№1890 от 15.12.2016
Приказ Федерального агентства по техническому регулированию и метрологии (Росстандарт)
# 27007
Об утверждении информационно-технического справочника по наилучшим доступным технологиям "Производство никеля и кобальта" (ИТС 12-2016)
ФЕДЕРАЛЬНОЕ АГЕНТСТВО
ПО ТЕХНИЧЕСКОМУ РЕГУЛИРОВАНИЮ И МЕТРОЛОГИИ
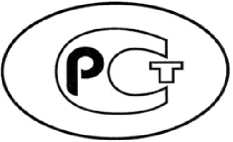
ИНФОРМАЦИОННО- | |
ТЕХНИЧЕСКИЙ |
ИТС |
СПРАВОЧНИК | |
П О НАИ ЛУЧ ШИ М |
12— |
ДОСТУПНЫМ |
2016 |
ТЕХНОЛОГИЯМ |
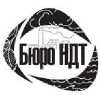
Москва
Бюро НДТ 2016
Раздел 1. Мировое состояние никель-кобальтовой промышленности
Раздел 2. Основные технологические процессы и оборудование,
применяемые в настоящее время при производстве никеля и кобальта в
Российской Федерации. Текущие уровни эмиссий
-
2.1 Производство никеля из сульфидных медно-никелевых
концентратов
Раздел 3. Определение наилучших доступных технологий
Раздел 4. Наилучшие доступные технологии
Раздел 5. Экономические аспекты применения наилучших доступных
технологий при производстве никеля и кобальта
Раздел 6. Перспективные технологии при производстве никеля и кобальта
-
6.2 Усовершенствование технологии гидрометаллургического
обогащения бедного никель-пирротинового концентрата
-
6.3 Производство никеля электроэкстракцией и рафинированием ПНТП
-
6.4 Производство никеля электроэкстракцией растворов
выщелачивания никелевого концентрата от разделения файнштейна
-
6.5 Технология производства карбонильного никеля с использованием
Заключительные положения и рекомендации
Приложение А (обязательное) Сфера распространения настоящего
Приложение Б (обязательное) Перечни маркерных веществ и
Приложение В (обязательное) Перечень НДТ
Приложение Г (обязательное) Энергоэффективность
ВведениеИнформационно-технический справочник по наилучшим доступным технологиям (далее — справочник НДТ) «Производство никеля и кобальта» разработан на основании анализа распространенных в Российской Федерации и перспективных технологий, оборудования, сырья, других ресурсов с учетом климатических, экономических и социальных особенностей Российской Федерации.
В соответствии с положениями Федерального закона от 10 января 2002 г. № 7 ФЗ «Об охране окружающей среды» [1] объекты, оказывающие воздействие на окружающую среду, подразделяются на четыре категории. Производство цинка, свинца и кадмия включено в I категорию и отнесено к областям применения наилучших до -ступных технологий (НДТ). Профильные предприятия рассматриваются как объекты, деятельность которых оказывает значительное негативное воздействие на окружающую среду и которые обязаны получать комплексные экологические разрешения на осуществление своей деятельности. Общая цель комплексного подхода к экологическому нормированию хозяйственной деятельности заключается в совершенствовании регулирования и контроля производственных процессов с целью обеспечения высокого уровня защиты окружающей среды. Хозяйствующие субъекты должны принимать все необходимые предупредительные меры, направленные на предотвращение загрязнения окружающей среды и рациональное использование ресурсов, в частности посредством внедрения НДТ, которые дают возможность обеспечить выполнение экологических требований.
Термин «наилучшие доступные технологии» определен в статье 1 Федерального закона № 7 ФЗ [1], согласно которому НДТ — это технология производства продукции (товаров), выполнения работ, оказания услуг, определяемая на основе современных достижений науки и техники и наилучшего сочетания критериев достижения охраны окружающей среды при условии наличия технической возможности ее применения.
Структура настоящего справочника НДТ соответствует ПНСТ 21—2014 [2], формат описания технологий — ПНСТ 23—2014 [3], термины приведены в соответствии с ПНСТ 22—2014 [4].
Краткое содержание справочникаВведение. Представлено краткое содержание справочника НДТ.
Предисловие. Указаны цель разработки справочника НДТ, его статус, законодательный контекст, краткое описание процедуры создания в соответствии с установленным порядком, а также взаимосвязь с аналогичными международными документами.
Область применения. Описаны основные виды деятельности, на которые распространяется действие справочника НДТ.
В разделе 1 представлена информация о мировом состоянии и уровне развития никель-кобальтовой промышленности — основных производителях и потребителях никеля и кобальта, рудной базе, применяемых при производстве технологических процессах, качестве товарной продукции.
В разделе 2 представлены сведения о технологических процессах , применяе -мых при производстве никеля и кобальта из руд и концентратов, дана оценка потребления энергоресурсов и уровней эмиссий в окружающую среду, характерных для производства никеля и кобальта в Российской Федерации.
Раздел подготовлен на основе данных, представленных предприятиями Российской Федерации в рамках разработки справочника НДТ, а также различных литературных источников.
В разделе 3 описаны особенности подходов, примененных при разработке данного справочника НДТ и в целом соответствующих Правилам определения технологии в качестве наилучшей доступной технологии, а также разработки, актуализации и опубликования информационно-технических справочников по наилучшим доступным технологиям (утверждены постановлением Правительства Российской Федерации от 23 декабря 2014 г. № 1458) и Методическим рекомендациям по определению технологии в качестве наилучшей доступной технологии (утверждены приказом Министерства промышленности и торговли Российской Федерации от 31 марта 2015 г. № 665).
В разделе 4 приведено краткое описание НДТ для производства никеля и ко -бальта, включая:
- системы экологического и энергетического менеджмента, контроля и монито -ринга технологических процессов;
- технические и технологические решения для повышения энергоэффективности , ресурсосбережения, снижения эмиссий загрязняющих веществ, методы обращения с отходами и побочными продуктами производства.
В разделе 5 приведены доступные сведения об экономических аспектах реали -зации НДТ на предприятиях Российской Федерации.
В разделе 6 приведены краткие сведения о новых технологических и техниче -ских решениях (не применяемых в России на момент подготовки справочника НДТ), направленных на повышение энергоэффективности, ресурсосбережения, снижение эмиссий загрязняющих веществ, эффективное обращение с отходами, промежуточными и побочными продуктами.
Заключительные положения и рекомендации. Приведены сведения о членах технической рабочей группы, принимавших участие в разработке справочника НДТ, и рекомендации предприятиям по дальнейшим исследованиям экологических аспектов их деятельности.
Библиография. Приведен перечень источников информации, использованных при разработке справочника НДТ.
ПредисловиеЦели, основные принципы и порядок разработки справочника НДТ установлены постановлением Правительства Российской Федерации от 23 декабря 2014 г. № 1458 «О порядке определения технологии в качестве наилучшей доступной технологии, а также разработки, актуализации и опубликования информационно-технических справочников по наилучшим доступным технологиям».
1 Статус документа
Настоящий справочник НДТ является документом по стандартизации.
2 Разработчик
Справочник НДТ разработан технической рабочей группой «Производство никеля и кобальта» (ТРГ 12), созданной приказом Росстандарта от 4 марта 2016 г. № 240 «О создании технической рабочей группы «Производство никеля и кобальта». Перечень организаций и их представителей, принимавших участие в разработке справочника НДТ, приведен в разделе «Заключительные положения и рекомендации».
Справочник НДТ представлен на утверждение Бюро наилучших доступных технологий (далее — Бюро НДТ) (www. burondt. ru).
3 Краткая характеристика
Справочник НДТ содержит описание применяемых при производстве никеля и кобальта технологических процессов, оборудования, технических способов, методов, в том числе позволяющих снизить эмиссии в окружающую среду, сократить водопотреб-ление, повысить энергоэффективность, обеспечить экономию ресурсов. Из числа описанных технологических процессов, технических способов, методов выделены решения, отнесенные к наилучшим доступным технологиям (НДТ). В справочнике НДТ установлены технологические показатели, соответствующие выделенным НДТ.
4 Взаимосвязь с международными , региональными аналогами
Справочник НДТ разработан на основе справочника Европейского союза (ЕС) по наилучшим доступным технологиям для предприятий цветной металлургии (Best Available Techniques (BAT) Reference Document for the Non-Ferrous Metals Industries) с учетом особенностей производства никеля и кобальта в Российской Федерации.
5 Сбор данных
Информация о технологических процессах, технических способах, методах, применяемых при производстве никеля и кобальта в Российской Федерации, была собрана в процессе разработки справочника НДТ в соответствии с Порядком сбора данных, необходимых для разработки информационно-технического справочника по наилучшим доступным технологиям и анализа приоритетных проблем отрасли, утвержденным приказом Росстандарта от 23 июля 2015 г. № 863.
6 Взаимосвязь с другими справочниками НДТ
Взаимосвязь настоящего справочника НДТ с другими справочниками НДТ, разрабатываемыми в соответствии с распоряжением правительства от 31 октября 2014 г. № 2178-р, приведена в разделе «Область применения».
7 Информация об утверждении и введении в действие
Настоящий справочник НДТ утвержден приказом Росстандарта от _____________ № _____.
Настоящий справочник НДТ введен в действие с 1 июля 2017 г., официально опубликован в информационной системе общего пользования — на официальном сайте Федерального агентства по техническому регулированию и метрологии в сети Интернет (www. gost. ru).
И НФОРМАЦИ ОННО-ТЕХНИ ЧЕСКИ Й СПРАВОЧНИ К ПО НАИ ЛУЧШИ М ДОС ТУПНЫМ ТЕХНОЛОГИ ЯМ
ПРОИЗВОДСТВО НИКЕЛЯ И КОБАЛЬТА
Production of nickel and cobalt
Дата введения — 2017-07-01
Область примененияНастоящий справочник НДТ «Производство никеля и кобальта» распространяется на процессы производства первичных никеля и кобальта, т. е. получаемых из рудного сырья.
Справочник НДТ также распространяется на процессы, связанные с основными видами деятельности по производству первичных никеля и кобальта, которые могут оказать влияние на объемы эмиссий и (или) масштабы загрязнения окружающей среды:
- хранение , подготовка и транспортировка сырья ;
- хранение и подготовка топлива , материалов , реагентов и продукции ;
- производственные процессы (пирометаллургические , гидрометаллургические ).
Справочник НДТ не распространяется на:
- добычу и обогащение никелевых и полиметаллических руд на месторождениях ;
- вопросы , которые касаются исключительно обеспечения промышленной без -опасности или охраны труда.
Вопросы обеспечения промышленной безопасности и охраны труда частично рассматриваются только в тех случаях, когда оказывают влияние на виды деятельности, включенные в область применения настоящего справочника НДТ.
Дополнительные виды деятельности при производстве никеля и кобальта, а также соответствующие им справочники НДТ (названия справочников НДТ даны в редакции распоряжения Правительства Российской Федерации от 31 октября 2014 г. № 2178-р) приведены в таблице ниже.
Вид деятельности |
Соответствующий справочник НДТ |
Методы очистки сточных вод, направленные на сокращение сбросов металлов в водные объекты |
ИТС 8-2016 Очистка сточных вод при производстве продукции (товаров), выполнении работ и оказании услуг на крупных предприятиях |
Методы очистки выбросов загрязняющих веществ в атмосферный воздух |
ИТС 22-2016 Очистка выбросов вредных (загрязняющих) веществ в атмосферный воздух при производстве продукции (товаров), а также при проведении работ и оказании услуг на крупных предприятиях |
Хранение и обработка материалов |
Сокращение выбросов загрязняющих веществ, сбросов загрязняющих веществ при хранении и складировании товаров (грузов) |
Промышленные системы охлаждения, например градирни, пластинчатые теплообменники |
ИТС 20-2016 Промышленные системы охлаждения |
Обращение с отходами |
ИТС 9-2016 Обезвреживание отходов термическим способом (сжигание отходов) ИТС 15-2016 Утилизация и обезвреживание отходов (кроме обезвреживания термическим способом (сжигание отходов) |
Выработка пара и электроэнергии на тепловых станциях |
Сжигание топлива на крупных установках в целях производства энергии |
Вопросы производственноэкологического контроля |
ИТС 22.1-2016 Общие принципы производственного экологического контроля и его метрологического обеспечения |
В настоящем справочнике использованы термины и определения в соответствии с ПНСТ 22—2014 ([4]).
Раздел 1. Мировое состояние никель-кобальтовой промышленности 1.1 Производство и потребление никеля и кобальтаМировое производство первичного никеля во всех видах в 2014 году, по данным Международной группы по изучению никеля (International Nickel Study Group — INSG), составило 1 994 тыс. т, в том числе 350 тыс. т никеля в ферроникеле и около 450 тыс. т никеля в никелистом чугуне ([5], [6]).
Под первичным никелем, по определению INSG, подразумевается продукция плавильных и рафинировочных заводов, пригодная для использования потребителями, в том числе:
- никель класса I с содержанием никеля 99 % и выше (электролитный никель — в виде полноразмерных или резаных катодов, гранулы, брикеты, порошки/хлопья, пеллеты, рондели);
- никель класса II c содержанием никеля менее 99 % (ферроникель , оксид нике -ля/синтер, ютилити-никель, никелистый чугун).
Отдельная группа включает химикаты на основе никеля.
На долю 10 крупнейших производителей пришлось почти 93 % мирового выпуска. Практически недосягаемым лидером является Китай, на который приходится более 1/3 мирового производства. Россия занимает второе место с долей в 12 % (таблица 1.1).
Таблица 1.1 — Производство никеля во всех видах в 2014 году по странам ([5], [6])
Страна |
Производство первичного никеля, тыс. т никеля |
Доля от мирового производства, % |
Китай |
688 |
34,5 |
Россия |
241 |
12,1 |
ЕС |
200 |
10,0 |
Япония |
185 |
9,3 |
Канада |
147 |
7,4 |
Австралия |
139 |
7,0 |
Бразилия |
84 |
4,2 |
Новая Каледония |
67 |
3,4 |
Колумбия |
41 |
2,1 |
Страна |
Производство первичного никеля, тыс. т никеля |
Доля от мирового производства, % |
ЮАР |
37 |
1,9 |
Прочие страны |
165 |
8,3 |
Мир в целом |
1 994 |
100,0 |
Мировое потребление первичного никеля во всех видах в 2014 году составило 1 863 тыс . т , из которых на долю первой пятерки стран — ведущих потребителей нике -ля пришлось 88 %. Безоговорочным лидером является Китай — более половины мирового потребления никеля, на Россию приходится менее 2 %, т. е. ~ 30 тыс. т (таблица 1.2).
Таблица 1.2 — Потребление первичного никеля во всех видах в 2014 году по странам ([5], [6])
Страна |
Потребление первичного никеля, тыс. т никеля |
Доля от мирового потребления, % |
Китай |
974 |
52,3 |
ЕС |
343 |
18,4 |
США |
158 |
8,5 |
Япония |
144 |
7,7 |
Южная Корея |
68 |
3,7 |
Россия |
31 |
1,7 |
Прочие страны |
145 |
7,7 |
Мир в целом |
1 863 |
100,0 |
Около 2/3 мирового потребления никеля приходится на сектор производства нержавеющей стали (рисунок 1.1). При этом структура потребления в отдельных странах может существенно отличаться от среднемировой. Так, в России, например, на производство нержавеющей стали приходится менее 1 / 3 от общего потребления никеля.
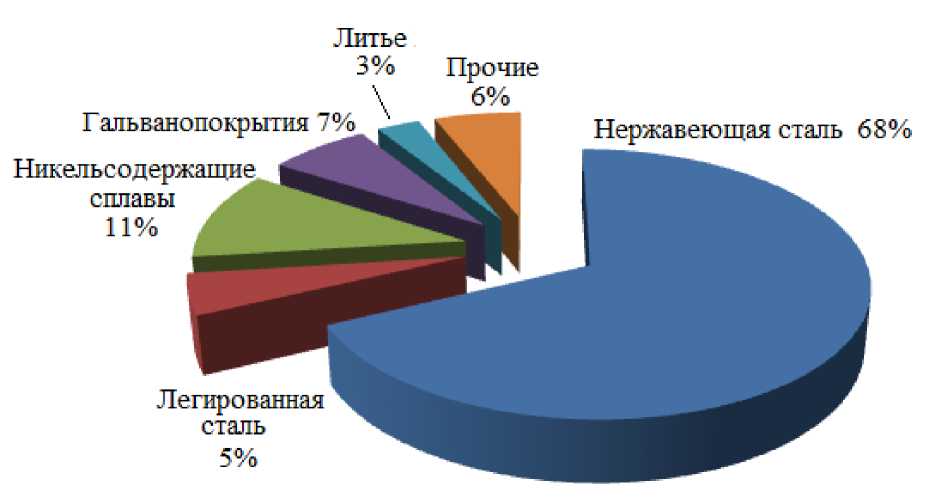
Легированная сталь
5%
Прочие
6%
Нержавеющая сталь 68%
Литье 3%
Гальванопокрытия 7%
Никельс о держащие сплавы 11% л
Рисунок 1.1 — Области потребления никеля в 2014 году (100 % = 1 863 тыс. т)
([7])
По Никелевому контракту Лондонской биржи металлов (ЛБМ) может быть поставлен первичный никель (т. е. произведенный из рудного сырья) в виде катодов (полноразмерных или резаных), дроби или брикетов, удовлетворяющий по химическому составу одному из двух стандартов: ASTM Standard Specification for Nickel B39-79 (2013) или GB/T 6516-2010 — Ni9990 grade (таблица 1.3).
Таблица 1.3 — Требования к составу первичного никеля, приведнные ASTM B39-79 (2013) и
GB/T 6516-2010 — Ni9990
Элемент, % масс. |
Стандарт ASTM |
Стандарт GB/T |
Сорт |
Ni9990 | |
Ni+Co |
Min 99,90 | |
Ni |
Min 99,80 | |
Co |
Max 0,15 |
Max 0,08 |
Cu |
Max 0,02 |
Max 0,02 |
C |
Max 0,03 |
Max 0,01 |
Fe |
Max 0,02 |
Max 0,02 |
S |
Max 0,01 |
Max 0,001 |
P |
<0,005 |
Max 0,001 |
Mn |
<0,005 | |
Si |
<0,005 |
Max 0,002 |
Элемент, % масс. |
Стандарт ASTM |
Стандарт GB/T |
As |
<0,005 |
Max 0,001 |
Pb |
<0,005 |
Max 0,0015 |
Sb |
<0,005 |
Max 0,0008 |
Bi |
<0,005 |
Max 0,0008 |
Sn |
<0,005 |
Max 0,0008 |
Zn |
<0,005 |
Max 0,002 |
Cd |
Max 0,0008 | |
Mg |
Max 0,002 |
Таблица 1.4 — Марки никеля, зарегистрированные на ЛБМ
Производитель |
Страна |
Марка |
Вид продукции* |
BHP Billiton Nickel West Pty Ltd |
Австралия |
BHP BILLITON NICKEL BRIQUETTES |
Б |
Minara Resources Pty Ltd |
MINARA HIGH GRADE NICK EL BRIQUETTES | ||
Votorantim Metais S.A. |
Бразилия |
TOCANTINS ** |
К, РК |
The Cobalt Refinery Company Inc |
Канада |
SHERRITT NICKEL BRI QUETTES |
Б |
Vale Canada Limited |
VALE ELECTROLYTIC NICKEL |
РК | |
VALE INCO |
К | ||
VALE NICKEL PELLETS |
Д | ||
Jiangxi Jiangli Sci-Tech Co., Ltd |
Китай |
GUORUN |
К |
Jinchuan Group Co., Ltd |
JINTUO GRADE 1 |
К, РК | |
Norilsk Nickel Harjavalta Oy |
Финляндия |
NORILSK NICKEL HARJAVALTA CATHODES |
К, РК |
NORILSK NICKEL HARJAVALTA BRIQUETTES |
Б | ||
Eramet S.A. |
Франция |
NICKEL HP |
К, РК |
Sumitomo Metal Mining Co., Ltd |
Япония |
SUMITOMO METAL MINING CO. LTD |
РК |
Производитель |
Страна |
Марка |
Вид продукции* |
SMM |
К | ||
Dynatec Madagascar S.A. |
Мадагаскар |
AMBATOVY NICKEL BRIQUETTES |
Б |
Glencore Nikkelverk AS |
Норвегия |
NIKKELVERK NICKEL |
К, РК |
PJSC MMC Norilsk Nickel |
Россия |
NORILSK COMBINE H-1 |
К, РК |
NORILSK COMBINE H-1Y |
К, РК | ||
JSC ‘'Kola GMK” |
SEVERONICKEL COMBINE H-1 |
К, РК | |
SEVERONICKEL COMBINE H-1Y |
К, РК | ||
Impala Platinum Ltd |
Южная Африка |
IMPALA NICKEL |
Б |
Rustenburg Platinum Mines Ltd |
RPM NICKEL |
К, РК | |
Vale Canada Limited/Vale Europe Limited |
Великобритания |
VALE NICKEL PELLETS |
Д |
RioZim Limited |
Зимбабве |
BCL EMPRESS ** |
К, РК |
* Б — брикеты; К — катоды ; РК — резаные катоды ; Д — дробь. ** Регистрация на ЛБМ не продлена. | |||
Ист.: ЛБМ |
Таблица 1.5 — Описание и химический состав некоторых марок никеля, зарегистрированных на ЛБМ (данные компаний)
8
Марки |
VALE ELECTROLYTIC NICKEL |
VALE INCO |
VALE NICKEL PELLETS |
GUORUN |
JINTUO GRADE 1 |
NICKEL HP |
NIKKELVERK NICKEL |
VALE NICKEL PELLETS |
Завод |
Thompson, Канада |
Thompson, Канада |
Copper Cliff, Канада |
Китай |
Китай |
Sandouville, Франция |
Nikkelverk, Норвегия |
Clydach, Британия |
Химический состав | ||||||||
Ni |
>99,91 |
>99,91 |
>99,98 |
>99,98 |
99,99 |
99,99 |
>99,98 |
>99,98 |
Со |
<0,06 |
<0,06 |
<0,00005 |
<0,007 |
0,005 |
<0,00009 |
<0,0002 |
<0,00005 |
Fe |
<0,0002 |
<0,0002 |
<0,001 |
<0,005 |
0,002 |
0,0009 |
<0,001 |
<0,01 |
C |
<0,0035 |
<0,0035 |
<0,007 |
<0,005 |
0,005 |
0,0021 |
<0,002 |
<0,015 |
S |
<0,0002 |
<0,0002 |
<0,0005 |
<0,001 |
0,001 |
<0,0003 |
<0,0002 |
<0,0005 |
Cu |
<0,001 |
<0,001 |
<0,0005 |
<0,0005 |
0,0015 |
<0,00012 |
<0,0001 |
<0,0005 |
Zn |
<0,0002 |
<0,0002 |
<0,00005 |
<0,001 |
0,001 |
<0,0001 |
<0,0002 |
<0,00005 |
Pb |
<0,0003 |
<0,0003 |
<0,00005 |
<0,0003 |
0,0003 |
0,00006 |
<0,0002 |
<0,00005 |
As |
<0,0013 |
<0,0013 |
<0,00005 |
<0,0008 |
0,0008 |
<0,00005 |
<0,00005 | |
Si |
<0,0005 |
<0,0012 |
0,001 |
<0,0005 | ||||
P |
<0,00005 |
<0,001 |
0,001 |
<0,0002 |
<0,00005 | |||
Cd |
<0,00005 |
<0,0003 |
0,0003 |
<0,00001 |
<0,00005 | |||
Sn |
<0,00005 |
<0,0003 |
0,0003 |
<0,00005 | ||||
Sb |
<0,00005 |
<0,0003 |
0,0003 |
<0,00005 | ||||
Bi |
<0,00005 |
<0,0003 |
0,0003 |
<0,00005 |
ИТС12-2016
9
Марки |
VALE ELECTROLYTIC NICKEL |
VALE INCO |
VALE NICKEL PELLETS |
GUORUN |
JINTUO GRADE 1 |
NICKEL HP |
NIKKELVERK NICKEL |
VALE NICKEL PELLETS |
Al |
<0,00005 |
<0,001 |
0,001 |
<0,00005 | ||||
Mn |
<0,00005 |
<0,001 |
0,001 |
<0,00005 | ||||
Mg |
<0,00005 |
<0,001 |
0,001 |
<0,00005 | ||||
O |
<0,007 |
<0,01 | ||||||
Вид продукции * |
РК |
К |
Д |
К |
РК, К |
РК, К |
РК, К |
Д |
Размеры |
25 х 25 мм, толщина — 15 мм |
72 х 103 см, толщина — 15 мм |
D <20 мм |
90 х 95 см, толщина — 3 / 5 мм |
К: 77 х 130 см, РК: 100 х 100, 50 х 50 мм, толщина — 13-15 мм |
К: 72 х 128 см РК: 25 х 25, 50 х 50, 100 х 100 мм |
D <20 мм | |
* К — катоды; РК — резаные катоды; Д — дробь. |
В дополнение к таблице 1.5 в таблице 1.6 приведено описание никелевой продукции зарубежных производителей , не зарегистрированной на ЛБМ.
ИТС 12-2016
10
Таблица 1.6 — Описание и химический состав никелевой продукции, не зарегистрированной на ЛБМ (данные компаний)
Pellets: |
Rounds: | ||||||
Завод/ Компания |
Copper Cliff/ Vale |
Clydach/ Vale |
Clydach/ Vale |
Thompson/ Vale |
Thompson/ Vale |
Thompson/ Vale |
Long Harbour/ Vale |
Наимен. |
Nickel P-Pellets |
Nickel P-Pellets |
Nickel S-Pellets |
Electrolytic Nickel S-Rounds |
Electrolytic Nickel R-Rounds |
Nickel Melt Rounds |
Nickel Melt Rounds |
Хим.состав | |||||||
Ni |
>99,98 |
>99,98 |
>99,97 |
>99,90 |
>99,90 |
Min 99,81 |
Min 99,81 |
Со |
<0,00002 |
<0,00002 |
<0,00002 |
<0,065 |
<0,08 | ||
Fe |
<0,0006 |
<0,004 |
<0,004 |
<0,0003 |
<0,0002 | ||
C |
<0,007 |
<0,011 |
<0,005 |
<0,0035 |
<0,0035 | ||
S |
<0,0001 |
<0,0002 |
~0,022-0,030 |
~0,019-0,025 |
<0,0002 | ||
Cu |
<0,00004 |
<0,0001 |
<0,0001 |
<0,0008 |
<0,0009 | ||
Zn |
<0,00002 |
<0,00002 |
<0,00002 |
<0,0002 |
<0,0002 | ||
Pb |
<0,000002 |
<0,00001 |
<0,000001 |
<0,0003 |
<0,0003 | ||
As |
<0,0015 |
<0,002 | |||||
Вид продукции |
Карбонил. дробь |
Карбонил. дробь |
Карбонил. дробь |
Электр. никель в виде «пуговиц» |
Электр. никель в виде «пуговиц» |
Электр. никель в виде «пуговиц» |
Электр. никель в виде «пуговиц» |
Размеры |
Диам =8-12 мм |
Диам.=8-12 мм |
Диам .=6-14 мм |
Диам.=25мм, толщина =6,5мм |
Диам.=23мм, толщина =8мм |
Диам.=22-25мм, толщина =6-10мм |
Диам.=25-29мм, толщина =5-6мм, вес 26-32г |
ИТС12-2016
11
Продолжение таблицы 1.6
Disks: |
Chips: | |||||||
Завод, Компания |
Copper Cliff, Vale |
Clydach,Vale |
Copper Cliff, Vale |
Clydach, Vale |
Jinhcuan/ Jinhcuan Group | |||
Наимен. |
Nickel Disks |
Nickel Disks |
Nickel Plating Chips |
Nickel Plating Chips |
Electrolytic Nickel Chips | |||
P-1 |
P-2 |
H-1 |
H-2 | |||||
Хим. состав | ||||||||
Ni |
Min 99,82 |
Min 99,82 |
>99,98 |
>99,98 |
>99,96* |
>99,9* |
>99,94* |
>99,9* |
Со |
<0,00002 |
<0,00002 |
0,02 |
0,08 |
0,02 |
0,08 | ||
Fe |
<0,0006 |
<0,004 |
0,01 |
0,02 |
0,01 |
0,02 | ||
C |
<0,007 |
<0,007 |
0,01 |
0,01 |
0,01 |
0,02 | ||
S |
<0,0001 |
<0,0001 |
0,001 |
0,001 |
0,02 |
0,02 | ||
Cu |
<0,00004 |
<0,0002 |
0,01 |
0,02 |
0,01 |
0,02 | ||
Zn |
<0,00002 |
<0,00002 |
0,0015 |
0,002 |
0,0015 |
0,002 | ||
Pb |
<0,000002 |
<0,000003 |
0,001 |
0,001 |
0,001 |
0,001 | ||
Si |
0,002 |
0,002 |
0,002 |
0,002 | ||||
Pb |
0,001 |
0,001 |
0,001 |
0,001 | ||||
As |
0,0008 |
0,001 |
0,0008 |
0,001 | ||||
Cd |
0,0003 |
0,0008 |
0,0003 |
0,0008 | ||||
Sn |
0,0003 |
0,0008 |
0,0003 |
0,0008 | ||||
Sb |
0,0003 |
0,0008 |
0,0003 |
0,0008 | ||||
Bi |
0,0003 |
0,0008 |
0,0003 |
0,0008 | ||||
Mg |
0,001 |
0,002 |
0,001 |
0,002 | ||||
Вид продукции |
Карбонильный Ni в виде дисков |
Карбонильный Ni в виде «похожем на диски» |
Электролитный Ni в виде «пуговиц» | |||||
Размеры |
диам.=14-18 мм, толщина 3,5-5,5мм |
диам.>11мм, толщина >5мм |
диам.=17-25мм, толщина =4-5мм |
диам.=18-22мм, тол щина =4-5мм |
* - Ni+Co
2 - по химическому составу превосходят следующие стандарты: ASTM B39, BS 375, R 99.5, NR9980, ISO 6283
ИТС 12-2016
12
Продолжение таблицы 1.6
Tonimet |
Utility |
Handy Nickel | ||||
Завод, Компания |
Matsusaka, Vale |
Kaohsiung, Onsan, Dalian, Vale |
Long Harbour, Vale |
Niihama, Sumitomo Metal Mining | ||
Наимен. |
Tonimet briquettes |
Tonimet compacts |
Utility Nickel |
Utility Rounds |
Handy-E |
Handy-S |
Хим. состав | ||||||
Ni |
~93 |
~97 |
>97 |
~97 |
>99,8 |
>99,9* |
Со |
~1,3 |
~1,3 |
~1,4 |
~2,4 |
<0,15 | |
Fe |
~0,6 |
~0,6 |
~0,7 |
~0,015 |
<0,02 |
<0,02 |
C |
~0,2 |
~0,005 |
<0,01 |
<0,010 | ||
S |
~0,003 |
~0,003 |
~0,1 |
~0,0005 |
<0,001 |
0,01-0,03 |
Cu |
~0,1 |
~0,1 |
~0,4 |
~0,090 |
<0,005 |
<0,005 |
Si |
~0,1 |
~0,001 |
<0,004 |
<0,005 | ||
P |
<0,001 |
<0,001 |
~0,005 |
~0,0001 | ||
Cr | ||||||
Mn |
<0,001 |
<0,001 | ||||
Pb |
<0,0015 |
<0,0015 | ||||
Вид прод-и |
Ni, рафинир. по собств. способу в виде гранул или брикетов |
Ni, рафинир. по собств. способу в виде «прессовок» цилиндрич. формы |
Ni, рафинир. по собств. способу в виде дроби |
Ni, рафинир. по собств. способу в виде «пуговиц» |
Электрол. Ni в виде «пуговиц» | |
Размеры |
Гранулы: 10-100 меш 0,2-0,4мм (60-90%) 0,4-0,9мм (10-40%) Брикеты: 20x30x15мм |
диамхвысота 25x15 мм |
3-80мм (>96%) |
диам.25-29мм, толщина 5-6 мм, вес 26-32 г |
Диаметр ~ 20 мм |
ИТС12-2016
* - Ni+Co
Продолжение таблицы 1.6
Завод, Компания |
Yabulu, Queensland Nickel |
Nikkelverk, Glencore |
Nikkelverk, Glencore | ||||
Наимен. |
Nickel Com pacts |
Hi Grade Nickel |
Crowns: |
Superelectro | |||
Crowns |
Microcrowns |
D-crowns |
D-Microcrowns | ||||
Хим.состав | |||||||
Ni |
>99,0 |
>99,45 |
>99,98 |
>99,98 |
>99,95 |
>99,95 |
>99,99 |
Со |
<0,06 |
<0,06 |
<0,0002 |
<0,0002 |
<0,0002 |
<0,0002 |
<0,0002 |
Fe |
<0,02 |
<0,02 |
<0,001 |
<0,001 |
<0,001 |
<0,001 |
<0,0005 |
C |
<0,01 |
<0,01 |
<0,002 |
<0,002 |
<0,002 |
<0,002 |
<0,0015 |
S |
<0,02 |
<0,01 |
<0,0002 |
<0,0002 |
<0,022 |
<0,02 |
<0,0002 |
Cu |
<0,01 |
<0,01 |
<0,0001 |
<0,0001 |
<0,0001 |
<0,0001 |
<0,0001 |
Zn |
<0,01 |
<0,01 |
<0,0002 |
<0,0002 |
<0,0002 |
<0,0002 | |
Pb |
<0,0002 |
<0,0002 |
<0,0002 |
<0,0002 |
Max 0,00010 | ||
Si |
<0,05 |
<0,05 | |||||
H |
<0,0003 | ||||||
- N |
<0,0002 | ||||||
' O |
<0,002 | ||||||
Ag |
Max 0,00010 | ||||||
Zn |
<0,0002 | ||||||
Mg |
<0,04 |
<0,04 | |||||
Al |
<0,02 |
<0,02 | |||||
Ca |
<0,03 |
<0,03 | |||||
Cr |
<0,001 |
<0,001 | |||||
Mn |
<0,06 |
<0,06 | |||||
Вид про-дукц. |
«Прессовки» цилиндрической формы |
Элетрол. Ni в виде «корон» |
Электрол. Ni в виде «микро-корон» |
Электрол. Ni с доб. S в виде «корон» |
Электрол. Ni c доб. S в виде «микро-корон» |
Электрол. Ni с пониженным сод-ем С в виде резанных квадратов | |
Размеры |
Цилиндр с 2мя плоск. Стенами Н=33 мм, D=33 мм |
D~20мм |
D~12 мм |
D~20мм |
D~12 мм |
50 Х 50 мм |
ИТС 12-2016
Мировое производство рафинированного кобальта, по оценкам Института развития кобальта (Cobalt Development Institute — CDI), составило в 2015 году 98 тыс. т, что на 6 тыс. т выше показателя 2014 года ([8]) (таблица 1.7).
Таблица 1.7 — Производство рафинированного кобальта в 2014-2015 годах, т
Компания/страна |
2014 |
2015 |
Китай (исключая производство Umicore в Китае) |
39 292 |
48 719 |
Freeport Cobalt, Финляндия (ранее OMG) |
11 452 |
8582 |
Glencore: Nikkelverk, Норвегия (ранее Falconbridge) |
3600 |
3100 |
Glencore: Katanga Mining, Демократическая Республика Конго |
2800 |
2900 |
Glencore: Minara, Австралия |
2900 |
3300 |
Umicore, Бельгия (включая производство в Китае) |
5850 |
6306 |
Chambishi Metals, Замбия (90 % ENRC) |
4317 |
2997 |
Sumitomo, Япония |
3654 |
4259 |
ICCI, Канада (Sherritt) |
3210 |
3733 |
Ambatovy, Мадагаскар (40 % Sherritt) |
2915 |
3464 |
Queensland Nickel, Австралия |
2519 |
1850 |
Норильский никель, Россия |
2302 |
2040 |
Vale, Канада (ранее Inco) |
2051 |
1858 |
CTT, Марокко |
1391 |
1722 |
Votorantim, Бразилия |
1350 |
1300 |
ЮАР |
1332 |
1300 |
Gecamines, Демократическая Республика Конго |
500 |
400 |
Eramet, Франция |
219 |
133 |
Индия (исключая Rubamin) |
100 |
150 |
Итого: |
91 754 |
98 113 |
Существенный вклад в предложение вносит вторичный кобальт — порядка 10 тыс. т/г, в том числе в США около 2,2-2,5 тыс. т. Однако оценки объемов его производства носят весьма приблизительный характер, так как многие предприятия перерабатывают как первичное, так и вторичное сырье, и разделить эти потоки не представляется возможным. В построении баланса рынка вторичный кобальт обычно не участвует.
По оценкам CDI, кажущееся потребление кобальта (производство + импорт и минус экспорт) составило около 82 тыс. т в 2014 году и 89 тыс. т в 2015 году ([8]).
Основная часть кобальта используется при производстве аккумуляторных батарей (46 %) и сплавов (18 % суперсплавы + 8 % твердые сплавы), причем уровень производства перезаряжаемых источников энергии и, соответственно, потребление кобальта неуклонно растут. Так, если в 1995 году оно оценивалось на уровне 700 т, то в 2014 году приблизилось к 40 тыс. т, т. е. составило почти половину от суммарного потребления кобальта (рисунок 3).
По требованиям ЛБМ поставляемый металл должен содержать не менее 99,3 % Со, что соответствует «низкосортному» кобальту. При этом максимальная концентрация примесей указывается в спецификации зарегистрированного на ЛБМ производителя. Производители «высокосортного» кобальта (99,8 % Со) получают премию к цене кобальта на ЛБМ. Однако и в рамках этой группы возможно различное содержание и номенклатура примесных элементов. Что касается формы, то по контракту ЛБМ может быть поставлен кобальт катодный (ломаные и резаные катоды), слитки, брикеты, гранулы и «таблетки» (таблицы 1.7, 1.8).
