опорного обеспечьте горизонтальность установки рычага по встроенному уровню. Установите на «0» отметку рычага груз (30 кг) из его комплекта и зафиксируйте показания индикатора канала измерения силы F0;
-
b) для стендов моделей BRAK 6000, BRAK 7000 в соответствии с рис. 4б. Регулировкой серьги на опорной тяге обеспечьте горизонтальность установки рычага по встроенному уровню и зафиксируйте показания индикатора канала измерения силы F0;
- проведите поверку канала измерений силы в соответствии с табл. 1 Приложения 2, передвигая груз по делениям рычага от начального до конечного и обратно и фиксируя при этом показания индикатора канала измерения тормозной силы Fu:5M i (рис. 3). При каждом перемещении груза контролируйте горизонтальность установки рычага по встроенному уровню и при необходимости корректируйте его. При поверке стендов BRAK 6000 и BRAK 7000 для получения последних 3-х значений силы используют два груза, помещаемых на указанные отметки рычага;
Места установки силоизмерительного рычага
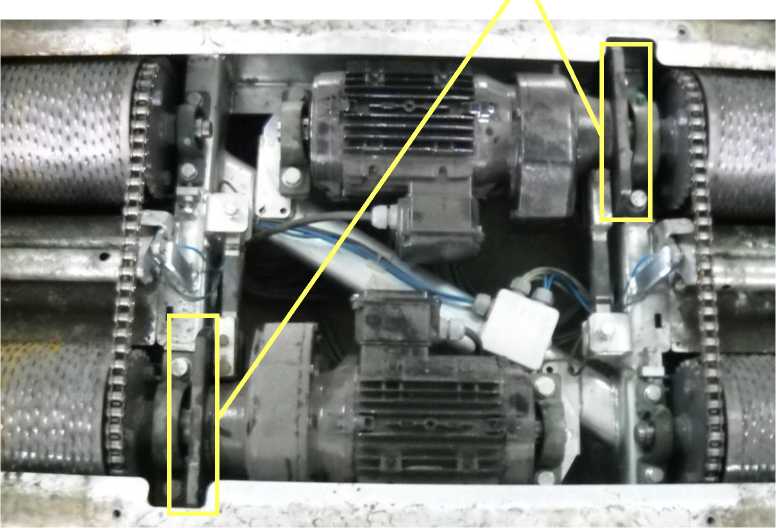
Рисунок 4а. Стенд тормозной роликовый BRAK 3000 со снятой крышкой
Серьга опорной тяги силоизмерительного рычага
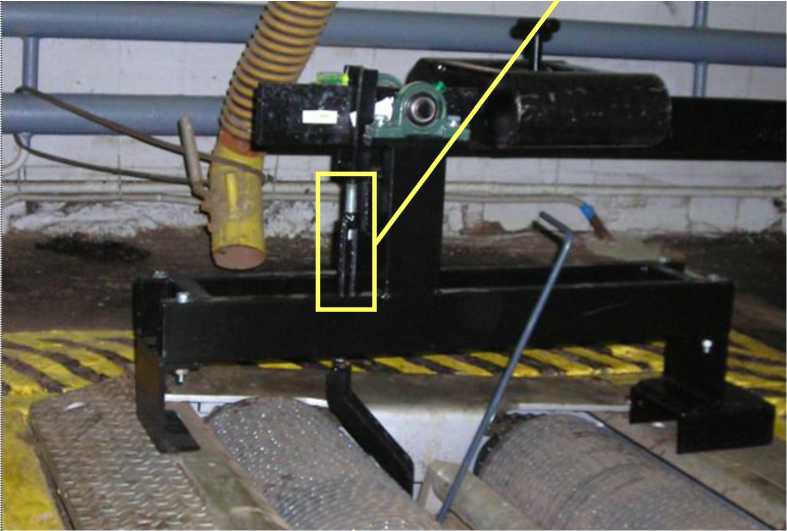
Рисунок 4б. Стенд тормозной роликовый BRAK 7000
- аналогичные измерения проведите для второго ролика стенда;
- относительную погрешность измерений определите по формуле:
Si = (Fu3M i - Fo -Бзад i)^ i • 100 %,
где FU3M i - измеренное значение силы в i-той точке, кН,
F3ag i - заданное значение силы, соответствующее i-той отметке рычага, кН из протокола аттестации рычага,
F0 - значение силы, измеренное в отметке «0» рычага с установленным грузом, кН.
