Методика поверки «Дефектоскопы ультразвуковые SONOSCREEN ST10 » (МП АПМ 91-20 )
СОГЛАСОВАНО
Генеральный директор
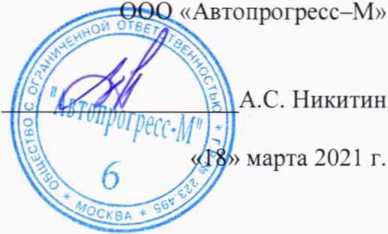
Государственная система обеспечения единства измерений
Дефектоскопы ультразвуковые SONOSCREEN ST10
МЕТОДИКА ПОВЕРКИ МП АПМ 91-20г. Москва
2021 г.
1 Общие положения
Настоящая методика поверки распространяется на дефектоскопы ультразвуковые SONOSCREEN ST 10. производства «SONOTEC GmbH», Германия (далее - дефектоскопы) и устанавливает методику их первичной и периодической поверки.
Выполнение всех требований настоящей методики обеспечивает прослеживаемость поверяемого средства измерений к следующим государственным первичным эталонам:
Выполнение всех требований настоящей методики обеспечивает прослеживаемость поверяемого средства измерений к следующим государственным первичным эталонам: ТЭТ 2-2021, ГЭТ 189-2014.
Интервал между поверками - 1 год.
-
2 Перечень операций поверки средств измерений
При проведении поверки средств измерений (далее - поверка) должны выполняться операции, указанные в таблице 1.
Таблица 1 - Операции поверки
Наименование операции |
№ пункта документа поверки |
Проведение операции при | |
первичной поверке |
периодической поверке | ||
Внешний осмотр средства измерений |
7 |
да |
да |
Подготовка к поверке и опробование средства измерений |
8 |
да |
да |
Идентификация программного обеспечения |
9 |
да |
да |
Определение метрологических характеристик |
10 |
- |
- |
Определение диапазона и относительной погрешности измерений толщины изделия (для стали) |
10.1 |
да |
да |
Определение диапазона и относительной погрешности измерений глубины залегания дефектов (для стали) |
10.2 |
да |
да |
Определение диапазона и относительной погрешности измерений координат залегания дефектов (для стали) |
10.3 |
да |
да |
3 Требования к условиям проведения поверки
При проведении поверки должны соблюдаться, следующие условия измерений:
- температура окружающей среды. °C 20±5.
4 Требования к специалистам, осуществляющим поверку
К проведению поверки допускаются лица, изучившие эксплуатационную документацию на дефектоскоп и средства поверки, и аттестованные в качестве поверителя средств измерений в установленном порядке.
5 Метрологические и технические требованиям к средствам поверки
При проведении поверки должны применяться эталоны и вспомогательные средства, приведенные в таблице 2.
Таблица 2
№ пункта документа по поверке |
Наименование эталонов, вспомогательных средств поверки и их основные метрологические и технические характеристики |
10.1: 10.2; 10.3 |
Рабочие эталоны единиц скоростей распространения и коэффициента затухания ультразвуковых волн в твердых средах 3-го разряда, согласно Государственной поверочной схемы для средств измерений скоростей распространения и коэффициента затухания ультразвуковых волн в твердых средах, утвержденной Приказом Госстандарта от 29 декабря 2018 г. № 2842 -меры для поверки толщиномеров, меры для поверки дефектоскопов |
Допускается применять другие средства поверки, обеспечивающие определение метрологических характеристик с точностью, удовлетворяющей требованиям настоящей методики.
6 Требования (условия) по обеспечению безопасности проведения поверки
При проведении поверки, должны соблюдаться требования по технике безопасности согласно эксплуатационной документации на дефектоскопы и поверочное оборудование, правила по технике безопасности, которые действуют на месте проведения поверки.
7 Внешний осмотр средства измерений
При внешнем осмотре должно быть установлено соответствие поверяемого дефектоскопа следующим требованиям:
-
- наличие маркировки (наименование или товарный знак фирмы-изготовителя, тип и заводской номер):
-
- комплектность дефектоскопов должна соответствовать руководству по эксплуатации:
-
- отсутствие механических повреждений и загрязнений дефектоскопа и ультразвуковых преобразователях, затрудняющих отсчет показаний и влияющих на их точность:
-
- наличие четких надписей и отметок на органах управления, разъемах и ультразвуковых преобразователях.
Если перечисленные требования не выполняются, дефектоскоп признают непригодным к применению, дальнейшие операции поверки не производят.