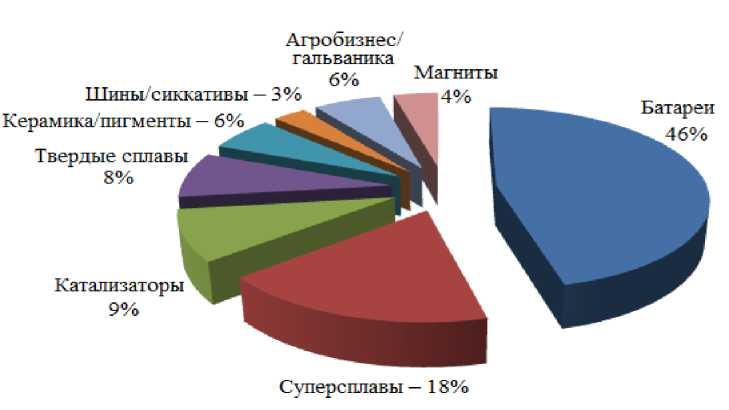
Катализаторы
9%
Агробизнес/ гальваника go/д Магниты
" 4%
Шины сиккативы — 3%
Керамика, пигменты —
Твердые гшавы ,
8% Л
Суперсплавы — 18%
Батареи
Рисунок 1.2 — Структура потребления кобальта в 2014 году (100 % = 82 тыс. т)
Таблица 1.8 — Марки кобальта, зарегистрированные на ЛБМ (по данным ЛБМ)
Производитель |
Страна |
Марка |
Вид продукции * |
Votorantim Metais S.A. |
Брази лия |
TOCANTINS ALLOY GRADE 99,8 % ** |
БК |
TOCANTINS CHEMICAL GRADE 99,7 % ** |
БК |
Производитель |
Страна |
Марка |
Вид продукции 1 |
TOCANTINS COBALT METAL GRADE 99,65 % 2 |
БК | ||
Vale Canada Limited |
Канада |
VALE ELECTROLYTIC COBALT ROUNDS |
ПГ |
Vale Inco Limited |
VALE INCO ELECTRO LYTIC COBALT ROUNDS 2 |
ПГ | |
Yantai Cash Industrial Co., Ltd. |
Китай |
CASH |
РК |
Jinchuan Group Co., Ltd |
GOLDEN CAMEL 9965 |
РК | |
GOLDEN CAMEL 9995 |
РК | ||
Sichuan Ni&Co Guorun New Materials Co., Ltd |
GUORUN |
ЛК | |
Jiangsu Cobalt Nickel Metal Co., Ltd. |
KLK 9995 |
РК | |
Ganzhou Yi Hao Umicore Industries Co.,Ltd. |
YHU 9995 |
РК | |
Nicomet Industries Ltd. |
Индия |
NICO |
РК |
Sumitomo Metal Mining Co., Ltd. |
Япония |
SMM CO 99,8 % |
РК |
CTT — Compagnie de Tifnout Ti-ranimine |
Марокко |
CMBA |
ЛК |
Kasese Cobalt Company Limited |
Уганда |
KCCL 2 |
ЛК |
Chambishi Metals Plc |
Замбия |
CMA |
ЛК |
Chambishi Metals Plc |
CMP |
ЛК | |
Mopani Copper Mines Plc |
MCM V9C 2 |
ЛК |
17
Марки |
VALE ELECTROLYTIC COBALT ROUNDS |
TOCANTINS ALLOY GRADE 99.8% |
SMM CO 99.8% |
GOLDEN CAMEL 9995 |
GOLDEN CAMEL 9965 |
KCCL |
KLK 9995 |
MCM V9B |
MCM V9C |
CASH |
Регистрация |
06.10.09 |
17.11.09 |
23.11.09 |
30.11.09 |
30.11.09 |
18.01.10 |
29.01.10 |
29.03.10 |
29.10.10 |
04.05.10 |
Хим. состав | ||||||||||
Al |
0,0002 |
0,0010 |
0,002 |
0,003 |
0,001 | |||||
As |
0,0002 |
0,0005 |
0,001 |
0,00002 |
0,0005 |
0,0003 | ||||
Bi |
0,0003 |
0,0003 |
0,0005 |
0,0003 | ||||||
C |
0,0050 |
0,0060 |
0,01 |
0,005 |
0,009 |
0,012 |
0,007 |
0,0050 |
0,010 |
0,005 |
Ca |
0,0010 |
0,005 | ||||||||
Cd |
0,0001 |
0,0020 |
0,0005 |
0,0003 |
0,001 |
0,005 |
0,0005 |
0,0020 |
0,0030 |
0,0003 |
Co |
99,8 |
99,80 |
99,8 |
99,95 |
99,65 |
99,8 |
99,95 |
99,65 |
99,60 |
99,95 |
Cr |
0,0010 |
0,005 | ||||||||
Cu |
0,0002 |
0,0030 |
0,01 |
0,003 |
0,02 |
0,02 |
0,006 |
0,0030 |
0,0050 |
0,004 |
Fe |
0,0008 |
0,0100 |
0,01 |
0,006 |
0,05 |
0,02 |
0,006 |
0,0050 |
0,010 |
0,005 |
Mg |
0,0010 |
0,002 |
0,005 |
0,002 |
0,0010 |
0,001 | ||||
Mn |
0,0005 |
0,0030 |
0,001 |
0,005 |
0,01 |
0,01 |
0,005 |
0,0010 |
0,0020 |
0,001 |
Ni |
0,1700 |
0,0800 |
0,15 |
0,002 |
0,2 |
0,08 |
0,008 |
0,25 |
0,33 |
0,005 |
P |
0,0005 |
0,001 |
0,001 |
0,002 |
0,001 | |||||
Pb |
0,0006 |
0,0020 |
0,001 |
0,0004 |
0,001 |
0,01 |
0,0005 |
0,0030 |
0,0050 |
0,001 |
S |
0,0010 |
0,0050 |
0,001 |
0,001 |
0,003 |
0,008 |
0,002 |
0,010 |
0,010 |
0,001 |
Sb |
0,0002 |
0,0003 |
0,005 |
0,0005 |
0,0003 | |||||
Se |
0,0001 | |||||||||
Si |
0,0010 |
0,001 |
0,003 |
0,003 |
0,001 | |||||
Sn |
0,0003 |
0,003 |
0,0005 |
0,00003 | ||||||
Zn |
0,0016 |
0,0025 |
0,005 |
0,002 |
0,002 |
0,01 |
0,003 |
0,0050 |
0,0070 |
0,001 |
O |
0,0080 |
0,03 | ||||||||
N |
0,0008 | |||||||||
H |
0,0004 |
0,008 | ||||||||
Вид продукции* |
ТБ |
ЛК |
РК |
РК |
РК |
ЛК |
РК |
ЛК |
ЛК |
ЛК |
ИТС 12-2016
18
Продолжение таблицы 1.9
Марки |
GUORUN |
MCM V9X |
NICO |
EVER STAR 99.98 |
EVER STAR 99.80 |
CMBA |
YHU 9995 |
TOCANTINS CHEMICAL GRADE 99.7% |
CMA |
CMP |
Регистрация |
15.11.10 |
22.11.10 |
22.11.10 |
18.01.11 |
18.01.11 |
26.04.11 |
07.03.12 |
29.06.12 |
29.08.13 |
29.08.13 |
Хим. состав | ||||||||||
Al |
0,002 |
0,001 |
0,002 |
0,0010 |
0,0020 |
0,0010 |
0,0010 | |||
As |
0,0008 |
0,0003 |
0,0005 |
0,0010 | ||||||
Bi |
0,0003 |
0,0002 |
0,0003 |
0,0010 | ||||||
C |
0,005 |
0,0150 |
0,001 |
0,004 |
0,005 |
0,0075 |
0,010 |
0,0100 |
0,0200 |
0,0100 |
Ca |
0,0050 |
0,0020 | ||||||||
Cd |
0,0004 |
0,0050 |
0,0020 |
0,0002 |
0,0003 |
0,0010 |
0,0010 |
0,0050 |
0,0050 |
0,0015 |
Co |
99,8 |
99,60 |
99,8 |
99,98 |
99,80 |
99,80 |
99,95 |
99,70 |
99,80 |
99,90 |
Cr |
0,0020 |
0,0020 | ||||||||
Cu |
0,004 |
0,0050 |
0,0050 |
0,001 |
0,003 |
0,0050 |
0,0080 |
0,0050 |
0,0050 |
0,0040 |
Fe |
0,006 |
0,010 |
0,01 |
0,003 |
0,006 |
0,010 |
0,010 |
0,0200 |
0,0100 |
0,0050 |
Mg |
0,002 |
0,0010 |
0,001 |
0,002 |
0,002 |
0,0010 |
0,0020 |
0,0030 |
0,0010 | |
Mn |
0,005 |
0,0030 |
0,0020 |
0,001 |
0,005 |
0,0050 |
0,0020 |
0,0300 |
0,0100 |
0,0020 |
Ni |
0,1 |
0,33 |
0,030 |
0,005 |
0,1 |
0,030 |
0,0030 |
0,1000 |
0,0500 |
0,0400 |
P |
0,001 |
0,001 |
0,001 |
0,0020 | ||||||
Pb |
0,0007 |
0,0070 |
0,0050 |
0,0003 |
0,0004 |
0,0050 |
0,0010 |
0,0030 |
0,0060 |
0,0040 |
S |
0,002 |
0,010 |
0,005 |
0,001 |
0,002 |
0,007 |
0,0030 |
0,0100 |
0,0050 |
0,0050 |
Sb |
0,0005 |
0,0002 |
0,0003 |
0,0010 | ||||||
Se | ||||||||||
Si |
0,003 |
0,001 |
0,003 |
0,0030 |
0,0020 |
0,0010 |
0,0010 | |||
Sn |
0,0003 |
0,0003 |
0,0003 |
0,0010 | ||||||
Zn |
0,002 |
0,010 |
0,0010 |
0,001 |
0,002 |
0,0050 |
0,0010 |
0,0050 |
0,0070 |
0,0050 |
O | ||||||||||
N | ||||||||||
H | ||||||||||
Вид продукции* |
ЛК |
ЛК |
РК |
РК |
РК |
ЛК |
РК |
ЛК |
ЛК |
ЛК |
ИТС12-2016
* - виды продукции: ЛК - ломанные катоды, РК - резанные катоды, ПГ - «пуговицы»
Содержание никеля в земной коре составляет около 0,01 %масс., однако количество пригодных для экономически эффективного извлечения металла промышленных месторождений ограничено.
Мировые запасы никеля в рудах оцениваются в 79 млн т. Выявленные наземные ресурсы никеля в рудах (таблица 1.9) составляют по крайней мере 130 млн т никеля, в том числе 60 % в латеритовых и 40 % в сульфидных месторождениях. Значительные ресурсы никеля сосредоточены также в глубоководных конкрециях.
Примерно десятая часть мировых запасов никеля сосредоточена в России (7,9 млн т). По этому показателю Россия занимает 4-е место в мире, уступая Австралии (19 млн т), Бразилии (10 млн т) и Новой Каледонии (8,4 млн т) (таблица 1.10) ([6], [10]).
Таблица 1.10 — Мировые запасы никеля, тыс. т
Страна |
Запасы |
Австралия |
19 000 |
Бразилия |
10 000 |
Новая Каледония |
8400 |
Россия |
7900 |
Куба |
5500 |
Индонезия |
4500 |
Южная Африка |
3700 |
Филиппины |
3100 |
Китай |
3000 |
Канада |
2900 |
Г ватемала |
1800 |
Мадагаскар |
1600 |
Колумбия |
1100 |
США |
160 |
Другие страны |
6500 |
Итого |
79 000 |
Мировые запасы кобальта, по оценкам US Geological Survey, составляют
7,1 млн т, а выявленные ресурсы — около 25 млн т (таблица 1.10). В дополнение к этому ресурсы кобальта в железомарганцевых конкрециях и корках на океанском дне оцениваются почти в 120 млн т.
Основными геолого-промышленными типами месторождений никеля и кобальта являются магматические сульфидные медно-никелевые, гипергенные силикатные никелевые коры выветривания и гидротермальные арсенидные и сульфоарсенидные никель-кобальтовые и собственно кобальтовые месторождения (таблица 1.11). Важнейшие промышленные минералы никеля (и кобальта) приведены в таблице 1.12.
Таблица 1.11 — Мировые запасы кобальта, тыс. т ([10], [11])
Страна |
Запасы |
Демократическая Республика Конго |
3400 |
Австралия |
1100 |
Куба |
500 |
Замбия |
270 |
Россия |
250 |
Филиппины |
250 |
Канада |
240 |
Новая Каледония |
200 |
Мадагаскар |
130 |
Китай |
80 |
Бразилия |
78 |
ЮАР |
31 |
США |
23 |
Прочие страны |
610 |
Итого |
7100 |
Таблица 1.12 — Содержание никеля и прочих компонентов в сульфидных и окисленных рудах *
([12]-[22])
Соде |
ржание, % |
Содержание, г/т | |||||
Компания/рудник |
Ni |
Cu Co |
Pt |
Pd |
Au |
прочие | |
Сульфидные руды: | |||||||
Vale (Садбери) |
1,19 |
1,50 |
0,04 |
0,9 |
1,0 |
0,4 | |
Vale (Манитоба) |
1,72 |
0,10 | |||||
Vale (Voisey's Bay) |
2,70 |
1,57 |
0,13 | ||||
BCL (Selebi-Phikwe) |
0,71 |
0,65 | |||||
Glencore (Raglan) |
3,04 |
0,76 |
0,06 |
0,84 |
1,96 | ||
Glencore (Садбери) |
1,42 |
1,61 |
0,03 |
0,85 |
0,92 | ||
Lundin (Eagle) |
2,9 |
2,4 |
0,1 |
0,64 |
0,43 |
0,25 |
Содержание, % |
Содержание, г/т | ||||||
Компания/рудник |
Ni |
Cu |
Co |
Pt |
Pd |
Au |
прочие |
BHP Billiton (Mt Keith) |
0,6 | ||||||
BHP Billiton (Leinster) |
1,3 | ||||||
Mirabela/Santa Rita |
0,52 |
0,13 |
0,015 |
MgO-27,2 | |||
Норильский никель (Талнах-ский узел) |
0,93 |
1,71 |
н/д |
1,12 |
4,21 |
0,24 | |
Норильский никель (Кольский п-в) |
0,59 |
0,28 |
н/д |
0,02 |
0,03 |
0,01 | |
Окисленные руды: | |||||||
Vale (Sorowako) |
1,79 |
Fe-21; SiO2-32; MgO-15 | |||||
Vale (Onca Puma) |
1,73 |
0,044 |
Fe-13; SiO2-39; MgO-24 | ||||
Vale (VNC (Goro)) |
1,46 |
0,11 |
MgO-4,64 | ||||
Glencore (MurrinMurrin) |
0,97 |
0,069 | |||||
Glencore (Koniambo) |
2,30 | ||||||
South32 (Cerro Matoso) |
1,1 | ||||||
Larco (Г реция) |
1-1,3 | ||||||
Sherritt (Moa Bay) |
1,15 |
0,12 |
44 Fe | ||||
Nickel Asia (сапролит) |
1,50 |
11,4Fe | |||||
Nickel Asia (лимонит) |
1,10 |
42 Fe | |||||
Antam (сапролит) |
1,8min |
25 Fe max | |||||
Antam (лимонит) |
1,2min |
>25 Fe | |||||
Sherritt (Ambatovy) |
0,84 |
0,07 | |||||
Южуралникель (Бурукталь-ское м-е) |
0,63 | ||||||
Уфалейникель (Серовское м-е) |
0,73 | ||||||
Южураникель (Сахаринское м-е) |
0,87 |
Таблица 1.13 — Важнейшие промышленные минералы никеля и кобальта ([23])
Название минерала и химическая формула |
Содержание, % | |
Ni |
Co | |
Сульфиды | ||
Пентландит (Fe, Ni)9S8 |
22-42 |
1-3 |
Никелистый пирротин FeS |
0,4-0,7 |
- |
Миллерит NiS |
61-64 |
0,1-0,5 |
Линнеит Co3S4 |
— |
40-53 |
Кобальтпирит (Fe, Co)S2 |
— |
0,05-3 |
Арсениды, сульфоарсениды и арсенаты | ||
Скуттерудит CoAs3 |
0-9 |
11-20 |
Саффлорит (Со, Fe)As2 |
0-0,3 |
10-30 |
Шмальтин - хлоантит (Со, Ni)As2 |
1-21 |
4-24 |
Кобальтин CoAsS |
0,5-2 |
26-34 |
Эритрин Co3(AsO4)2 • 8H2O |
0-6 |
20-30 |
Силикаты, гидросиликаты и гидроксиды |
Гарниерит (Ni, Mg)4[Si4Oio] (OH)4 • 4H2O |
16-35 |
0-0,1 |
Ревдинскит (Ni, Mg)8[Si4Oio] (ОН)8 |
16-35 |
0,0-0,1 |
Никелевый керолит (Mg, Ni)4[Si4Oio] (ОН)4 • 4Н2О |
10-15 |
Следы |
Нонтронит rn{Mg3[Si4Oio](OH)2} • p{(Al, Fe)2 • [Si4Oio] (ОН)2} |
0,5-2,0 |
Следы |
Никелевый серпофит (Mg, Ni, Fe)6[Si4Oio] (ОН)8 |
4-5 |
Следы |
Характерной особенностью сульфидных месторождений, сосредоточенных преимущественно на территории России и Канады, является сравнительно выдержанный минеральный состав руд. Главными минералами руд являются: пирротин, пентландит, халькопирит и магнетит. Руды содержат никель, медь, кобальт, платиноиды, а также селен и теллур, золото, серебро и серу. Месторождения описываемого типа являются ведущими в запасах и добыче никеля и кобальта в России.
В сульфидных рудах чаще всего основная часть никеля, по существу, встречается в виде минерала пентландита (Ni, Fe)9S8. Лишь небольшие количества никеля бывают представлены миллеритом NiS, виоларитом Ni2FeS4 и никельсодержащим пирротином (Fe, Ni)8S9. В рудах некоторых месторождений Австралии, например, существенная часть никеля представлена полидимитом Ni3S4. Пентландит всегда встречается вместе с другими сульфидными минералами, чаще всего с пирротином Fe8S9 и халькопиритом CuFeS2. Эти сульфидные минералы вмещает силикатная и алюмосиликатная порода. В таблице 1.13 приведен примерный минералогический состав некоторых сульфидных руд.
Таблица 1.14 — Минералогический состав некоторых сульфидных никелевых руд ([24])
Рудники |
Пентландит, % |
Халькопирит, % |
Пирротин, % |
Пустая порода, % |
Raglan |
8 |
2,4 |
11 |
79 |
Садбери (1) |
3,6 |
4,3 |
23 |
70 |
Садбери (2) |
3-6 |
2-5 |
20-30 |
Остальное |
Манитоба, Томпсон |
7 |
0,4 |
11 |
70 |
Большинство месторождений окисленных (латеритовых) руд, представляющих интерес для добычи, сосредоточено в экваториальном поясе: в Новой Каледонии, на Кубе, Мадагаскаре, Филиппинах, в Индонезии и др. Силикатные никелевые месторождения России играют подчиненную роль в запасах и добыче никеля и кобальта. Минеральный состав окисленных никелевых руд очень сложный: металлы распределены по многим минеральным формам и представлены как силикатными, так и оксидными и гидрокидными соединениями.
Двумя основными подтипами латеритовых руд, представляющих коммерческий интерес, являются лимониты и сапролиты. Лимониты обычно залегают ближе к поверхности, непосредственно под покрывающим пластом (зона феррикрета), ниже залегают сапролиты. Лимониты и сапролиты существенно различаются по составу. В целом в лимонитах содержание никеля (0,8 % — 1,5 %), магния (0 % — 5 % MgO) и кремнезема (0 % — 10 % SiO2) ниже, а железа (40 % — 50 %) и кобальта (0,10 % — 0,20 %) выше, чем в сапролитах. В случае если никель сосредоточен в основном в силикатной фазе сапролитовой зоны, латеритовое месторождение относят к «гарниеритовому типу», содержащему 1,8 % — 3,5 % Ni, 0,02 % — 0,08 % Co, 10 % — 25 % Fe, 15 % — 25 % MgO и 30 % — 50 % SiO2.
Чисто лимонитовая руда представляет собой в основном окислы (гидроокислы) железа, в то время как серпентинитовая руда представлена в основном сложными железо-магниевыми силикатами. В обеих разновидностях окисленных руд никель изоморфно замещает железо (и магний) в решётке, соответственно, окислов и силикатов (за очень редким исключением в таких рудах присутствуют собственно никелевые силикаты), поэтому окисленные руды не могут быть обогащены с применением обычных физических методов обогащения (флотации, гравитации и т. п.), как это имеет место при переработке сульфидных руд. Иногда производится рудоразборка с отбраковыванием крупных кусков — фазы, которая в ряде случаев существенно обеднена никелем (например, обогащение разделением по классам крупности было заложено в схему Cawse). Однако этот прием позволяет лишь незначительно обогатить сырье.
Почти половина мировых запасов кобальта сосредоточена в Демократической Республике Конго в многочисленных медно-кобальтовых месторождениях Медного пояса, тянущегося из Замбии через провинцию Катанга в юго-восточной части Демократической Республики Конго. Содержание кобальта в наиболее богатых зонах достигает 1 % — 2 %. Первичная минерализация — сульфидная; основные медьсодержащие минералы — халькопирит, халькозин Cu2S; кобальт преимущественно — в карролите (Cu(Co, Ni)2S4). Гипергенная (вторичная) минерализация ассоциирована с высокой степенью окисления минералов, залегающих вблизи поверхности (не глубже 100 м от поверхности). Медь и кобальт сосредоточены преимущественно в малахите Cu2CO3(OH)2 и гетерогените CoO(OH). Содержание кобальта обычно составляет 0,3 %, меди ~3 %.
На сегодняшний день богатые кобальтом месторождения так называемой первичной кобальтовой руды, или собственно кобальтовой руды, практически исчерпаны. Единственным рудником (подземным), где c 1928 года по сию пору ведут разработку, является рудник Bou-Azzer (Марокко) компании CTT Managem. Содержание кобальта в руде, включающей Co-Ni-Fe-арсениды и сульфоарсениды (главный промышленный минерал скуттерудит (Co, Fe, Ni)As2), а также сульфиды меди и молибденит — высокое, порядка 1 %.
Имеются проекты добычи и переработки мышьяковистой руды: проект Idaho Cobalt Project (США), где основными кобальт- и медьсодержащими минералами являются соответственно кобальтин CoAsS и халькопирит CuFeS2; проект NICO (Канада) компании Fortune Minerals, предусматривающий переработку Co-Bi-Cu-Au-руды, в которой основным кобальтсодержащим минералом является арсенопирит и др.
1.3 Добыча никеля и кобальтаНовых крупных сульфидных месторождений никеля, и тем более богатых, в последние годы не выявлено. Некоторые разрабатываемые десятилетиями месторождения сульфидной руды имеют ограниченный оставшийся срок эксплуатации.
В ретроспективе объем добычи никеля из сульфидных руд заметно превышал добычу из латеритовых руд, однако в последние годы доля сульфидного никеля в общем объеме добычи снизилась. Так, по данным Wood Mackenzie Ltd, общемировая горная добыча никеля в 2014 году составила 2042 тыс. т никеля, из которых 38,5 % пришлось на сульфидную руду и 61,5 % на окисленную. По данным же USGS (United States Geological Survey), горная добыча никеля была значительно больше и составила 2450 тыс. т, преимущественно за счет Филиппин и стран, отнесенных к категории «Прочие» (таблица 1.15).
Таблица 1.15 — Горная добыча никеля в 2014 году по странам
Страна |
По данным ([5]) |
По данным ([10]) | ||
Горная добыча, тыс. т никеля |
Доля от мировой добычи, % |
Горная добыча, тыс. т никеля |
Доля от мировой добычи, % | |
Филиппины |
417 |
20,4 |
523 |
21,3 |
Россия |
260 |
12,7 |
239 |
9,8 |
Канада |
225 |
11,0 |
235 |
9,6 |
Австралия |
210 |
10,3 |
245 |
10,0 |
Новая Каледония |
183 |
9,0 |
178 |
7,3 |
Индонезия |
179 |
8,8 |
177 |
7,2 |
Бразилия |
119 |
5,8 |
102 |
4,2 |
Страна |
По данным ([5]) |
По данным ([10]) | ||
Горная добыча, тыс. т никеля |
Доля от мировой добычи, % |
Горная добыча, тыс. т никеля |
Доля от мировой добычи, % | |
Китай |
105 |
5,1 |
100 |
4,1 |
Куба |
54 |
2,6 |
50,4 |
2,1 |
ЮАР |
52 |
2,5 |
55 |
2,2 |
Прочие страны |
238 |
11,7 |
571 |
23,3 |
Мир в целом |
2042 |
100,0 |
2450 |
100,0 |
По данным US Geological Survey3) мировая добыча кобальта в 2014-2015 годах составляла 123-124 тыс. т/год, причем примерно половина приходится на Демократическую Республику Конго (Киншаса). Дать более или менее надежную оценку объемов добычи кобальта сложно хотя бы потому, что из всего объема добытого вместе с никелем «латеритового» кобальта надо вычесть латериты, пошедшие на переработку, например в ферроникель, где кобальт теряется безвозвратно (таблица 1.16).
Таблица 1.16 — Горная добыча кобальта в 2015 году по странам, тыс. т ([10], [11])
Страна |
Добыча, тыс. т |
Демократическая Республика Конго |
63 |
Китай |
7,2 |
Канада |
6,3 |
Россия |
6,3 |
Австралия |
6,0 |
Замбия |
5,5 |
Филиппины |
4,6 |
Куба |
4,2 |
Страна |
Добыча, тыс. т |
Мадагаскар |
3,6 |
Новая Каледония |
3,3 |
Южная Африка |
2,8 |
Бразилия |
2,6 |
Прочие страны |
7,7 |
Мир в целом |
124 |
Технологические схемы переработки никелевых руд определяются их типом и особенностями химического состава. Так, если переработка сульфидных руд не отличается разнообразием (за исключением двух гидрометаллургических производств — Надежнинского металлургического завода в Норильске (Заполярный филиал ПАО «ГМК «Норильский никель», Россия) 4 и завода в Long Harbour (Vale, Канада), головными операциями технологической схемы являются пирометаллургические процессы, обеспечивающие получение медно-никелевого файнштейна), то схемы получения никеля из латеритов весьма рознятся между собой, как по типу и набору технологических операций, так и по виду конечной продукции. При этом наибольшее распространение имеет плавка окисленной никелевой руды на ферроникель, в меньшей степени распространены процессы высокотемпературного автоклавного выщелачивания и Карон-процесс (таблице 1.17). В настоящее время все шире применяется плавка окисленных никелевых руд на никелистый чугун (продукт, близкий по составу к ферроникелю), весьма широко востребованный при производстве нержавеющих сталей.
Таблица 1.17 — Основные никелевые предприятия мира (за исключением производителей никелистого чугуна и предприятий, перерабатывающих малосульфидные платиновые руды)
Владелец |
Технология |
Товарная продукция |
Месторасположение | |
Переработка сульфидного рудного сырья | ||||
1. |
Glencore |
Производство файнштейна |
Файнштейн |
Falconbridge, Канада |
Владелец |
Технология |
Товарная продукция |
Месторасположение | |
2. |
BCL Ltd. |
Производство файнштейна |
Файнштейн |
Selebi-Phikwe, Ботсвана |
3. |
Boliden |
Производство файнштейна |
Файнштейн |
Harjavalta, Финляндия |
4. |
Норильский Ни кель |
Производство файнштейна |
Файнштейн |
Никель, Россия |
5. |
Норильский Ни кель |
Производство файнштейна |
Файнштейн |
Норильск, Россия |
6. |
BHP Billiton |
Производство файнштейна |
Файнштейн |
Kalgoorlie, Австралия |
7. |
Vale |
Производство файнштейна, рафинированного никеля |
Карбонильный никель |
Sudbury, Канада |
8. |
Jinchuan Group |
Производство файнштейна, рафинированного никеля |
Никелевые катоды |
Jinchang (Gansu), Китай |
9. |
Vale |
Производство файнштейна, рафинированного никеля |
Никелевые катоды, рондели |
Thompson, Канала |
10. |
ASA Resource Group, Bindura Nickel Corp (BNC) |
Производство рафинированного никеля |
Никелевые катоды, медный сульфидный концентрат, гидроксид кобальта |
Зимбабве |
11. |
Vale |
Автоклавная переработка сульфидных Cu-Ni-руд с получением рафинированных Cu, Ni и Co |
Никелевые, медные и кобальтовые катоды |
Long Harbour, Канада |
Переработка латеритовых руд | ||||
12. |
Glencore |
Производство ферроникеля |
Ферроникель |
Bonao, Доминиканская Республика |
13. |
Anglo American |
Производство ферроникеля |
Ферроникель |
West of Caracas, Венесуэла |
Владелец |
Технология |
Товарная продукция |
Месторасположение | |
14. |
BHP Billiton |
Производство ферроникеля |
Ферроникель |
Монтелибано, Колумбия |
15. |
Vale |
Производство ферроникеля |
Ферроникель |
Ourilandia do Norte, Бразилия |
16. |
Posco |
Производство ферроникеля |
Ферроникель |
Gwangyang, Корея |
17. |
Sumitomo |
Производство ферроникеля |
Ферроникель |
Hyuga (Kyushu), Япония |
18. |
Nippon Yakin |
Производство ферроникеля |
Ферроникель |
Miyazu (Honshu), Япония |
19. |
Pacific Metals |
Производство ферроникеля |
Ферроникель |
Hachinohe (Honshu), Япония |
20. |
Hyuga Smelting Co. |
Производство ферроникеля |
Ферроникель |
Miyazaki, Япония |
21. |
Antam |
Производство ферроникеля |
Ферроникель |
Pomalaa (Sulawesi), Индонезия |
22. |
Glencore |
Производство ферроникеля |
Ферроникель |
Koniambo, Новая Каледония |
23. |
Eramet (Le Nickel) |
Производство ферроникеля |
Ферроникель |
Noumea, Новая Ка ледония |
24. |
Larco |
Производство ферроникеля |
Ферроникель |
Larymna, Греция |
25. |
Feni Industries |
Производство ферроникеля |
Ферроникель |
Kavadarci, Македония |
26. |
Побужский ферроникеле-вый комбинат |
Производство ферроникеля |
Ферроникель |
Побужье, Украина |
27. |
Уфалейникель (остановлен) |
Производство ферроникеля |
Ферроникель |
В. Уфалей, Россия |
28. |
Режникель (остановлен) |
Производство ферроникеля |
Ферроникель |
Реж, Россия |
29. |
Южуралникель (остановлен) |
Производство ферроникеля |
Ферроникель |
Орск, Россия |
Владелец |
Технология |
Товарная продукция |
Месторасположение | |
30. |
Sherritt |
Высокотемпературное сернокислотное выщелачивание |
Никель-кобальт- сульфидный концентрат |
Moa Bay, Куба |
31. |
Nickel Asia |
Высокотемпературное сернокислотное автоклавное выщелачивание |
Ni-Co-сульфидный концентрат |
Coral Bay, Филиппины |
32. |
Sumitomo |
Высокотемпературное сернокислотное выщелачивание |
Ni-Co-сульфидный концентрат |
Manila, Филиппины |
33. |
Ramu NiCo Management (MCC) Ltd |
Высокотемпературное сернокислотное выщелачивание |
Смешанные Ni-Co-гидроксиды |
Basamuk, Папуа- Новая Гвинея |
34. |
First Quantum Minerals Ltd. |
Высокотемпературное сернокислотное выщелачивание + атмосферное выщелачивание |
Смешанные гидроксиды |
Ravensthorpe, Австралия |
35. |
Wingstar investments pty ltd (остановлен) |
Высокотемпературное сернокислотное выщелачивание |
Смешанные гидроксиды (карбонаты) |
Cawse, Австралия |
36. |
Vale |
Высокотемпературное сернокислотное выщелачивание |
Синтер, CoCO3 |
Goro, Новая Кале дония |
37. |
Ambatovy (Sher-ritt, Sumitomo, Korea Resources) |
Высокотемпературное сернокислотное автоклавное выщелачивание |
99,8 % Ni, 99,8 % Co |
Toamasina, Мадагаскар |
38. |
Glencore |
Высокотемпературное сернокислотное выщелачивание + кучное выщелачивание |
Никелевый порошок, никелевые брикеты |
Murrin-Murrin, Австралия |
Владелец |
Технология |
Товарная продукция |
Месторасположение | |
39. |
Wingstar invest ments pty ltd (остановлен) |
Высокотемпературное сернокислотное выщелачивание |
Никелевые катоды, сульфид кобальта |
Avalon, Австралия |
40. |
Кубинское правительство |
Карон-процесс |
Синтер, Ni-Co-сульфидный концентрат |
Punta Gorda, Куба |
41. |
Кубинское правительство |
Карон-процесс |
Синтер |
Nicaro, Куба |
42. |
Queensland Nickel |
Карон-процесс |
99,5 % Ni, ChemGrade Cobalt |
Townsville, Австралия |
43. |
Votorantim Metals (остановлен) |
Карон-процесс |
Н. д. |
Niquelandia, Бразилия |
44. |
Votorantim Metals (остановлен) |
Производство файнштейна |
Файнштейн |
Fortaleza de Minas, Бразилия |
45. |
Vale |
Производство файнштейна из латеритов |
Файнштейн |
Sorowako (Sulawesi), Индонезия |
Рафинировочные предприятия | ||||
46. |
Sherritt |
Производство рафинированного никеля |
Н. д. |
Ft. Saskatchewan, Канада |
47. |
Glencore |
Производство рафинированного никеля |
Никелевые катоды |
Kristiansand, Норвегия |
48. |
Eramet |
Производство рафинированного никеля |
Никелевые катоды |
Sandouville, Франция |
49. |
Sumitomo |
Производство рафинированного никеля |
Никелевые катоды, соли |
Niihama (Shikoku), Япония |
Владелец |
Технология |
Товарная продукция |
Месторасположение | |
50. |
Норильский Ни кель |
Производство рафинированного никеля |
Никелевые катоды, брикеты, соли |
Harjavalta, Финляндия |
51. |
Норильский Ни кель |
Производство рафинированного никеля |
Никелевые катоды, карбонильный никель |
Мончегорск, Россия |
52. |
BHP Billiton |
Производство рафинированного никеля |
Никелевый порошок, никелевые брикеты |
Kwinana, Австралия |
53. |
Vale |
Производство рафинированного никеля |
Карбонильный никель |
Clydach, Уэльс |
54. |
Vale |
Производство рафинированного никеля |
Синтер, брикеты |
Matsuzaka (Honshu), Япония |
55. |
Votorantim Metals (остановлен) |
Рафинирование файнштейна |
Sao Paulo, Бразилия | |
Н. д. — нет данных. |
1.4.1 Переработка латеритовых руд с получением богатых промышленных продуктов или товарных металлов
Латеритовые Ni-Co-руды перерабатывают пирометаллургическими методами (плавка на ферроникель, никелистый чугун или штейн), гидрометаллургическими методами (сернокислотное автоклавное выщелачивание, иногда в комбинации с атмосферным и кучным выщелачиванием) и комбинированными методами, сочетающими приемы пиро- и гидрометаллургии (например, аммиачное выщелачивание по методу М. Карона). Выбор метода в значительной степени определяется химическим и минералогическим составом руды. Так, для переработки Mg-гидросиликатного подтипа руды почти в % случаев применяется плавка. Напротив, для переработки железооксидного подтипа используются преимущественно гидрометаллургические способы, включая метод Карона (рисунок 1.3).
Среднее содержание (%) | ||||
Ni |
Co |
Fe |
MgO | |
Красный лимонит |
<0.8 |
<0.1 |
>50 |
<0.5 |
Желтый лимонит |
0.8 to 1.5 |
0.1 to 0.2 |
40 to 50 |
0.5 to 5 |
Переходный тип |
1.5 to 4 |
0.02 to 0.1 |
25 to 40 |
5 to 15 |
Сапролит/ Гарниерит/ Серпентин |
1.8 to 3 |
10 to 25 |
15 to 35 | |
Невыветре-лая порода |
0.3 |
0.01 |
5 |
35 to 45 |
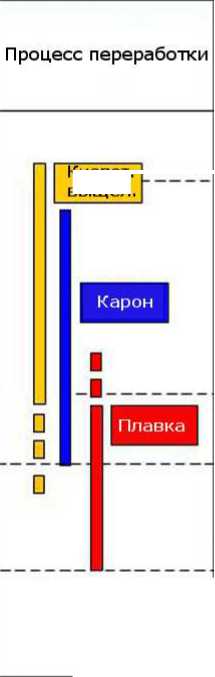
Кислот, вышел.
Рисунок 1.3 — Вертикальный разрез месторождения тропических
Ni-Co-латеритов ([26])
Плавка латеритовой никелевой руды на ферроникель, никелистый чугун, штейн за рубежом
Совместное присутствие в латеритах никеля и железа создает предпосылки для получения железосодержащих никелевых продуктов, пригодных для производства нержавеющих сталей — ферроникеля и никелистого чугуна.
Сырьем для производства ферроникеля служит преимущественно сапролит (%: Ni — 1,5-3; Co — 0,04-0,08; Fe — 15; SiO2-40; MgO — 25), позволяющий из-за пониженного по сравнению с лимонитом содержания железа при меньших производственных затратах получать ферроникель заданного состава ([24]).
Технологический процесс включает в себя сушку руды, обжиг, восстановление оксидов никеля и железа в электропечах с получением чернового ферроникеля и его рафинирование, обеспечивающее удаление серы и фосфора. Своеобразным стандартом отрасли стал процесс RKEF (rotating kiln — electric furnace), включающий в себя обжиг во вращающейся печи (‘RF') и восстановительную плавку в электропечи (‘EF'). В типичном случае готовый ферроникель содержит 20 % — 40 % Ni.
Производство никелистого чугуна (НЧ) началось в Китае в 2005 году как реакция на высокие цены на никель и уже к 2014 году получило весьма широкое распространение. К этому времени никелистый чугун стал покрывать до 52 % потребности в никеле китайских производителей нержавеющей стали.
Использование для производства НЧ стандартных доменных печей позволяло получать продукт весьма низкого качества с небольшим содержанием никеля и высоким — примесей, пригодный для производства нержавеющей стали серии. Замена их электропечами обеспечила содержание никеля в НЧ на уровне 10 % — 15 % Ni, что сделало его пригодным для производства нержавеющих сталей серии 300.
С 2011 года началось быстрое развитие производства НЧ по хорошо известной технологии производства ферроникеля RKEF. Такой никелистый чугун, как по составу, так и по способу производства практически ничем не отличается от обычного ферроникеля. Содержание никеля в нем достигает 20 % и более, вредных примесей меньше, а издержки ниже, чем при плавке в домне.
Несмотря на всю привлекательность непосредственного производства никельжелезных сплавов, часть латеритовой руды перерабатывается по схеме с получением никелевого штейна (Vale на заводе Sorowako, Индонезия, и Eramet на заводе Doniambo, Новая Каледония).
На заводе Sorowako компании Vale производительностью порядка 80 тыс. т год по никелю окисленную руду последовательно подвергают сульфидирующему обжигу с использованием элементарной серы, плавке на никелевый штейн (~26 % Ni) и конвертированию в конвертерах Пирса — Смита с получением файнштейна с ~78 % Ni.
Основную часть (80 %) гранулированного файнштейна Vale отправляет на рафинировочный завод Matsuzaka (Япония), часть — продает компании Sumitomo для рафинирования на заводе Niihama (Япония) совместно со смешанными сульфидами, полученными на двух своих заводах на Филиппинах, перерабатывающих латеритовую руду способом автоклавного сернокислотного выщелачивания.