Относительная погрешность измерений тормозной силы в каждой точке при нагружении и разгружении не должна превышать ±3 %.
-
5.4.2 Определение погрешности измерений массы автотранспортного средства.
Определение погрешности измерений массы автотранспортного средства (каждого колеса одной оси) производится с помощью эталонных гирь 4 разряда. Поверка выполняется поочередно для левой и правой платформ стендов диагностирования подвески EUSAMA и стендов тормозных роликовых BRAK при наличии функции измерений массы. При периодической поверке допускается использовать метод замещающей массы или подкладных весов.
Для стендов BRAK поверка производится в программе теста тормозов (рис. 5).
Индикатор канала измерения массы левого колеса
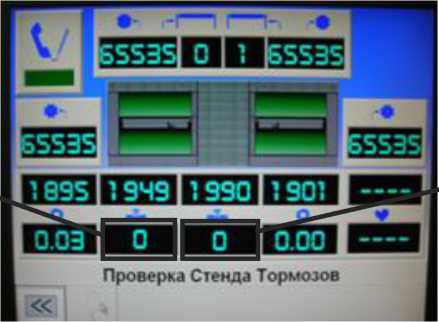
Индикатор канала измерения массы правого колеса
Рисунок 5. Экран программы теста тормозов
Для стендов EUSAMA поверка производится в программе теста амортизаторов подвески
(рис. 6).
Индикатор канала измерения массы левого колеса
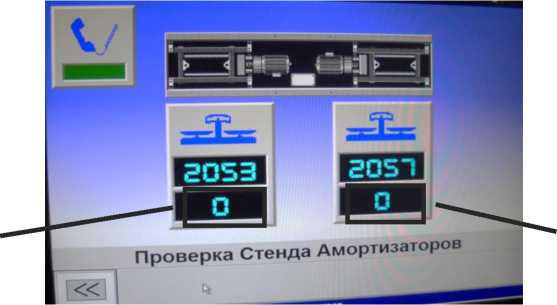
Индикатор канала измерения массы правого колеса
Рисунок 6. Экран программы теста амортизаторов подвески
Для входа в программу теста амортизаторов подвески необходимо с помощью кнопки № последовательности:

вернуться в стартовый экран программы VTEQWin (рис. 2) и вызвать кнопкой программу теста амортизаторов подвески (рис. 6).
Определение погрешности измерений массы проводить в следующей
-
- последовательно размещая на левой платформе поверяемого стенда эталонные гири массой, указанной в табл. 2 Приложения 2, снимать показания с индикатора канала измерения массы левого колеса на экране дисплея (рис. 5 или 6). Измерения проводить при нагружении и разгружении платформы;
-
- аналогичные измерения провести для правой измерительной платформы;
- относительная погрешность измерений массы определить по формуле:
Si = (Мизм i - Мзад i)Mag i • 100 %,
где Мизм i - измеренное значение массы в i-той точке, кг, Мзад i - значение массы, заданное эталонными гирями, кг.
Относительная погрешность измерений массы в каждой точке при нагружении и разгружении не должна превышать ±3 %.
-
5.4.3 Определение погрешности измерений перемещения платформы стенда бокового увода колес.
Определение погрешности измерений перемещения платформы стенда бокового увода колес моделей SLIP производится с помощью мер длины концевых плоскопараллельных, установленных в державку 80 мм с плоскопараллельными боковиками набора принадлежностей ПК-1 для измерения внутреннего размера (сторона державки без концевых мер должна быть повернута к центру стенда) рис. 7.