8 Подготовка к поверке и опробование средства измерений
-
8.1 Подготовка к поверке
Перед проведением поверки должны быть выполнены следующие подготовительные работы:
-
- средства измерений, применяемые при поверке должны иметь действующие свидетельства о поверке:
-
- выдержать дефектоскоп и средства поверки в условиях, соответствующих п. 3, не менее 1 часа;
-
- все части дефектоскопа должны быть очищены от пыли и грязи.
-
8.2 Опробование
При опробовании проверить работоспособность дефектоскопа с помощью комплекта образцовых ультразвуковых мер КМТ176М-1. Для этого нажать на клавишу включения дефектоскопа, дождаться загрузки программного обеспечения, провести измерение любой меры из диапазона измеряемой толщины, убедиться, что результат измерений отображается на экране дефектоскопа.
Если перечисленные требования не выполняются, дефектоскоп признают непригодным к применению, дальнейшие операции поверки не производят.
9 Идентификация программного обеспечения
-
9.1 Используя левый джойстик, выберите пункт меню «Установки устройства», далее подпункт «информация о системе». На экране дефектоскопа отобразится информация об установленном программном обеспечении (далее - ПО), как это показано на рисунке 1.
/•^формация о системе
HW
FPGA КВС СС
R08
122
1.5 0
6 0/4 0
1.3 <В1 0.6)
М/А
Device version ГЛк III Сериииыи номер 10216 ID устройства
00:00 17 18 E5 D2
Опции
АРК АРД. AWS
ОК
Рисунок 1 - Информация об установленном ПО Дефектоскоп считается выдержавшим проверку, если идентификационные данные соответствуют приведённым в таблице 3.
Таблица 3 - Идентификационные данные программного обеспечения
Идентификационные данные (признаки) |
Значение |
Идентификационное наименование ПО |
SONOSCREEN ST 10 |
Номер версии (идентификационный номер) ПО. не ниже |
1.2.0 |
Если перечисленные требования не выполняются, дефектоскоп признают непригодным к применению, дальнейшие операции поверки не производят.
10 Определение диапазона и относительной погрешности измерений толщины изделия, глубины и координат залегания дефектов (для стали)
-
10.1 Определение диапазона и относительной погрешности измерений толщины изделия (для стали)
Осуществляется с использованием прямых ПЭП и комплекта образцовых ультразвуковых мер КМТ176М-1.
-
10.1.1 Используя органы управления, выбрать соответствующий ПЭП из списка ПЭП.
-
10.1.2 Для раздельно-совмещенных преобразователей выбрать режим работы Р/С. Для этого выделить пункт меню «параметры измерения» и выбрать режим работы соответствующей кнопкой.
-
10.1.3 Используя левый джойстик выбрать пункт меню «измерения», далее «калибровка расстояния» (рисунок 2). Выбрать пункт «Выполнить калиб
Manual distance adiustme'
измерении
Рисунок 2 - Калибровка расстояния
-
10.1.4 Выбрать две меры из комплекта КМТ176М-1.
-
10.1.5 Ввести действительные значения толщины выбранных мер в пункт «1 отражатель» и «2 отражатель» с помощью соответствующих кнопок на передней панели дефектоскопа и джойстика.
1___ _________1_________________________________
.•-хр-ь «гонтосля
Параметр4 Настройка чувствитель Калибрационный блок
-
-
10.1.6 Выбрать пункт «Выполнить калибровку».
-
10.1.7 Установить преобразователь на выбранную меру с меньшим значением толщины.
-
10.1.8 Измерения проводить с помощью строба по второму пику, как это показано на рисунке 3.
Рисунок 3 - Установка строба
-
10.1.9 Установив строб на втором пике, нажать кнопку «1 отражение» на передней панели дефектоскопа.
-
10.1.10 Установить преобразователь на выбранную меру с большим значением толщины.
-
10.1.11 Повторить измерения в соответствии с п. 10.1.8.
-
10.1.12 Установив строб на втором пике, нажать кнопку «2 отражение» на передней панели дефектоскопа.
-
10.1.13 Нажать кнопку «готово» на передней панели дефектоскопа.
-
10.1.14 Выбирают пять мер толщины из комплекта КМТ176М-1. номинальные значения толщин мер должны быть равномерно распределены по диапазону измерений толщины изделия, соответствующих началу, середине и концу диапазона измерений данного датчика. Диапазон измерений для каждого датчика указан в паспорте на датчик.
-
10.1.15 Проводят пять измерений по второму пику (рисунок 2) для каждой выбранной меры.
-
10.1.16 Установить преобразователь на меру с номинальным значением толщины 100 мм из комплекта КМТ176М-1.
-
10.1.15 Установить диапазон измерения 7050 мм.