На заводе Doniambo (Новая Каледония) компании Le Nickel-SLN, входящей в группу Eramet, окисленная (гарниеритовая) руда плавится на ферроникель в электропечи. Основная часть ферроникеля поставляется потребителям в качестве товарного продукта, а часть — сульфидируется элементарной серой с получением файнштейна и передается на завод компании Sandouville (Франция) для производства рафинированных никеля и кобальта (металлический никель высокой чистоты (>99,97 %), хлорид и карбонат никеля, хлорид кобальта).
Переработка окисленных никелевых руд в России осуществляется с получением товарного огневого никеля на комбинате Уфалейникель. Ввиду убыточности комбинаты Южуралникель и Режский никелевый завод остановлены.
Гидрометаллургическая переработка латеритовых руд
Высокотемпературное сернокислотное автоклавное выщелачивание (HPAL) является вторым по распространенности в мире процессом, предназначенным для производства никеля из окисленных никелевых руд, и обеспечивает возможность извлечения в товарную продукцию до 90 % и более никеля и основную часть кобальта.
Технология реализована на двух заводах компании Sherrit на Кубе и Мадагаскаре, а также предприятиях Sumitomo (Coral Bay) на Филиппинах, Vale (Goro) в Новой Каледонии, Glencore и First Quantum Minerals Ltd (MurrinMurrin и Ravensthorpe 5 соответственно) в Австралии, Ramu NiCo Management (MCC) Ltd (Basamuk) в Папуа-Новой Гвинее. Заводы Cawse и Avalon компании Wingstar investments pty ltd в Австралии, принадлежавшие до 2014 года различным компаниям (в том числе ПАО «ГМК «Норильский никель»), в настоящее время законсервированы (таблица 1.17).
Процесс HPAL — это процесс, в котором никель и кобальт из латеритовой руды выщелачиваются серной кислотой при высоких давлении (~40 ат) и температуре (230 °C — 240 °С). Из раствора выщелачивания после очистки его от примесей либо осаждают смешанные сульфиды или гидроксиды никеля и кобальта, либо ведут процесс с использованием жидкостной экстракции и электроэкстракции до получения металлических никеля и кобальта. Последнее характерно для относительно новых предприятий.
Гидрометаллургическая технология получения никеля и кобальта с использованием процесса Карона (восстановительный обжиг с последующим аммиачным выщелачиванием) позволяет перерабатывать лимонитовую руду или смесь лимонитов с сапролитами, при этом с увеличением относительной доли сапролита извлечение никеля и кобальта снижается. По сравнению с процессом автоклавного кислотного выщелачи -вания (HPAL) применение процесса Карона экономически оправдано для переработки руды с более высоким содержанием магния (примерно до 8 %). Однако в этой технологии извлечение никеля и особенно кобальта существенно ниже, чем в HPAL.
35
Предприятие |
Страна |
Производительность, т/год |
Тип руд |
Содержание, % |
Извлечение при выщелачивании, % |
Товарная продукция | ||
Ni |
Co |
Ni |
Co | |||||
Moa Bay |
Куба |
33000 |
Л |
1,3 |
0,14 |
96 |
96 |
Ni-Co-сульфид-ный концентрат |
Murrin Murrin |
Австралия |
40000 |
Л, СМ |
1,2 |
0,08 |
Н. д. |
Н. д. |
Никелевый порошок, никелевые брикеты |
Coral Bay |
Филиппины |
20000 |
Л |
1,3 |
0,03 |
95 |
95 |
Ni-Co-сульфид-ный концентрат |
Goro |
Новая Кале дония |
60000 |
Л, С. |
Н. д. |
Н. д. |
Н. д. |
Н. д. |
Синтер, CoCO3 |
Ambatovy |
Мадагаскар |
60000 |
М |
1,3 |
0,11 |
97 |
97 |
99,8 % Ni, 99,8 % Co |
Ramu |
Папуа-Новая Гвинея |
31000 |
Н. д. |
Н. д. |
Н. д. |
Н. д. |
Н. д. |
Смешанные Ni-Co-гидро- ксиды |
Taganito |
Филиппины |
30000 |
Н. д. |
Н. д. |
Н. д. |
Н. д. |
Н. д. |
Ni-Co-сульфид-ный концентрат |
ИТС 12-2016
Предприятие |
Страна |
Производительность, т/год |
Тип руд |
Содержание, % |
Извлечение при выщелачивании, % |
Товарная продукция | ||
Ni |
Co |
Ni |
Co | |||||
Gordes (проектируется (?) нет данных о вводе в эксплуатацию) |
Турция |
10000 |
Н. д. |
Н. д. |
Н. д. |
Н. д. |
Н. д. |
Н. д. |
Ravensthorpe * |
Австралия |
Н.д. |
Л, С |
Н. д. |
Н. д. |
96 |
96 |
Смешанные Ni-Co-гидро-ксиды |
C — сапролит; СМ — смектит; Л — лимонит; М — смешанный тип; Сил — силикатная Со-руда.
* Используется процесс EPAL — сочетание автоклавного (PAL) и атмосферного выщелачивания (AL).
ИТС12-2016
В настоящее время процесс Карона применяется на трех действующих заводах : Nicaro, Punta Gorda (оба на Кубе) и Yabulu (Австралия). Завод Sao Miguel Paulista (Бразилия) из-за низких цен на никель на неопределенное время остановлен (таблица 1.19).
Таблица 1.19 — Показатели извлечения никеля и кобальта и способы их извлечения из аммиачно-карбонатных растворов на предприятиях, использующих Карон-процесс
Nicaro, Куба |
Punta Gorda, Куба |
Yabulu, Townsville, Австралия |
Sao Miguel Paulista, Бразилия | |
Ввод в эксплуатацию |
1941 |
1990 |
1974 |
1981 |
Извлечение, % | ||||
Ni |
75 |
84 |
80 | |
Co |
40 |
40 |
50 | |
Товарная продукция |
Синтер, Ni-Co-сульфидный концентрат |
ChemGrade Cobalt |
Катодный никель, катодный кобальт | |
Способ выделения металлов | ||||
Ni |
Отгонкой аммиака в виде основного карбоната |
Жидкостная экстракция, реэкстракция, отгонка аммиака с получением основного карбоната Ni, прокалка, восстановление водородом |
Осаждение основных карбонатов Ni и Co, растворение в H2SO4, электроэкстракция |
Nicaro, Куба |
Punta Gorda, Куба |
Yabulu, Townsville, Австралия |
Sao Miguel Paulista, Бразилия | |
Co |
(NH4)2S в виде смешанных Ni-Co-сульфидов перед выделением Ni |
H2S в виде сульфида из никелевого рафината, доводка до Co металлического |
Экстракционное выделение из Ni-Co-раствора, электроэкстракция |
В 2010-2011 годах компания Direct Nickel презентовала технологию переработки латеритов в азотнокислой среде с регенерацией азотной кислоты и запустила демонстрационную пилотную установку. Одним из элементов установки был агрегат для термического разложения, в который подается моногидрат нитрата магния, а образуется MgO в виде порошка и выделяются газы NOx, проходящие через серию абсорберов и скрубберов, в которых извлекается 99 % окислов азота и получается 55 %-ная азотная кислота. Работа демонстрационной установки показала возможность регенерации более 95 % азотной кислоты и извлечения никеля и кобальта в гидратный продукт — более 90 %. Однако, несмотря на высокие показатели эффективности, на сегодняшний день информация о коммерческом использовании технологии отсутствует.
Следует упомянуть и о таком направлении, как хлоридное выщелачивание. Исследования возможности переработки латеритовых руд в солянокислой среде идут с 70-х гг. Среди компаний, активно ведущих разработки в области хлоридной технологии, следует упомянуть: BHP Billiton (разработавшую процесс хлоридного кучного выщелачивания), Jaguar Nickel, Nichromet Solutions Inc, Intec Ltd, Anglo American (процесс Anglo Research Nickel — ARNi) и др. Однако ни один из перечисленных процессов пока не достиг стадии коммерческого внедрения.
1.4.2 Переработка сульфидных руд с получением файнштейна
Никельсодержащие сульфидные руды, в отличие от окисленных, поддаются флотационному обогащению. Так, из руды, содержащей 1 % — 3 % Ni, получают концентрат с 7-20+ % Ni. Технологическая схема включает в себя дробление, измельчение и флотацию. В зависимости от состава руды, в частности соотношения меди и никеля, используются различные схемы.
При небольшом содержании в руде халькопирита реализуется процесс коллективной флотации с получением Ni-Cu-концентрата, при значительном (массовое соотношение Cu : Ni >0,3) — производится разделение на никелевый (медно-никелевый) и медный концентраты. На Талнахской обогатительной фабрике ЗФ ПАО «ГМК «Норильский Никель», перерабатывающей сплошные сульфидные руды, осуществлялось также выделение никелистого пирротина в отдельный, так называемый пирротиновый концентрат.
Наиболее распространенной практикой переработки никелевых сульфидных концентратов является штейновая плавка, которая может быть реализована либо в автогенных агрегатах (печь взвешенной плавки), либо в руднотермических электропечах. Полученный штейн конвертируют с получением файнштейна, который затем рафинируют гидрометаллургическим (весь мир) или комбинированным способом (Россия6) с получением товарных металлов (рисунок 1.4).
40
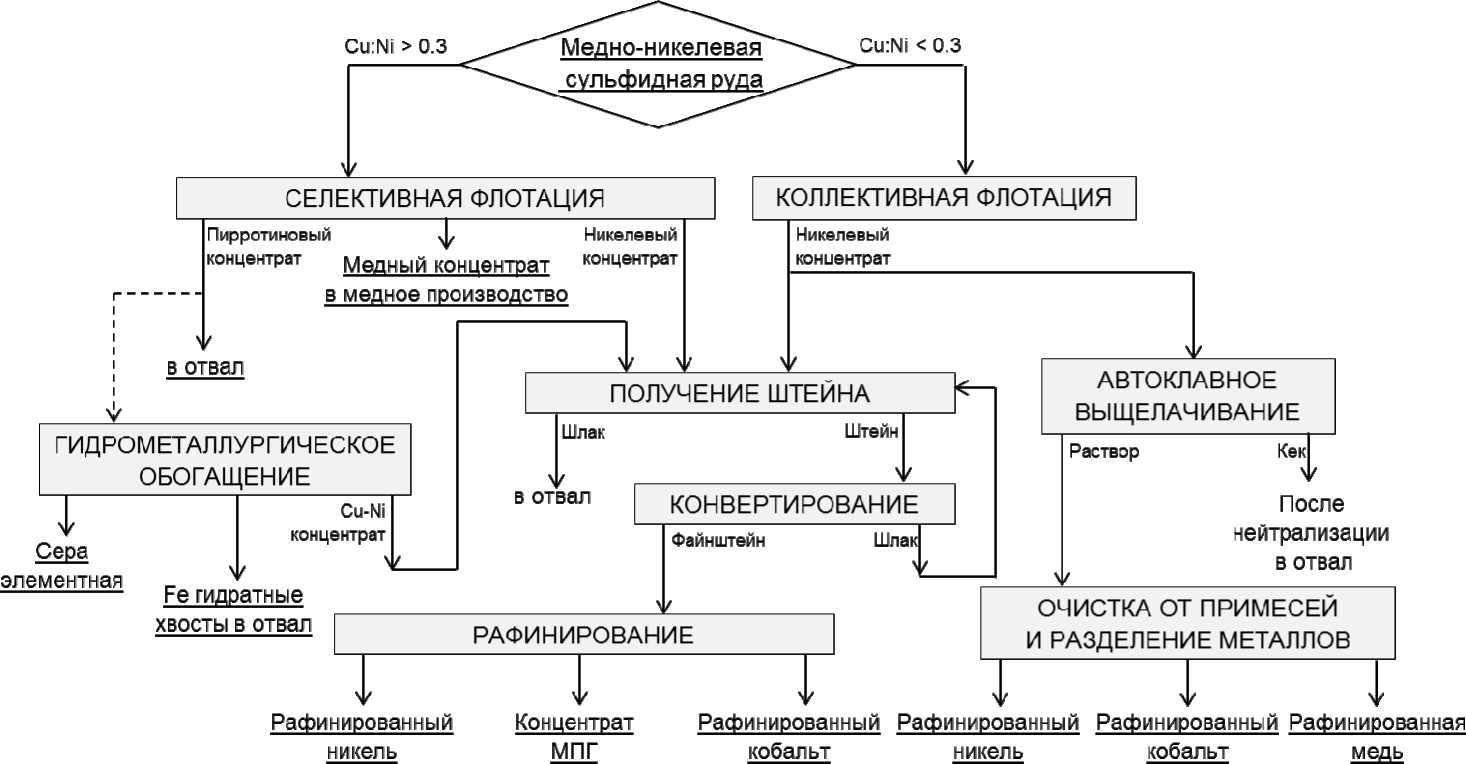
Рисунок 1.4 — Принципиальная схема переработки сульфидных медно-никелевых руд
ИТС12-2016
Главным преимуществом пирометаллургической головной переработки материала является возможность практически количественного концентрирования (за исключением серебра) присутствующих в сульфидных медно-никелевых рудах драгоценных металлов.
Для руд, не содержащих драгоценных металлов (медно-никелевые руды месторождения Voisey's Bay), возможна гидрометаллургическая переработка с тотальным вскрытием сульфидной составляющей и получением медно-никель-кобальтового раствора, пригодного для дальнейшей переработки с получением катодных рафинированных металлов и отвального кека, пригодного после нейтрализации для захоронения.
Следует также остановиться на переработке пирротиновых никельсодержащих концентратов, прямая пирометаллургическая переработка которых ввиду низкого содержания ценных компонентов экономически нецелесообразна 7. Процедура гидрометаллургического обогащения, реализованная на Надеждинском металлургическом заводе ЗФ ПАО «ГМК «Норильский Никель», с выводом в отдельные продукты основной части серы в элементарной форме, а железа — в гидратной делает данный получаемый сульфидный концентрат весьма привлекательным для извлечения из него ценных компонентов (никеля, кобальта, меди, драгоценных металлов) стандартными пирометаллургическими способами.
Производство штейна
Головной операций пирометаллургической переработки никельсодержащих руд и концентратов является плавка на штейн.
К наиболее старым вариантам реализации процесса относится плавка предварительно обожженных и окускованных концентратов или кусковой руды в отражательных или шахтных печах. Такие процессы характеризовались относительно низкой удельной производительностью, высоким расходом кокса и повышенными потерями ценных компонентов с отвальными шлаками из-за присущей минералам пустой породы медно-никелевых руд тугоплавкости. Данные обстоятельства, а также стремительное развитие электроэнергетики привели к достаточно быстрому вытеснению этих процессов значительно более эффективной и менее «капризной» электроплавкой, которая, в свою очередь, также постепенно заменяется плавкой в автогенных печах.
До недавнего времени электроплавка предварительно обожженного никелевого (медно-никелевого) концентрата применялась на пяти заводах (в том числе двух, расположенных на территории Российской Федерации)8 9, перерабатывающих никелевое (никель-медное) сульфидное сырье. В никель-платиновой подотрасли руднотермическая плавка повсеместно используется и по сей день, при этом из-за низкого содержания серы материал не обжигают, а после сушки непосредственно подают в электропечь (таблицы 1.19-1.20).
Несмотря на то, что процесс электроплавки является довольно старым, он имеет ряд неоспоримых преимуществ, а именно:
-
- возможность переработки малосульфидного высокомагнезиального сырья за счет способности электропечи обеспечивать высокие температуры шлаковых расплавов;
-
- возможность переработки конвертерных шлаков и прямого получения отвальных по цветным и драгоценным металлам шлаков, не требующих специального обеднения.
Именно эти обстоятельства и обусловливают повсеместное применение руднотермических печей для плавки платиносодержащих концентратов. Даже при содержании в шлаке оксида магния на уровне 13 % — 23 % за счет поддержания высокой температуры шлаковой ванны удается обеспечить чрезвычайно низкие потери цветных и драгоценных металлов (потери драгоценных металлов пропорциональны потерям меди, так как никель может присутствовать в шлаках не только в виде корольков, но и в растворенной форме) (таблица 1.20 7).
К недостаткам процесса следует отнести высокий удельный расход электроэнергии (который может быть несколько снижен при загрузке в печь горячего огарка, как это реализовано на канадских заводах), практически полное отсутствие возможности управления степенью десульфуризации в процессе плавки и выходом штейна (данные показатели регулируются степенью удаления серы на стадии предварительного обжига), а также получение большого объема бедных по сернистому ангидриду газов, утилизация которых затруднена.
На действующих на сегодняшний день предприятиях, использующих схему окислительный обжиг-электроплавка, флотационный концентрат обжигают в печах кипящего слоя (КС) (таблица 1.20) как в наиболее эффективном обжиговом агрегате с удалением основного количества серы в газовую фазу. Содержания SO2 в отходящих газах на уровне 5 % — 15 % (по объему) вполне достаточно для использования в сернокислотном производстве, а интенсивный массобмен в агрегате обеспечивает высокую удельную производительность.
Таблица 1.20 — Обжиг концентратов на никелевых заводах, работающих по технологии обжиг/электроплавка [24], [27])
Садбери, Канада, Glencore |
Томпсон, Канада, Vale (по 2018 год) | |
Ввод в строй |
1978 г. |
1961 г. |
Печи: | ||
Тип и число обжиговых печей |
2 печи КС |
2 печи КС |
Внутрутренние размеры каждой печи, м |
Диаметр слоя — 5,6 м, диаметр надслоевого пространства — 8 м |
Диаметр слоя — 5,5 м, диаметр надслоевого пространства — 6,4 м, высота над фурмами — 6,5 м |
Номинальная мощность каждой печи, т/час (сух.) |
40 |
55 |
Число фурм |
Н. д. |
256 |
Сырье: |
Концентрат — 70 %, вода — 30 % |
Концентрат — 90 %, вода — 10 % |
Степеньдесульфуриза- ции, % |
70 |
40 |
Направление SO2 |
На сернокислотный завод |
В трубу |
Садбери, Канада, Glencore |
Томпсон, Канада, Vale (по 2018 год) | |
Температура, °С: | ||
слоя |
760 |
600 |
огарка при выгрузке |
760 |
580 |
отходящего газа |
- |
530 |
Отходящий газ: | ||
Скорость образования, нм3/час |
40 000 |
48 000 при 530 °С |
SO2, об. % |
11-13 |
До 25 |
Система газоулавливания |
Циклоны — охлаждение газа, электрофильтры, очистка газа в скруббере, удаление воды и на сернокислотный завод |
Циклоны, дымоход, дымовая труба |
Таблица 1.21 — Плавка на штейн обожженного никелевого концентрата ([24], [27], [28]) (в скобках для комбината «Печенганикель» указаны характеристики РТП-5)
45
Садбери, Канада, Glencore |
Томпсон, Канада, Vale (по 2018 г.) |
Печенганикель Россия, Норильский Никель |
Bindura Nickel Corp., Зимбабве |
Waterval (Anglo American Platinum), ЮАР |
Mortimer (Anglo American Platinum), ЮАР | |
Печи: | ||||||
Тип |
1 прямоугольная |
2 прямоуголь ные |
2 прямоугольные (1 прямоугольная) |
1 прямоугольная |
2 прямоугольные |
1 прямоугольная |
Внешние размеры: Д х Ш х В, м |
30 х 9 х 2,7 (внутр.) |
31,7 х 10,7 х 6,4 |
27,5 х 11,1 х 6,6 (17,2 х 7,9 х 7,5) |
Н. д. |
26 х 8 (внутр.) |
25 х 7 |
Рабочие характеристики: | ||||||
Средняя рабочая мощность, МВт |
40 |
16 |
24 (18) |
Н. д. |
34 |
20 |
Энергопотребление, кВтчас/т сух. твердого |
440 |
470 |
600-720 |
853 |
700 |
820-850 |
Производительность, т/час/печь |
80 |
65 |
50 (25-30) |
Н. д. |
36 |
20 |
Сырье: | ||||||
Тип добавленного восстановителя |
Кокс (~0,04 т/т огарка) |
Н. д. |
Угольный штыб |
Н. д. |
Н. д. |
Н. д. |
ИТС 12-2016
46
Садбери, Канада, Glencore |
Томпсон, Канада, Vale (по 2018 г.) |
Печенганикель Россия, Норильский Никель |
Bindura Nickel Corp., Зимбабве |
Waterval (Anglo American Platinum), ЮАР |
Mortimer (Anglo American Platinum), ЮАР | |
Флюс |
Н. д. |
Н. д. |
Н. д. |
Известняк |
Известняк |
Известняк |
Примерный состав сырья, % |
Ni — 12; Cu — 4,5; Co — 0,5; Fe — 31; S — 28 |
Ni — 14; Cu — 0,3; Co — 0,3; Fe — 37; S — 29 |
Ni — 5-10; Cu — 2,5; Co — 0,2; Fe — 40; S — 20-25 |
Ni — 10,5; Cu — 2,1; Co — 0,3; Fe — 22; S — 17, MgO — 17 |
Ni — 3,6; Cu — 2,1; Co — 0,08; Fe — 16; S — 9; MgO — 20 |
Ni — 2.2; Cu — 1.1; Co — 0,04; Fe — 12; S — 5; MgO — 20 |
Конвертерный шлак |
Нет |
Да (расплавленный) |
Да (расплавленный) |
Да (расплавленный) |
Да (гранулированный) |
Н. д. |
Электроды: | ||||||
Количество |
6 |
6 |
6 (3) |
6 |
Н. д. |
Н. д. |
Диаметр, м |
1,4 |
1,2 |
1,1 (1,2) |
Н. д. |
1,1 |
1,25 |
Расход массы, кг/т сух. тверд. сырья |
3,5 |
1,1 |
Н. д. |
2 |
Н. д. | |
Продукты плавки: | ||||||
Штейн, т/час |
~30 |
По ~30 с печи |
Н. д. |
Н. д. |
7-8 |
3 |
t штейна °С |
1250-1275 |
1190 |
1250 |
1300 |
Н. д. |
1550 |
ИТС12-2016
47
Садбери, Канада, Glencore |
Томпсон, Канада, Vale (по 2018 г.) |
Печенганикель Россия, Норильский Никель |
Bindura Nickel Corp., Зимбабве |
Waterval (Anglo American Platinum), ЮАР |
Mortimer (Anglo American Platinum), ЮАР | |
Состав, % |
Ni — 36; Cu — 11; Co — 1; Fe — 33; S — 17 |
Ni — 30; Cu — 1; Co — 1; Fe — 37; S — 27 |
NiCuCo — 18 26; Fe — 0-50; S — 23,3 |
Ni — 26,5; Cu — 5,0; Co — 1,2; Fe — 34,5; S — 27,2 |
Ni — 17; Cu — 9; Co — 0,5; Fe — 41; S — 27 |
Ni — 12; Cu — 7; Co — 0,3; Fe — 37; S — 25 |
Переработка штейна |
Конвертер Пирс — Смита |
Конвертер Пирс — Смита |
Конвертер Пирс — Смита |
Конвертер Пирс — Смита |
Непрерывное конвертирование |
Непрерывное конвертирование |
Шлак, т/час |
~50 |
~35 (с каждой печи) |
Не определя ется |
Н. д. |
36 |
14 |
^шлака °С |
1300-1320 |
1310 |
1350 |
1500 |
1550 |
1650 |
Способ переработки |
Отвал |
Грануляция и отвал |
Грануляция и отвал |
Грануляция и отвал |
Грануляция, измельчение, флотация |
Грануляция, измельчение, флотация |
Состав, % |
Fe — 35; SiO2-35; MgO — 4-6 |
Ni — 0,4; Co — 0,2; Fe — 37; Fe3O4-10; SiO2-35; MgO — 2,7 |
Ni — 0,2; Cu — 0,12; Fe — 35; SiO2-38-40; MgO — 12,5 |
Ni — 0,23; Cu — 0,11; Co — 0,23; Fe — 24; SiO2- 42; MgO — 22 |
Ni — 0,19; Cu — 0,11; SiO2-46; Fe — 24, MgO — 15 |
SiO2-41; Fe — 16, MgO — 13 |
SO2 в отходящем газе, об. % |
1 |
3,3 |
<0,3 |
Н. д. |
0,5-1,3 |
0,5-1,0 |
ИТС 12-2016
48
Садбери, Канада, Glencore |
Томпсон, Канада, Vale (по 2018 г.) |
Печенганикель Россия, Норильский Никель |
Bindura Nickel Corp., Зимбабве |
Waterval (Anglo American Platinum), ЮАР |
Mortimer (Anglo American Platinum), ЮАР | |
Способ утилизации газов |
Дым. труба |
Дым. труба |
Дым. труба |
Н. д. |
Сернокислотное производство |
Н. д |
Печи: | ||||||
Тип, количество электродов |
1 прямоугольная |
4 прямоугольные (из них 2 эксплуатируются) |
1 круглая |
1 прямоугольная |
1 круглая |
1 прямоугольная |
Внешние размеры, Д х Ш х В, м |
29 х 10 |
26 х 8 |
0 11 м |
26 х 9 |
0 12 м (наружный) |
9 х 5 |
Рабочие характеристики: | ||||||
Средняя рабочая мощность, МВт |
68 |
35 и 38 |
28 |
15 |
12,5 |
5 |
Энергопотребление, кВтчас/т сух. твердого |
750-850 |
721 |
850 |
1000 |
900 |
900 |
Производительность, т/час/печь |
46 |
30 |
10 |
10 |
1 | |
Сырье: | ||||||
Тип добавленного восстановителя |
Н. д. |
Н. д. |
Н. д. |
Н. д. |
Н. д. |
Н. д. |
ИТС12-2016
49
Садбери, Канада, Glencore |
Томпсон, Канада, Vale (по 2018 г.) |
Печенганикель Россия, Норильский Никель |
Bindura Nickel Corp., Зимбабве |
Waterval (Anglo American Platinum), ЮАР |
Mortimer (Anglo American Platinum), ЮАР | |
Флюс |
Известняк |
Не добавляется |
Н. д. |
Н. д. |
Известняк |
Известняк, отработанные катализаторы |
Примерный состав сырья, % |
Ni — 2.1; Cu — 1,2; Co — 0,04; Fe — 12; S — 5; MgO — 18 |
Ni — 1.7; Cu — 1,1; Co — 0,05; Fe — 12; S — 5; MgO — 18 |
Ni — 2,5; Cu — 1,5; Co — 0,13; Fe — 17; S — 6; MgO — 17 |
Ni — 2,5; Cu — 1,3; Co — 0,05; Fe — 13; S — 5; MgO — 18 |
Ni — 2,0; Cu — 1,5; Co — 0,07; Fe — 13; S — 6; MgO — 24 |
Ni — 5,3; Cu — 3,2; Co — 0,01; Fe — 15; S — 13; MgO — 12 |
Конвертерный шлак |
Н. д. |
Н. д. |
Н. д. |
Н. д. |
Н. д. |
Да (гранулированный) |
Электроды: | ||||||
Количество |
Н. д. |
Н. д. |
3 |
6 |
3 |
3 |
Диаметр, м |
1,6 |
1,4 |
1,4 |
1,0 |
1,2 |
0,3 (предварительно спеченные) |
Расход массы, кг/т сух. тверд. сырья |
3 |
2 |
2,6 |
2,6 |
3,1 |
3,5 |
Продукты плавки: | ||||||
Штейн, т/час |
Н. д. |
5-6 |
4 |
1,8 |
1,2 |
0,14-0,25 |
^штейна °С |
1550 |
1300 |
1550 |
1400 |
1400 |
1200 |
ИТС 12-2016
50
Садбери, Канада, Glencore |
Томпсон, Канада, Vale (по 2018 г.) |
Печенганикель Россия, Норильский Никель |
Bindura Nickel Corp., Зимбабве |
Waterval (Anglo American Platinum), ЮАР |
Mortimer (Anglo American Platinum), ЮАР | |
Состав, % |
Ni — 14; Cu — 8; Co — 0,3; Fe — 40; S — 30 |
Ni — 14; Cu — 9; Co — 0,3; Fe — 45; S — 30 |
Ni — 15; Cu — 9; Co — 0,5; Fe — 43; S — 28 |
Ni — 16; Cu — 8; Co — 0,4; Fe — 41; S — 27 |
Ni — 15; Cu — 10; Co — 0,7; Fe — 43; S — 28 |
Ni-17; Cu-11; Co-0,02; Fe-43; S-27 |
Переработка штейна |
Непрерывное конвертирование |
Конвертер Пирс — Смита |
Конвертер Пирс — Смита |
Конвертер Пирс — Смита |
Конвертер Пирс — Смита |
TBRC |
Шлак, т/час |
41 | |||||
^шлака °С |
1600 |
1460 |
1650 |
1500 |
1600 |
1500 |
Способ переработки |
Грануляция и отвал |
Грануляция, измельчение, флотация |
Н. д. |
Н. д. |
Г рануляция и отвал |
Медленное охлаждение, измельчение, флотация |
Состав, % |
SiO2-52; Fe — 8, MgO — 23 |
Ni — 0,11; Cu — 0,11; SiO2-47; Fe — 9, MgO — 21 |
SiO2-45; Fe — 22, MgO — 20 |
Ni — 0,2, Cu — 0,1; SiO2-44; Fe — 16, MgO — 20 |
SiO2-54; Fe — 14, MgO — 22 |
SiO2-45; Fe — 10, MgO — 14 |
SO2 в отходящем газе, об. % |
0,5-1,5 |
0,9 |
Н. д |
Н. д. |
0,1 |
4 |
ИТС12-2016
51
Садбери, Канада, Glencore |
Томпсон, Канада, Vale (по 2018 г.) |
Печенганикель Россия, Норильский Никель |
Bindura Nickel Corp., Зимбабве |
Waterval (Anglo American Platinum), ЮАР |
Mortimer (Anglo American Platinum), ЮАР | |
Способ утилизации газов |
Н. д. |
Сернокислотное производ ство |
Сернокислотное производство |
Н. д. |
Н. д. |
Н. д. |
ИТС 12-2016
Основной тенденцией современной металлургии в области переработки высокосернистых концентратов является применение автогенных процессов. К наиболее распространенным относятся технология и печь взвешенной плавки, разработанные и внедренные в производство в конце 1940-х годов фирмой Outokumpu для плавки медных концентратов. Начиная с 1960-х годов это процесс начал свое победоносное шествие по миру и на сегодняшний день реализован на многих предприятиях медной и никелевой подотраслей.
В настоящее время по этой технологии в мире работает 6 заводов, перерабаты -вающих никельсодержащие сульфидные концентраты 10, один из них — Fortaleza (Бразилия) был остановлен в 2013 году Завод Copper Cliff компании Vale использует собственную технологию взвешенной плавки в горизонтальной печи (таблица 1.21).
В автогенных процессах большая часть потребности в тепле удовлетворяется за счет окисления железа и серы, содержащихся в концентрате, в результате чего расходы топлива или электричества малы. Производительность печей взвешенной плавки по сырью (в пересчете на сухой вес) обычно составляет 100-150 т/ч. В печах Outotec содержание кислорода в реакционном газе меняется от 30-40 об. % до 70 об. %; печи Inco (завод Copper Cliff) работают на кислородном дутье.
Одним из усовершенствований технологии (но не печи) взвешенной плавки является DON-процесс. При его реализации в одном агрегате совмещаются процессы штейновой плавки и конвертирования, таким образом, на выходе из печи получается три продукта: богатый штейн, или файнштейн; шлак, близкий по составу к конвертерному; и поток богатых по сернистому ангидриду газов. Для обеднения шлаков используется электропечь, обеспечивающая получение отвальных шлаков и малосернистого штейна, который затем вместе с файнштейном может быть направлен на гидрометаллургическую переработку (ранее на таком сырье работал рафинировочный завод Har-javalta) или после грануляции, сушки и измельчения возвращен в ПВП.
Другим вариантом усовершенствования печи и, соответственно, технологии взвешенной плавки, является интеграция электропечи для обеднения шлаков в ПВП. Подобная концепция реализована на заводах Kalgoorlie (Австралия) и Jinchuan (Китай).
53
Завод, страна, компания |
Copper Cliff Канада, Vale |
Kalgoorlie Австралия, BHP Billiton |
Selebi Phikwe Ботсвана, BCL |
Jinchang Китай, Jinchuan |
НМЗ Россия, Норникель |
Harjavalta Финляндия, Boliden |
Ввод в строй |
1993 |
1972 |
1973 |
1992 |
1981 |
1959 |
Процесс |
ВП Inco |
ВП Outotec со встроенной электропечью |
ВП Outotec |
ВП Outotec со встроенной электропечью |
ВП Outotec |
DON Outotec (с 1995 года) |
Ni в штейне, тыс. т/год |
133 |
100 |
27 |
65 |
140-170(2 печи) |
38 |
Размеры (внутренние), м: | ||||||
Под, Ш х Д х В |
2 печи * 8 х 30 х 9 |
8 х 37 х 3,5 |
8 х 22 х 4 |
7 х 32 х 3,5 |
10 х 31 х 6 |
7 х 19 х 2,6 |
Реакц. шахта: | ||||||
Диаметр |
7 |
8 |
6 |
8 |
4,6 | |
Высота над крышей отстойника |
6 |
11 |
6 |
9 |
7,6 | |
Число концентр. горелок |
4 горизонтальные |
4 |
4 |
4 |
1 |
1 |
Аптейк: |
Квадратный |
Круглый | ||||
Диаметр |
4 х 4 |
3,5 х 8 |
5 |
3 | ||
Высота над крышей отстойника |
15 |
7 |
17 |
7 |
ИТС 12-2016
54
Завод, страна, компания |
Copper Cliff Канада, Vale |
Kalgoorlie Австралия, BHP Billiton |
Selebi Phikwe Ботсвана, BCL |
Jinchang Китай, Jinchuan |
НМЗ Россия, Норникель |
Harjavalta Финляндия, Boliden |
Кампания, лет |
2-3 |
10 |
9 |
8 |
5 |
10 |
Сырье: | ||||||
Свежий сухой концентрат, т/час |
125 |
140 |
120 |
50 |
150 |
45 |
Состав, % |
Ni — 10; Cu — 12; Co — 0,3; Fe — 39; S — 34 |
Ni — 15; Cu — 0,3; Co — 0,4;Fe — 34;S — 32 |
Ni — 5; Cu — 4; Co — 0,2; Fe — 43; S — 31 |
Ni — 9; Cu — 4; Co — 0,2; Fe — 38; S — 27 |
Ni — 9; Cu — 4; Co — 0,5; Fe — 44; S — 33 |
Ni — 15; Cu — 0,8; Co — 0,4; Fe — 30; S — 29 |
Дутье: | ||||||
Температура, °С |
t окружающей среды |
500 |
260 |
Н. д. |
t окружающей среды |
t окружающей среды |
О2, об. % |
96 |
35 |
31 |
42 |
70 |
75 |
Скорость потока, нм3/час |
14000 |
85000 |
150000 |
33000 |
60000 |
7000 |
Питание кислородом, т/час |
11 |
25 |
40 |
12 |
40-50 |
4 |
Продукция: | ||||||
Штейн, т/час |
65 |
25 |
25 |
25-35 |
5 |
ИТС12-2016
55
Завод, страна, компания |
Copper Cliff Канада, Vale |
Kalgoorlie Австралия, BHP Billiton |
Selebi Phikwe Ботсвана, BCL |
Jinchang Китай, Jinchuan |
НМЗ Россия, Норникель |
Harjavalta Финляндия, Boliden |
Состав штейна, % |
Ni — 23; Cu — 25; Co — 0,6; Fe — 24; S — 26 |
Ni — 47; Cu — 1,5; Co — 0,8;Fe — 20;S — 27 |
Ni — 17; Cu — 15; Co — 0,4; Fe — 33; S — 25 |
Ni — 29; Cu — 15; Co — 0,6; Fe — 29; S — 23 |
Ni — 33; Cu — 14; Co — 0,5; Fe — 23; S — 27 |
Ni — 65; Cu — 5; Co — 0,7; Fe — 5; S — 22 |
Шлак, т/час |
120 |
70 |
110 |
50 |
160 |
20 |
Состав шлака, % |
Ni — 0,5; Cu — 0,5; Co — 0,2; Fe — 43; SiO2- 36 |
Ni — 0,7; Cu — 0,1; Co — 0,2; Fe — 40; SiO2- 33 |
Ni — 1,5; Cu — 1,3; Co — 0,1; Fe — 40; SiO2-28 |
Ni — 0,2; Cu — 0,2; Co — 0,1; Fe — 41; SiO2-36 |
Ni — 0,6; Cu — 0,3; Co — 0,2; Fe — 40; SiO2- 34 |
Ni — 4; Cu — 0,3; Co — 0,5; Fe — 38; SiO2- 29 |
Отходящий газ: | ||||||
Скорость потока, нм3/час |
26000 |
100000 |
60000 (на пылеуловителе) |
60 000 |
16000 | |
SO2, об. % на выходе из печи |
55 (сух.) |
7,2 |
8 (на сернокис. заводе) |
35 |
30 | |
Направление SO2 |
Сернокис. завод |
В атмосферу |
Сернокис. завод |
В атмосферу |
Сернокис. завод | |
Температура штейн/шлак/газ,°С |
1210/1280/1350 |
1170/1300/1400 |
1160/1240/1400 |
1320/1380/1380 |
1150/1250/1150 |
1360/1400/1400 |
Подача топлива: |
ИТС 12-2016
Завод, страна, компания |
Copper Cliff Кана да, Vale |
Kalgoorlie Австралия, BHP Billiton |
Selebi Phikwe Ботсвана, BCL |
Jinchang Китай, Jinchuan |
НМЗ Россия, Норникель |
Harjavalta Финляндия, Boliden |
Количествово углеводородного топлива, сгорающего в час |
340 нм3 природного газа + 1,4 т кокса (на по-верхн. шлака) |
1,5 м3 нефти |
6 т угля |
1,3 м3 нефти + 0,8 т угля |
До 6000 нм3 газа в час (18 горелок в отстойнике) |
1 т сырой нефти |
Электроэнергия |
6,25 МВт, 6 электродов |
0 |
5 МВт, 6 электродов |
Нет |
Н. д. | |
* В январе 2013 г. Vale приняла решение о переходе на плавку в одной печи. |
ИТС12-2016
Главным преимуществом технологии взвешенной плавки являются низкие энергозатраты, возможность получения стабильного потока богатых по сере газов, содержащих 20 % — 25 % об. SO2. К недостаткам следует отнести необходимость строгого соблюдения требований к подготовке сырья (гранулометрический состав, влажность) и невозможность прямого получения отвальных шлаков.
Производство файнштейна
Полученный при плавке сульфидного сырья штейн содержит большое количество железа, которое может быть удалено из него в силикатный шлак в ходе окислительной продувки — конвертирования.