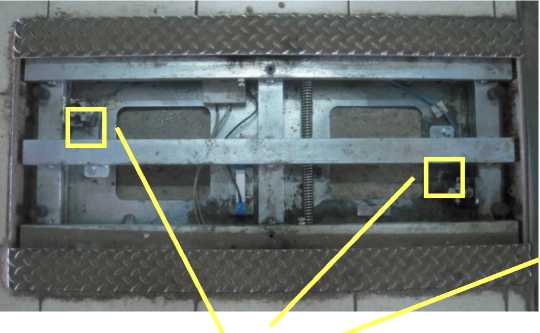
Места установки державки с концевыми мерами
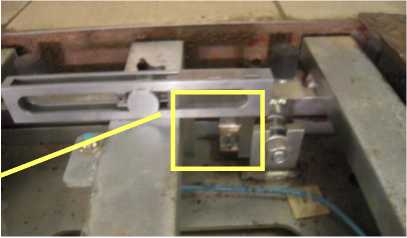
Рисунок 7. Стенд бокового увода колес (со снятой платформой)
Для входа в программу теста бокового увода колес необходимо с помощью кнопки №
вернуться в стартовый экран программы VTEQWin (рис. 2) и вызвать кнопкой программу теста бокового увода колес (рис. 8).
Индикатор канала измерения перемещения платформы
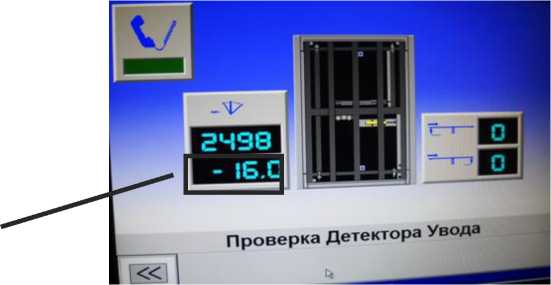
Рисунок 8. Экран программы теста бокового увода колес
Определение погрешности измерений перемещения платформы стенда бокового увода колес проводить в следующей последовательности:
-
- снять подвижную платформу стенда;
-
- наборы концевых мер в державке (с учетом исходного расстояния между опорой и перемещаемой рамой), необходимые для получения заданной величины перемещения в соответствии с табл. 3 Приложения 2, установить между опорой левой/правой и перемещаемой рамой. Для каждого значения перемещения снять показания с индикатора канала измерения перемещения платформы на экране дисплея (рис. 8). Измерения проводить при перемещении рамы влево и вправо;
- абсолютную погрешность измерений перемещения платформы определить по формуле:
^Li LU3M i - L3ag ь
где LU3M i - измеренное значение перемещения в i-той точке, мм,
L3ag i - заданное значение перемещения в i-той точке, мм;
- относительную погрешность измерений перемещения платформы определить по формуле: Si = Ды ^ад i • 100 %.
Погрешность измерений перемещения платформы не должна превышать пределов, указанных в таблице 4.
Таблица 4. Пределы допускаемых погрешностей измерений перемещения платформы.
Модель стенда |
Диапазон измерений перемещения, мм |
Пределы допускаемой погрешности измерений перемещения |
SLIP 3000 |
0-20 |
±0,3 мм в диапазоне (0-8) мм; |
SLIP 7000 |
±5 % свыше 8 мм |
-
6.1 Результаты измерений, полученные в процессе поверки, оформляют рабочими записями произвольной формы. Допускаются компьютерные записи, формирование и хранение результатов поверки.
-
6.2 Положительные результаты поверки оформляют свидетельством о поверке на каждый стенд комплекса в соответствии с действующими нормативными документами.
-
6.3 При несоответствии результатов поверки требованиям пунктов настоящей методики соответствующий стенд комплекса к дальнейшей эксплуатации не допускают и выдают извещение о непригодности в соответствии с действующими нормативными документами. В извещении указывают причину непригодности.