-
10.1.16 Установить строб на второй пик 69-го отражения (соответствует толщине 6900 мм) и записать показания дефектоскопа. Измеренное значение толщины соответствует диапазону измерения толщины изделия.
-
10.1.17 Результаты измерений записать в протокол.
-
10.2 Определение диапазона и относительной погрешности измерений глубины залегания дефектов (для стали)
Осуществляется с использованием прямых ПЭП и контрольного образца №2 из комплекта контрольных образцов и вспомогательных устройств КОУ-2.
-
10.2.1 Выполнить калибровку расстояния в соответствии с п.п. 10.1.1 - 10.1.13. За первое отражение принимают второй пик первого донного сигнала, за второе отражение принимают второй пик второго данного сигнала.
-
10.2.2 Установить преобразователь на контрольный образец, обработанный контактной смазкой, как показано на рисунке 4.
ПЭП
о
№ 2
О
о
Рисунок 4
-
10.2.3 Перемещая преобразователь по контрольному образцу получить наибольшую амплитуду сигнала на дефектоскопе от отверстия диаметром 6 мм. залегающего на глубине 41 мм (Нном).
-
10.2.4 Изменить усиление на дефектоскопе так. чтобы сигнал от дефекта занимал 80% экрана.
-
10.2.5 Установить строб на полученный сигнал и измерить глубину залегания дефекта.
-
10.2.6 Повторить измерение глубины залегания дефекта еще четыре раза, каждый раз заново устанавливая датчик на контрольный образец.
-
10.3 Определение диапазона и относительной погрешности измерений координат залегания дефектов (для стали).
Осуществляется с использованием контрольного образца №2 и №3 из комплекта контрольных образцов и вспомогательных устройств КОУ-2.
-
10.3.1 Подключить наклонный ПЭП к дефектоскопу.
-
10.3.2 Если ПЭП отсутствует в «Список датчиков», угол ввода УЗ волны преобразователя, стрелу и время задержки в призме взять из сертификата о калибровки ПЭП. Если на ПЭП отсутствует сертификат о калибровке, то определить точку ввода (стрелу) и у тол ввода датчика на контрольных образцах №3 и №2 из комплекта КОУ-2.
-
10.3.3 Определение точки ввода (стрелы) датчика:
-
- установить ПЭП на поверхность контрольного образца №3. обработанную контактной смазкой:
-
- перемещая ПЭП вперед-назад и поворачивая его вокруг оси на 5 - 10 угловых градусов, добиться максимального уровня эхо-сигнала от цилиндрической поверхности образца:
-
- метка «0» на образце контрольного образца №3. перенесенная на боковую поверхность ПЭП. указывает на точку ввода преобразователя. Стрела преобразователя расстояние отточки ввода до торца преобразователя (рисунок 5).
Рисунок 5 - Определение точки ввода (стрелы) датчика
-
10.3.4 Определение угла ввода ПЭП:
-установить ПЭП на поверхность контрольного образца №2. обработанную контактной смазкой:
-
- перемещая ПЭП вперед-назад по контрольному образцу и поворачивая его вокруг оси на 5 - 10 угловых градусов, получить на экране дефектоскопа эхо-сигнал максимальной амплитуды от цилиндрического бокового отражателя диаметром 6 мм:
-
- для ПЭП с углами ввода в диапазоне 40° - 60°, включительно, угол ввода определять по боковому цилиндрическому отражателю диаметром 6 мм. залегающему на глубине 44 мм. Для датчиков с углами ввода в диапазоне 60° - 75°. включительно, угол ввода определять по боковому цилиндрическому отражателю диаметром 6 мм. залегающему на глубине 15 мм.
-
- отсчет утла ввода ПЭП осуществлять по точке ввода датчика, определенной в п. 10.3.3:
-
- измерение утла ввода датчика следует повторить не менее трех раз. результат усреднить.
-
10.3.5 Поместив ПЭП на метку «0» контрольного образца №3 из комплекта КОУ-2, выполнить по п.п. 10.1.1 - 10.1.13 для данного датчика. За 1-е отражение принимают второй пик первого донного сигнала, за 2-е отражение принимают второй пик второго данного сигнала.
-
10.3.6 Установить преобразователь на контрольный образец №2 как показано на рисунке 5.
-
10.3.7 Перемещая ПЭП по контрольному образцу получить эхо-сигнал максимальной амплитуды от цилиндрического отражателя диаметром 6 мм. залегающего на глубине 44 мм. На рисунке 6 схематично изображено определение координат дефекта с помощью наклонного ПЭП и контрольного образца №2. На рисунке отмечено: 1 - наклонный ПЭП. 2 - контрольный образец №2. d - стрела преобразователя: а- угол ввода: L- расстояние от точки ввода датчика до проекции дефекта на поверхность: Н - глубина залегания дефекта: t - толщина образца.
d

Рисунок 6 - Определение координат дефекта при наклонном прозвучивании
-
10.3.8 Изменить усиление на дефектоскопе так. чтобы эхо-сигнал от дефекта занимал 80% экрана.