Традиционно конвертирование в никелевой отрасли осуществляют в конвертерах Пирса — Смита — агрегатах периодического действия, представляющих собой горизонтальную цилиндрическую печь с расположенными на боковой поверхности фурмами для подачи в расплав воздуха и кислорода. Заливка расплава и удаление отходящих газов осуществляются через горловину, расположенную в средней части корпуса. К недостаткам конвертеров Пирса — Смита относятся периодичность процесса и, как следствие, нестабильный поток отходящих газов, затрудняющий утилизацию из них серы, малый срок службы конвертера (футеровка разрушается из-за колебаний температуры и при воздействии высоких температур в околофурменной зоне), невозможность применения дутья, обогащенного кислородом, из-за снижения стойкости футеровки, выбросы сернистого газа в атмосферу цеха, малое время работы под дутьем.
В настоящее время происходит постепенный уход от получения файнштейна в конвертерах Пирса — Смита с внедрением TBRC-конвертеров, процесса Ausmelt или ACP — Anglo Platinum Converting System (Система конвертирования Anglo Platinum) (таблица 1.22). Также подобная задача может быть решена путем внедрения DON-процесса (см. выше).
Процесс TBRC — плавка во вращающемся наклонном конвертере с верхней продувкой (печь Калдо) — применяется в черной и цветной металлургии, в частности, для конвертирования чугуна и штейнов, а также драгметальном производстве для выплавки Доре-металла. Продувка ведется с помощью вводимой через горловину фурмы, не погруженной в расплав. Интенсивное перемешивание расплава в конвертере достигается как за счет барботирования его дутьем, так и за счет вращения конвертера, что обусловливает весьма высокую производительность последнего (по черновому никелю — 275 т/сут). Достоинства конвертирования TBRC:
- хорошая теплопередача и высокая скорость протекания физико -химических ре -акций за счет вращения агрегата;
- точная система наклона конвертера упрощает его загрузку и способствует хо -рошему разделению шлака и сульфидного или металлического расплава;
- отсутствие погружной фурмы увеличивает срок службы агрегата и упрощает технологические процессы.
К недостаткам следует отнести сложность конструкции агрегата и его высокую стоимость, а также периодический режим плавки.
Процесс Ausmelt — плавка в вертикальном агрегате с жидкой ванной с подачей дутья через погруженную в расплав сверху фурму со сменными насадками — был изобретен в начале 1970-х. В печи Ausmelt может осуществляться как плавка на штейн, так и конвертирование последнего; также возможно объединение процессов плавки и конвертирования в одном агрегате. Технология может применяться как в периодическом, так и в непрерывном режиме.
Расплав в печи Ausmelt перемешивается с очень большой интенсивностью, что обусловливает высокую удельную производительность агрегата. Простая и полностью герметичная система загрузки обеспечивает высокую степень улавливания SO2 и утилизацию более 99 % серы. Дутье в данном агрегате может быть обогащено до 60 % кислорода, что достаточно при использовании отходящих газов для производства серной кислоты, но может оказаться недостаточным для получения из них элементной серы. Срок службы футеровки печи Ausmelt значительно выше, чем в конвертерах Пирса — Смита.
Главными недостатками процесса является невозможность прямого получения отвального шлака (при штейновой плавке) из-за высокой интенсивности перемешивания расплава в печи и, соответственно, необходимость эксплуатации обогреваемого отстойника или электропечи обеднения, а также возможность установки агрегата в цехах большой высоты из-за необходимости обслуживания вертикально расположенной фурмы.
Близкими по конструкции и эксплуатационным характеристикам являются печи ACP (Anglo Platinum Converting System) южноафриканской компании Anglo Platinum.
Таблица 1.23 — Конвертирование Ni — (Cu, Co, МПГ) штейнов в конвертерах Пирса — Смита
60
Sudbury Glencore, Канада |
Thompson Vale, Канада |
«Печенгани-кель», «Норникель», Россия |
НМЗ Норникель, Россия |
Kalgoorlie BHPB, Австралия |
Jinchuan, Китай |
BCL, Ботсвана |
Сэр-СИГТ Vale, Канада | |
Тип штейна |
ЭП |
ЭП |
ЭП |
ВП Outotec |
ВП Outotec |
ВП Outotec |
ВП Outotec |
ВП Inco |
Производительность, тыс. т Ni/год |
63 |
50 |
35 |
140 |
100 |
65 (2004 г.) 115 (2015) |
27,5 |
134 |
Число конвертеров |
3 |
5 |
6 |
3 |
3 |
2 + (1-резерв.) |
5* | |
Внутренние размеры: 0 х Д, м |
1: 4 х 15 2: 4 х 9 |
4 х 10,7 |
4 х 12 |
4 х 9 |
3,6 х 7,3 |
3,6 х 8,2 |
3,96 х 9,14 |
3: 3,96 х 13,7 2: 3,96 х 10,7 |
Число и диаметр фурм, мм |
1: 6, 032, 2: 42, 050 |
30-42, 051 |
52, 050 |
52, 050 |
28, 063,5 |
34, 048 |
44, 038 |
3: н. д., 051 2: н. д., 042 |
Расход дутья, нм3/ч |
1: 6450 2: 30000 |
36000 |
36000 |
19000 |
18000 22000 |
32000 |
~35000 | |
O2 в дутье, об. % |
33 % — 43 % и 21 % |
21 |
21 |
21 |
21 |
21 |
21 |
24-27 |
Добавки оборотов перв. штейна, вес, % |
- |
10 |
25-30 |
25 |
- | |||
Флюс (SiO2), % |
76 |
98,7 |
95,4 |
82,8 |
96 |
ИТС12-2016
61
Sudbury Glencore, Канада |
Thompson Vale, Канада |
«Печенгани-кель», «Норникель», Россия |
НМЗ Норникель, Россия |
Kalgoorlie BHPB, Австралия |
Jinchuan, Китай |
BCL, Ботсвана |
Сор-Ciiff Vale, Канада | |
Файнштейн: | ||||||||
SNi, Cu, Co, % |
75,5 |
80 |
72,6 |
Ni40-52, Cu18-30, Co0,2-0,3 |
69 |
73 |
80,82 |
77,3 |
Ni/Cu (Ni/Co) |
3,1 (30) |
26 (109) |
1,6 (55) |
1,9 (180) |
37 (74) |
1,93 (56) |
1,12 (95) |
0,82 (79) |
Fe, % |
2-2,5 |
0,6 |
3 |
3,4 |
4,2 |
4,2 |
1,49 |
0,52 |
S, % |
21 |
18,7 |
24,3 |
22-23 |
24 |
22,4 |
16,7 |
21-22 |
Шлак: | ||||||||
SiO2 %/Fe%/Fe3O4 |
21/48 |
26/50 |
20/45 |
20/52/25 |
21/55/32 |
24 28/48/14-18 |
26/44/17,6 |
26/51/23 |
Переработка шла ка |
На обеднение |
Возврат в ЭП |
Возврат в ЭП |
На обеднение |
Возврат на ПВП |
На обеднение |
На обеднение |
Возврат на ВП |
коэф. разубож. газов через подсосы в напыльник |
3-4 |
1 : 1 на H2SO4-завод,2 : 1 в дымовую трубу |
2,5-3 |
2,5 |
~3-4 |
ИТС 12-2016
62
Sudbury Glencore, Канада |
Thompson Vale, Канада |
«Печенгани-кель», «Норникель», Россия |
НМЗ Норникель, Россия |
Kalgoorlie BHPB, Австралия |
Jinchuan, Китай |
BCL, Ботсвана |
Cop.Cliff Vale, Канада | |
разубож. объем отход. конв. газов, нм3/ч |
- |
75 000 |
180 000 |
140 000 |
41 000 на H2SO4^-вод, «60000 — в дымовую трубу |
50 000 60 000 |
80 000 на 1 конверт. |
140 000 |
SO2 (сух.), об. % |
- |
3,6 |
2,5 |
2,5 |
«4 % на H2SO4- завод 2,7 % — в трубу |
2,5-3,5 |
5,2 |
3-5 |
Охлажд. и система очистки газов |
Котел-утилизатор, э/фильтр |
Форсуночный холодильник (воздух и вода) |
Котел- утилизатор, и э/фильтр |
Н. д. |
Котел- утилизатор, и э/фильтр | |||
Утилизация газов |
В атмосферу |
В атмосферу |
H2SO4-завод |
В атмосферу |
На H2SO4-завод или в атмосферу |
На H2SO4- завод |
В атмосферу |
В атмосферу |
ИТС12-2016
63
Sudbury Glencore, Канада |
Thompson Vale, Канада |
«Печенгани-кель», «Норникель», Россия |
НМЗ Норникель, Россия |
Kalgoorlie BHPB, Ав стралия |
Jinchuan, Китай |
BCL, Ботсвана |
Cop.Cliff Vale, Канада | |
Утилизация пыли |
Возврат в конвертеры |
Возврат на ВП |
Возврат на ВП |
Возврат на ВП |
Возврат на ВП |
Возврат су хой пыли на ВП | ||
* По состоянию на конец 2015 г. в рамках реализации проекта по сокращению выбросов в атмосферу диоксида серы, пыли и т. д. компания Vale на заводе Copper Cliff уже установила два новых конвертера TBRC из планируемых трех конвертеров взамен 5 конвертеров Пирс — Смита. Конвертеры диаметром 3 м, длиной 6 м имеют скорость вращения =10 об./мин; рабочая температура — 1450 °C — 1650 °C. Размер партии — 40-70 т, продолжительность «от выпуска до выпуска» 3-4 ча. Диоксид серы, образовывающийся при конвертировании, ранее поступал в дымовую трубу, а теперь будет улавливаться новой системой мокрой газоочистки, а затем поступать на сернокислотный завод. |
64
Waterval AngloPlat, ЮАР |
Springs , Impala, ЮАР |
Maricana Lonmin, ЮАР |
Northam, ЮАР |
Selous Zim-plats, Зимбабве |
Columbus Stillwater, США | |
Число и диаметр фурм, мм |
- |
26 (малые) 32 (большие); 51 мм |
20; 65 мм |
22 |
18; 50 мм |
- |
Средняя скорость дутья, нм3/ч |
25000 макс. |
11000-22000 |
11000 |
8500 |
2600 | |
O2 в дутье, об. % |
До 40 % |
Воздух без обогащения |
Воздух |
Воздух |
Воздух |
92-94 (тех. кислород) |
Файнштейн: | ||||||
NiCuCo, % |
73,5 |
78,0 |
77,6 |
78,5 |
79,1 |
75 |
Ni/Cu |
1,81 |
1,6 |
1,7 |
1,9 |
1,4 |
«1,3 |
Ni/Co |
94 |
160 |
80 |
102 |
114 |
- |
Fe, % |
2,9 |
0,6 |
1,4 |
1,0 |
0,6 |
«2 |
S, % |
21,7 |
20,3 |
20 |
19 |
17,5 |
20 |
SiO2 %/Fe%/Fe3O4 в конв. шлаке |
24-28/42-48 |
27/64,5 (FeO) |
29/62 (FeO) |
27/49,8 |
27,5/51,3 |
5-7 SiO2, 20 % — 25 % CaO, 45-50 Fe |
SO2 (сух.), об. % в отходящем разу-бож. газе |
12-16 |
3-8 (без разубожив.) |
0,4 |
65 |
ИТС12-2016
Waterval AngloPlat, ЮАР |
Springs , Impala, ЮАР |
Maricana Lonmin, ЮАР |
Northam, ЮАР |
Selous Zim-plats, Зимбабве |
Columbus Stillwater, США | |
Производительность, тыс. т Ni/год |
22, включая Union и Polokwane |
12,7 |
3,7 |
1,5 |
1,6 |
0,1 |
Тип и число конвертеров |
2 ACP |
6 ПС |
3 ПС |
2 ПС |
2 ПС |
2 TBRC |
Внутренние размеры: Д х Дл, м |
4,5 (внутренний диаметр) х 4 высота |
2: 3,6 х 7,3 4: 3 х 4,5 |
3 х 4,6 |
3х6,1 |
3 х 4,6 |
8 х 1,5 |
ИТС 12-2016
65
Waterval AngloPlat, ЮАР |
Springs , Impala, ЮАР |
Maricana Lonmin, ЮАР |
Northam, ЮАР |
Selous Zim-plats, Зимбабве |
Columbus Stillwater, США | |
Размещение от-ход.газов |
На H2SO4-3aeog |
На H2SO4-3aeog |
Э/фильтр, двойная щелочная очистка |
В дымовую трубу |
В дымовую трубу |
Тканевый фильтр, скруббер SO2, дымовая труба |
Размещение кон верт. шлаков |
Гранулир. и обедн. электропечь |
Гранулир., из-мельче-ние/флотация |
Гранулир., флотация |
Возврат на ЭП |
Возврат на ЭП |
Гранулир., возврат на ЭП |
ИТС 12-2016
1.4.3 Получение рафинированного никеля
Как было показано выше, при переработке сульфидных и окисленных никелевых руд никель и кобальт обычно (за исключением гидрометаллургических технологий, использующих метод жидкостной экстракции, позволяющий производить товарные катодные металлы без промежуточного осаждения концентратов) концентрируются в богатых промпродуктах, пригодных для дальнейшего рафинирования с получением товарных никеля и кобальта, — файнштейне (сульфидные руды), штейне, смешанных никель-кобальтовых гидроксидах (карбонатах), смешанных никель-кобальтовых сульфидах (окисленные никелевые руды).
Способы переработки сульфидных никелевых продуктов чрезвычайно разнообразны (таблица 1.23) и определяются составом и экономическими соображениями с учетом географического положения и исторических особенностей развития конкретных предприятий. Однако обзор мировой практики получения рафинированного никеля показывает практически повсеместное распространение процессов гидрометаллургического рафинирования файнштейна. Наряду с получением никеля электроэкстракцией в мировой практике достаточно широко применяется карбонил-процесс, позволяющий получать никелевую продукцию с высокой добавленной стоимостью. Он реализован на предприятиях Vale: Copper Cliff (Канада) и Clydach (Соединенное Королевство (Уэльс)), а также заводе Jinchuan (Nonferrous Metals, Китай) и на комбинате Североникель (АО КГМК, ПАО «ГМК «Норильский никель», Россия). На заводах Copper Cliff и Nonferrous Metals также осуществляют электролитическое рафинирование сульфидных анодов.
Для упрощения технологической схемы на ряде предприятий файнштейны с высоким содержанием меди предварительно разделяют на никелевый и медный концентраты методом флотации (Copper Cliff (Vale, Канада), Jinchuan (Nonferrous Metals, Китай), комбинат Североникель (ПАО «ГМК «Норильский никель», Россия), в ряде случаев также осуществляется выделение металлизированной фракции, обогащенной драгоценными металлами (Copper Cliff (Vale, Канада), Jinchuan (Nonferrous Metals, Китай), на рафинировочном заводе Anglo American Platinum в Рустенбурге, ЮАР), методом магнитной сепарации. Обособленная переработка магнитной фракции существенно сокращает длительность технологического цикла получения концентратов драгметаллов и их безвозвратные потери .
Таблица 1.24 — Способы получения рафинированного никеля на некоторых предприятиях
67
Завод, компания, страна |
Исходный материал |
Состав, % |
Принцип переработки |
Продукция |
Nikkelwerk (Норвегия), Glencore |
Файнштейн |
Ni — 52,0; Cu — 19,0-20,0; Co — 2,5; Fe — 2,5, остальное — сера |
Хлорное выщелачивание, автоклавное выщелачивание, электроэкстракция |
Ni-катоды, Cu-катоды, концентрат МПГ |
Niihama (Япония), Sumitomo Metal Mining |
Файнштейн, Ni-Co-осажденные сульфидные концентраты |
Ni — 73 ; Cu— 4,5; Co — 2,5 |
Хлорное выщелачивание, электроэкстракция для получения катодного никеля; автоклавное выщелачивание, жидкостная экстракция — для солей |
Ni-катоды, Co-катоды, Ni-соли |
Sandouville (Франция), Eramet |
Файнштейн, полученный сульфидированием ферроникеля |
Ni — 78; Cu — 0,2; Co — 2; Fe — 3; , остальное — сера |
Хлорное выщелачивание, электроэкстракция |
Ni-катоды |
Matsuzaka, Vale (Япония) |
Файнштейн |
Н. g. |
Окислительный обжиг, восстановительный обжиг, брикетирование |
Tonimet-брикеты, Tonimet, Tonimet 97, синтер, Compact 97 |
68
Завод, компания, страна |
Исходный материал |
Состав, % |
Принцип переработки |
Продукция |
Комбинат Севе-роникель, ПАО «ГМК «Норильский Никель», Мончегорск, Россия |
Файнштейн |
Ni — 40 % — 52 %, Cu — 18 % — 30 %, Co — 0,2 % — 0,3 % |
Медленно охлажденный файнштейн дробят, измельчают, флотируют с получением никелевого и медного концентратов. Затем никелевый концентрат обжигают намертво, восстанавливают и плавят с получением металлических никелевых анодов, направляемых на электролитическое рафинирование. В ближайшей перспективе обожженный и восстановленный никелевый концентрат (никелевый порошок трубчатых печей) будет направляться на операции хлорного растворения и последующей электроэкстракции |
Ni-катоды, Ni-карбонильный (порошки, дробь), Cu-катодная, Co-катодный, концентрат МПГ, концентрат Ag |
Thompson (Кана да), Vale |
Файнштейн |
Ni — 73,0-75,0; Cu — 2,5-4; Co — 1,0; Fe — <1,0; S — 20,0 |
Электролитическое рафинирование сульфидных анодов, отлитых из файнштейна |
Ni-катоды |
ИТС12-2016
ИТС 12-2016
69
Завод, компания, страна |
Исходный материал |
Состав, % |
Принцип переработки |
Продукция |
Copper Cliff, Vale, Канада |
Файнштейн |
Ni — 45,0; Cu — 35,0 |
Из файнштейна выделяется обогащенная ДМ магнитная фракция, а немагнитная фракция разделяется флотацией на никелевый и медный концентраты. Никелевый концентрат обжигается, восстанавливается до металла, далее, как и магнитная фракция, рафинируется карбонилированием |
Карбонильная никелевая продукция |
Jinchuan, Nonferrous Metals, Китай |
Файнштейн |
Ni 47,0; Cu 23,0-26,0; Co 0,6-0,7; Fe 2,4; S 22,0 |
Из файнштейна обогатительными методами выделяются обогащенный ДМ-концентрат, медный и никелевый концентраты. Из никелевого концентрата отливаются сульфидные аноды, которые рафинируются электролизом |
Катодный никель, карбонильная никелевая продукция |
Kwinana, BHP Billiton, Австралия |
Файнштейн |
Ni 73,5; Cu 4,0; Fe 0,8; Co 0,7; S 20,0 |
Аммиачное выщелачивание, водородное восстановление |
Ni-брикеты, Ni-порошок, Cu-сульфидный концентрат, Ni-Co-сульфидный концентрат |
ИТС 12-2016
70
Завод, компания, страна |
Исходный материал |
Состав, % |
Принцип переработки |
Продукция |
Fort Saskatchewan, Канада |
Ni-Co осажденный сульфидный концентрат |
Н.д. |
Аммиачное выщелачивание, водородное восстановление |
Ni-брикеты, Co-брикеты |
Bindura, Bindura Nickel, Зимбабве |
Файнштейн |
Ni 38,0; Cu 54,0; Fe 0,1; S 5,5; As 0,1 |
Сернокислотное автоклавное выщелачивание, электроэкстракция |
Ni-катоды, медный сульфидный концентрат, гидроксид кобальта |
Harjavalta, ПАО «ГМК «Норильский никель», Финляндия |
Немагнитная фракция никелевого концентрата флотации файнштейна |
Ni 65,0; Cu 5,0; Fe 4,0; S 21,0 |
Комбинация процессов атмосферного и автоклавного сернокислотного выщелачивания, электроэкстракция и/или восстановление H2 |
Ni-катоды, Ni-брикеты, Co-брикеты, Cu-сульфидный концентрат |
Yabulu Refinery, Австралия |
Смешанные Ni- Co-гидроксиды^ |
Н. д. |
Жидкостная экстракция, реэкстракция, отгонка аммиака с получением основного карбоната никеля, прокалка, восстановление водородом, кобальт осаждается в виде сульфида, затем доводится до кобальта металлического, медь осаждается в виде сульфида |
«QNI Highgrade» — 99,5 % Ni, рондели — 98,5 % Ni, QN ChemGrade Cobalt, медный сульфидный концентрат |
ИТС12-2016
9) Смешанные гидроксиды поступают в технологический цикл переработки окисленных никелевых руд методом Карона.
71
Завод, компания, страна |
Исходный материал |
Состав, % |
Принцип переработки |
Продукция |
Waterval, Amplats, ЮАР |
Файнштейн |
Ni 47,0-48,0; Cu 28,0 |
Сернокислотное автоклавное выщелачивание | |
Impala Platinum, Springs ЮАР |
Файнштейн |
N 45,0; Cu 28,0 |
Сернокислотное автоклавное выщелачивание, восстановление H2 |
Ni-порошки, брикеты |
Stillwater, MarathonPGM Corp., США |
Файнштейн |
Н. д. |
Комбинация процессов атмосферного и автоклавного сернокислотного выщелачивания закалённого файн-штейна |
Сульфат никеля, катодная медь, концентрат МПГ |
Anglo American Platinum Rusten-burg (ЮАР) |
Файнштейн |
Н. д. |
Медленно охлажденный файнштейн измельчают, выделяют металлизированную фракцию магнитной сепарацией, раздельное выщелачивание продуктов, электроэкстракция |
Ni-катоды, Cu-катоды, концентрат МПГ |
Northam Platinum (ЮАР) |
Файнштейн |
Н. д. |
Комбинация процессов атмосферного и автоклавного сернокислотного выщелачивания закалённого файн-штейна |
Сульфат никеля, катодная медь, концентрат МПГ |
Clydach, Соединенное Королевство (Уэльс) |
Обожженный никелевый концентрат немагнитной фракции флотации файнштейна |
Н. д. |
Карбонил-процесс |
Карбонильная продук ция |
ИТС 12-2016
Переработка сульфидных никель-кобальтовых концентратов, осажденных из растворов высокотемпературного автоклавного сернокислотного выщелачивания окисленных никелевых руд, аналогична таковой для файнштейнов; смешанные никелькобальтовые гидроксиды (карбонаты) могут быть легко интегрированы в технологический цикл любого рафинировочного завода, хотя более логичным представляется их использование в сульфатных схемах.
Следует отметить, что гидрометаллургическое рафинирование файнштейна и производство никеля методом карбонилирования целесообразно рассматривать как основу современных и прогрессивных технологий получения рафинированного никеля.
Гидрометаллургическое рафинирование файнштейнов
Во всех случаях гидрометаллургического рафинирования богатых никелевых промпродуктов (за исключением смешанных гидроксидов) головной операцией рафинирования является окислительное выщелачивание, которое осуществляется в хло-ридных, сульфатных или аммиачно-сульфатных средах. Дальнейшая конфигурация технологической схемы предусматривает очистку раствора от примесей и разделение присутствующих в растворе меди, никеля и кобальта. Ниже рассмотрены примеры реализации процесса на некоторых предприятиях (таблица 1.24).
Рафинирование файнштейна в хлоридных средах
В настоящее время технология рафинирования файнштейна в хлоридных сре -дах применяется на трех предприятиях, технологические схемы которых существенно различаются между собой, как по условиям растворения файнштейна, так и по способу очистки растворов от примесей.
На заводе Kristiansand (Glencore, Норвегия) измельченный файнштейн выщелачивается при температуре кипения в каскаде реакторов в оборотном никелевом анолите при подаче хлора и поддержании заданного окислительно-восстановительного потенциала для коллектирования в нерастворимом остатке меди и драгоценных металлов. Затем выщелоченная пульпа подается в каскад автоклавов, работающих при температуре 140 °C — 145 °C и давлении 0,3-0,4 МПа. Пульпа из хвостового автоклава непрерывно через холодильник разгружается в реакторы медеочистки, которая осуществляется частью свежего файнштейна.
73
Thompson, Vale, Канада |
Harjavalta, Норильский Никель, Фин ляндия |
Rustenburg, ЮАР (2009) |
Rustenburg (новый электролизный цех), ЮАР (2011) |
Niihama, Sumi tomo, Япония |
Kristiansand, Glencore, Норвегия |
Комбинат «Североникель», «Норильский никель», Россия | ||
Рафинирование анодов |
Рафинирова ние НПТП (проект) | |||||||
Производитель ность, т/год Ni |
60000 |
15000/20000 |
21500 |
33000 |
30000 |
90000 |
120000 |
145000 |
Количество ванн, шт. |
684 |
128 |
Н. д. |
208 |
200 |
430 |
476 |
476 |
Размер ванн, Д х Ш х В, м |
5,8 х 1,6 х х 0,9 |
6 х 1,2 х 1,2 |
6,6 х 1,2 х х 1,2 |
Н. д. |
6 х 0,9 х 1,1 |
7 х 0,8 х 1,6 |
8,5 х 1,4 х 1,8 |
8,5 х 1,4 х 1,8 |
Материал |
Бетонные, покрытые пластиком |
Армированный монолитный бетон, вставка ПВХ |
Блочный бетон |
Полимербе тон |
168-бетонные, покрытые пластиком, 32-полимербетон |
Армированный бетон с пластиковой вставкой |
Полимербе тон |
Полимербе тон |
Электролит: |
Сульфат-хлоридный |
Сульфатный |
Сульфатный |
Сульфатный |
Хлоридный |
Хлоридный |
Сульфат-хлоридный |
Сульфат-хлоридный |
ИТС 12-2016
74
Thompson, Vale, Канада |
Harjavalta, Норильский Никель, Фин ляндия |
Rustenburg, ЮАР (2009) |
Rustenburg (новый электролизный цех), ЮАР (2011) |
Niihama, Sumi tomo, Япония |
Kristiansand, Glencore, Норвегия |
Комбинат «Североникель», «Норильский никель», Россия | ||
Рафинирование анодов |
Рафинирова ние НПТП (проект) | |||||||
Состав, г/дм3 |
Ni — 75 85/75-85 Cl — 50-60 H3BO3- 78 |
Ni100 на входе, 65 на выходе, ла-урилсуль-фат натрия — 20 мг/л |
Ni 80 на входе, 50 на выходе H3BO3 6 10 |
80 на входе, 50 на выхо де, H3BO3 6-10 |
Ni — 70-75, Cl — 85 |
60 на входе, 54 на выхо де, Cl — 60 |
Ni — 70-75, Cl — 50-55, H3BO3- 3-6 |
Ni — 70, Cl — 63, H3BO3- 4-6 |
рН |
1,5/3,0 |
3,5-3,8 |
3,5 |
3,5 |
2 |
1,4-2,0 |
1,5/3,0 |
1,4/1,6 |
Скорость цирку ляции электролита, м3/мин/ванну |
0,7 |
0,025-0,030 |
0,009 |
Н.д. |
0,035 |
0,07 |
0,025 |
0,03 |
Аноды: | ||||||||
Количество |
27 |
50 |
41 |
49 |
53 |
52 |
51 |
61 |
Размер, Д х Ш х В, м |
1,1 х 0,7 х х 0,045 |
Н. д. |
Н. д. |
Н. д. |
1 х 0,8 х 0,002 |
1 х 0,8 х х 0,002 |
0,92 х 0,83 х х 0,095 |
1,24 х 0,835 |
ИТС12-2016
75
Thompson, Vale, Канада |
Harjavalta, Норильский Никель, Фин ляндия |
Rustenburg, ЮАР (2009) |
Rustenburg (новый электролизный цех), ЮАР (2011) |
Niihama, Sumi tomo, Япония |
Kristiansand, Glencore, Норвегия |
Комбинат «Североникель», «Норильский никель», Россия | ||
Рафинирование анодов |
Рафинирова ние НПТП (проект) | |||||||
Состав |
Ni -76 %, Cu — 2,5 %, S — 19 % |
Свинец |
Свинцовый сплав (0,6 % Sn, 0,05 % Sr) |
Свинцовый сплав (0,6 % Sn, 0,05 % Sr) |
Покрытая оксидом рутения титановая сетка |
Покрытая оксидом рутения титановая сетка |
Ni 87 % — 90 %, Cu 4,5 Fe 3,5 |
Покрытая оксидом рутения титановая сетка |
Анодная кампания, сут. |
16-17 |
- |
- |
- |
- |
- |
27 |
- |
Катоды: | ||||||||
Количество |
26 |
49 |
40 |
48 |
52 |
51 |
50 |
60 |
Расстояние между катодами, м |
0,2 |
0,133 |
0,16 |
Н. д. |
0,11 |
0,13 |
0,165 |
0,13 |
Размер, Д х Ш, мм |
970 х 890 |
1300 х 700 |
1085 х935 |
1340x935 | ||||
Катодная кампания, сут. |
10 |
7+2 (для основы на Ti-матрице) |
6+2 (для основы на Ti-матрице) |
10-14 (без-основный) |
7 |
7 |
3-5 |
(5-7) + 1 |
ИТС 12-2016
76
Thompson, Vale, Канада |
Harjavalta, Норильский Никель, Фин ляндия |
Rustenburg, ЮАР (2009) |
Rustenburg (новый электролизный цех), ЮАР (2011) |
Niihama, Sumi tomo, Япония |
Kristiansand, Glencore, Норвегия |
Комбинат «Североникель», «Норильский никель», Россия | ||
Рафинирование анодов |
Рафинирова ние НПТП (проект) | |||||||
Напряжение на ванне, В |
3 с повышением до 6 по мере роста толщины шламовой корки |
3,8-4,0 |
3,6-3,9 |
3,6-3,9 |
3,0-3,1 |
Н. д. |
2,4-2,5 |
3,6-4,0 |
Катодная плот ность тока, А/м2 |
250 |
220-230 |
220 |
220-260 |
233-273 |
260 |
250-270 |
227 |
Выход по току, % |
93 |
97 |
>95 |
99,5 |
98-99 |
96,5 |
95,5 |
ИТС12-2016
Очищенный от меди фильтрат поступает на гидролитическую железоочистку, которая осуществляется в реакторах путем подачи карбоната никеля и хлора, затем на выделение гипса и жидкостную экстракцию кобальта 15 %-ным раствором три-изо-октиламина в керосине.
Никелевый рафинат после разбавления оборотным электролитом и гидролитической очистки от свинца и марганца подается на передел электроэкстракции никеля. Из кобальтового реэкстракта после дополнительной гидролитической очистки получают катодный кобальт.
На заводе Niihama (Япония) компании Sumitomo Metal Mining (SMM) файнштейн подвергают хлорному растворению в две стадии по протовотоку. На первой стадии (цементации) медистый раствор (40 г/дм3 Cu) реагирует с исходным файнштейном с переводом в раствор части никеля (~20 %) и осаждением меди в виде сульфида до остаточного содержания ~0,01 г/дм3.
На второй стадии при использовании хлора в качестве окислителя из кека глубоко выщелачивается никель и медь, таким образом, что суммарное извлечение никеля в раствор на двух стадиях выщелачивания оказывается более 95 %, а окисление серы до сульфатной не превышает 3 %.
Богатый никелем раствор со стадии цементации поступает на гидролитическую очистку от кобальта и железа окислением их хлором в присутствии карбоната никеля, а затем на электроэкстракцию с получением катодного никеля и возвратом газообразного хлора на стадию выщелачивания и очистки растворов. Кобальт извлекается из железо-кобальтового кека растворением в серной кислоте с подачей сульфита натрия. Полученный раствор после очистки от железа и меди направляют на жидкостную экстракцию с получением чистых хлоридных растворов никеля и кобальта, из которых получают никелевые соли и катодный кобальт и кобальтовые соли, соответственно.
Удаление меди из цикла выщелачивания осуществляется электроэкстракцией, которая предусмотрена технологической схемой между стадиями выщелачивания и цементации, с получением промпродуктового медного порошка, передаваемого затем на медный завод.
На заводе Sandouville компании Eramet (Франция) низкомедистый (0,2 % меди) файнштейн выщелачивается в две стадии раствором хлорного железа в солянокислой среде с подачей хлора. В результате выщелачивания получают раствор хлоридов никеля, кобальта и железа. Сера в элементарной форме отделяется от раствора вместе с нерастворимым остатком.
Из раствора трибутилфосфатом экстрагируют железо (которое после реэкстракции частично возвращается на выщелачивание, а частично выпускается в качестве товарного хлорида железа), а затем с помощью три-изо-октиламина — кобальт, который реэкстрагируется в форме хлорида, являющегося товарной продукцией. Оставшийся после выделения железа и кобальта раствор хлорида никеля очищается от свинца электроэкстракцией, от других примесей — ионообменом, от органики — активированным углем. Из очищенного раствора электроэкстракцией получают катодный никель; образующийся в процессе электролиза хлор поступает на выщелачивание исходного файнштейна.
Рафинирование файнштейна в сульфатных средах
Технологические схемы рафинирования файнштейна в сульфатных средах более распространены в мире и ближе друг к другу по идеологии, нежели хлоридные. Обычно они представляют собой комбинацию процессов атмосферного и автоклавного выщелачивания, организованную в противоточном режиме. В качестве примеров рассмотрим технологии рафинирования файнштейна на заводе Harjavalta (Финляндия) и предприятиях Южной Африки.
На гидрометаллургическом заводе Harjavalta (Норильский никель, Финляндия) в настоящее время перерабатывается немагнитная фракция никелевого концентрата флотации файнштейна российских предприятий ПАО «ГМК «Норильский никель».
Согласно технологической схеме материал подвергается двухстадийному атмосферному окислительному выщелачиванию. Целью первой стадии — медеочистки — является глубокая очистка оборотного раствора от меди и железа, второй — повышение извлечения в раствор никеля за счет частичного разложения сульфидов.
Более глубоко разложение сульфидов протекает на стадии автоклавного выщелачивания, реализуемой под давлением кислорода. Полученная пульпа, содержащая в жидкой части достаточное количество меди для растворения никеля, подается без разделения жидкого и твердого на автоклавное рафинирование, которое проводится в атмосфере паров воды без подачи окислителя. На этой стадии происходит взаимодействие сульфидной составляющей с присутствующим в растворе сульфатом меди с получением медного кека, коллектирующего драгоценные металлы. Этот кек для дальнейшей переработки направляется на медерафинировочные предприятия. Раствор автоклавного рафинирования после автоклавной железоочистки, осуществляемой с использованием в качестве нейтрализатора натриевой щелочи, направляется на первую атмосферную стадию (медеочистку).
Из раствора медеочистки жидкостной экстракцией выделяется кобальт, а также малые примеси меди, железа, цинка, марганца и др. Серной кислотой из промытого экстракта реэкстрагируют кобальт с получением раствора сульфата кобальта, из которого после дополнительной очистки от малых примесей получают товарные кобальтовые соли.
Товарную никелевую продукцию — катодный никель и никелевые брикеты, получаемые из порошка автоклавного водородного осаждения в аммиачно-сульфатных средах, — производят из никелевого рафината в двух цехах: электролизном и цехе водородного восстановления. Из относительно небольшой части никелевого рафината в цикле жидкостной экстракции никеля получают более чистый никелевый реэкстракт, который направляется на производство никелевых солей. Побочной продукцией предприятия является сульфат аммония, получаемый из растворов после водородного восстановления никеля.
Гидрометаллургическая технология рафинирования файнштейна на заводах ЮАР и Зимбабве представляет собой многостадийную противоточную схему сернокислотного автоклавного выщелачивания файнштейна.
На заводе Springs (Impala Platinum, ЮАР) измельченный файнштейн проходит через три противоточных стадии автоклавного окислительного выщелачивания. На первой и второй стадиях в раствор переходит до 85 % никеля. На третьей стадии автоклавного окислительного выщелачивания в раствор извлекают остатки цветных металлов и серы и получают концентрат ДМ, который передают на аффинаж. Богатый раствор первой стадии выщелачивания очищают от меди осаждением гидросульфидом натрия, что обеспечивает полноту осаждения ДМ. Кек после осаждения меди направляется на вторую стадию автоклавного окислительного выщелачивания, фильтрат которой после железоочистки направляется на электроэкстракцию меди. Из очищенного от меди раствора первой стадии автоклавного окислительного выщелачивания также гидролитическим способом осаждают железо. Затем из него автоклавным водородным восстановлением получают чистый никелевый порошок, который непосредственно отправляют на продажу или предварительно брикетируют. Водородное восстановление осуществляют в аммиачно-сульфатных средах, а из растворов после осаждения никеля регенерируют аммиак подачей извести, что позволяет выводить сульфат-ион в форме отвального гипса. Остаток никеля и кобальта осаждают из раствора гидросульфидом натрия в виде смешанных никель-кобальтовых сульфидов, которые перерабатывают по технологии, предусматривающей применение жидкостной экстракции для разделения никеля и кобальта.
В отличие от завода Springs на заводе Rustenburg (Anglo American Platinum, ЮАР) файнштейн перед рафинированием проходит через магнитную сепарацию, которая отделяет магнитную фракцию, содержащую основное количество металлов платиновой группы, от немагнитной, обедненной по ДМ-фракции.
Магнитная фракция выщелачивается в отдельном трехстадийном цикле с получением богатого концентрата ДМ, который направляется на аффинажное предприятие. Растворы выщелачивания магнитной фракции передаются на стадию автоклавного рафинирования цикла переработки немагнитной фракции.
Немагнитная фракция файнштейна растворяется в отдельном противоточном цикле выщелачивания, включающем атмосферную стадию медеочистки файнштейном, атмосферную стадию окислительного выщелачивания, автоклавное рафинирование и автоклавное окислительное выщелачивание медного сульфидного кека стадии автоклавного рафинирования. Фильтрат автоклавного выщелачивания медного кека после очистки от селена и теллура направляется на производство товарной меди электроэкстракцией. Железо из раствора цикла выщелачивания выводится автоклавным окислением с использованием раствора каустика. Очистке от железа подвергается фильтрат второй стадии атмосферного выщелачивания перед его подачей на первую стадию, где осуществляется очистка от меди.
Никелевый раствор после стадии очистки от меди очищается от свинца добавкой гидроксида бария. Далее фильтрат очищается от кобальта полученным электрохимическим окислением черным гидратом никеля.
Очищенный от примесей никелевый раствор поступает на электроэкстракцию никеля. Анолит из цеха электроэкстракции никеля возвращается на атмосферное выщелачивание никеля и частично отсекается на передел осаждения карбоната никеля, производимого для операций гидролитических очисток. Из фильтрата карбонатного передела производится товарный сульфат натрия.