Приложение 1
Чертеж калибровочного приспособления для стендов моделей BRAK 1000, BRAK 2000, BRAK 2080, BRAK 3000, BRAK 3011, BRAK 3014, BRAK 3080.
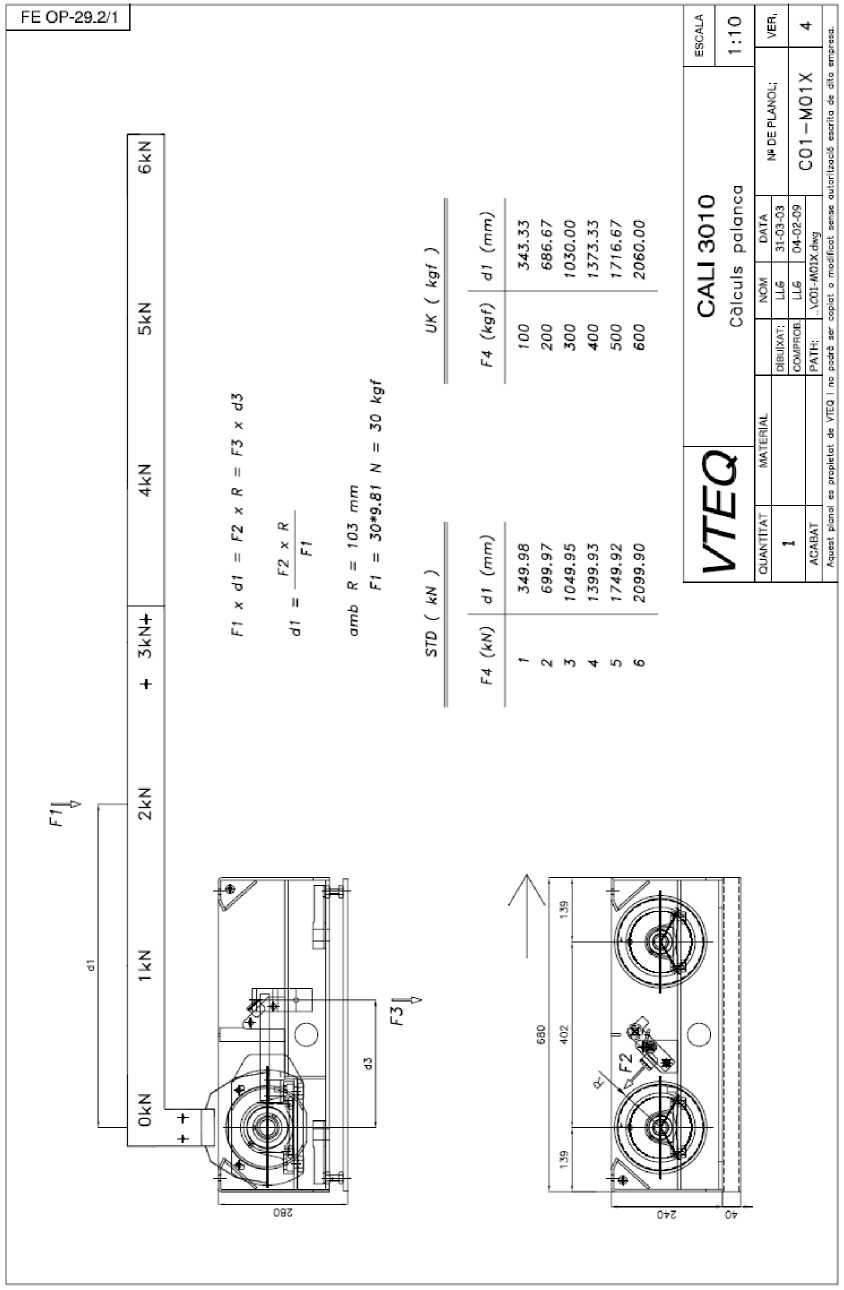
Чертеж калибровочного приспособления для стендов моделей BRAK 6000, BRAK 7000.