-
10.3.9 Установить строб дефектоскопа на второй пик сигнала от дефекта.
-
10.3.10 Определить глубину залегания дефекта (НИЗм, мм) и расстояние от точки ввода датчика до проекции дефекта на поверхность (L,nM, мм).
-
10.3.11 Повторить измерения еще четыре раза, каждый раз заново устанавливая датчик на контрольный образец и записать в протокол.
11 Подтверждение соответствия средства измерений метрологическим требованиям
-
11.1 Определение диапазона и относительной погрешности измерений толщины изделия (для стали)
-
11.1.1 Вычисляют средние значения измерений толщины по каждой измеренной мере. Относительную погрешность 6Ht измерений толщины изделия вычисляют по формуле:
-
8Н. = "изм ~ ■ 100% (1),
“НОМ
где Низм - среднее арифметическое значение толщины меры из пяти измерений дефектоскопа на /-ой мере, мм;
^ном" номинальное значение толщины меры, указанное в свидетельстве о ее поверке на меру, мм.
-
11.1.2 Дефектоскоп считается прошедшим поверку с положительным результатом, если относительная погрешность измерения толщины изделия для прямых датчиков не превышает ± 2% и определяется пик 69-го отражения на мере 100 мм.
-
11.2 Определение диапазона и относительной погрешности глубины и координат залегания дефектов (для стали) с использованием прямого ПЭП.
-
11.2.1 Рассчитать среднее арифметическое значение глубины залегания дефекта Низм и записать в протокол.
-
11.2.2 Вычислить относительную погрешность измерения глубины залегания дефекта ЗЩ по формуле 1.
-
где Низм - среднее арифметическое значение глубины залегания дефекта из пяти измерений дефектоскопа, мм:
#ном~ номинальное значение глубины залегания дефекта, указанное в свидетельстве о поверке контрольного образца.
-
11.2.3 Дефектоскоп считается прошедшим поверку с положительным результатом, если относительная погрешность измерения толщины изделия, глубины залегания дефектов для прямых датчиков не превышает ± 2%
-
11.3 Определение диапазона и относительной погрешности глубины и координат залегания дефектов (для стали) с использованием наклонного ПЭП.
-
11.3.1 По паспортным данным контрольного образца (координатам расположения дефекта относительно ребер и граней образца) и используя вычисленное значение угла ввода а (п. 10.3.4), по схеме на рисунке 5 вычислить номинальные значения ЬНом и ННОм.
-
11.3.2 Вычислить относительную погрешность измерения координат дефекта (L. Н) по формулам:
-
• 100% (2),
100% (3),
ном
где Ьнзм, Низм - измеренные средние арифметические значения, глубины залегания дефекта, расстояния отточки ввода датчика до проекции дефекта на поверхность, мм: Ьном, Ином - номинальные значения глубины залегания дефекта, расстояния от точки ввода ПЭП до проекции дефекта на поверхность, мм.
-
11.3.3 Дефектоскоп считается прошедшим поверку с положительным результатом, если относительная погрешность измерения толщины изделия, глубины и координат залегания дефектов для наклонных датчиков не превышает ± 2%.
Если перечисленные требования в п.п. 11.1; 11.2; 11.3 не
выполняются, дефектоскоп признают непригодным к применению.
12 Оформление результатов поверки
-
12.1 Результаты поверки оформляются протоколом, составленным в виде сводной таблицы результатов поверки по каждому пункту разделов 7-11 настоящей методики поверки.
-
12.2 Сведения о результатах поверки средств измерений в целях подтверждения поверки должны быть переданы в Федеральный информационный фонд по обеспечению единства измерений.
-
12.3 При положительных результатах поверки дефектоскоп признается пригодным к применению и по заявлению владельца средств измерений или лица, представляющего средства измерений на поверку выдается свидетельство о поверке установленной формы. Нанесение знака поверки на средство измерений не предусмотрено.
-
12.4 При отрицательных результатах поверки, дефектоскоп признается непригодным к применению и по заявлению владельца средств измерений или лица, представляющего средства измерений на поверку выдаётся извещение о непригодности установленной формы с указанием основных причин.
Руководитель отдела ООО «Автопрогресс-М»
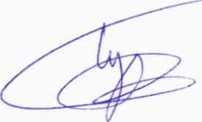
А.О. Бутаков