Рафинирование файнштейна в аммиачных средах
Рафинирование файнштейна по методу Sherrit в аммиачных средах реализовано на заводах Fort Saskatchewan (Sherrit, Канада) и Kwinana (BHP Billiton, Австралия). В этом случае технологическая схема включает в себя стадии автоклавного окисли -тельного выщелачивания в аммиачных средах и переработку растворов с водородным осаждением никеля и кобальта. С другой стороны, широкое распространение имеют технологические схемы, использующие в качестве головных операций сернокислотное автоклавное выщелачивание, а завершающих — водородное осаждение из аммиачных сред (Harjavalta, Финдяндия, Impala Platinum, ЮАР). В последнем случае разделение никеля и кобальта, а также очистка от примесей реализуются на стадии работы с кислыми сульфатными растворами, а осаждение производится из чистых индивидуальных растворов никеля и кобальта.
На заводе «Форт Саскачеван» файнштейн выщелачивают в автоклавах в аммиачных растворах под давлением кислорода. При этом порядка 90 % никеля, 80 % меди и 45 % кобальта переходят в раствор в форме комплексных солей — аммиакатов , сера извлекается в раствор на 75 %. Железо образует гидроксид и выпадает в осадок.
Полученный раствор перерабатывается гексаминовым методом, суть которого заключается в осаждении смешанной соли — гексамина кобальта (III) — никеля (II), который является исходным сырьем для получения рафинированного кобальта.
После фильтрации раствор поступает на двухстадийную очистку от меди (на первой стадии медь осаждается за счет отгонки аммиака, на второй — путем введения сероводорода), а затем после оксигидролиза на восстановление никеля водородом в автоклаве. Полученный медный сульфид направляется на производство товарной меди на медные заводы.
Переработка гексамина кобальта (III) — никеля (II) включает в себя выщелачивание водой и слабым оборотным раствором для удаления никеля, а затем перекристаллизацию в аммиачно-сульфатном растворе. Полученная соль характеризуется соотношением Co : Ni = 2000 : 1 и направляется на получение товарного кобальта.
Для этого ее растворяют, кобальт восстанавливают до степени окисления 2+ оборотным кобальтовым порошком и серной кислотой, а затем полученный раствор обрабатывают водородом для получения товарного металла.
Продуктами аммиачной технологии переработки сульфидных никелевых концентратов являются сульфид меди (~70 % Си), никелевый порошок, кобальтовый порошок (99,8 % Со) и сульфат аммония.
Электролитическое рафинирование файнштейна
Электролитическое рафинирование файнштейна реализовано на двух заводах — Thompson компании Vale (Канада) и Jinchuan компании Nonferrous Metals (Китай).
На заводе Thompson маломедистый файнштейн разливается в горизонтальные изложницы для получения анодов размером 1,1 х 0,7 х 0,045 м, которые затем помещают в полипропиленовые мешки и завешивают в электролизные ванны. Анолит, образующийся в процессе растворения черновых анодов, очищается от примесей в гидрометаллургическом отделении, а затем подается в катодное.
На комбинате Jinchuan измельченный файнштейн проходит через магнитную сепарацию для выделения обогащенного ДМ металлического сплава (магнитной фракции), который направляют в шламовый цех для извлечения драгоценных металлов. Немагнитная фракция файнштейна флотацией разделяется на никелевый и медный концентраты. Никелевый концентрат от флотационного разделения файнштейна плавится в отражательных печах на аноды, которые подвергаются электролитическому рафинированию.
Карбонильный процесс
Около четверти всего объема файнштейна превращается в никель высокой чистоты с помощью газофазного процесса карбонилирования. Этот процесс применяется в Канаде (завод Copper Cliff), России (Кольская ГМК), Китае (Jinchuan) и Великобритании (завод Clydach).
Процесс карбонилирования может проходить при атмосферном давлении (Cly-dach), при высоком давлении (Кольская ГМК), а также при среднем давлении (Copper Cliff).
Vale производит по карбонильной технологии порошки и дробь на рафинировочных заводах в Великобритании (Clydach) и Канаде (Copper Cliff) суммарной мощностью более 100 тыс. т/год, из которых около 25 тыс. т/год приходится на порошки.
В настоящее время Vale производит 2 типа никелевых порошков: тип 123 — дис -кретные квазисферические частицы со средним размером частиц (по Фишеру) 810 мкм и тип 255 — частицы с трехмерной цепочечной структурой со средним размером цепочек 15-20 мкм.
Основным сырьем для никелевого рафинировочного завода Clydach компании Vale служит оксид никеля (синтер 75), поставляемый с канадского комплекса Copper Cliff, также принадлежащего Vale. Суммарная мощность завода оценивается примерно в 40 тыс. т/год. В 2015 году выпуск завода Clydach составил ~9-10 тыс. т карбонильного порошка, остальное — карбонильная дробь.
Компания Jilin Jien Nickel (Китай) производит никелевый порошок по технологии, предоставленной канадской компанией CVMR (карбонилирование при атмосферном давлении). Основным сырьем служит промпродукт — гидроксид никеля, из которого получается оксид никеля и далее восстановлением водородом никель металлический. Никель затем взаимодействует при атмосферном давлении с СО с образованием газо-
образного карбонила никеля, в результате термического разложения которого получают как дискретные, так и нитеобразные порошки в реакторах, аналогичных установленным у компании Vale. Мощность по никелевым порошкам — около 2000 т/год.
Канадский рафинировочный никелевый завод Copper Cliff Nickel Refinery (CCNR) компании Vale работает с 1972 года по технологии карбонилирования под средним давлением, запатентованной компанией Inco. Синтез тетракарбонила никеля при среднем давлении реакционного газа (70 бар) и повышенных температурах осуществляется из-за необходимости извлекать никель в присутствии меди в сравнительно больших концентрациях, а также существенного ускорения реакции и, соответственно, увеличения производительности оборудования.
На заводе CCNR перерабатывают промпродукты от разделения файнштейна с плавильно-рафинировочного комплекса Copper Cliff в Садбери, а также Ni-содержащие (и содержащие драгоценные металлы) остатки других предприятий компании, которые для получения однородного по составу нерафинированного расплава никеля переплавляют в TBRC конвертере и гранулируют с образованием маленьких пористых гранул.
Выделенные при флотации немагнитной фракции сульфиды никеля (с низким содержанием меди) обжигают в кипящем слое до NiO и отправляют на завод Clydach для извлечения никеля по карбонильной технологии при атмосферном давлении.
В зависимости от состава сырья и аппаратурного оформления в процессе карбонилирования параллельно с образованием карбонила никеля, Ni(CO)4, протекают реакции синтеза карбонилов железа, кобальта, серы. Этот продукт — карбонил-сырец — подвергают ректификации для получения чистого карбонила никеля.
Разложение чистого карбонила никеля с получением дроби осуществляется в разложителях с циркулирующими в нем частицами никелевой дроби, предварительно подогретыми до 240 °C — 270 °C. Часть Ni(CO)4 после перегонки конденсируют и затем повторно переводят в газовую фазу, но с более высокой концентрацией. Этот газ поступает в разложитель для порошков с наружным электрообогревом стенок. Тетракарбонил подвергается тепловому удару, в результате нуклеации образуется множество никелевых частиц, которые впоследствии лишь немного увеличиваются в размерах. Размер и морфологию (например, сферическую форму или нитевидную) можно контролировать изменением скорости подачи сырья, концентрации и температуры внутри разложителя, а также путем добавок небольших количеств химических агентов, затрудняющих или способствующих разложению карбонила на различных участках.
Некоторое время назад китайская компания Jinchuan ввела в строй завод по «стандартной» карбонильной технологии мощностью ~5000 т/год никелевого порошка. Известно лишь, что процесс включает синтез при среднем давлении. В настоящее время Jinchuan выпускает два типа порошков: с нитеобразными частицами — тип N06, аналог Т255 (Vale), и с дискретными частицами N24 — аналоги Т123 (Vale). Другие нитеобразные порошки Jinchuan N04 и N09, грубо говоря, аналогичны порошкам Т210 и Т287, производство которых Vale было прекращено.
Комбинированные пиро-гидрометаллургические способы
Электрорафинирование черновых металлических никелевых анодов, полученных пирометаллургическими способом из сульфидного никелевого продукта от разделения файнштейна, до чистых никелевых катодов ранее было распространенным способом получения товарного никеля. На сегодняшний день оно сохранилось на одном предприятии, расположенном на территории Российской Федерации, — комбинате Се-вероникель АО «Кольская ГМК». Однако и на нем происходит его постепенная замена на метод электроэкстракции из хлоридных растворов.
Комбинированная технологическая схема получения товарного никеля в Российской Федерации будет рассмотрена ниже.
-
1.4.4 Переработка кобальтомышьяковых и медно-кобальтовых руд
Переработка кобальто-мышьяковых руд
Как упоминалось выше, единственным рудником, где в настоящее время добывают кобальтовую мышьяковистую руду, является рудник Bou-Azzer (Марокко) компании CTT Managem, остальные по экологическим соображениям были закрыты. Из руды с ~1 % Co получают флотационный концентрат , содержащий ~10 % — 11 % Co. Руды , подобные марокканским, традиционно перерабатывали по схеме, включающей обжиг и выщелачивание кислотой. Концентрат обжигали в печи с кипящим слоем с целью удаления 60 % — 70 % мышьяка в виде As2O5.
Огарок можно обрабатывать либо соляной кислотой и хлором, либо серной кислотой. Раствор выщелачивания очищается от примесей гидрометаллургическими методами, а из очищенного раствора кобальт извлекают электроэкстракцией или осаждением в виде карбоната CoCO3.
В проекте Idaho Cobalt (США) канадской компании Formation Metals предусматривается использование автоклавного кислотного выщелачивания в присутствии кислорода и катализатора — азотсодержащих частиц. При этом на этапе выщелачивания происходит практически полная стабилизация мышьяка — содержащееся в сырье железо образует c мышьяком скородит FeAsO4^2H2O ([29]).
Переработка медно-кобальтовых руд
Технологическая схема переработки медно-кобальтовых руд включает в себя флотационное обогащение с выделением сульфидной и окисленной составляющих и пирометаллургическую переработку.
Поскольку при флотации медно-кобальтовых руд извлечение кобальта обычно составляет 40 % — 80 %, хвосты обогащения, накопленные за десятилетия добы-чи/обогащения, можно рассматривать как техногенный источник кобальта (например, проект переработки хвостов Kolwezi, содержащих 1,3 % — 1,6 % Cu и 0,3 % — 0,4 % Co). Также в качестве техногенных источников кобальта следует рассматривать и шлаковые отвалы старых медеплавильных предприятий. Так, в шлаковых отвалах завода Nkana (Замбия) содержится порядка 0,65 % Co.
Одним из вариантов переработки шлака (заводе Chambishi) является плавка в дуговой печи постоянного тока с добавками восстановителя (угля) с получением богатого по кобальту сплава, который затем после диспергирования выщелачивается под давлением, полученный раствор после соответствующих очисток направляется на получение катодного кобальта ([30]).
В 2008 году в Замбии компания Konkola Copper Mines ввела в строй новый медный завод Nchanga на «300 тыс. т/год меди по технологии Outotec взвешенной плавки прямо на черновую медь — ‘direct-to-blister' для переработки обогащенных кобальтом медных концентратов из района Медного пояса Замбии.
Получаемый в результате богатый («17 % — 18 % Cu) шлак направляется на двухстадийное обеднение в двух последовательно соединенных электропечах.
В первой (основной) обеднительной печи идет процесс восстановления с использованием металлургического кокса с целью извлечения меди в черновую медь. Во второй, «кобальтовой» электропечи проходит восстановление коксом шлака из первой обеднительной печи и взаимодействие со свежим концентратом. В результате плавки образуется малосульфидный сплав (63,3 % Cu, 23,8 % Fe, 6,3 % Co, 6,2 % S) и сильно восстановленный шлак.
Альтернативой плавке медно-кобальтовых руд является переработка по схеме обжиг-выщелачивание-электроэкстракция. На рафинировочном заводе Luilu (ДРК) компании Katanga Mining (75,2 % у Glencore), перерабатывающем окисленные и сульфидные концентраты, полученные при обогащении медно-кобальтовой руды, сульфидный концентрат обжигается для перевода меди и кобальта в кислоторастворимые формы. Окисленный концентрат после репульпации отработанным электролитом и огарок сульфидного концентрата в виде пульпы с отработанным электролитом объединяют и выщелачивают при атмосферном давлении серной кислотой с добавками метабисульфита натрия Na2S2O5 (для улучшения растворения кобальта). Полученный раствор направляют на электроэкстракцию меди.
Извлечение кобальта осуществляется из отсечного электролита цеха электролиза меди. После очистки раствора от алюминия, железа, и меди, никеля и цинка раствор поступает на электроэкстракцию кобальта ([31]).
В настоящее время на заводе реализуется программа создания новых гидроме -таллургических мощностей по выщелачиванию всей массы руды (‘WOL'), что позволит избавиться от проблемы неэффективной флотации окисленной руды.
1.5 Ресурсная база никеля и кобальтаРоссия обладает значительной сырьевой базой никеля, основу которой составляют месторождения сульфидного медно-никелевого геолого-промышленного типа. Их руды характеризуются комплексностью и, помимо никеля, в промышленных количествах содержат медь, платиноиды, кобальт, золото и некоторые другие металлы. Иные геолого-промышленные типы месторождений, в том числе важный для минеральносырьевой базы ряда зарубежных стран латеритный (силикатный кобальто-никелевый), в российской сырьевой базе никеля имеют подчиненное значение ([32])-([33]).
В разрабатываемых и осваиваемых месторождениях страны заключено более 13 % мировых промышленных запасов никеля. Государственным балансом учтено 56 месторождений никеля, в том числе четырнадцать только с забалансовыми запасами. Кроме того, учтены и эксплуатируются три техногенных месторождения никеля: одно — в Мурманской области и два — в Красноярском крае.
Распределение запасов и прогнозных ресурсов никеля на территории России весьма неравномерно (рисунок 1.5). Более трех четвертей запасов заключено в сульфидных медно-никелевых рудах месторождений Норильского рудного района в Красноярском крае (таблица 1.25), входящего в Норильско-Хараелахскую металлогениче-скую зону (месторождения сплошных руд Октябрьское, заключающее 36 % российских запасов категорий А+В+С1, и Талнахское (25 %), а также месторождение вкрапленных руд Норильск 1 (7 % запасов)).
На разных стадиях освоения и изучения находятся еще два месторождения вкрапленных руд — Черногорское и Масловское.
На юге Красноярского края, в пределах Канского рудного района, находятся Кин-гашское и Верхнекингашское сульфидные медно-никелевые месторождения вкрапленных руд с совокупными запасами категорий А+В+С1+С2, составляющими почти 8 % российских.
В Печенгском рудном районе Имандра-Варзугской металлогенической зоны в Мурманской области сосредоточено около 13 % запасов никеля Российской Федерации в составе вкрапленных руд с низкими содержаниями полезных компонентов.
ЗАПАСЫ и РЕСУРСЫ
Респ. Карелия
Мурманская обл.
Ждановское
Воронежская обл,
Г
200
Челябинская обл.
Оренбургская
обл.
Свердловская обл.
qГ злнахское
У ОКТЯОрЬ'.К'
Красноярский край
Амурская
оол.
Камчатский край
Бурукаальское
Запасы,%
Месторождения:
о эазрабааываемые
О 2 запасы, %
О ресурсы Pi, тыс. т
Рисунок 1.5 — Основные месторождения никеля и распределение его запасов, % и прогнозных ресурсов категории Р1 ( тыс . т) по субъектам Российской Федерации ([32])
В Лапландской металлогенической зоне сосредоточены почти все известные в России месторождения малосульфидного собственно платиноидного геологопромышленного типа. Запасы никеля, заключенные в самом крупном из месторождений, Вуручуайвенч, достигают 0,9 % российских, однако большая их часть относится к категории С2. В рудах второго по масштабу малосульфидного месторождения Федорова тундра заключено 0,7 % российских запасов, преимущественно категорий А+В+С1.
Остальные малосульфидные платиноидные объекты невелики по масштабу и заключают бедные никелем (0,07 % — 0,12 %) руды.
В пределах Норильско -Хараелахской металлогенической зоны локализовано по -чти две пятых российских прогнозных ресурсов категории Р1 (500 тыс. т никеля), преимущественно на флангах Октябрьского месторождения. В пределах Имандра-Варзугской и Лапландской металлогенических зон локализованы прогнозные ресурсы никеля обоих геолого-промышленных типов, в том числе категории Р1 — 270 тыс. т.
В пределах Эртельской металлогенической зоны (Воронежская область ) прогно -зируется выявление месторождений сульфидных медноникелевых руд. Ресурсы никеля категории Р1 здесь оцениваются в 200 тыс. т, все они связаны с Еланским рудопро-явлением.
Незначительное количество никеля во вкрапленных рудах сульфидного мед-но-никелевого типа установлено в Джугджурской металлогенической зоне (Хабаровский край и Амурская область), где разведано месторождение Кун-Манье, а также в Срединно-Камчатской зоне (Шануч). Ресурсы, локализованные в этих регионах, имеют низкую достоверность.
Почти 10 % российских запасов никеля заключено в латеритных кобальто-никелевых месторождениях, разведанных в пределах Восточно-Уральской провинции, на территории Оренбургской, Свердловской и Челябинской областей. Уровень прогнозных ресурсов категории Р1 составляет 260 тыс. т. Среднее содержание никеля в латеритных рудах составляет порядка 0,6 %, за исключением мелкого по масштабу Черемшанского в Челябинской области, на некоторых участках которого содержание никеля достигает 4,1 % (таблица 1.26).
Таблица 1.26 — Основные месторождения сульфидной руды на 31 декабря 2014 г. ([18])
Руда, тыс. т |
Ni, % |
Cu,% |
Pd, г/т |
Pt, г/т |
Au, г/т | |
Талнахский рудный узел | ||||||
Доказанные и вероятные запасы |
713 920 |
0,93 |
1,71 |
4,21 |
1,12 |
0,24 |
Оцененные и выявленные ресурсы |
1 661 679 |
0,72 |
1,36 |
3,61 |
1,01 |
0,22 |
Предполагаемые ресурсы |
453 239 |
0,88 |
1,83 |
4,36 |
1,11 |
0,26 |
Кольский полуостров | ||||||
Доказанные и вероятные запасы |
147 883 |
0,59 |
0,28 |
0,03 |
0,02 |
0,01 |
Оцененные и выявленные ресурсы |
354 489 |
0,68 |
0,33 |
0,05 |
0,03 |
0,02 |
Предполагаемые ресурсы |
144 880 |
0,63 |
0,31 |
0,04 |
0,03 |
0,01 |
Таблица 1.27 — Основные силикатные месторождения никеля в РФ ([32])
Месторождение, область |
Доля А+В+С, РФ, % |
Содержание Ni, % |
Буруктальское, Оренбургская область |
6,5 |
0,63 |
Серовское, Свердловская область |
1,7 |
0,73 |
Сахаринское, Челябинская область |
0,4 |
0,87 |
Все значимые объекты с запасами никеля распределены. В государственном резерве по состоянию на начало 2015 года находятся 22 месторождения различных геолого-промышленных типов, в том числе десять — только с забалансовыми запасами.
В 2014 году российские запасы никеля категорий А +В + С 1 в результате геолого -разведочных работ увеличились на 427,5 тыс. т. Это позволило не только полностью компенсировать убыль запасов в результате добычи, но и нарастить их на 0,5 % относительно 2013 года. Запасы никеля категории С2 увеличились за этот период на 1,1 %.
В России более 97 % (2014 год) горной добычи никеля и кобальта приходится на ПАО «ГМК Норильский никель» — одну из крупнейших никелевых компаний мира, которой принадлежат разрабатываемые месторождения сульфидной медно-никелевой руды Норильского и Печенгского района. Добычу окисленной силикатной руды на Се-ровском руднике ведет компания ООО «Русникель».
Производством рафинированного никеля из рудного сырья в России в настоящее время занимаются две компании: ПАО «ГМК «Норильский никель» — получает никель из сульфидных медно-никелевых руд; ООО «Русникель» — из силикатных руд Урала. В 2014 году на ПАО «ГМК Норильский никель» приходилось практически 95 % производства рафинированного никеля в России. Совокупный объем производства товарного никеля ПАО «ГМК Норильский никель» в 2014 году составил 274 тыс. т, включая зарубежные предприятия.
Наиболее значимые никелевые предприятия России приведены на рисунке 1.6, основные технологически процессы — в таблице 1.27.
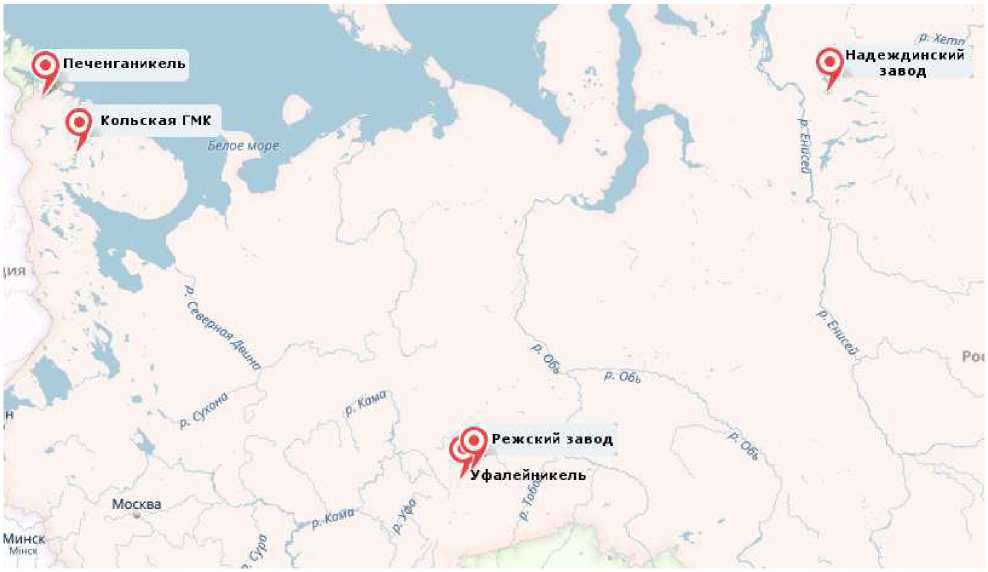
Рисунок 1.6 — Территориальное размещение никелевых предприятий России
91
Компания |
Предприятие, местоположение |
Процесс/технологическая схема |
Ссылка на разделы/зарубежный аналог |
Примечание |
Русникель |
Режский завод, г. Реж (РФ) |
Плавка окисленной никелевой руды в шахтных печах на штейн; штейн перерабатывается далее на комбинате Уфалейникель |
Зарубежных аналогов по части шахтной плавки нет |
- |
Русникель |
Комбинат Уфалейникель, г. Верхний Уфалей (РФ) |
Плавка окисленной никелевой руды на штейн в шахтных печах, конвертирование, обжиг в печах КС, хлорирование, выщелачивание от меди, повторный обжиг в трубчатых печах -с получением NiO, восстановительная электроплавка NiO |
Зарубежных аналогов по части шахтной плавки нет, дальнейшая схема переработки отчасти аналогична Soro-wako/ Matsusaka |
- |
ПАО «ГМК Норильский никель» |
Никелевый завод, г. Норильск; комбинат Печенгани-кель, п. Никель |
Плавка в электропечи предварительно обожженного флотационного рудного концентрата на штейн |
Заводы Sudbury (Glencore); Thompson (Vale), Bindura Nickel, заводы платиновой подотрасли ЮАР |
Никелевый завод, остановлен в июне 2016 г. |
ПАО «ГМК Норильский никель» |
Надеждинский завод, г. Норильск |
Взвешенная плавка Outokumpu флотационных концентратов на штейн |
Заводы Selebi Phikwe, Kalgoor-lie, Jinchang |
- |
ИТС 12-2016
Компания |
Предприятие, местоположение |
Процесс/технологическая схема |
Ссылка на разделы/зарубежный аналог |
Примечание |
ПАО «ГМК Но рильский никель» |
Печенганикель (п. Никель), Надеждинский завод (г. Норильск) |
Конвертирование штейна до файнштейна в конвертерах Пирса — Смита |
Sudbury (Glencore); Thompson (Vale) — до 2018 года, Kalgoor-lie, Gansu, BCL, Copper Cliff (до 2013 года) и др. |
- |
ПАО «ГМК Но рильский никель» |
Кольская ГМК, г. Мончегорск |
Получение никеля высокой чистоты методом карбонилирования |
- | |
ПАО «ГМК Норильский никель» |
АО «Кольская ГМК», г. Мончегорск |
Электролитическое рафинирование черновых никелевых анодов |
Зарубежных аналогов нет |
Осуществляется переход на рафинирование ПНТП |
ПАО «ГМК Норильский никель» |
Кольская ГМК, г. Мончегорск |
Г идрометаллургическая технология рафинирования НПТП |
Зарубежных аналогов нет |
- |
ИТС12-2016
Предприятия ПАО «ГМК «Норильский Никель», выпускающие порядка 12 % мирового никеля, имеют 4 зарегистрированные на ЛБМ марки никеля со статусом Good Delivery и опережают по данному показателю все зарубежные компании (таблица 1.28).
Таблица 1.29 — Выпускаемые ГМК «Норильский никель» марки никеля, зарегистрированные на ЛБМ
№ |
Марка |
Компания/предприятие |
Продукт |
1 |
Norilsk Nickel Harjaval- ta Cathodes |
Norilsk Nickel Harjavalta Oy/ Харьявалта (Финляндия) |
Резаные катоды Полноразмерные катоды |
2 |
Norilsk Nickel Harjaval-ta Briquettes |
Norilsk Nickel Harjavalta Oy/ Харьявалта (Финляндия) |
Брикеты |
3 |
Severonickel Combine H-1 |
Кольская ГМК |
Резаные катоды Полноразмерные катоды |
4 |
Severonickel Combine H-1Y |
Кольская ГМК |
Резаные катоды Полноразмерные катоды |
Прочие формы товарной никелевой продукции, выпускаемой ПАО «ГМК «Но
рильский Никель», представлены в таблицах 1.29-1.30.
Таблица 1.30 — Качество катодного никеля, выпускаемого АО «Кольская ГМК» (среднее за 2015 год)
ЛБМ 1 |
Н-1 |
у |
Н-1 |
Н-3 |
Н-4 ГОСТ | |||
ГОСТ 849 —2008 |
Факт |
ГОСТ 4 |
Факт |
ГОСТ |
Факт | |||
Ni |
99,80min |
99,97 2 |
99,96 2 |
99,93 7 | ||||
Ni+Co |
99,95 |
99,98 |
99,93 |
99,98 |
98,6 |
99,96 |
97,6 | |
Co |
0,1 5max |
0,10 |
0,012 |
0,10 |
0,017 |
0,7 |
0,021 |
0,70 |
Cu |
0,02max |
0,015 |
0,0053 |
0,02 |
0,0066 |
- |
0,0093 |
1 |
C |
0,03max |
0,01 |
0,005 |
0,01 |
0,005 |
0,1 |
0,009 |
0,15 |
Fe |
0,02max |
0,01 |
0,0069 |
0,02 |
0,0069 |
0,022 | ||
S |
0,01 max |
0,001 |
0,0006 |
0,001 |
0,0007 |
0,03 |
0,0013 |
0,04 |
P |
<0,005 |
0,001 |
<0,0003 |
0,001 |
<0,0003 |
- |
<0,0003 | |
Mn |
<0,005 |
- |
<0,0002 |
- |
- |
- |
- | |
Si |
<0,005 |
0,002 |
0,0008 |
0,002 |
0,0009 |
0,6 |
0,0012 | |
As |
<0,005 |
0,001 |
<0,0002 |
0,001 |
<0,0003 |
- |
0,0003 |
ЛБМ 1 |
Н-1 у |
Н-1 |
Н-3 |
Н-4 ГОСТ | ||||
ГОСТ 849 —2008 |
Факт |
ГОСТ 4 |
Факт |
ГОСТ |
Факт | |||
Pb |
<0,005 |
0,0005 |
0,00030 |
0,001 |
0,00057 |
- |
0,00064 | |
Sb |
<0,005 |
0,0005 |
<0,0001 |
0,001 |
<0,0001 |
- |
<0,0001 | |
Bi |
<0,005 |
0,0003 |
<0,00002 |
0,0006 |
<0,00002 |
- |
<0,00002 | |
Sn |
<0,005 |
0,0005 |
<0,0001 |
0,001 |
<0,0001 |
- |
<0,0001 | |
Zn |
<0,005 |
0,001 |
0,00057 |
0,001 |
0,00073 |
- |
0,00077 | |
Mg |
0,001 |
<0,0002 |
0,001 |
<0,0002 |
- |
<0,0002 | ||
Cd |
0,0005 |
<0,0001 |
0,001 |
<0,0001 |
- |
<0,0001 |
1 Требования к никелю Лондонской биржи металлов.
2 Расчетный метод определения .
Размеры для марок полноразмерных катодов Н-1 у и Н-1: с обрезанной кромкой 895-915 х 1145-1165 мм, толщина 2-10 мм, вес 30-80 кг. Размеры для марок полноразмерных катодов Н-3 и Н-4: Кольская — необрезанный 935 х 1135, толщина 2-6 мм, вес 30-70 кг.
Кроме того, Кольская ГМК выпускает резаные катодные листы: Н-1 у и Н-1 2 х 2 и 4 х 4 дюйма, толщина пластины 2-6 мм, а также брикеты Н-3.
Таблица 1.31 — Карбонильные никелевые порошки и дробь, выпускаемые Кольской ГМК, ПАО «ГМК Норильский никель», ГОСТ 9722, ТУ
Тип |
Средний размер частиц |
Форма частиц |
Насып . плотн., г/см3 |
O, % |
C, % |
Fe, % |
S, % |
S20 |
1,85-2,2 |
Цепочечная |
0,51-0,64 |
- |
0,09 |
0,0015 |
0,0007 |
S30 |
2,91-3,5 |
Цепочечная |
0,6-0,8 |
- |
0,28 |
0,002 |
0,001 |
Л5 (1L5) |
2,1-2,4 |
Цепочечная |
1,01-1,4 |
- |
0,28 |
0,002 |
0,001 |
Л8 (1L8) |
1,4-1,6 |
Цепочечная |
0,45-0,6 |
- |
0,28 |
0,002 |
0,001 |
УТ1 (UT1) |
7-8,5 |
Высокоплотная квазисфе-рическая |
3,0-3,5 |
0,02 |
0,09 |
0,0015 |
0,0007 |
УТ3 (UT3) |
3-6 |
Квазисфе-рическая |
1,91-2,5 |
0,02 |
0,09 |
0,0015 |
0,0007 |
Тип |
Средний размер частиц |
Форма частиц |
Насып. плотн., г/см3 |
O, % |
C, % |
Fe, % |
S, % |
DNK-0 Дробь(ТУ) |
8-20 мм |
Сферическая |
- |
0,02 |
0,015 |
0,015 |
0,001 |
Ист: ГМК Норильский никель. |
Комбинат Уфалейникель выпускает гранулированный огневой никель марок H3 и Н4, оксид никеля, оксиды кобальта и кобальт металлический марок К1АУ, К-1А, К1 и К2.
Раздел 2. Основные технологические процессы и оборудование, применяемые в настоящее время при производстве никеля и кобальта в Российской Федерации. Текущие уровни эмиссий 2.1 Производство никеля из сульфидных медно-никелевых концентратов 1-
2.1.1 Головные переделы
2.1.1.1 Гидрометаллургическое обогащение бедного никель-пирротинового концентрата
Гидрометаллургическое обогащение никель-пирротинового концентрата является уникальным в своем роде процессом и преследует цель повышения содержания цветных металлов за счет окисления основной части пирротина и отделения невскрывшихся и вторичных сульфидов цветных металлов от сформировавшегося при автоклавном окислительном выщелачивании (АОВ) железистого гидратного осадка и элементарной серы.
Процесс реализуется в условиях высокотемпературного автоклавного (130150 °С) выщелачивания (ВТВ) при использовании кислородо-воздушной смеси (80 % O2) в качестве окислителя и лигносульфоната технического (ЛСТ) в качестве поверхностно-активного вещества (ПАВ), препятствующего пассивации поверхности сульфидов пленкой элементарной серы. Реализация процесса при температуре выше точки плавления серы обеспечивает не только высокую скорость окисления, но и существен- 11 но снижает скорость образования серосульфидных настылей на поверхности теплообменников.
ВТВ осуществляется с обязательной добавкой ПАВ, препятствующих смачиванию расплавленной серой поверхности сульфидов. Недостаток ПАВ приводит к образованию серосульфидных гранул — «песков», нарушающих ход технологического процесса, или плавов — «козлов», полностью останавливающих процесс, избыток — к повышению потерь ценных компонентов с отвальными хвостами.
Химизм процесса окисления пирротина при выщелачивании описывается реакцией, по которой порядка 80 % серы пирротина переходит в элементарную фор-му.Перешедшее в раствор в процессе окисления сульфидов железо далее подвергается окислению и гидролизу с формированием твердой железоокисной фазы.
Учитывая последовательно-параллельное протекание реакций окисления сульфидов цветных металлов и пирротина, для обеспечения глубокого окисления последнего необходимо частично вскрыть также пентландит и халькопирит. В результате этого в раствор переходит порядка 75 % никеля, 50 % меди, 70 % кобальта.
Учитывая конечную цель процесса гидрометаллургического обогащения бедного никель-пирротинового концентрата — получение пригодного для дальнейшей переработки пирометаллургическими методами сульфидного концентрата цветных металлов, из растворов автоклавного выщелачивания производится осаждение частично растворившихся цветных металлов.
В качестве осадителя используются железные окатыши и присутствующая в пульпе элементарная сера. Осажденные на этой операции вторичные сульфиды меди, никеля и кобальта, а также не вскрытые на головном выщелачивании первичные сульфиды цветных металлов вместе с элементарной серой извлекаются в серосульфидный концентрат методом флотации.
Подавление побочных процессов (растворение в кислоте, восстановление Fe3+ до Fe2+), по которым расходуется необходимое для сульфидирования меди и никеля металлическое железо, возможно за счет постепенного введения в пульпу восстановителя и поддержания технологических параметров процесса (в первую очередь кислотности пульпы и температуры) на заданном уровне.
Учитывая флотационные свойства компонентов пульпы и задачи процесса, флотацию ведут в кислой среде при использовании в качестве собирателя бутилового ксантогената. Промпродукты флотации являются оборотными и возвращаются на основную флотацию, концентрат направляется на получение элементарной серы и товарного сульфидного концентрата, хвосты после двухстадийной нейтрализации в присутствии воздуха — в отвал.
Процесс получения элементарной серы и товарного сульфидного концентрата из серосульфидного концентрата состоит из нескольких основных технологических операций: дезинтеграции, серной флотации и автоклавной выплавки серы.
Целью дезинтеграции — высокотемпературной обработки серосульфидного концентрата — является разрушение сростков сульфидов цветных металлов и железа с элементной серой. При этом происходит выделение серы и сульфидов из их мелкодисперсных конгломератов в самостоятельные частицы и агрегации — укрупнение капель выделенной серы до размеров, обеспечивающих оптимальные показатели последующих операций. Введение технической извести в серосодержащую пульпу приводит к развитию процессов образования различных серосодержащих соединений кальция, в том числе сульфида и гидросульфида, подавляющих процесс смачивания сульфидов расплавленной серой.
Полученную пульпу вместе с хвостами серной плавки направляют на серную флотацию, концентрат которой — на автоклавную выплавку серы, а хвосты, являющиеся товарным концентратом ЦМ — в пирометаллургическое производство.
Хвосты плавки передаются на серную флотацию, расплавленная сера — в аппараты отстойники, где происходит окончательное отделение зольной составляющей (сульфидов). Зола вместе с частью серы гранулируется и передается на серную плавку, чистая сера — на склад готовой продукции.
Основное технологическое оборудование, используемое в технологической схеме переработки никель-пирротинового концентрата представлено в таблице 2.1.
Таблица 2.1 — Основное оборудование
№ |
Наименование оборудования |
Назначение оборудования |
Технологические характеристики |
1 |
Сгуститель П-50 (Ц-50) |
Сгущение пирроти- нового концентрата |
Сгуститель с периферическим (центральным) приводом в кислотостойком исполнении, диаметр — 50 м, глубина чана — 4,5 м, площадь сгущения — 1800 м2 |
№ |
Наименование оборудования |
Назначение оборудования |
Технологические характеристики |
2 |
Реактор |
Приготовление пульпы автоклавного выщелачивания, осаждение ЦМ из раствора автоклавного выщелачивания |
Из двухслойной стали (титана), емкость — 80 м3 |
3 |
Автоклав |
Автоклавное окислительное выщелачивание |
геометрическая емкость без футеровки — 125 м3 , рабочее давление — 15 кг/см2 , с перемешивающими устройствами |
4 |
Сгуститель П-25 |
Сгущение пульпы серосульфидного концентрата, сгущение пульпы серного концентрата |
Сгуститель с периферическим приводом в кислотостойком исполнении, диаметр — 25 м, площадь сгущения — 500 м2, глубина чана — 3,6 м, |
5 |
Механическая флотомашина ФМР — 63К, 8-камерная |
Серосульфидная флотация |
Объем камеры — 6,3 м3 , производительность по потоку пульпы — до 12 м3 /мин |
6 |
Механическая флотомашина ФМР — 63К, 12-камерная |
Серная флотация |
Объем камеры — 6,3 м3 , производительность по потоку пульпы — до 12 м3 /мин |
7 |
Пачук для нейтрализации |
Нейтрализация хвостов серосульфид-ной флотации |
Объем — 225 м3 , из стали Х18Н10Т |
8 |
Смеситель-подогреватель |
Нагрев пульпы се-росульфидного концентрата |
Емкость — 40 м3 , из стали Х18Н10Т, с перемешивающими устройствами |
№ |
Наименование оборудования |
Назначение оборудования |
Технологические характеристики |
9 |
Автоклав дез интеграции |
Дезинтеграция пульпы серосуль-фидного концентрата |
Емкость — 50 м3, из титана ВТ1-0, рабочее давление — 5 кг/см2 , с перемешивающим устройством |
10 |
Реактор-охладитель |
Отстаивание расплавленной серы |
Емкость — 80 м3, из титана ВТ1-0, с перемешивающим устройством |
11 |
Реактор-подогреватель |
Нагрев пульпы серного концентрата |
Емкость — 50 м3, из титана ВТ1-0, рабочее давление — 5 кг/см2, с перемешивающим устройством |
12 |
Автоклав серо плавильный |
Выплавка серы |
Емкость — 32 м3 , из титана ВТ1-0, рабочее давление — 5 кг/см2, с перемешивающим устройством |
При гидрометаллургическом обогащении никель-пирротинового концентрата в качестве основных технологических материалов и реагентов используются: осадитель металлизированный, лигносульфонат технический, кислородо-воздушная смесь, технический азот, сжатый воздух, пульпа известняка, известковое молоко, моторное топливо регенерированное, бутиловый ксантогенат калия, натр едкий, нефелиновый шлам.