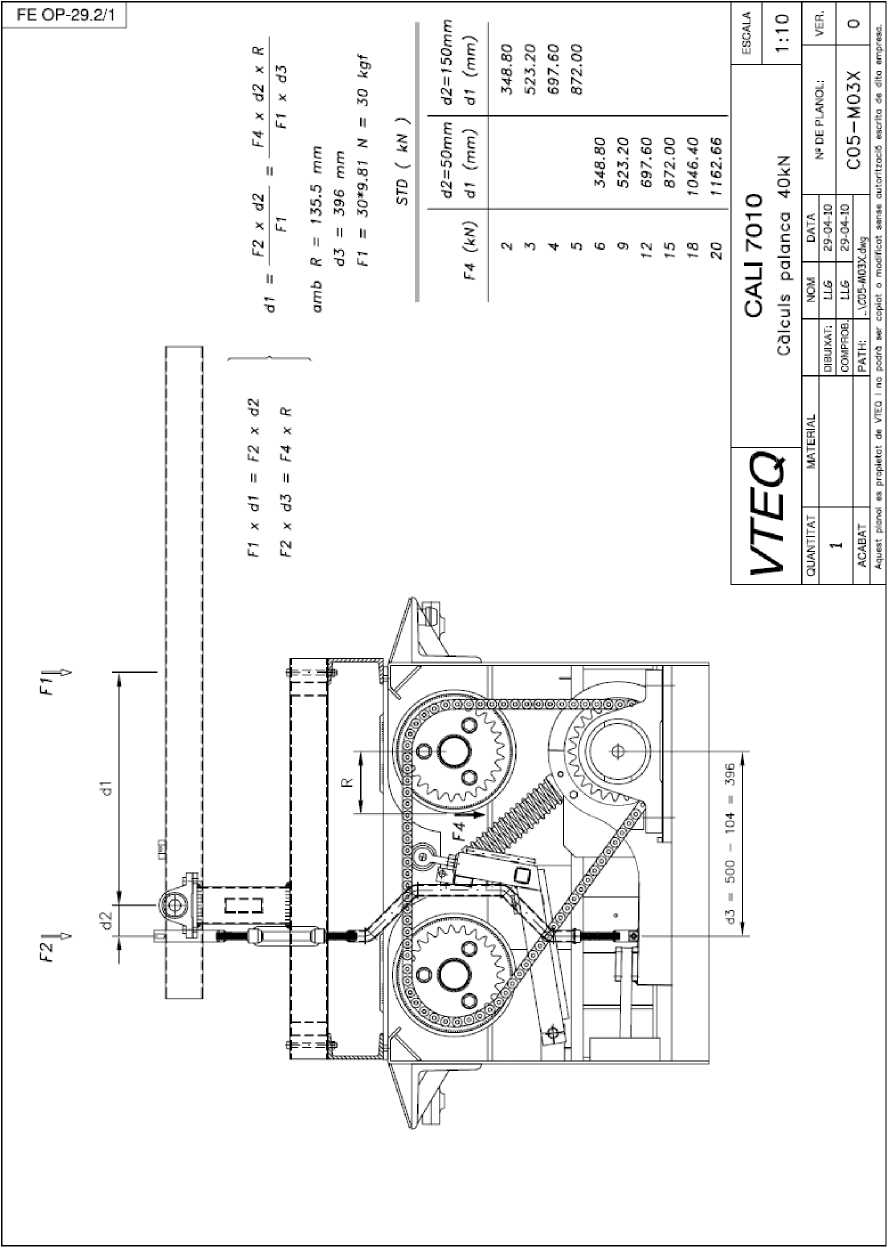
Приложение 2
Таблица 1
Определение погрешности измерений тормозной силы стендов тормозных BRAK
Модель стенда |
Заданное значение тормозной силы, кН |
Измеренное значение тормозной силы, кН |
Пределы допускаемой погрешности измерений тормозной силы, % (кН) | |
нагружение |
разгружение | |||
BRAK 1000 |
0 |
- | ||
1 |
±3 (±0,03) | |||
2 |
±3 (±0,06) | |||
3 |
±3 (±0,09) | |||
BRAK 2000, BRAK 2080, BRAK 3000, BRAK 3011, BRAK 3014, BRAK 3080 |
0 |
- | ||
1 |
±3 (±0,03) | |||
2 |
±3 (±0,06) | |||
3 |
±3 (±0,09) | |||
4 |
±3 (±0,12) | |||
5 |
±3 (±0,15) | |||
6 |
±3 (±0,18) | |||
BRAK 6000, BRAK 7000 |
0 |
- | ||
6 |
±3 (±0,18) | |||
9 |
±3 (±0,27) | |||
12 |
±3 (±0,36) | |||
15 |
±3 (±0,45) | |||
18 |
±3 (±0,54) | |||
24 (12 • 2) |
±3 (±0,72) | |||
30 (15 • 2) |
±3 (±0,90) | |||
36 (18 • 2) |
±3 (±1,08) | |||
40 (20 • 2) |
±3 (±1,20) |
Таблица 2а
Определение погрешности измерений массы автотранспортного средства (каждого колеса одной оси) стендов тормозных BRAK
Модель стенда |
Заданное значение массы, кг |
Измеренное значение массы каждого колеса одной оси, кг |
Пределы допускаемой погрешности измерений массы, % (кг) | |||
левого |
правого | |||||
нагружение |
разгру-жение |
нагружение |
разгру-жение | |||
BRAK 1000 |
50 |
±3 (±1) | ||||
100 |
±3 (±3) | |||||
200 |
±3 (±6) | |||||
400 |
±3 (±12) | |||||
600 |
±3 (±18) | |||||