Основными источниками выбросов загрязняющих веществ в атмосферу являются отходящие газы автоклавов окислительного выщелачивания и аппаратов участка выплавки элементарной серы (таблица 2.2).
Таблица 2.2 — Выбросы загрязняющих веществ в атмосферу
Источники выбросов |
Выбрасываемые вредные вещества |
Метод очистки, повторного использования |
Валовый выброс, г/т Ni-сульфидного концентрата |
Автоклавы окислительного выщелачивания, пачуки нейтрализации |
Ni, Cu, Co, Fe и их соединения, серная кислота |
Улавливание брызг в каплеотбойниках |
4,4 |
Источники выбросов |
Выбрасываемые вредные вещества |
Метод очистки, повторного использования |
Валовый выброс, г/т Ni-сульфидного концентрата |
Смесители, подогреватели, самоиспарители, дезинтеграторы, автоклавы |
H2S |
Очистка в газопромывателе типа «труба Вентури», улавливание брызг в каплеотбойниках |
4280 |
Пульпа нейтрализованных отвальных хвостов, явялющаяся отходом производства, откачивается на складирование в хвостохранилище по пульпопроводу. Осветленная вода (слив хвостохранилища) возвращается в цех для повторного использования в технологии (таблица 2.3).
Таблица 2.3 — Отходы производства и потребления
Наименование |
Объем или масса образующихся отходов, т/т Ni |
Метод очистки, повторного использования |
Объем или масса размещенных отходов, т/т Ni |
Нейтрализованные хвосты серосульфидной флотации (твердая часть пульпы) |
70-75 |
- |
70-75 |
-
2.1.1.2 Производство штейна
Получение штейна в руднотермической печи РТП
В настоящее время сульфидный медно -никелевый концентрат подвергают бри -кетированию и направляют на электроплавку без обжига.
Схема переработки пульпы концентрата на стадии приготовления брикетов включает в себя следующие основные этапы:
- первичное обезвоживание пульпы на пресс -фильтрах ;
- смешивание концентрата со связующим (жидкий лигносульфонат );
- сушка смеси в сушильном барабане ;
- повторное введение в подсушенную шихту лигносульфоната;
- брикетирование шихты на валковом брикет - прессе .
Перечень основного технологического оборудования участка брикетирования приведен таблице 2.4.
Таблица 2.4 — Основное оборудование передела брикетирования концентрата
№ |
Наименование оборудования |
Назначение оборудования |
Технологические характеристики |
1 |
Контактные чаны |
Приемка концентра та |
Емкость — 50 м3 |
2 |
Ленточные сита |
Удаление инородных тел |
Площадь фильтрации — 0,825 м2, полимерный материал |
3 |
Фильтр-пресс |
Первичное обезвоживание концентрата |
Площадь фильтрации — 96 м2, количество фильтрующих плит — 16 шт., фильтровальная ткань — полипропилен, потребляемая мощность — 90 кВт, давление: подача пульпы — 0,2-1,0 МПа, прессование — 0,5-1,6 МПа, сушка — 0,41,2 МПа, вода для промывки ткани — 1,01,4 МПа |
4 |
Приемные бун кера |
Приемка первично обезвоженного концентрата |
Емкость — 50 т |
5 |
Двойной ленточный конвейер |
Т ранспортировка первично обезвоженного концентрата | |
6 |
Смеситель интенсивного действия |
Формирование шихты из CuNi-концентрата и ЛСТ заданной консистенции |
Полезный объем — 1,5 м3, длина — 3 м, диаметр — 1,1 м, число оборотов мешалки — 107, число оборотов завихрителя — 1500 |
7 |
Барабанная сушилка |
Предварительная сушка концентрата |
Диаметр — 3 м, длина — 25 м, температура: материала при загрузке — 10 °C — 20 °C, продукта на выходе — 70 °C — 90 °C, отходящих газов — 190 °С |
№ |
Наименование оборудования |
Назначение оборудования |
Технологические характеристики |
8 |
Рукавный фильтр |
Очистка газов сушильного барабана |
Площадь фильтрации 1642 м2, рабочий объемный расход газа — 100 000 м3/час, максимальная температура газов — 250 °С, расход воздуха на регенерацию — 100 м3/час, материал рукавов PTFE |
9 |
Приемный бункер сухого материала |
Приемка сухого ма териала | |
10 |
Ковшовый элеватор |
Подъем материала в смеситель | |
11 |
Шнековый смеситель |
Усреднение материала и смешение с ЛСТ |
Число оборотов шнека — 15-40 мин-1 |
12 |
Валковый брикет-пресс |
Брикетирование ма териала | |
13 |
Система конвейеров |
Т ранспортировка брикетов на склад готовой продукции |
Со склада готовой продукции готовые брикеты железнодорожным или автомобильным транспортом транспортируются на склад привозного сырья участка подготовки сырья и шихты (УПСиШ), где шихтуется со флюсом и восстановителем и транспортером по тракту подачи шихты подаются в расходные бункера РТП.
Основным сырьем для электроплавки является шихта, состоящая из: сульфидной медно-никелевой руды, брикетов, собственных и привозных оборотных никельсодержащих оборотов, флюса (песка), углеродистого восстановителя.
Физико-химические превращения шихтовых материалов и образование продуктов плавки происходит в основном в ванне печи на поверхности шихты, погруженной в шлак.
При нагреве шихты до 1000 °С в ней протекают процессы термического разложения сложных сульфидов, сульфатов, карбонатов и гидратов, а также процессы взаимодействия между различными химическими соединениями, наиболее важными из которых являются реакции между сульфидами и окислами. При повышении температуры шихты до 1000 °C-1300 °C эти процессы получают активное развитие.
Сульфиды никеля, меди, кобальта, железа расплавляются, частично разлагаются (общая десульфуризация при электроплавке составляет около 20 % — 35 %) и, взаимно растворяясь, образуют основной продукт электроплавки — штейн, в котором также растворяются драгоценные металлы и магнетит.
Полученный штейн (% масс.: никель — 7-17, медь — 3-12, кобальт — 0,6-0,8, железо — 38-50, сера — 25-27; излечение никеля в штейн составляет 97 % — 98 %, меди — 95 % — 97 %, кобальта — 77 % — 85 %) в жидком виде направляется на конвертирование.
Окисленное железо и другие основные оксиды, вступая во взаимодействие с SiO2, образуют силикаты типа mMeO х nSiO2, которые, смешиваясь в расплавленном состоянии, образуют другой продукт электроплавки — шлак. Выход шлаков при электроплавке составляет 85 % — 110 % от общей массы загруженной шихты. Основу шлаков электроплавки (97 % — 98 %) составляют кремнезем (SiO2), закись железа (FeO), окись магния (MgO), глинозем (AL2O3) и окись кальция (СаО). Содержание SiO2 в шлаке — 37 % — 42 %, Ni — не более 0,25 %, Co — не более 0,1 %.
Газы, отходящие из печного пространства при температуре 500 °C-600 °C, состоят из азота (N2), кислорода (О2), сернистого газа (SO2), углекислого газа (СО2) и паров воды (Н2О), эвакуируются через систему газоходов и подаются в пылевую камеру, а затем — в трубу. Улавливаемая в пылевой камере и газоходах металлосодержащая пыль выгружается через воронки в автомобиль и перевозится на переработку в закрытый склад СПС.
Основное оборудование процесса плавки сульфидного сырья на штейн показано в таблице 2.5.
Таблица 2.5 — Основное оборудование процесса переработки сульфидного медно-никелевого сырья на штейн в руднотермической печи
Наименование оборудования |
Назначение оборудования |
Технологические характеристики |
Руднотермическая печь |
Электроплавка руды, брикетов |
Установленная мощность — 45 МВт, число электродов — 6 шт., площадь пода — 150160 м2, количество штейновых шпуров — 3 шт., количество шлаковых шпуров — 4 шт., два торцевых и четыре боковых футерованных газохода |
Руднотермическая печь |
Электроплавка руды, брикетов |
Установленная мощность — 30 МВт, число электродов — 3 шт., площадь пода — 80 м2, количество штейновых шпуров — 3 шт., количество шлаковых шпуров — 2 шт., два водоохлаждаемых патрубка, соединяющие свод печи с вертикальными футерованными газоходами (штейновым и шлаковым) |
Получение штейна в печи взвешенной плавки
Технологическая схема получения штейна в печи взвешенной плавки включает в себя (рисунок 2.3):
- фильтрацию концентратов на керамических фильтрах ;
- сушку концентратов и флюсов в распылительных и барабанных сушилках ;
- взвешенную плавку шихты концентратов в двух печах взвешенной плавки ;
- пневматическую транспортировку высушенных концентратов;
- охлаждение отходящих газов в котле -утилизаторе с одновременной грубой очисткой от пыли;
- тонкую очистку от пыли в электрофильтрах;
- обеднение шлаков печей взвешенной плавки и конвертеров в электрообедни -тельных печах;
- грануляцию шлака обеднительных печей и его транспортирование на склад временного хранения.
Печь взвешенной плавки является головным агрегатом в цепи переработки сульфидных концентратов.
Степень обогащения дутья кислородом на печах взвешенной плавки может достигать 70 %, что позволяет вести процесс плавки в автогенном режиме, без применения дополнительного топлива. Дутье предварительно не подогревают. Пылевынос из печей взвешенной плавки составляет не более 5 % — 7 % от веса загружаемой шихты.
Медно-никелевый штейн из ПВП (Ni — 25,2 % — 28,5 %, Cu — 11,5 % — 13,6 %, Co — 0,65 %, Fe — 29,5 % — 31,8 %, S — 26,3 % — 27,0 %), как и любой штейн, представляет собой сплав сульфидов никеля, меди, железа, кобальта с небольшим содержанием магнетита, которое зависит от содержания цветных металлов. Выпуск штейна осуществляется в ковши через шпуры, расположенные в отстойной зоне печи; штейн передают на никелевое конвертирование для переработки до файнштейна.
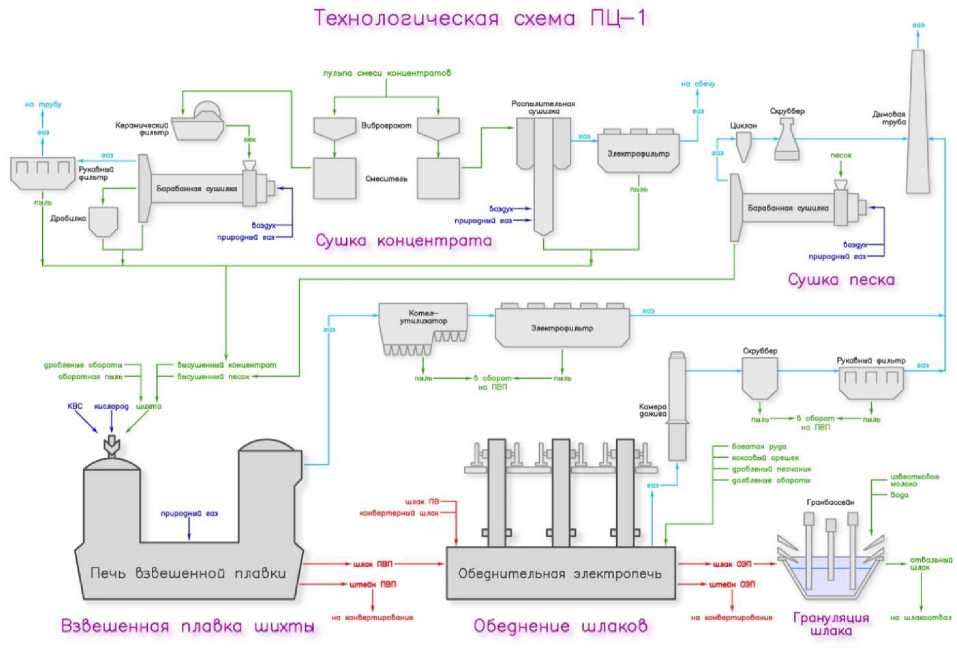
труба
Технологическая
схема ПЦ—1
Барабанная сушилка
Сушка концентрата
Сушка песка
Гранбассеан
Печь взвешенной плавки
Обеднительная электропечь
Взвешенная плавка шихты
Обеднение шлаков
J О О i j
I' "| г-— внСушвннаО Концентрат
> --- басушеннпО песок -
пул опа смеси концентра той ,_____________J______________.
Рисунок 2.1 — Аппаратурно-технологическая схема плавильного цеха № 1
— |
И 1 |
V | |
конвертирование Г рОНуЛЯЦиЯ
шлака
Шлак ПВП представляет собой многокомпонентный сплав оксидов и в значительной степени обогащен цветными металлами (таблица 2.6), в связи с чем подается (в расплавленном состоянии) в обеднительные печи (вместе с конвертерными шлаками).
Таблица 2.6 — Химический состав шлаков ПВП, %
Никель |
Медь |
Кобальт |
Железо |
Сера |
Диоксид кремния |
0,46-0,6 |
0,31-0,35 |
0,175-0,178 |
42,0-44,5 |
1,12-1,40 |
32,0-34,0 |
Основными реакциями, протекающими в реакционной шахте печи, являются реакции диссоциации и окисления сульфидов. Эти реакции экзотермические, их тепловой эффект обеспечивает самопроизвольный ход процесса без затрат тепла извне. Неокислившиеся сульфиды формируют штейн.
В отстойнике ПВП проходят основные реакции шлакообразования , обменные реакции и процесс физического разделения расплава на штейновую и шлаковую фазы, связанный с разностью их удельных весов. С учетом высокого содержания ценных компонентов в шлаках их направляют на обеднение.
При обеднении в печи периодически заливают жидкий шлак, производят загрузку твердой шихты: руду, песчаник, коксовый орешек, дробленые обороты. Руда рудников «Комсомольский» и «Октябрьский» используется в качестве извлекающей фазы (суль-фидизатора) для процесса штейнообразования, дробленый песчаник — в качестве флюсующего материала, коксовый орешек — в качестве восстановителя, дробленые бедные обороты — для регулирования состава штейна ОЭП по содержанию цветных металлов, а также в качестве металлосодержащего сырья.
Перечень основного технологического оборудования участка обезвоживания и сушки концентратов и комплекса печи взвешенной плавки приведен таблице 2.7. Параметры электропечей, используемых для обеднения шлаков ПВП и шлаков конвертирования, приведены в таблице 2.8.
Таблица 2.7 — Характеристики основного технологического оборудования обезвоживания и сушки концентратом и комплекса печи взвешенной плавки
Наименование |
Назначение |
Технические характеристики | |
1 |
Сгуститель |
Сгущение концентратов |
С центральным приводом в кислотостойком исполнении, диаметр — 12 м, глубина чана — 3 м |
2 |
Керамический фильтр СС-60 |
Фильтрация пульпы концентратов |
Площадь фильтрации (1 фильтра) — 60 м2, влажность после фильтрации — до 12 % |
Наименование |
Назначение |
Технические характеристики | |
3 |
Барабанная сушилка концентрата |
Сушка концентратов |
Диаметр — 3,2 м, длина — 27000 мм, с газовым воздухоподогревателем и системой газоочистки |
4 |
Смеситель «Денвер» |
В кислотостойком исполнении, с перемешивающим устройством, диаметр — 7,2 м, высота — 7,2 м | |
5 |
Сушилки распылительные «Ниро-Атомайзер» |
Сушка концентратов |
Диаметр — 14 м, высота — 18 м, с центробежным распылителем и газовым воздухоподогревателем «ПибодиГольмс» с горелкой кольцевого типа |
6 |
Электрофильтры «Элекс» |
Очистка газового потока распылительных сушилок |
Двухпольные, производительность по газу — 375000 нм3 /час, КПД — 99,8 % |
7 |
Сушилки барабанные |
Диаметр — 2,5 м, длина — 19500 мм, с газовым воздухоподогревателем и системой газоочистки | |
8 |
Печи взвешенной плавки «Оутокумпу» |
Плавка концентратов |
Площадь зеркала ванны — 245 м2 , с устройствами распыления шихты и подачи кислородо-воздушной смеси с обогащением кислорода до 70 %. Печь оборудована газогорелочными устройствами и выпускными шпурами штейна и шлака |
9 |
Котел-утилизатор для печи взвешенной плавки |
Охлаждение газов ПВП |
Производительность по газу — до 125 000 нм3 /час, по утилизационному пару — до 100 т/час |
10 |
Электрофильтры «Флект» |
Очистка газового потока печи ПВП |
Пятипольные, производительность по газу — 65000 нм3 /час каждый, КПД — 99,8 % |
11 |
Обеднительные электропечи «Крупп» |
Обеднение шлаков печи ПВП |
Наименование |
Назначение |
Технические характеристики | |
Обеднительные электропечи Outokumpu Technology Ou — ОЭП-1,3 |
Обеднение шлаков печи ПВП | ||
12 |
Установки грануляции отвального шлака |
Грануляция шлака обеднительных печей |
Производительность — до 250 т/ч. Тип — водная грануляция. Оборудованы системой замкнутого оборотного водоснабжения |
Таблица 2.8 — Основные характеристики обеднительных электропечей НМЗ
№ |
Наименование параметра |
Значение параметра | |
ОЭП-1,3 |
ОЭП-2,4 | ||
1 |
Мощность трансформатора, МВт А |
35 |
30 |
2 |
Площадь зеркала ванны, м2 |
175 |
176 |
3 |
Диаметр электрода, мм |
1272 |
1272 |
4 |
Распад электродов, мм |
4850 |
4850 |
5 |
Тип электродов |
Самоспекающиеся |
Самоспекающиеся |
6 |
Охлаждение корпуса |
Кессонированное |
Кессонированное |
В таблице 2.9 приведены выбросы загрязняющих веществ при производстве штейна в печах РТП и на комплексе ПВП-обеднительные электропечи.
Таблица 2.9 — Выбросы загрязняющих веществ в атмосферу при плавке в РТП на медно-никелевый штейн (на тонну никеля в штейне)
Источники выбросов |
Наименование |
Метод очистки, повторного использования |
Масса выбросов ЗВ после очистки г/т Ni |
Участок сушки и брикетирования перед РТП |
Пыль неорганическая — <20 % SiO2 |
Рукавный фильтр, фильтры аспирационных систем |
<20 мг/нм3 |
Руднотермические печи (дымовая труба) |
Пыль неорганическая — <20 % SiO2 |
Пылевая камера |
62441 |
Источники выбросов |
Наименование |
Никель | |
Кобальт | |
Медь | |
Мышьяк | |
Свинец | |
Диоксид азота | |
Оксид азота | |
Диоксид серы | |
Участок подготовки шихты, обезвоживания и сушки концентратов перед ПВП |
Пыль неорганическая — <20 % SiO2 |
Пыль неорганическая — >70 % SiO2 | |
Оксид никеля | |
Оксид меди | |
Оксид кобальта | |
Свинец | |
Диоксид серы | |
Диоксид азота | |
Комплекс печей ПВП и обеднительных печей |
Пыль неорганическая <20 % SiO2 |
Оксид никеля | |
Оксид меди | |
Оксид кобальта | |
Свинец | |
Диоксид серы | |
Диоксид азота | |
Серная кислота |
Метод очистки, повторного использования |
Масса выбросов ЗВ после очистки г/т Ni |
3602 | |
187 | |
2758 | |
457 | |
96 | |
1379 | |
224 | |
632324 | |
Выхлопные газы от различного оборудования очищаются разными методами. В технологии очистки используются: рукавные фильтры, электрофильтры, циклоны, скрубберы |
5 |
937 | |
307 | |
57,9 | |
5 | |
95399 | |
2002 | |
Выхлопные газы от различного оборудования очищаются разными методами. В технологии очистки используются: котел-утилизатор, электрофильтр, камера до-жига, скруббер, рукавный фильтр |
5065 |
52 | |
37 | |
12 | |
10 | |
5855762 | |
797 | |
45058 |
При переработке сульфидного медно-никелевого сырья в руднотермических электропечах и на комплексе ПВП-обеднительные печи образуется отвальный шлак, который подвергается грануляции. Кроме того, твёрдые отходы образуются в результате обслуживания и ремонта оборудования — выломки футеровки печей, бой кирпича, бетон, теплоизоляция, металлолом (таблица 2.10). Гранулированный отвальный шлак НМЗ используется для приготовления закладочных смесей и как материал для дорожного строительства, для отсыпки дамб, насыпей и т. д.
Таблица 2.10 — Шлаки штейновой плавки, направляемые в отвал
Наименование отхода |
Средний состав, % |
Способ утилизации |
Количество, т/т Ni в штейне |
Шлак РТП |
Ni — 0,198; Cu — 0,123; Co — 0,091; Fe — 27,71; SiO2-37,4; CaO — 2,3; MgO — 12,5; S — 1,15 |
В отвал |
12 |
Шлак обединитель- ных печей |
Ni — 0,13; Cu — 0,24; Co — 0,14; Fe — 40,3; SiO2-36,0; CaO — 2,7; MgO — 1,4; S — 1,0 |
В отвал |
15 |
2.1.1.3 Производство файнштейна
При конвертировании штейнов в конвертер могут быть загружены штейн, песок, медный шлак и другие оборотные холодные материалы (таблица 2.11). Основными реакциями, протекающими при конвертировании штейнов, являются реакции окисления, обменного взаимодействия, восстановления и шлакообразования.
2.2 Характеристика процесса конвертирования
Предприятие |
Тип штейна |
Тип окислителя |
Комбинат «Печенгани-кель» |
Штейн РТП |
Воздух |
ЗФ ПАО «ГМК «Норильский Никель» |
Штейн ПВП, штейн обеднитель-ных электропечей |
Воздух, при недостатке тепла — кислород |
При конвертировании штейнов выделяют следующие технологические операции:
- зарядка конвертера ;
- период выбора массы ;
- « варка » файнштейна;
- разливка и охлаждение файнштейна.
В период набора массы при конвертировании в шлак интенсивно удаляется железо, в результате чего количество обогащенной массы сокращается. В этот период идет активная загрузка в конвертер кварцевого песка и холодных материалов для поддержания теплового баланса процесса. После прекращения набора штейна начинается период варки файнштейна. В задачу этого периода входит почти полное удаление железа из обогащенной конвертерной массы. Полученный файнштейн содержит 23 % — 24 % S и до 3,5 % железа.
Полученный медно-никелевый файнштейн перевозится в разливочный пролет цеха и разливается в стальные формы — изложницы, зафутерованные плитами из графита, для медленного охлаждения и раскристаллизации расплава, обеспечивающих хорошие показатели разделения на никелевый и медный концентраты.
Отходящие от горловины конвертера газы содержат 7 % — 11 % SO2, однако за счет подсосов воздуха через напыльник и неплотности газохода концентрация SO2 снижается. На комбинате Печенганикель очищенные от пыли газы частично передаются в сернокислотное производство, частично — выбрасываются в трубу; в ЗФ — выбрасываются в трубу.
Химический состав продуктов конвертирования приведен в таблице 2.12, перечень основного оборудования передела конвертирования штейнов — в таблице 2.13.
Таблица 2.12 — Химический состав продуктов конвертирования
Предприятие |
Продукт |
Массовая доля, % | |||||||||
Ni |
Cu |
Co |
Fe |
S |
SiO2 |
MgO |
AI2O3 |
CaO |
Fe3O4 | ||
Комбинат «Печенга-никель» |
Шлак |
0,88 |
0,62 |
0,249 |
49,1 |
3,15 |
26 |
1,1 |
1,4 |
14,7 | |
Файн-штейн |
43 |
28 |
0,9 |
2,8 |
23,6 | ||||||
ЗФ ПАО «ГМК «Норильский Никель» |
Шлак |
2,0 2,5 |
1,5 2,0 |
0,8 1,0 |
50,0 52,0 |
1,2 1,6 |
18,0 20,0 |
0,3 |
2,2 |
0,6 |
29 |
Файн-штейн |
46 |
25 |
1,4 |
3,5 |
23 |
0,095 |
Таблица 2.13 — Характеристика основного оборудования конвертерного передела
Предприятие |
Наименование |
Назначение |
Технические характеристики |
ЗФ ПАО «ГМК «Норильский Никель» |
Конвертертипа Пирса — Смита |
Конвертирование штейна |
Емкость — 80 т, на воздушном дутье, число фурм — 48 |
Котел-утилизатор для конвертеров |
Утилизация тепла, охлаждение газов |
Производительность по газу — до 65000 нм3 /час, по утилизационному пару — до 13 т/час | |
Электрофильтры «Флект» |
Очистка газов от тонкой пыли |
Двухпольные, производительность по газу — 65000 нм3 /час каждый, КПД — 99,8 % | |
Комбинат «Пе-ченганикель» |
Конвертер Пирса — Смита |
Конвертирование штейна |
Емкость — 100 м3, длина кожуха — 12 м, внутренний диаметр кожуха — 3,96 м, число фурм — 44, диаметр фурм — 0,05 м, расход воздуха — 10-12,5 нм3/с |
1. |
Пылевая камера |
Очистка конвертерных газов крупной пыли |
д х Ш х В — 7,2 х 4,0 х 15,6 м, пропускная способность — 27 42 нм3/с, КПД — 30 % |
1. |
Электрофильтр |
Очистка газов от тонкой пыли |
Площадь сечения электрофильтра по осадительным электродам — 60 м2, КПД — 92 % |
Выбросы основных загрязняющих веществ в атмосферу при конвертировании штейна показаны в таблице 2.14.
Таблица 2.14 — Выбросы загрязняющих веществ в атмосферу при конвертировании медно-никелевого штейна (на тонну никеля в файнштейне) (за исключением газов, передаваемых на сернокислотное производство на комбинате «Печенганикель»)
Предприятие |
Метод очистки |
Наименование |
Масса выбросов ЗВ после очистки г/т Ni файнштей-на |
Комбинат «Печенга-никель» |
Пылевая каме ра, электрофильтр |
Пыль неорганическая — <20 % SiO2 |
14320 |
Диоксид азота |
851 |
Предприятие |
Метод очистки |
Наименование |
Масса выбросов ЗВ после очистки г/т Ni файнштей-на |
Кобальт |
117 | ||
Никель |
1703 | ||
Медь |
2112 | ||
Мышьяк |
95 | ||
Свинец |
24,5 | ||
Диоксид серы |
870593 | ||
Серная кислота |
681 | ||
Оксид азота |
138 | ||
ЗФ ПАО «ГМК «Но рильский Никель» |
Котел- утилизатор, электрофильтр |
Пыль неорганическая — <20 % SiO2 |
1830 |
Никель |
129 | ||
Медь |
635 | ||
Кобальт |
6 | ||
Свинец |
8 | ||
Диоксид серы |
970317 | ||
Диоксид азота |
337 | ||
Серная кислота |
7391 | ||
Оксид углерода |
501 |
2.2.1 Рафинировочные переделы
2.2.1.1 Разделение медно-никелевого файнштейна с получением никелевого сульфидного концентрата
Флотационное разделение файнштейна на медный и никелевый концентраты было предложено в конце 1940-х — начале 1950-х годов И. Н. Масленицким (АС № 113715). Согласно предложенному способу, медно-никелевый файнштейн измельчали, а затем флотировали в «обычном» режиме с переводом медных сульфидов в пенный продукт, а никелевых — в камерный. Одним из описанных И. Н. Масленицким вариантов реализации данного способа являлось применение перед флотацией магнитной сепарации, что обеспечивало не только получение более бедного по меди никелевого концентрата, но и извлечение в отдельный, обогащенный продукт основного количества содержащихся в файнштейне платиновых металлов.
Впервые процесс был внедрен на Норильском горно-металлургическом комбинате в 1957 году, и без особых изменений способ дошел до сегодняшних дней, однако за счет оптимизации реагентного режима, параметров операций и организации технологической схемы удалось достичь более низких, чем заявлено в АС, содержаний вторых металлов в концентратах.
Химическими основами флотационного разделения файнштейна являются различные условия формирования и устойчивости пленок ксантогенатов меди и никеля на поверхности соответствующих минералов. Регулированием концентрации гидроксидионов в водной части пульпы обеспечиваются условия для подавления процесса образования ксантогената никеля и образования на поверхности пленки гидроксида.
Технологический процесс разделения файнштейна на никелевый и медный концентраты включает в себя следующие технологические операции: крупное дробление, шихтовка, дробление и измельчение и собственно флотацию. Перечень основного технологического оборудования представлен в таблице 2.15.
Таблица 2.15 — Основное оборудование
№ пп |
Наименование оборудования |
Назначение оборудования |
1 |
Агрегат первичного дробения Rammer G 90 |
Первичное дробление |
2 |
Щековые дробилки ЩДП-9 х 12 и СМД-118 |
Крупное дробление |
3 |
Конусные дробилки КСД-2200Т и КМД-2200Т |
Мелкое дробление |
4 |
МШР-3200 х 3100 |
Измельчение |
5 |
Классификатор Тип I КСН-20 | |
6 |
Г идроциклон Кребса |
Г идравлическая классификация промпродуктов |
7 |
Флотационные машины ФМР-10 |
Флотация |
8 |
Флотационные машины WEMCO |
Флотация |
9 |
Сгустители тип Ц-6М1, тип Ц-9М1, тип Ц-12М1 |
Сгущение конечных и промежуточных продуктов |
10 |
Свечевые фильтры ПАР-80-248М и ПТЖ-80-3Т-41 |
Разделение файнштейна, предварительно измельченного до крупности 85 % — 95 % — 45 мкм, происходит во флотомашинах основной флотации с получением пенного и камерного продуктов, представляющих собой черновые медный и никелевый концентрат соответственно, которые затем подвергаются дополнительной очистке.
Никелевый очищается от меди за счет добавки свежего ксантогената, который повышает флотируемость медных сульфидов. Медный — от никеля, на 1-4 перечист-ных флотациях за счет повышения щелочности пульпы и снижения плотности камерных продуктов от первой до последней перечистки.
Для обеспечения эффективного разделения медных и никелевых сульфидов часть пенных и камерных промпродуктов объединяют и направляют на классификацию, пески которой доизмельчаются. Точки рецикла промпродуктов и объединения потоков пенных и камерных продуктов выбирают, исходя из их состава, в первую очередь из содержания в них вторых металлов.
Существующая технологическая схема флотационного разделения файнштейна позволяет достичь извлечения никеля в никелевый концентрат до 92 %, меди в медный — до 91 %.
Получаемый медный концентрат содержит 67 % — 68 % меди и 3,2 % — 4,2 % никеля, никелевый — 68 % — 69 % никеля и 2,3 % - 2,9 % меди.
При разделении медно-никелевого файнштейна в качестве основных технологических материалов используются бутиловый ксантогенат калия, сода каустическая, шары стальные и вода оборотного водоснабжения.
Образующие при разделении файнштейна соединения меди, никеля и кобальта попадают в атмосферу в составе пыли, выделяющейся через неплотности технологического оборудования. Вредности удаляются с вентвыбросами естественным путем через дефлекторы и вентшахты (таблица 2.16).
Таблица 2.16 — Выбросы загрязняющих веществ в атмосферу
Наименование |
Масса выбросов ЗВ до очистки, г/т Ni |
Источники выбросов |
Метод очистки, повторного использования |
Масса выбросов ЗВ после очистки, г/т Ni |
Кобальт и его соединения (в пересчете на кобальт) |
5,7 |
Дробилки, транспортеры, мельницы , классификато- |
- |
5,7 |
Наименование |
Масса выбросов ЗВ до очистки, г/т Ni |
Источники выбросов ры, сгустители, флотомашины |
Метод очистки, повторного использования |
Масса выбросов ЗВ после очистки, г/т Ni |
Никель и его соединения (в пересчете на никель) |
192,8 |
- |
192,8 | |
Медь и ее соединения (в пе ресчете на медь) |
44,7 |
- |
44,7 | |
Пыль неоргани ческая |
406,1 |
- |
406,1 |
Жидкая фаза, образующаяся при обезвоживании продуктов флотации (никелевого и медного концентратов), наплавляется в систему оборотного водоснабжения участка. Избыточное количество воды передается в производственную канализацию; сброс воды в природные объекты отсутствует (таблица 2.17).
Таблица 2.17 — Состав и способ утилизации сточных вод
Наименование |
Масса сбросов ЗВ до очистки, г/т Ni |
Источники сброса |
Направление сброса (водный объект, канализация) |
Метод очистки, повторного использования |
Масса сбросов ЗВ после очистки, г/т Ni |
Никель в/р |
<4,1 |
Верхний слив отстойников, фильтрат свечевых фильтров |
Оборотное водоснабжение участка, производственная канализация |
Оборотное водоснабжение участка |
<4,1 |
Медь в/р |
<0,08 |
<0,08 | |||
Взвешенные вещества |
<123 |
<123 | |||
Ксантогенат |
<0,008 |
<0,008 |
Твердые отходы процесса образуются в ходе ремонтных и строительных работ.
2.2.1.2 Получение частично восстановленного никелевого огарка
Технология получения частично восстановленного никелевого огарка (ПНТП — порошка никелевого трубчатых печей) включает в себя операции обезвоживания никелевого концентрата флотации файнштейна, его окислительного обжига в печах кипящего слоя и восстановительного обжига в трубчатых вращающихся печах.
Окислительный обжиг, целью которого является максимальное удаление серы и подготовка материала к восстановлению, ведется при температуре 1050 °C-1250 °C. Загрузку шихты регулируют по температуре в слое, по концентрации диоксида серы (SO2) в отходящих газах, по заданному расходу воздуха (или воздуха, обогащенного кислородом).
Основная часть полученного огарка передается на восстановление в трубчатые вращающиеся печи, часть — в бункер «горячего» огарка для использования его без восстановления при доводке анодного металла по углероду.
Газы после прохождения через систему газоочистки, включающей в себя охладитель газов, циклоны испарительного охлаждения и электрофильтр, передаются в сернокислотное производство. Газы аспирационных систем передаются в общий газоход и выбрасываются в трубу.
В процессе (1050 °C-1150 °C) происходит дальнейшее укрупнение огарка и восстановление до металла присутствующих в огарке никеля и кобальта (85 % — 90 %), а также части железа и меди. В качестве восстановителя используют доменный кокс и уголь в количестве 12 % — 14 %.
Перечень основного технологического оборудования приведен в таблице 2.18, выбросы основных загрязняющих веществ в атмосферу при получении ПНТП — в таблице 2.19, характеристика сточных вод — в таблице 2.20.
Таблица 2.18 — Перечень основного технологического оборудования
№ |
Наименование оборудования |
Назначение оборудования |
Характеристика оборудования |
1 |
Сгустители Ц9 |
Сгущение пульпы никелевого концентрата |
Площадь поверхности 60 м |
2 |
Сгустители Ц12 |
Сгущение пульпы никелевого концентрата |
Площадь поверхности 110 м |
№ |
Наименование оборудования |
Назначение оборудования |
Характеристика оборудования |
3 |
Барабанный ва куумный фильтр |
Фильтрация сгущенного никелевого концентрата |
Площадь фильтрации — 40 м2, содержание влаги в кеке — 6 % — 9 % |
4 |
Печь кипящего слоя |
Обжиг концентрата |
Площадь пода — 24 м2 |
5 |
Трубчатая вращающаяся печь (ТВП) |
Восстановление огарка окислительного обжига |
Длина печи — 20 м, диаметр печи — 2,2 м, диаметр в свету — 1,688 м |
Таблица 2.19 — Выбросы загрязняющих веществ в атмосферу при получении ПНТП
Источники выбросов |
Наименование |
Метод очистки |
Масса выбросов ЗВ после очистки г/т Ni в анодах |
Трубчатые печи, печи кипящего слоя |
Диоксид азота |
Охладители газов, циклоны, электрофильтры, струйно-пенные аппараты |
20,7 |
Кобальт |
140 | ||
Никель |
7 124 | ||
Медь |
367 | ||
Мышьяк |
35 | ||
Пыль неоргани ческая |
21 284 | ||
Свинец |
395 | ||
Диоксид серы |
6 718 |
Таблица 2.20 — Сточные воды, образующиеся при получении ПНТП
Наименование сточных вод по переделам |
Нормируемое количество в сутки, м3/т Ni |
Содержание вредных примесей |
Место сброса |
Оборотная вода комбината |
0,005 |
Не более уровня в оборотной системы |
Самотечные коллекторы оборотной системы |
В ходе ремонтных и строительных работ образуются твердые отходы процесса получения ПНТП: выломки футеровки печей, бой кирпича, бетон, теплоизоляция, металлолом.
2.2.1.3 Производство черновых никелевых анодов
На сегодняшний день основная часть никелевого порошка трубчатых печей поступает на анодную плавку в дуговые электропечи, часть — на хлорное растворение для восполнения дефицита никеля. Шихта печей включает в себя, помимо порошка, восстановитель и анодный скрап.
При расплавлении шихты свободной углерод и закись никеля растворяются в расплавленном металле, при этом происходит «науглероживание» ванны металла по реакции с образованием карбида никеля (Ni3C), который при растворении в металле взаимодействует с закисью никеля.
Растворимость углерода в металле высока, и на начальных этапах плавки с учетом положительного влияния науглероживания расплава на температуру плавления металла процесс ведут с избытком восстановителя, который на финальных этапах удаляют присадкой огарка в жидкий металл. Доводка металла по содержанию углерода может также осуществляться кислородной продувкой.
К моменту полного расплавления шихты в печи образуются шлаковая и металлические фазы. В основном шлак состоит из окислов, содержание которых может достигнуть 95 %. Снижение потерь цветных металлов со шлаками и увеличение их извлечения в анодной никель происходит тем полнее, чем лучше восстановительные условия в печи и чем выше активность окислов в шлаке, которая зависит от количества флюсующих добавок, таких как известняк, окись кремния.
После обеднения шлака избыток его порционно сливают путем наклона печи. При этом богатая часть шлака возвращается на плавку, а бедная — отправляется на переработку в РТП. Готовый металл разливается по изложницам карусельной машины и направляется на электролитическое рафинирование с получением катодного метал -ла. Запыленные отходящие газы очищаются в электрофильтрах и выбрасываются в атмосферу.
Перечень основного технологического оборудования приведен в таблице 2.21, выбросы загрязняющих веществ — в таблице 2.22.
Таблица 2.21 — Перечень основного технологического оборудования
№ |
Наименование оборудования |
Основные характеристики |
1 |
Бункер восстановленной закиси |
Емкость — 40 т |
1 |
Емкость — 60 т | |
2 |
Бункер невосстановленной закиси |
Емкость — 10 т |
№ |
Наименование оборудования |
Основные характеристики |
1 |
Емкость — 5 т | |
3 |
Бункер восстановителя |
Объем — 25 м3 |
4 |
Питатель тарельчатый |
Диаметр тарелки — 1000 мм |
1 |
Диаметр тарелки — 800 мм | |
5 |
Питатель шнековый |
Диаметр шнека — 450 мм |
6 |
Электропечь РКЗ № 1 |
Мощность трансформатора — 12500 кВА |
7 |
Электропечь ОКБ № 2 |
Мощность трансформатора — 9000 кВА |
8 |
Электропечь РКЗ № 3 |
Мощность трансформатора — 15000 кВА |
9 |
Индукционный миксер ИЧТМ-16 |
Мощность трансформатора — 1300 кВА |
10 |
Индукционный миксер ИЧТМ-16 |
Мощность трансформатора — 1600 кВА |
11 |
Разливочная машина |
Диаметр — 10 м |
Таблица 2.22 — Выбросы загрязняющих веществ в атмосферу при анодной плавке
Источники выбросов |
Наименование |
Метод очистки |
Масса выбросов ЗВ после очистки, г/т Ni в анодах |
Печи, карусельноразливочные машины, загрузочные бункера |
Никель |
Циклоны, электрофильтр |
1985 |
Кобальт |
38,8 | ||
Медь |
228 | ||
Мышьяк |
4,8 | ||
Пыль неоргани ческая |
4105 | ||
Свинец |
25,7 | ||
Диоксид серы |
402 |
Шлак анодной плавки, выломки футеровки, улавливаемая в электрофильтрах пыль не являются отвальными продуктами и направляются на переработку на другие переделы технологического цикла. Прочие твердые отходы передела связаны с проведением ремонта оборудования и зданий.
2.2.1.4 Получение катодного никеля
Электролитическое рафинирование черновых никелевых анодов — достаточно старая технология, обеспечивающая получение товарного никеля в том числе из драгметаллсодержащего сырья. В настоящее время производство сохранилось только на Кольской ГМК. Следует отметить, что и на КГМК также предусматривается постепенная 120
замена технологии рафинирования черновых анодов рафинированием никелевого порошка трубчатых печей (ПНТП).
Наряду с металлическим никелем черновые аноды содержат первые проценты основных примесей: железа и меди, кобальта и доли процента серы. Кроме того, в черновых анодах содержится широкий спектр различных микропримесей, включая драгоценные металлы. Рафинирование черновых никелевых анодов осуществляется в электролизных ваннах (электролизерах ящичного типа) с разделением катодного и анодного пространств проточной тканевой диафрагмой. При этом используется суль-фат-хлоридный никелевый электролит. Катоды внутри ванн помещены в диафрагменные ячейки, а аноды находятся в общем анодном пространстве. За счет прохождения постоянного тока на анодах происходит растворение никеля и примесей с получением загрязненного никелевого раствора — анолита. На катодах в эквивалентном пропущенному току количестве осаждается чистый катодный никель. В каждую катодную ячейку непрерывно подается очищенный от примесей никелевый раствор — католит. За счет его подачи уровень раствора в катодных ячейках превышает уровень в анодном пространстве. Католит просачивается через поры диафрагмы в анодное пространство ванны, препятствуя попаданию в катодное пространство примесей из анолита. После прохождения через диафрагму католит объединяется с анолитом и самотеком удаляется из ванны на очистку. Часть анодных примесей не растворяется и, преимущественно осаждаясь в донной части анодного пространства ванны, формирует на поверхности анода нерастворимый шлам, в котором, в частности, концентрируются драгоценные металлы.
Осаждение товарного никеля осуществляется на никелевые основы, которые производятся в отдельных электролизных ваннах путем катодного осаждения никеля на титановые матрицы. Такие ванны, в отличие от ванн производства товарного никеля, называются матричными. Срок наращивания основ составляет 12-24 ч. Катоды с осажденными на них основами выгружаются, промываются, основы сдираются и правятся. К ним контактной сваркой привариваются вырезанные из основ ушки. Никелевые основы с приваренными ушками загружаются в товарные ванны для наращивания на них товарных никелевых катодов. Срок наращивания товарных катодов (катодная компания) составляет 3-4 сут. По завершении катодной компании товарные катоды выгружаются, промываются и передаются в дальнейшую обработку, включающую взвешивание, пробоотбор, резку, сортировку (разбраковку), фасовку (упаковку) первичного никеля для отправки партиями на склад готовой продукции. По завершении анодной компании осуществляется чистка ванн. Перед чисткой ванны шунтируются. Из ванн выгружаются анодный скрап и катодные ячейки, ванны опорожняются и очищаются от идущего на производство драгоценных металлов шлама. Растворившаяся часть анодов из ванн — скрап после промывки от шлама направляется на анодную плавку. Анодная осыпь направляется на хлорное выщелачивание либо на анодную плавку. После чистки в ванны устанавливаются новые аноды и катодные ячейки, ванна заполняется католитом и цикл рафинирования повторяется.
Загрязненный примесями анолит из ванн очищается от примесей гидрометаллургическими способами, включающими в себя последовательное удаление железа путем его окисления воздухом в присутствии основного карбоната никеля в качестве нейтрализатора, меди — цементационным осаждением на ПНТП и кобальта при окислении хлором в присутствии нейтрализатора — основного карбоната никеля.
После корректировки кислотности очищенный от кобальта раствор в качестве католита подается в ванны рафинирования. Первичный железистый кек репульпируется для удаления из него никеля и получения отвального гидратного железистого кека.
Кобальтовый кек также репульпируется для удаления присутствующего в нем никеля и направляется на производство катодного кобальта.
Содержащая никель и иные примеси цементная медь передается в производство меди. Дефицит водорастворимого никеля восполняется хлорированием ПНТП. Основной карбонат никеля для очистки от примесей получают на карбонатном переделе с использованием бедных никелевых растворов от репульпации первичных кеков примесей. Осаждение карбоната осуществляется раствором кальцинированной соды. В производство вовлекаются никельсодержащие растворы и иные полупродукты смежных медного и кобальтового производств, а также продукты участка переработки шламов. На репульпациях и для регулирования кислотности по операциям очисток используется серная кислота смежного сернокислотного производства, производимая как попутный продукт из газов пирометаллургических производств. В качестве основных отходов производства образуются очищенные от цветных металлов сульфат-хлоридные сливы карбонатного передела и отвальный железистый кек.
Организационно производство электролитного никеля включает в себя три основных отделения: электролизное, гидрометаллургическое (ГМО) и отделение готовой продукции. Основное технологическое оборудование (таблица 2.23), трубопроводы и запорная арматура преимущественно выполнены в титановом исполнении либо из стали с кислотоупорной футеровкой.
Таблица 2.23 — Основное технологическое оборудование цеха электролиза никеля
Наименование оборудования |
Назначение |
Характеристика |
Электролизное отделение | ||
Ванны электролизные |
Получение катодного никеля |
Полимербетонные ванны, 51 51 анодов, 49-50 катодов, с рабочей поверхностью 935 х1085 |
Мостовые краны |
Q = 10 т, Н = 13 м , L = 21 м | |
Спецкраны |
Обслуживание ванн |
Q = 3,2/30 т, L = 10,5 м |
Гильотинные и дисковые ножницы |
Резка основ на уши, резка заготовок основ | |
Машины точечной сварки |
Приварка ушей |
МТ-1222 (МТ-2202) |
Г идрометаллургическое отделение | ||
Баковое оборудование |
Сборники католита и анолита |
Емкость — до 400 м3 |
Аппараты с пневматическим перемешиванием (пачуки) |
Реакционное оборудо вание |
Емкость — до 170 м3 |
Аппараты с механическим перемешиванием, с коническим и плоским днищем |
Репульпация осадков, проведение технологических процессов |
Емкость — до 20 м3 |
Аппараты с перемешиванием в псевдоожиженном слое (цементаторы) |
Очистка анолита от примесей |
Емкость — до 90 м3 |
Патронные фильтры |
Разделение жидкого и твердого | |
Дисковые вакуумные фильтры |
Разделение жидкого и твердого | |
Фильтр-прессы рамные |
Разделение жидкого и твердого | |
Ленточный вакуумный фильтр |
Разделение жидкого и твердого | |
Гидроциклон |
Разделение жидкого и твердого |
Наименование оборудования |
Назначение |
Характеристика |
Сгуститель одноярусный, с центральным приводом |
Разделение жидкого и твердого | |
Двухспиральные классифи каторы |
Разделение жидкого и твердого |
Диаметр спиралей — 280 мм, шаг спиралей — 300 мм |
Отделение готовой продукции | ||
Мостовые краны |
Транспортировка готовой продукции |
Q = 5/20 т |
Аккумуляторные погрузчики, электрические моторные тележки |
Транспортировка готовой продукции |
Q = 10 т |
Гильотинные ножницы кривошипные, линии автоматической резки |
Резка катодов | |
Приспособления для фасовки и упаковки товарного никеля |
Упаковка катодов |
В процессе многолетней эксплуатации технология рафинирования черновых никелевых анодов непрерывно совершенствовалась, и к настоящему времени пути ее дальнейшего улучшения практически исчерпаны и экономически бесперспективны. Именно поэтому эта технология, имевшая ранее широкое распространение, повсеместно замещена более современными способами. Основные недостатки технологии рафинирования черновых никелевых анодов определяются собственно необходимостью их производства. Альтернативные гидрометаллургические способы рафинирования файнштейна или продуктов его переработки предполагают в качестве товарного передела электроэкстракцию никеля из хлоридных или сульфатных растворов. При этом передел производства черновых никелевых анодов заменяется переделом растворения файнштейна или продуктов его переработки. Очевидны следующие общие преимущества подобных решений:
- ликвидация затрат на производство промежуточных продуктов , а именно чер -новых анодов;
- ликвидация определяющихся наличием анодного скрапа оборотов;
- существенное упрощение обслуживания электролизных ванн (обработка ано -дов и скрапа, чистка ванн с выделением и переработкой шлама);
- возможности более полной механизации и внедрения дополнительных , более совершенных систем контроля процессов рафинирования;
- возможности использования более современного основного оборудования ;
- существенное сокращение незавершенного производства (срок растворения черновых анодов составляет приблизительно 30 сут, кроме того, он увеличивается за счет наличия оборотного скрапа).
Кроме того, в зависимости от состава перерабатываемого сырья, основы рафинировочного раствора, конфигурации рафинировочных мощностей и принципа конкретных рафинировочных операций используются различные реагенты и энергоносители и формируются различные отходы.
Исходным сырьем процессов гидрометаллургического рафинирования может быть как собственно файнштейн, так и продукты его переработки, в частности никелевый концентрат и/или металлизированная фракция от разделения файнштейна.
В настоящее время на Кольской ГМК — единственном отечественном предприя -тии, выпускающем товарный никель высокой чистоты, начался постепенный переход от технологии рафинирования черновых никелевых анодов к гидрометаллургической технологии рафинирования. Эта технология предусматривает получение товарного никеля электроэкстракцией из хлоридных растворов. На первом этапе в качестве исходного сырья предусматривается использование НПТП. В дальнейшей перспективе представляется целесообразным использование в качестве обособленного сырья металлизированной фракции от разделения файнштейна и далее никелевого концентрата от разделения файнштейна. Замена НПТП никелевым концентратом позволит полностью ликвидировать переделы окислительного и восстановительного обжига, что позволит существенно сократить в том числе потери ценных компонентов, трудозатраты, энергозатраты и эмиссию вредных веществ.
На сегодняшний день хлорное растворение ПНТП играет вспомогательную роль в производстве товарного никеля и преследует цель восполнения дефицита никеля и сокращения оборотов цеха электролиза, однако в ближайшей перспективе данный процесс должен полностью вытеснить морально и физически устаревшее электрорафинирование черновых анодов.
По химическому составу ПНТП близок черновым никелевым анодам, однако содержит значительное количество кремния, кальция, магния и алюминия, поступающих в процесс с зольной составляющей угля, используемого на операции восстановления.
Технология переработки ПНТП включает в себя три основных блока: хлорное растворение в обедненном никелевом растворе, очистку от примесей и электроэкстракцию никеля.
В процессе хлорного растворения в жидкую часть пульпы извлекаются никель и основные примеси, при этом сера и драгоценные металлы коллектируются в нерастворимом остатке. Хлорное выщелачивание осуществляется в аппаратах с псевдоожижением — цементаторах.
Обогащенный никелем раствор хлорного выщелачивания очищается от примесей совместно с анолитом от рафинирования черновых анодов, при этом данный факт следует рассматривать как временную меру. Очищенный от примесей, богатый никелем продукционный раствор в качестве католита поступает в ванны электроэкстракции.
Электроэкстракция никеля осуществляется в полимербетонных электролизных ваннах с разделением катодного и анодного пространств проточной тканевой диафрагмой. При этом используется общий с рафинировочными ваннами никелевый электролит. Нерастворимые титановые аноды с активным покрытием типа ОРТА помещены в оборудованные колпаками и работающие под разряжением диафрагменные ячейки, а катоды находятся в общем катодном пространстве ванны . За счет прохождения по -стоянного тока на анодах выделяется хлор. На катодах в эквивалентном пропущенному току количестве осаждается чистый катодный никель. Католит непрерывно подается в общее катодное пространство ванны. Из каждой анодной ячейки анолит совместно с анодным хлором эвакуируется за счет разряжения в бортовой коллектор. Католит просачивается через поры диафрагмы в анодные ячейки, препятствуя попаданию в катодное пространство хлора. Анодный хлор-газ отделяется от анолита вне ванны, в бортовом коллекторе, и направляется на хлорное выщелачивание ПНТП. Анолит направляется на совместную с анолитом рафинировочных ванн очистку от примесей.
Обслуживание электролизных ванн не требует их остановки, чистки и замены анодов. Осаждение катодного никеля осуществляется на никелевых основах. Операции изготовления никелевых основ и обработки товарных катодов при электроэкстракции никеля и рафинировании черновых никелевых анодов совпадают.
С учетом одновременной эксплуатации электрорафинирования черновых никелевых анодов и рафинирования ПНТП в технологической цепочке используется основное технологическое оборудование электролизного отделения рафинирования черновых никелевых анодов. Принципиально отличается лишь конструкция и расположение электродов внутри электролизных ванн, а также обвязка ванн по растворам. В каждой ванне 61 стационарный нерастворимый титановый анод с активным покрытием типа ОРТА и 60 катодов, рабочей поверхностью 935 х 1340 мм. Вдоль борта ванны проходит коллектор для совместной эвакуации анолита и хлора. Сохраняется попарная группировка ванн в блоки с последовательным подключением ванн по току в серии. Максимальная токовая нагрузка — до 35 кА.
Основное технологическое оборудование гидрометаллургического отделения и отделения готовой продукции является общим с технологией производства никеля через рафинирование черновых никелевых анодов.
При рафинировании черновых никелевых анодов и ПНТП используются следующие основные материалы и реагенты: кислота серная, хлор, сода кальцинированная, борная кислота (будет исключена по завершении переходного этапа), ткани диафрагменная (хлопколавсановая) и фильтровальные (лавсановая, полипропиленовая и смесовые).
При производстве катодного никеля основными вредными веществами, выбрасываемыми в атмосферу, является никель (в том числе в водорастворимой форме), серная кислота в виде аэрозолей, а также хлор. Удаление аэрозолей осуществляется через аэрационные фонари и систему вытяжной вентиляции электролизного отделения (таблица 2.24).
Удаление паровоздушной хлорсодержащей смеси производится с помощью аспирационных систем из емкостного оборудования с последующей очисткой в пенных аппаратах.
Таблица 2.24 — Выбросы загрязняющих веществ в атмосферу при производстве никелевых катодов
Наименование |
Источники выбросов |
Метод очистки, повторного использования |
Масса выбросов ЗВ после очистки г/т Ni |
Никель и его соединения (в пересчете на никель) |
Электролизные ванны, емкостное оборудование |
- |
9,0 |
Серная кислота |
Емкостное оборудование |
- |
10,6 |
Хлор |
Очистка анолита от кобальта, восполнение дефицита нике-ля/рафинирование ПНТП |
Очистка содовыми растворами в пенных газоочистителях |
77,6 |
Сточные воды образуются в результате получения карбоната никеля и вследствие использования на очистных операциях основных реагентов — серной кислоты, соды каустической и хлора.
Твердые отходы передела получения товарного электролитного никеля образуются в процессе эксплуатации электролизных ванн и очистки никелевого анолита от железа. Железистый кек, отходы диафрагменных тканей и кек отстойников складируют совместно как один отвальный продукт.
2.2.1.5 Производство карбонильного никеля
Сырьем для карбонильного производства служат никелевые гранулы, выплавляемые из продуктов обжигового отделения и собственных оборотов ЭПО РЦ, а также различных видов привозных металлосодержащих материалов других цехов в рафинировочном цехе.
Физико-химические показатели гранул никелевых в соответствии с
ТУ 9-052-48200234—2010: никель — не менее 85,0 %, медь — не более 5,0 %, железо — не более 4,0 %; сера — 1,5 % — 3,0 %; углерод — не более 0,1 %; содержание влаги — не более 0,5 %; насыпная плотность — не менее 3,6 т/м3; крупность — не более 75 мм.
Основными переделами процесса являются передел газификации пекового кокса, синтеза, ректификации и разложения тетракарбонила никеля.
Передел газификации пекового кокса предназначен для получения оксида углерода газификацией пекового кокса в газогенераторе. Полученный оксид углерода очищают от пыли водой в пенном аппарате и в скрубберах, при этом коксовая пыль смывается водой в водяные баки.
Передел синтеза предназначен для получения тетракарбонила никеля (ТКН) способом карбонилирования твердых никельсодержащих материалов оксидом углерода под высоким давлением.
Передел синтеза ТКН состоит из технологических секций, где расположены установки синтеза, коридор разводки трубопроводов, помещения пароперегревателя, камер приточной, вытяжной и аварийной вентиляции, узла производственного водоснабжения, пульта управления, административных и бытовых помещений, понизительной подстанции с пультом управления, помещений РП и ремонтных мастерских.
В состав установки синтеза входят реакционные колонны , подогреватели реак -ционного газа, пылевой фильтр, холодильник-конденсатор, сборник-отделитель и контрольный сборник — отделитель сырого ТКН, сборник — разрядник сырого ТКН и фильтры для отделения масла и влаги (маслоловушки). Циркуляция реакционного газа в процессе синтеза ТКН осуществляется циркуляционным компрессором, расположенным на переделе газовых компрессоров.
После окончания загрузки сырья в колонны и закрытия верхних затворов система трубопроводов и аппаратов установки синтеза ТКН опрессовывается азотом, затем после полного сброса давления промывочного газа включаются в работу циркуляционный компрессор и подогреватель газа. Подогретый реакционный газ подается в нижнюю часть колонны, проходит через слой сырья и извлекает из него никель в виде карбонила никеля. Кроме карбонила никеля, в процессе синтеза происходит образование карбонилов железа и кобальта.
Для восполнения убыли оксида углерода, который расходуется на образование карбонилов и частично растворяется в жидком карбониле, система непрерывно или периодически подпитывается «свежим» газом из ресиверов высокого давления.
Выходящий из колонн реакционный газ, содержащий пары карбонилов, проходит через выносной пылевой фильтр и направляется в холодильник-конденсатор (аппарат типа «труба в трубе»), где за счет снижения температуры газа до 10 °C-40 °C происходит конденсация паров карбонилов. Конденсат отделяется от газа в системе сборников-отделителей, которые представляют собой горизонтальные цилиндрические аппараты высокого давления.
Реакционный газ из сборника-отделителя через маслоловушку направляется в циркуляционный компрессор, из которого подается в подогреватели и поступает вновь в колонны синтеза.
В сырой карбонил извлекается до 96 % - 97 % никеля, до 15 % кобальта, до 70 % железа. Практически вся медь, сера и благородные металлы остаются в остатках синтеза, которые затем направляются на обжиг в трубчатой печи для полной дегазации и сульфатизирующего обжига остатков синтеза, обеспечивающего подготовку материала к переработке в цикле основного производства.
Передел ректификации предназначен для производства дистиллята тетракарбонила никеля, получаемого путем отгонки его из смеси нагретых карбонилов никеля, железа и кобальта, с последующей термической обработкой кубовых остатков с образованием остатков дожигания.
При нагревании исходного продукта в кубе карбонил никеля полностью испаряется, карбонил железа испаряется частично и в основном остается в кубе. В процессе ректификации поднимающиеся в колонне пары постепенно обогащаются низкокипя-щим компонентом смеси, а стекающая вниз жидкость — высококипящим компонентом. Пар, выходящий из верхней части ректификационной колонны, представляет собой чистый легколетучий компонент смеси, конденсация которого дает готовый продукт — дистиллят, основная часть которого направляется в соответствующие сборники для производства готовой продукции, а другая часть в виде флегмы остается в ректификационной колонне. Из нижней части куба отбирается продукт, богатый высококипящим компонентом, который является кубовым остатком, и дополнительно перегоняется в колоннах II ректификации.
Установки ректификации размещены в помещениях четырех технологических секций, в том числе четыре установки I ректификации, две установки II ректификации, промежуточные аппараты, сборники и емкости. Все аппараты соединены с газгольдерами оксида углерода уравнительными трубопроводами.
Очищенные пары карбонила никеля конденсируются и охлаждаются в дефлегматоре (трубчатый теплообменник, охлаждаемый проточной холодной водой). Пары, не успевшие сконденсироваться в дефлегматоре, попадают в конденсатор остаточного газа, где происходит их окончательная конденсация. Часть конденсата направляется в колонну на орошение насадки (флегма), остальная часть (дистиллят) выводится из колонны в сборники, из которых давлением оксида углерода передавливается в напорные баки отделения разложения, ОПУ дроби и спецпорошков.
Кубовые остатки первой ректификации направляются в сборник, из которого подаются на дополнительную перегонку в колонны II ректификации. Дистиллят II ректификации направляют в сборники I ректификации на повторную очистку.
Кубовые остатки II ректификации направляют в сборник, из которого их передавливают в промежуточный аппарат и далее, самотеком, продукт поступает на термическую дегазацию в печь дожигания № 1.
Передел разложения тетракарбонила никеля предназначен для производства карбонильных никелевых порошков и карбонильной никелевой дроби путем термического разложения тетракарбонила никеля.
Выделившийся оксид углерода направляется из разложителя на очистку от никелевого порошка, а затем направляется в газгольдеры оборотного газа.
Передел разложения состоит из пяти технологических секций, разделенных по горизонтали перекрытиями на три уровня. В каждой секции расположены четыре установки разложения, связанные через общий коллектор парообразного ТКН с башней, где установлены два напорных бака, два испарителя, буферная емкость, две газодувки и система обогрева испарителя .
Получение никелевых порошков разной насыпной плотности обеспечивается ведением процесса разложения паров ТКН при различных температурных режимах и различных количествах подачи паров ТКН в реторту разложителя.
Наращивание дроби осуществляют термическим разложением паров карбонила никеля на нагретой поверхности непрерывно циркулирующей исходной загрузки, составленной из дроби разных фракций размерами от -1 до +10 мм. Постоянно работающий вертикальный ковшовый элеватор забирает дробь внизу на выходе из аппарата и поднимает ее наверх , где она разгружается из ковшей и вновь поступает в аппарат на укрупнение.
2.3 Производство никеля из окисленных рудПлавкой окисленных никелевых руд в России занимаются три уральских предприятия: комбинаты «Южуралникель» и «Уфалейникель», а также Режский никелевый завод (см. ниже).
Все три предприятия находятся на значительном удалении (200-500 км) от действующих рудников: комбинат «Южуралникель» — в г. Орск (Оренбургская обл.), Реж-ский никелевый завод — в г. Реж (Свердловская обл.), комбинат «Уфалейникель» — в г. Верхний Уфалей (Челябинская обл.).
На всех трех предприятиях все еще применяется шахтная плавка агломерированной руды на штейн.
Производственные мощности комбината «Южуралникель» (с 2001 гогда комбинат входит в ОАО «Мечел») были законсервированы в декабре 2012 г. и выставлены на продажу, но покупателя пока не нашлось. Мощности могут быть перезапущены в случае кардинального изменения ситуации на рынке никеля и роста цен на металл.
Сырьем для комбината являлась окисленная руда Буруктальского и Сахаринско-го месторождений. Буруктальский рудник расположен рядом с г. Светлый в Оренбургской области, рядом с границей с Казахстаном и в 230 км к востоку от Орска. Сахарин-ский рудник расположен в Челябинской области — в 10-15 км от пос. Субутак и примерно в 375 км от Орска. Руду с обоих рудников по железной дороге перевозят в Орск. Примерный состав руд приведен в таблице 2.25.
Таблица 2.25 — Примерный химический состав Буруктальской и Сахаринской руд
Ni |
Co |
F еобщ |
MgO |
CaO |
SiO2 |
AhO3 |
Cr2O3 | |
Бурукталь-ская |
1,02 |
0,115 |
23,1 |
11,8 |
0,8 |
41,5 |
3,5 |
1,7 |
Сахарин-ская |
1,09 |
0,055 |
20,6 |
10,5 |
0,7 |
41,4 |
5,0 |
1,9 |
На переработку поступала смесь руд двух месторождений (примерно в соотношении 1 : 1-2 : 1. Руду сушили и агломерировали. Агломерат имеет примерный состав, %: Ni — 1,15-1,20; Co — 0,08-0,1; Беобщ — 22,5-24,5; SiO2-45-48; MgO — 12-13; CaO — 0,7-1,2; Al2O3-4-5; C-0,5-2,0. Этот агломерат в смеси с коксом, сульфидизато-ром (железным колчеданом) и флюсом (известняком) плавят в шахтной печи на штейн. Штейн шахтных печей продувается в конвертерах до файнштейна, содержащего 78 % — 79,5 % никеля, 0,3 % — 0,5 % кобальта, 0,2 % — 0,3 % железа, 0,8 % — 2,5 % меди и 17 % — 19 % серы. Фанштейн дробится, измельчается и обжигается в две стадии.
Первая стадия осуществляется в печах КС при температуре 900 °C-950 °C, при этом обеспечивается снижение содержания серы до 1,0 % — 1,5 %. Полученный огарок полностью или частично подвергают хлорирующему обжигу для очистки от меди. С этой целью огарок печей КС в горячем состоянии смешивают с 10 % — 15 % сильвинита и обжигают при температуре 700 °C-750 °C. Образующиеся при этом хлориды и сульфаты меди хорошо выщелачиваются горячим (70 °C-80 °C) слабым раствором серной кислоты. Выщелоченный огарок вместе с газоходной пылью, пылью электрофильтров и другими оборотными материалами поступает на вторую стадию окислительного обжига в трубчатой вращающейся печи (750 °C-800 °C в хвостовой части, куда идет загрузка, и 1250 °C-1300 °C — в головной, в месте выгрузки) с целью получения закиси никеля, содержащей не более 0,02 % серы.
Полученная в результате двойного обжига закись никеля может быть восстановлена до металла в дуговых электропечах с восстановителем (нефтяной или пековый кокс). В последнее время в электропечь загружали железные отходы, поэтому получали не огневой никель, как раньше, а так называемый маложелезистый ферроникель, содержащий более 85 % никеля и 4 % — 12 % железа, что, заметим, снижает требования по содержанию кобальта (максимальное содержание кобальта в огневом никеле по ГОСТ — 0,7 %, а в маложелезистом ферроникеле — до 3 %).
С 2015 г. двумя уральскими предприятиями Уфалейникель и Режский завод управляет ООО «Русникель». Серовский рудник является структурным подразделением Уфалейникель
Добыча окисленной руды осуществляется на Серовском руднике. В последние годы рудник сталкивается с массой нерешенных проблем, в результате чего на начало 2016 года запасы промышленного склада были полностью выбраны, а запасы руды на «Уфалейникеле» и «Режникеле» составляли от 1 до 3 дн. В январе 2016 г. была разработана комплексная программа выхода из сложившейся ситуации и начата ее реализация. С марта 2016 г. Серовский рудник осуществляет суточную добычу руды сверх плановых показателей, на промышленном складе началось формирование новых объемов руды.
Руда с Серовского рудника поставляется на промышленные предприятия компании — заводы «Уфалейникель» и «Режникель», где путем использования технологии шахтной плавки производится конечный продукт — высококачественный гранулированный никель марок Н-3 и Н-4.
Режский никелевый завод был построен в 1936 году для переработки соседних месторождений окисленных руд, ресурсы которых были полностью исчерпаны к 1994 году.
Основное производство завода в настоящее время — это плавка в трех шахтных печах никелевой руды Серовского рудника с получением никелевого штейна, который отправляется на «Уфалейникель». Мощности Режского никелевого завода позволяют перерабатывать до 700 тыс. т руды в год. За счет ряда технических мероприятий и налаживания снабжения завода рудой выпуск штейна может составлять примерно до 7 тыс . т никеля в штейне в год .
Кроме того, завод располагает электротермическим цехом, в котором перерабатывались отработанные железоникелевые аккумуляторы и другие никельсодержащие ломы и отходы с выпуском гранулированного ферроникеля и других сплавов на железоникелевой основе. В 2005 году электротермический цех освоил выпуск никеля Н-3 из закиси никеля «Уфалейникеля».
Мощности комбината «Уфалейникель» — около 15 тыс. т/г никеля.
Производство никеля основано на шахтной плавке предварительно подсушенной окисленной никелевой руды. В качестве серосодержащего агента используется колчедан.
Полученный отвальный шлак гранулируется и выводится в отвал, газы очищаются от пыли и выбрасываются в атмосферу. Штейн поступает на конвертирование, куда также добавляется в качестве холодных присадок -металлоотходы, штейн Режского завода, в качестве флюса — кварц. Полученные газы от конвертеров очищаются от пыли в электрофильтре.
Файнштейн (78 % никеля) разливается в песчаные изложницы. Затем файн-штейн дробится, мелется и поступает вместе с оборотной пылью в печь кипящего слоя (КС) для выжигания серы. Огарок далее подвергается хлорированию сильвинитом (смесь натриевой и калиевой солей), хлорированный огарок выщелачивается на перколяторе для максимального перевода меди и кобальта в раствор с получением мало-медистого твердого остатка (не более 0,05 % кислотнорастворимой меди). Фильтрат направляется на гидрометаллургическое извлечение никеля, кобальта и меди.
Твердый остаток далее подвергается второму обжигу в трубчатых печах до полного удаления серы. Полученная закись никеля (76 % никеля) является товарной продукцией или идет на электроплавку (на Режском заводе) с получением гранулированного никеля. При электроплавке в качестве восстановителя используется нефтекоксик.
Товарной продукцией является никель марки Н-3 (Ni+Co — не менее 98,6 %) и закись никеля (Ni+Co — не менее 76 %).
Перечень основного технологического оборудования приведен в таблице 2.26, выбросы вредных веществ в атмосферу — в таблице 2.27.
Таблица 2.26 — Основное оборудование
Наименование оборудования |
Назначение оборудования |
Технологические характеристики |
Сушильный ба рабан |
Сушка руды |
Прямоточный, топливо — газ или мазут, регулируемая скорость вращения |
Шахтная печь |
Плавка на штейн |
Площадь сечения в области фурм — 20 м2, число фурм — 28, диаметр фурм — 273 мм, производительность — 25-35 т/м^сут, топливо — кокс металлургический, воздушное дутье — 55000-75000 нм3/ч, число газоотводящих труб — 4, диаметр газоотводящих труб — 1812 мм |
Наименование оборудования |
Назначение оборудования |
Технологические характеристики |
Горизонтальный конвертор |
Конвертирование штейна |
Вместимость по файнштейну — 3,6 м3 (30 т), количество фурм — 16-18 шт., диаметр фурм — 50 мм, площадь сечения фурм — 294,37 см2, расход воздуха — 120 м3/мин, давление дутья — 0,7-0,9 атм, расход электроэнергии — 50 кВт на 1 т файнштейна |
Печь кипящего слоя |
Окислительный обжиг файнштейна |
Тип печи — цилиндрическая с раструбом вверху, высота печи — 9900 мм, расход воздуха — 3500-5000 м3/ч, удельная производительность — 5-7,3 т/м2^ сутки, давление воздуха под слоем — 0,25-0,4 атм, производительность — 65 т/сутки |
Трубчатый реактор |
Сульфатохлорирующий обжиг файн-штейна |
Тип — вращающийся, трубчатый, длина — 12500-14000 мм, диаметр — 2000-2200 мм, длина реакционной зоны — 10,5 м |
Нутч-фильтры |
Обезмеживание — сернокислотное выщелачивание хлорированного огарка |
Тип — механический, вакуумный, опрокидывающийся, номинальная вместимость — 19502600 кг, фильтрующая поверхность — 4 м2, разрежение — до 80 Па, объем заливаемого раствора — 1,5-2,0 м3 |
Трубчатая печь |
2 -я стадия обжига (обжиг твердого остатка и оборотных материалов) |
Тип — трубчатая, вращающаяся, частота вращения — 1,2-1,5 об./мин, топка — откатная, трубчатого типа, топливо — газ, расход природного газа — 250-350 м3, расход воздуха — 1600-1950 м3/ч, электродвигатель АО 2-52-6, 7,5 кВт, 1000 об./мин |
Наименование оборудования |
Назначение оборудования |
Технологические характеристики |
Электропечь |
Электроплавка за киси никеля |
Мощность трансформаторов — 3000 кВА, номинальный линейный ток с высокой стороны — 288 А, номинальное линейное напряжение с низкой стороны — 135 В, номинальный линейный ток с низкой стороны — 12773 А, футеровка хромомагнезитовая или периклазовая |
Таблица 2.27 — Выбросы загрязняющих веществ в атмосферу
Источники выбросов |
Метод очистки, повторного использования |
Наименование |
Масса выбросов загрязняющих веществ после очистки, г/т Ni |
Шахтная плавка |
Скруббер, бат. циклон |
Диоксид азота |
5660 |
Оксид азота |
919,7 | ||
Кобальт |
193,0 | ||
Никель |
4825,1 | ||
Медь |
97,1 | ||
Мышьяк |
40,3 | ||
Неорганическая пыль |
664200 | ||
Диоксид серы |
4633000 | ||
Конвертирование штейна |
Электрофильтр |
Диоксид азота |
49,9 |
Оксид азота |
8,1 | ||
Кобальт |
28,2 | ||
Никель |
457,4 | ||
Медь |
14,1 | ||
Мышьяк |
8,1 | ||
Неорганическая пыль |
6100 | ||
Диоксид серы |
594900 | ||
Окислительный и сульфат- |
Электрофильтр |
Диоксид азота |
119,1 |
Оксид азота |
19,4 |
Источники выбросов |
Метод очистки, повторного использования |
Наименование |
Масса выбросов загрязняющих веществ после очистки, г/т Ni |
хлорирующий обжиг |
Кобальт |
6,4 | |
Никель |
564,3 | ||
Медь |
60,8 | ||
Мышьяк |
30,9 | ||
Неорганическая пыль |
3500 * | ||
Диоксид серы |
400000 * | ||
Обжиг в трубчатой вращающейся печи |
ЦБУ-6Т-2 |
Кобальт |
0,5 |
Никель |
21,1 | ||
Медь |
130,7 | ||
Мышьяк |
0,1 | ||
Пыль неорганическая |
3500 * | ||
Диоксид серы |
400000 * | ||
Электроплавка |
Циклоны |
Кобальт |
11,8 |
Никель |
1942,8 | ||
Медь |
23,5 | ||
Неорганическая пыль |
1300 | ||
Диоксид серы |
2000 | ||
* Общий выброс для печей КС и ТВП. |
В Советском Союзе существовал единственный кобальтовый комбинат — « Тува -кобальт», перерабатывавший гидрометаллургическим способом до богатого концентрата местные бедные кобальтовые мышьяковистые рудные концентраты. В настоящее время он закрыт. На остальных отечественных предприятиях в ходе комплексной переработки никельсодержащих руд, в которых кобальт присутствует в подчиненном количестве, производился огневой кобальт, либо оксид кобальта. Технология производства огневого кобальта устарела и не имела действующих мировых аналогов. С закрытием Никелевого завода ЗФ ПАО « ГМК « Норильский никель» производство огневого кобальта в России прекращено.
При производстве никеля из кобальтсодержащих никелевых руд сырье для производства кобальта выделяется в качестве полупродукта на рафинировочных операциях. В частности, при традиционном рафинировании черновых никелевых анодов кобальт выделяется в гидратный осадок в ходе очистки никелевого анолита. В настоящее время в России только на Кольской ГМК действует технология производ -ства металлического кобальта. Сырьем для этого производства является пульпа первичного кобальтового кека гидролитической очистки никелевых растворов. Технология предусматривает производство катодного кобальта электроэкстракцией из хлоридных растворов и находится на стадии промышленного освоения. Качество электролитного кобальта регламентируется документом Кольской ГМК — ТУ 1731-231-48200234—2014. Организационно кобальтовое производство является отделением цеха электролиза никеля.
Готовой продукцией кобальтового производства является электролитный (катодный) кобальт, который должен соответствовать ТУ 1731-231-48200234—2014 «Кобальт электролитный. Опытные партии».
Предусматривается выпуск трех сортов кобальта, различающихся по внешнему виду и химическому составу, согласно таблице 2.28.
Таблица 2.28 — Химический состав электролитного кобальта согласно ТУ 1731-231-48200234—2014 «Кобальт электролитный. Опытные партии»
Компонент |
Массовая доля, %* | ||
I сорт |
II сорт |
III сорт | |
Co, не менее |
99,8 |
99,8 |
99,25 |
Примеси, не более | |||
Ni |
0,02 |
0,05 |
0,3 |
Fe |
0,003 |
0,05 |
0,4 |
Cu |
0,003 |
0,02 |
0,03 |
Mn |
0,0005 |
- |
- |
Si |
0,001 |
- |
- |
Al |
0,001 |
- |
- |
As |
0,0005 |
0,001 |
0,002 |
Bi |
0,0003 |
0,0004 |
- |
Компонент |
Массовая доля, %* | ||
I сорт |
II сорт |
III сорт | |
Sb |
0,0003 |
0,0006 |
- |
Sn |
0,0003 |
0,0004 |
- |
Pb |
0,0003 |
0,0005 |
- |
Zn |
0,0003 |
0,002 |
- |
Cd |
0,0001 |
0,001 |
- |
P |
0,0003 |
0,003 |
- |
Mg |
0,0005 |
- |
- |
S |
0,001 |
0,004 |
0,004 |
C |
0,005 |
0,02 |
0,03 |
Кобальт выпускают в виде пластин или полос произвольного размера, нарезанных из катодных листов толщиной от 1,5 до 10,0 мм. Размеры пластин и полос приведены в таблице 2.29. Основную массу готовой продукции (сорт I) составляет кобальт в виде пластин размером 100 х 100 мм.