BRAK 2000, BRAK 3000, BRAK 3011 |
250 |
±3 (±7) | ||||
500 |
±3 (±15) | |||||
750 |
±3 (±22) | |||||
1000 |
±3 (±30) | |||||
1500 |
±3 (±45) | |||||
BRAK 2080, BRAK 3014, BRAK 3080 |
650 |
±3 (±19) | ||||
1000 |
±3 (±30) | |||||
2000 |
±3 (±60) | |||||
2500 |
±3 (±75) | |||||
3000 |
±3 (±90) |
BRAK 6000, BRAK 7000 |
850 |
±3 (±25) | ||||
1500 |
±3 (±45) | |||||
3000 |
±3 (±90) | |||||
6000 |
±3 (±180) | |||||
9000 |
±3 (±270) |
Таблица 2б
Определение погрешности измерений массы автотранспортного средства (каждого колеса одной оси) стендов диагностирования подвески EUSUMA
Модель стенда |
Заданное значение массы, кг |
Измеренное значение массы каждого колеса одной оси, кг |
Пределы допускаемой погрешности измерений массы, % (кг) | |||
левого |
правого | |||||
нагружение |
разгру-жение |
нагружение |
разгру-жение | |||
EUSUMA 3000, EUSUMA 3012, EUSUMA 3013 |
250 |
±3 (±7) | ||||
600 |
±3 (±18) | |||||
1100 |
±3 (±33) | |||||
1600 |
±3 (±48) | |||||
2000 |
±3 (±60) |
Таблица 3
Определение погрешности измерений перемещения платформы стендов увода колеса SLIP
Модель стенда |
Заданное значение перемещения, мм |
Измеренное значение перемещения, мм |
Пределы допускаемой погрешности измерений перемещения | |
влево |
вправо | |||
SLIP 3000, SLIP 7000 |
0 |
±0,3 мм | ||
3 |
±0,3 мм | |||
8 |
±0,3 мм | |||
10 |
±3 % (±0,5 мм) | |||
15 |
±3 % (±0,7 мм) | |||
20 |
±3 % (±1,0 мм) |
13