Таблица 2.29 — Размеры пластин и полос товарного кобальта согласно ТУ 1731-231-48200234—2014 «Кобальт электролитный. Опытные партии»
Сорт |
Форма изготовителя |
Размер, мм |
I, II, III |
Пластины |
25±10 х 25±10 50±10 х 50±10 100±10 х 100±10 550±10 х 550±10 |
I, II, III |
Полосы произвольного размера |
Длина — не более 200, ширина — не менее 20 |
Пульпа первичного кобальтового кека после водной отмывки репульпацией растворяется в солянокислом хлоридном никельсодержащем растворе в присутствии восстановителя, в качестве которого используются находящиеся в растворе в низшей форме окисленности поливалентые ионы железа и меди. Для растворения используется привозная соляная кислота. Последующая регенерация окислителя осуществляется за счет восстановления ионов железа и меди на сопряженной с операцией растворения кобальта операции растворения ПНТП. Одновременно за счет цементационного осаждения на ПНТП обеспечивается грубая очистка растворов от меди. Далее экстракцией обеспечивается глубокая очистка полученного фильтрата от меди и цинка. Примеси из полученного экстракта выделяются при их реэкстракции реэкстрактом примесей из цикла экстракции кобальта.
Никель-кобальтовый рафинат смешивается с рафинатом экстракции кобальта и упаривается. Из упаренного раствора осуществляется основная, грубая экстракция кобальта, и большая часть рафината возвращается на упаривание, а меньшая часть подвергается глубокой экстракции кобальта и далее передается на гидролитическую очистку от железа и малых примесей. Полученный при глубокой экстракции кобальта экстракт смешивается с оборотным экстрагентом и подается на основную экстракцию кобальта. Из экстракта основной кобальтовой экстракции после промывки кобальтовым раствором от электроэкстракции (католитом) реэкстрагируют кобальт с получением богатого кобальтового реэкстракта. Основное количество экстрагента после этого возвращается в цикл экстракции, а из меньшей части, после дополнительной отмывки от кобальта, реэкстракцией водой выделяют примеси меди, железа и цинка. Полученный реэкстракт примесей далее используется для реэкстракции меди.
На всех экстракционных операциях используется экстрагент на основе третичных алкиламинов фракции С7-С9 в разбавителе из технической смеси ароматических и насыщенных алифатических углеводородов с модификатором из алифатических спиртов фракции С8-С10.
В результате растворения ПНТП и очисток от примесей образуется ряд направляемых на переработку в гидрометаллургическое отделение производства рафинированного никеля кеков и растворов. В частности, из передаваемого в никелевое производство никелевого рафината предварительно окислением хлором или гипохлоритом натрия в присутствии основного карбоната никеля осаждают железо, свинец и марганец. Никелевый раствор передается на хлорное выщелачивание ПНТП, а кек очистки направляется на гидратный передел никелевого производства. Таким образом, обеспечивается канал вывода из сопряженного никелевого производства в отвальный железистый кек проблемных микропримесей свинца и марганца.
Богатый кобальтовый реэкстракт после контрольной гидролитической очистки от железа и микропримесей, где в качестве нейтрализатора используется основной карбонат кобальта собственного производства, смешивается с частью отходящего из ванн электроэкстракции кобальтового анолита и в качестве католита поступает в ванны электроэкстракции.
Электроэкстракция кобальта осуществляется в аналогичных никелевому производству полимербетонных электролизных ваннах с разделением катодного и анодного пространств проточной тканевой диафрагмой. При этом используется хлоридный электролит. Нерастворимые титановые аноды с активным покрытием типа ОРТА помещены в оборудованные колпаками и работающие под разряжением диафрагменные ячейки, а катоды находятся в общем катодном пространстве ванны . За счет прохождения по -стоянного тока на анодах выделяется хлор. На катодах в эквивалентном пропущенному току количестве с учетом пониженного выхода по току кобальта осаждается чистый катодный кобальт. Осаждение товарного кобальта осуществляется на кобальтовые основы, которые наращиваются отдельно на титановых матрицах. Католит непрерывно подается в общее катодное пространство ванны. Из каждой анодной ячейки анолит совместно с анодным хлором эвакуируется за счет разряжения в бортовой коллектор. Католит просачивается через поры диафрагмы в анодные ячейки, препятствуя попаданию в катодное пространство хлора. Анодный хлор-газ отделяется от анолита вне ванны, в коллекторе и сепараторах, и направляется в никелевое производство, на очистку от кобальта никелевого анолита. Анолит частично направляется на выпарку и растворение исходного сырья, а частично — на реэкстракцию хлорида кобальта.
По завершении катодной компании товарные катоды выгружаются, промываются и передаются в дальнейшую обработку , включающую взвешивание , пробоотбор , резку , сортировку (разбраковку), фасовку (упаковку) товарного кобальта для отправки партиями на склад готовой продукции.
Основное оборудование производства катодного кобальта включает в себя реакционное, фильтровальное, экстракционное оборудование, электролизные ванны.
Основное реакционное оборудование: аппараты с пневматическим перемешиванием (пачуки) емкостью 170 м3, аппараты с механическим перемешиванием и плоским или коническим днищем различного объема (до 20 м3), аппараты с псевдоожижением (цементаторы) емкостью 11 м3. Основное емкостное оборудование — баки (аппараты) емкостью от 0,23 до 200 м3.
Фильтровальное оборудование: фильтры патронные ПКФ-40, дисковые вакуум-фильтры ДТ68-2,5 и ДТ34-2,5, фильтр-прессы рамные ФРП-50-2П.
Экстракционное оборудование: экстракторы ящичные типа смеситель-отстойник с площадью камер отстаивания 2,6 м 3 и аналогичные экстракторы с выносной камерой смешения и площадью камер отстаивания 17,5 м3.
Выпарная станция вакуумная, двухкорпусная с выносными теплообменниками F = 37,6 и 48,5 м2, кожухотрубным поверхностным конденсатором F = 37,9 м2 и предварительным пластинчатым нагревателем-теплообменником F = 10 м2.
Транспортирующее оборудование. Центробежные насосы (станции) типа АХН Q/H.21, ХМ-8/40.
Система компримирования хлора и хлорной безопасности компании EGR (Англия) на базе водокольцевого компрессора хлора Q = 180 нм3/ч, Ризб = 0,15 МПа, N = 22 кВт .
Блоки сдвоенные ванн электролизных полимербетонных на 61 титановый анод с покрытием типа ОРТА в диафрагменных ячейках с колпаками и 60 катод, рабочей поверхностью 935 х 1340 мм. Вдоль борта ванны проходит коллектор для совместной эвакуации анолита и хлора. По току ванны последовательно включены в серию с максимальной токовой нагрузкой до 35 кА.
Подьемно-транспортное оборудование включает мостовой кран (Q = 10 т, Н = 13 м , L = 21 м) и спецкран (Q = 3,2/30 т, L = 10,5 м) для обслуживания ванн. Обработка готовой продукции осуществляется на участке, выделенном в составе отделения готовой продукции никелевого производства с использованием его оборудования.
Для снижения выбросов загрязняющих веществ в атмосферный воздух предусмотрено:
-
- установка герметичного, оснащенного аспирационными отсосами оборудования;
-
- общеобменная приточно-вытяжная вентиляция помещений в требуемых объемах;
-
- оборудование аспирационных систем газоочистными установками, позволяющими сократить выбросы на 98,0 % — 99,97 %;
-
- аварийная вентиляция насосных помещений склада соляной кислоты с автоматическим включением в работу при превышении концентраций хлористого водорода;
-
- аварийная вентиляция части производственных помещений электролизного участка с автоматическим включением в работу при превышении концентрации хлора с очисткой хлорсодержащих газов.
Для очистки аспирационных отсосов от емкостного оборудования (с хлоридными растворами металлов; с растворами соляной кислоты) устанавливается пенный газоочиститель, орошаемый содовым раствором (степень очистки — 98,5 %). Прошедшие очистку газы сбрасываются в атмосферу через вентсистему. Аспирационные газы от оборудования, в котором возможно выделение хлора, направляются на очистку для исключения возможных проскоков хлора в существующие пенные газоочистители (степень очистки — 98 %), где происходит их нейтрализация содовым раствором. Прошедшие очистку газы сбрасываются в атмосферу через существующую свечу.
Для аспирации экстракторов, насадочных колонн, емкостей с органической фазой предусмотрены системы с естественной тягой с выбросом на новые свечи. Ввиду отсутствия экономичных и эффективных систем улавливания паров предельных углеводородов (компонентов экстрагента) для снижения выбросов в атмосферу и потерь дорогостоящих реагентов предусмотрено водяное охлаждение секций аспирационных газоходов.
Технологической схемой электролизного участка предусмотрена установка двух скрубберов для очистки (нейтрализации) хлорсодержащих газов: аспирационного и аварийного, орошаемых щелочным раствором (15-20%-ным раствором NaOH). Скрубберы включены в комплектную поставку системы хлороудаления, дехлорирования анолита, очистки хлорсодержащих газов. Расчетная степень очистки газов на скрубберах (99,97 %) определена исходя из немецких нормативов по содержанию хлора в очищенных сбросных газах — не более 3 мг/м3. На постоянно работающий аспирационный скруббер поступают аспирационные отсосы от укрытий электролизных ванн, ванн регенерации, емкостного и фильтровального оборудования электролизного участка, продувочные газы, а также «бедные» хлорсодержащие газы аварийной вентиляции из помещений.
Абгазы емкостей соляной кислоты направляются в аппарат-газоочиститель для нейтрализации содовым раствором. Очищенные газы сбрасываются в атмосферу через свечу.
Самостоятельные стоки кобальтового производства не образуются, поскольку все полупродукты перерабатываются в ГМО никелевого производства (ЦЭН).
Производственные (солевые) стоки ЦЭН отводятся на очистные сооружения общего стока комбината, где подвергаются известковой очистке и сбрасываются в озеро Нюд.
Ввод в работу кобальтового производства уменьшает сброс в озеро Нюд суль-фат-иона на 6807 т/год и увеличивает сброс хлорид-иона на 1004 т/год.
Раздел 3. Определение наилучших доступных технологийТермин «наилучшие доступные технологии» определен в Федеральном законе «Об охране окружающей среды» № 7-ФЗ ([36]).
Под технологией понимается как используемая технология, так и способ, с помощью которого объект спроектирован, построен, эксплуатируется и выводится из эксплуатации; это не только и не столько технология производства, но и различные технические и нетехнические методы (экологический менеджмент, управленческие решения) повышения экологической результативности.
Под доступной понимается экономически целесообразная и неуникальная технология, которая достигла уровня, позволяющего обеспечить ее внедрение в никелькобальтовой промышленности с учётом экономической и технической обоснованности, принимая во внимание затраты и преимущества; при этом технология должна быть реализована хотя бы на двух предприятиях отрасли.
Под «наилучшей» понимается технология, в максимальной мере обеспечивающая охрану окружающей среды и сбережение ресурсов (сырья, воды, энергии).
Порядок определения технологии в качестве наилучшей доступной технологии определён постановлением Правительства Российской Федерации от 23 декабря 2014 г. № 1458 «О порядке определения технологии в качестве наилучшей доступной технологии, а также разработки, актуализации и опубликования информационнотехнических справочников по наилучшим доступным технологиям», на основании которого Министерство промышленности и торговли Российской Федерации разработало Методические рекомендации по определению технологии в качестве наилучшей доступной технологии.
Согласно этим документам, при отнесении технологических процессов, оборудования, технических способов и методов к НДТ необходимо учитывать следующие критерии:
а) наименьший уровень негативного воздействия на окружающую среду в расчете на единицу времени или объем производимой продукции (товара), выполняемой работы, оказываемой услуги либо соответствие другим показателям воздействия на окружающую среду, предусмотренным международными договорами Российской Федерации; приоритетным, оказывающим наименьшее отрицательное воздействие на окружающую среду, рекомендовано считать воздействие от отходов, затем выбросы в воду и загрязнение почвы; воздействие от выбросов в воздух рекомендовано рассматривать как фактор, имеющий наибольший отрицательный эффект;
б) экономическая эффективность внедрения и эксплуатации; анализ экономической эффективности заключается в оценке затрат на внедрение и эксплуатацию технологии и выгоды от ее внедрения путем применения метода анализа затрат и выгод; в процессе оценки рекомендуется разделять объекты (предприятия) на новые и действующие;
в) применение ресурсо- и энергосберегающих методов;
г) период внедрения;
д) промышленное внедрение технологических процессов, оборудования, технических способов, методов на двух и более объектах в Российской Федерации, оказывающих негативное воздействие на окружающую среду.
В качестве источников информации о применяемых на практике технологиях, относящихся к НДТ, были использованы окончательный проект второй редакции справочника ЕС по НДТ для предприятий цветной металлургии (октябрь-2014), сведения, полученные в результате анкетирования предприятий отрасли, результаты научноисследовательских работ, публикаций, а также информация, полученная в ходе консультаций с профильными экспертами.
Наилучшие доступные технологии и методы, а также, в необходимых случаях, соответствующие им технологические показатели (значения концентрации эмиссий) определялись технической рабочей группой применительно к вспомогательным и основным процессам производства никеля и кобальта, приведенным ниже.
Процессы подготовки сырья:
а) сушка, окускование (брикетирование);
б) гидрометаллургическое обогащение никель-пирротинового концентрата.
Процессы плавки первичного сырья и конвертирования с использованием следующих агрегатов:
а) Руднотермическая печь
б) Печь взвешенной плавки
в) Электропечь обеднения
г) Шахтная печь
д) Конвертер Пирса — Смита
Процессы получения товарных форм никеля и кобальта:
а) флотационное разделение файнштейна;
б) окислительный обжиг никелевого концентрата флотации файнштейна;
в) получение порошка никелевого трубчатых печей (ПНТП);
г) рафинирование ПНТП в хлоридных средах до катодного никеля;
д) получение электролитного кобальта.
Раздел 4. Наилучшие доступные технологииНастоящий раздел содержит перечень кратких описаний НДТ, применяемых при производстве никеля и кобальта на различных этапах технологического процесса.
НДТ в рамках раздела сгруппированы в подразделы в соответствии с целями их применения, например НДТ для повышения эффективности использования энергии, НДТ для управления отходами, промежуточными и побочными продуктами и др.
При выборе НДТ необходимо обращать внимание на указание в описании НДТ на конкретное производство (передел/установку), для которого должна применяться соответствующая технология. Также для каждой НДТ, где необходимо, указаны ограничения применимости включённых в описание НДТ методов.
4.1 Системы экологического менеджмента (СЭМ)
НДТ 1. Повышение общей результативности природоохранной деятельности. Внедрение и поддержание системы экологического менеджмента (СЭМ), соответствующей требованиям ГОСТ Р ИСО 140011) или ISO 140011).
-
4.2 Энергоменеджмент и энергия
НДТ 2. Повышение эффективности использования энергии: использование комбинации двух или более методов, приведенных в таблице 4.1.
Таблица 4.1.
Метод/оборудование |
Применимость | |
а) |
Система управления энергоэффективностью (например, в соответствии с требованиями ГОСТ Р ИСО 50001 1 или ISO 50001 1) |
Общеприменим |
б) |
Оптимальное размещение взаимосвязанных производств, переделов и отдельного оборудования, обеспечивающее минимизацию материальных потоков |
Общеприменимо при новом строительстве, изменении конфигурации существующих производств или реконструкции |
1 Соответствие систем менеджмента указанным стандартам не означает ее обязательную сертификацию
Метод/оборудование |
Применимость | |
в) |
Использование избыточного тепла (например, пара, горячей воды или горячего воздуха), образующегося при реализации основных процессов |
Применим для пирометаллургических процессов |
г) |
Регенеративные дожигающие устройства |
Применим, когда требуется очистка выбросов от горючих загрязняющих веществ |
д) |
Подача на горелки воздуха, обогащенного кислородом, или чистого кислорода для уменьшения потребления энергии |
Применим для пирометаллургических процессов |
е) |
Низкотемпературная сушка концентратов и влажного сырья перед плавкой |
Общеприменим |
ж) |
Теплоизоляция объектов, функционирующих при высоких температурах, например трубопроводов пара и горячей воды |
Общеприменим |
з) |
Использование высокоэффективных электродвигателей, оборудованных частотными преобразователями, для таких устройств как, например, вентиляторы |
Общеприменим |
и) |
Использование горячих технологических газов от процессов плавления для нагревания подаваемых компонентов |
Применим для пирометаллургических процессов |
к) |
Применение автогенных процессов плавки сырья |
Применим для пирометаллургических процессов |
л) |
Использование тепла химических реакций для поддержания теплового баланса гидрометаллургических процессов |
Применим при реализации окислительных процессов, сопровождающихся выделением тепла |
1) Соответствие систем менеджмента указанным стандартам не означает ее обязательную сертификацию. |
-
4.3 Контроль технологических процессов и мониторинг эмиссий
НДТ 3. Обеспечение стабильности производственного процесса. Внедрение системы автоматизированного контроля и использование комбинации двух или более методов, приведенных в таблице 4.2.
Таблица 4.2.
Метод/оборудование |
Применимость | |
а) |
Проверка и сортировка исходных материалов в соответствии с требованиями, определяемыми используемым технологическим оборудованием и применяемыми методами сокращения загрязнения |
Общеприменим |
Метод/оборудование |
Применимость | |
б) |
Тщательное перемешивание различных материалов, входящих в состав шихты, для достижения оптимальной эффективности переработки и сокращения выбросов и отходов | |
в) |
Системы взвешивания и дозирования шихты | |
г) |
Использование микропроцессорных устройств для контроля скорости подачи материала, ключевых технологических параметров, включая сигнализацию, условий сжигания и подачи дополнительного газа | |
д) |
Непрерывный инструментальный контроль температуры, давления, расхода реагентов | |
е) |
Контроль критических параметров процессов, реализуемых на установках очистки воздуха, таких как температура газа, количество подаваемых реагентов, падение давления, ток и напряжение на электрофильтре, объем подачи и pH жидкости в мокром скруббере | |
ж) |
Контроль содержания пыли в отходящих газах перед их подачей на сернокислотную установку |
Применим для заводов по производству цветных металлов, включающих производство серной кислоты или жидкого SO2 |
з) |
Непрерывный инструментальный контроль силы тока, напряжения, скорости циркуляции, состава растворов и качества электрических контактов и др. |
Применим для процессов электролиза |
и) |
Непрерывный инструментальный контроль содержания вредных веществ в воздухе рабочей зоны с системами оповещения и аварийной остановки (при наличии технической возможности) работы основного оборудования в случае превышения их пороговых значений |
Общеприменим |
к) |
Контроль и регулирование температуры для предотвращения образования выбросов металлов и оксидов металлов из-за перегрева |
Применим для спекающих и плавильных печей |
л) |
Использование локальных и глобальных систем контроля и управления работой оборудования, включая непрерывный инструментальный контроль основных параметров: температуры, мутности, ОВП, pH, электропроводности, давления, уровня, потоков, состава и др. |
Общеприменим для гидрометаллургических процессов |
-
4.4 Сокращение расхода реагентов и материалов
НТД 4 Сокращение расхода реагентов за счет внедрения новых процессов, (таблица 4.3).
Таблица 4.3
Метод/оборудование |
Применимость | |
а) |
Использование сульфата натрия или сульфата кальция в качестве флюсующих добавок для улучшения физикохимических свойств шлаков и снижения потерь цветных металлов |
Применим для пирометаллургических процессов |
б) |
Замена гидролитического способа выделения кобальта из никелевого раствора безреагентным экстракционным |
Применимо для хлоридных сред рафинирования ПНТП или иных полупродуктов, после разработки не гидролитического способа очистки от свинца и марганца |
в) |
Утилизация солевого стока дробной выпаркой с выделением товарного сульфата натрия и оборотного хлорида натрия и производства хлора электролизом последнего взамен использования привозного хлора |
Применим для установок очистки сточных вод от хлоридного рафинирования ПНТП или иных полупродуктов |
г) |
Использование известково-серного отвара в качестве осадителя тяжелых цветных металлов |
Применим в гидрометаллургических производствах, сопровождающихся образованием и выделением элементарной серы |
д) |
Применение фильтрации расплавленной элементарной серы взамен автоклавной выплавки |
Применим для гидрометаллургических процессов, сопровождающихся образованием элементарной серы при необходимости ее выделения |
-
4.5 Неорганизованные эмиссии
НДТ 5. Предотвращение или уменьшение неорганизованных выбросов пыли: разработка и реализация в качестве составной части СЭМ (см. НДТ 1) плана мероприятий по неорганизованным выбросам, предусматривающего, в том числе, использование методов, приведенных в таблице 4.4.
Таблица 4.4.
Метод/оборудование | |
а) |
Инвентаризация наиболее характерных источников неорганизованных выбросов |
б) |
Определение и реализацию соответствующих мероприятий и методов по предотвращению и сокращению неорганизованных выбросов в течение определенного периода времени. |
НДТ 6. Предотвращение или уменьшение неорганизованных эмиссий в воздух и водные объекты: организация местных систем аспирации, замена реагентов и материалов менее летучими и токсичными, ликвидация складов хранения токсичных реагентов и материалов или сокращение объема их хранения и потребления за счет улучшения логистики производства или изменения технологии производства.
НДТ 7. Уменьшение неорганизованных выбросов, образующихся при хранении сырья (таблица 4.5).
Таблица 4.5.
Метод/оборудование |
Применимость | |
а) |
Регулярная уборка и, при необходимости, увлажнение площадки хранения и обращения сыпучими материалами |
Общеприменим |
б) |
Применение защитных посадок, ограждений для защиты от ветра или обвалований с наветренной стороны для снижения скорости ветра |
Применяется при складировании на открытом воздухе |
в) |
Хранение материалов там, где это возможно, в одной куче вместо нескольких |
Общеприменим |
г) |
Герметичная упаковка |
Применяется для хранения и транспортировки пылящих материалов, а также сырья, содержащего растворимые в воде органические соединения |
д) |
Разбрызгивание воды с применением или без применения таких добавок как латекс |
Не применяется для процессов, в которых используются сухие материалы или ру-ды/концентраты, содержащие достаточное количество естественной влаги, чтобы предотвратить пылеобразо-вание. Применение также ограничено в регионах с нехваткой воды или с очень низкими зимними температурами |
е) |
Размещение устройств для улавливания пыли в точках загрузки и перегрузки |
Применяется в местах складирования пылящих материалов |
НДТ 8. Уменьшение неорганизованных эмиссий, образующихся при обработке и транспортировке сырья (таблица 4.6).
Таблица 4.6.
Метод/оборудование |
Применимость | |
а) |
Использование закрытых конвейеров или пневматических транспортных систем |
Общеприменим |
б) |
Сооружение конвейеров для непылящих твердых материалов под навесами | |
в) |
Организация систем аспирации при транспортировке и перегрузке пылящих |
Общеприменим |
Метод/оборудование |
Применимость | |
материалов в сочетании с системой пылеулавливания и очистки отходящих газов | ||
г) |
Установка устройств для сбора пыли в пунктах доставки, вентиляционных отверстиях, пневматических транспортных системах и точках перегрузки на конвейерах передачи, и их подключение к системе фильтрации |
Применяется при использовании пылящих материалов |
д) |
Использование для обращения с измельченными или водорастворимыми материалами закрытых мешков или бочек |
Общеприменим |
е) |
Использование специальных контейнеров для обработки уложенных на поддонах материалов |
Общеприменим |
ж) |
Обработка пылящих материалов, например их смешивание, в закрытом помещении |
Общеприменим. Для существующих заводов применение может быть затруднено в связи с необходимостью больших пространств |
з) |
Разбрызгивание воды для увлажнения материалов в местах их обработки |
Не применяется для процессов, требующих сухих материалов |
и) |
Использование максимально коротких маршрутов транспортировки |
Общеприменим |
к) |
Регулировка скорости открытых ленточных конвейеров (< 3,5 м/с) |
Применяется при использовании открытых ленточных конвейеров |
л) |
Размещение передающих конвейеров и трубопроводов на безопасных открытых площадках выше уровня земной поверхности с целью оперативного обнаружения утечек и предупреждения повреждений транспортными средствами и другим оборудованием. Если для перемещения неопасных материалов используются подземные трубопроводы, местоположение их трасс должно быть документально зафиксировано и отмечено на местности соответствующими предупреждающими знаками; должны применяться системы безопасного ведения земляных работ. |
Общеприменим |
м) |
Мойка колес и шасси транспортных средств, используемых для доставки или обработки пылящих материалов |
Не применяется в условиях, которые могут привести к обледенению |
н) |
Проведение плановых кампаний по уборке дорог |
Общеприменим |
о) |
Использование систем пылеподавления, таких как водометы или дождевальные установки |
Применяется при перемешивании материалов вне помещений. Не применяется для процессов, требующих сухих материалов. Применение также ограничено в регионах с нехваткой воды или с очень низкими зимними температурами |
Метод/оборудование |
Применимость | |
п) |
Использование закрытого оборудования, оснащенного системой улавливания отходящих газов, связанной с системой газоочистки |
Применяется при подаче смесей, полученных с помощью бункеров-дозаторов или системы потери веса, при сушке, смешивании, помоле, разделении и гранулировании |
НДТ 9. Предупреждение или уменьшение неорганизованных выбросов: оптимизация параметров эффективности улавливания и очистки отходящих газов (таблица 4.7).
Таблица 4.7.
Метод/оборудование |
Применимость | |
а) |
Использование закрытых печей, оснащенных системами пылеулавливания, или оснащение печей и другого технологического оборудования вытяжными системами |
Применение может быть ограничено соображениями безопасности (например, типом/конструкцией печи, наличием угрозы взрыва) |
б) |
Оснащение печей вторичными системами отведения газов в точках загрузки и выгрузки |
Общеприменим |
в) |
Оптимизация конструкции и технологии эксплуатации вытяжных устройств и газоходов с целью улавливания газов, возникающих при загрузке шихты и отходящих от разогретого металла; выдача и перемещение расплавов сульфидов или шлаков по закрытым желобам |
Для существующих заводов применение может быть ограничено имеющимся пространством и сложившейся планировкой размещения объектов в цехах |
г) |
Сооружение укрытий печей/реакторов, для улавливания выбросов при загрузочных операциях и выдаче расплавов |
Применение может быть ограничено соображениями безопасности (например, типом/конструкцией печи, наличием угрозы взрыва) |
д) |
Использование систем, позволяющих подавать сырье небольшими порциями |
Общеприменим |
е) |
Использование непрерывных процессов и агрегатов, например замена периодического процесса конвертирования в горизонтальных конвертерах Пирса-Смита на двухзонную печь Ванюкова для конвертирования медно-никелевых штейнов, процесс Ausmelt, ACP-процесс |
Применим при новом строительстве или реконструкции |
ж) |
Оптимизация потока отходящих из печи газов на основе компьютеризированных исследований и индикаторов гидродинамики |
Общеприменим |
з) |
Окускование сырья (брикетирование, окатывание) |
Применим только для процессов и печей, предназначенных для использования окускованного сырья |
и) |
Эксплуатация печи и газоотводящих каналов при разрежении и скорости газоотведения, достаточной для предотвращения повышения давления |
Общеприменим |
к) |
Размещение печи в вытяжном укрытии |
Применим при малых размерах печи |
л) |
Поддержание температуры в печи на самом низком допустимом уровне |
Общеприменим |
м) |
Закрытые помещения в сочетании с другими методами улавливания неорганизованных выбросов |
Применение может быть ограничено соображениями безопасности (например, типом/конструкцией печи, наличием угрозы взрыва) |
н) |
Система вторичных вытяжных зонтов, дополняющих основной при загрузке печи и выпуске из нее металла |
Для существующих заводов применение может быть ограничено имеющимся пространством и сложившейся планировкой размещения объектов в цехах |
НДТ 10. Уменьшение неорганизованных выбросов при реализации гидрометаллургических процессов (таблица 4.8)
Таблица 4.8
Метод/оборудование |
Применимость | |
а) |
Организация укрытия зеркала флотомашин |
Для существующих заводов применение может быть ограничено имеющимся пространством и сложившейся планировкой размещения объектов в цехах |
б) |
Использование закрытого реакторного и бакового оборудования, трубопроводов вместо желобов для транспортировки растворов и пульп |
Общеприменим при осутствии необходимости визуального контроля за процессом |
в) |
Добавление поверхностно-активных веществ при электролизе |
Применим, если не нарушает ведение основных процессов |
г) |
Использование общеобменной вентиляции и локальной аспирации из области зеркала ванн с последующей очисткой абгазов |
Общеприменим |
д) |
Использование укрытия электролизных ванн и отведение абгазов в систему газоочистки |
Применим для электролизных ванн за исключением случаев, когда они должны оставаться не укрытыми |
е) |
Улавливание аэрзолей от скрапомывочных машин |
Применимо для рафинирования черновых анодов |
-
4.6 Организованные эмиссии
НДТ 11. Сокращение выбросов пыли и металлов. Поддержание в качестве составляющей СЭМ (см. НДТ 1) подсистемы, обеспечивающей эффективность эксплуатации систем пылеподавления и пылеулавливания.
НДТ 12. Сокращение выбросов пыли (взвешенных веществ) и металлов от пирометаллургических процессов производства никеля и кобальта. Использование газоочистного оборудование, в т.ч. «сухих» и «мокрых» электрофильтров (таблица 4.9).
Таблица 4.9 - Технологический показатель: выбросы пыли и металлов
Параметр |
Единица измерений |
Средний уровень выбросов для НДТ1) | |
Для действующих предприятий |
Для вновь вводимых предприятий/ при реконструкции действующих предприятий | ||
Взвешенные вещества |
мг/нм3 |
< 500 |
< 70 |
Никель, оксид никеля (в пересчете на никель) |
мг/нм3 |
< 180,0 |
< 25,0 |
Свинец и его соединения, кроме тетраэтилсвинца, в пересчете на свинец |
мг/нм3 |
< 7,0 |
< 2,0 |
Мышьяк и его соеди-нения2), кроме водорода мышьяковистого |
мг/нм3 |
< 2,5 |
< 1,1 |
|
НДТ 13. Снижение выбросов SO2 за счет направления отходящих газов (с предварительной очисткой от пыли) на установки по производству серной кислоты, жидкого диоксида серы, элементарной серы, бисульфита натрия или других аналогичных продуктов, а также нейтрализация пульпой известняка (таблица 4.10).
Таблица 4.10 - Технологический показатель: степень утилизации диоксида серы
Параметр |
Единица измерений |
Эффективность утилизации |
Степень утилизации диоксида серы |
% |
90 - 95 |
Применимость: Только для новых/реконструируемых предприятий в зависимости от содержания диоксида серы в газах, от наличия рынка производимого продукта или условий для долговременного хранения.
НДТ 14. Снижение выброса в воздух кислых газов от гидрометаллургических операций (таблица 4.11).
Таблица 4.11.
Метод/оборудование |
Применимость | |
а) |
Локальные системы аспирации основного оборудования с последующей переработкой абгазов в системах каплеотбойников и мокрых скрубберов |
Общеприменимо |
б) |
Мокрый скруббер |
Для существующих заводов применение может быть ограничено имеющимся пространством и сложившейся планировкой размещения объектов в цехах |
в) |
Каплеотбойник |
НДТ 15. Снижение выброса в воздух NOx от пирометаллургических процессов:
использование одного из методов, приведенных в таблице 4.12.
Таблица 4.12.
Метод/оборудование |
Применимость | |
а) |
Г орелки с автоматическим поддержанием необходимого сочетания топлива и окислителя |
Общеприменим |
б) |
Кислородно-топливные горелки |
Общеприменим |
Таблица 4.12 - Технологический показатель: выбросы оксидов азота
Параметр |
Единица измерений |
Средний уровень выбросов для НДТ1) |
Азота оксид и азота диоксид (суммарно) |
мг/нм3 |
< 250 |
-
4.7 Охрана почвы и подземных вод
НДТ 16. Уменьшение неорганизованных сбросов в водные объекты (таблица 4.13). Таблица 4.13
Метод/оборудование |
Применимость | |
а) |
Применение современных коррозионностойких конструкционных и футеровочных материалов для изготовления бакового и реакторного оборудования, трубопроводов |
Применим при новом строительстве и реконструкции |
б) |
Хранение кислот и других агрессивных реагентов и рабочих растворов в емкостях с двойными стенками или в емкостях, размещенных внутри устойчивого к воздействию агрессивных сред обвалования избыточной |
Применим при небольших объемах емкостей |
вместимости | ||
в) |
Проектирование площадок для хранения таким образом, чтобы любые утечки из емкостей и систем доставки удерживались внутри обвалования, способного вместить объем жидкости, равный, по крайней мере, объему наибольшей емкости, размещенной внутри обвалования. Площадка для хранения должна быть обвалована и иметь покрытие, не подверженное воздействию хранящегося агрессивного материала |
Применим при новом строительстве или реконструкции |
г) |
Использование нефтеловушек и песколову-шек в дренаже площадок хранения и обращения с сыпучими материалами. |
Общеприменим |
д) |
Использование для хранения материалов, которые могут содержать нефтепродукты (например, замасленной стружки), бетонированных площадок с бортами или иными удерживающими устройствами |
Общеприменим |
е) |
Применение надежных систем обнаружения утечек и индикации уровня заполнения емкостей с подачей сигналов для предотвращения их переполнения |
Общеприменим |
НДТ 17. Предотвращение загрязнения почвы и подземных вод при эксплуатации хвостохранилищ (таблица 4.14).
Таблица 4.14
Метод/оборудование |
Применимость | |
а) |
Комплекс противодренажных мероприятия |
Общеприменим |
б) |
Организация гидроизоляции |
При строительстве новых хво-стохранилищ |
НДТ 18. Предотвращение загрязнения почвы и подземных вод электролитом при производстве никеля и кобальта: использование комбинации двух или более методов, приведенных в таблице 4.15.
Таблица 4.15.
Метод/оборудование | ||
а) |
Использование оборотной дренажной системы |
Общеприменим |
б) |
Использование влагонепроницаемых подвалов с зумпфом и кислотостойких полов |
Применим при новом строительстве и реконструкции |
в) |
Использование ёмкостей с двойными стенками или размещение их внутри прочного обвалования с непроницаемыми полами |
НДТ 19. Предотвращение образования сточных вод: использование одного из или комбинации методов, приведенных в таблице 4.16.
Таблица 4.16.
Метод/оборудование |
Применимость | |
а) |
Повторное использование слабых кислот из стоков, образующихся в мокрых электростатических фильтрах и мокрых скрубберах |
Применяется в зависимости от содержания в сточных водах металлов и твердых веществ |
б) |
Использование поверхностных стоков |
Общеприменим |
в) |
Использования систем полного или частичного оборотного водоснабжения |
Общеприменим |
г) |
Утилизация солевых стоков рафинирования никеля выпаркой и дробной кристаллизацией товарных или оборотных сульфата и хлорида натрия и возвратом конденсата выпарки в основное производство |
Применим для процессов рафинирования черновых анодов, ПНТП или иных полупродуктов |
НДТ 20. Очистка сточных вод, образующихся при производстве никеля и кобальта, с целью удаления металлов и сульфатов на основе применения методов, приведенных в таблице 4.17.
Таблица 4.17.
Метод/оборудование |
Применимость | |
а) |
Химическое осаждение |
Общеприменим |
б) |
Седиментация |
Общеприменим |
в) |
Фильтрация |
Общеприменим |
г) |
Флотация |
Общеприменим |
д) |
Обратный осмос |
Общеприменим |
е) |
Выпарка и кристаллизация солей |
Общеприменим |
Таблица 4.18 - Технологические показатели: средний уровень концентраций загрязняющих веществ в прямых сбросах, образующихся при производстве никеля и кобальта, в принимающие водные объекты
Параметр |
Единица измерений |
Концентрация загрязняющего вещества1) |
As |
мг/л |
< 0,2 |
Pb |
мг/л |
< 1,0 |
Zn |
мг/л |
< 1,0 |
Ni |
мг/л |
< 2,5 |
Co |
мг/л |
< 0,5 |
взвешенные вещества |
мг/л |
< 50 |
pH |
ед. |
6 - 10 |
1) Среднесуточное значение |
НДТ 21. Уменьшение количества отходов, направляемых на утилизацию при производстве никеля и кобальта: организация обращения с отходами, промежуточными и побочными продуктами, способствующая их повторному использованию, а в случае невозможности — вторичной их переработке (таблица 4.19).
Таблица 4.19.
Метод/оборудование |
Применимость | |
а) |
Извлечение металлов из пыли поступающих из системы пылеулавливания |
Общеприменим |
б) |
Регенерация или переработка отработанных катализаторов |
Общеприменим |
в) |
Извлечение металла из осадка, образующегося при очистке сточных вод |
Применим в зависимости от содержания металлов и от наличия рынка/процесса |
г) |
Использование отвальных шлаков в качестве абразивных или строительных (для отсыпки дорог) материалов |
Применим в зависимости от содержания металлов и от наличия рынка |
д) |
Использование футеровки печей для извлечения металлов или повторное её использование в качестве огнеупорных материалов |
Общеприменим |
е) |
Использование гипса с установок по очистке сточных вод в пирометаллургических процессах или в качестве закладочного материала для отработанных горных выработок |
Применим в зависимости от качества получаемого гипса и особенностей технологического процесса |
Ресурсы, которые предприятия отрасли могут направить на модернизацию производств и реализацию природоохранных мероприятий, напрямую зависят от конъюнктуры рынка никеля — основного металла, определяющего доходность никелевых предприятий. На таком рынке компании — производители никеля не имеют возможности по отдельности воздействовать на цену конечной продукции, что позволило бы в той или иной степени переложить понесенные в связи с реализацией природоохранных мероприятий и внедрением экологически эффективных технологий затраты на потребителя.
Это означает, что возможности по компенсации любых существенных затрат, понесенных в связи с реализацией природоохранных мероприятий компаниями — производителями никеля, ограничены и преимущественно могут быть реализованы за счет внедрения новых способов производства и расширения прежде всего номенклатуры 158
выпускаемой продукциис высокой добавленной стоимостью. Оба варианта связаны с технологическими и экономическими рисками и требуют значительных капитальных затрат, срок окупаемости которых весьма высок.
Усовершенствования «на конце трубы» в большинстве случаев приводят к увеличению эксплуатационных расходов и не дают такого повышения эффективности производственного процесса, которое может быть получено в результате внедрения мер, интегрированных в технологический процесс производства продукции. Это также свидетельствует в пользу выбора проектов коренной модернизации производственного процесса при определении мер, направленных на сокращение эмиссий загрязняющих веществ в окружающую среду. Причем при ранжировании мотиваций последние находятся в подчиненном положении. Вместе с тем такой подход связан со значительными капитальными вложениями и иными потерями ввиду необходимости временной остановки производства и перестройки производственного процесса в целом, что обусловливает снижение привлекательности полномасштабной модернизации производства при неблагоприятной рыночной конъюнктуре.
Собственный экономический потенциал природоохранных мероприятий, таких как, например, внедрение малоотходных технологий, производство побочной продукции и (или) полезное использование образующихся в основном производственном процессе отходов, в российских условиях следует признать скорее незначительным. С одной стороны , природоохранные технологии во многих случаях характеризуются высокой энергоемкостью, а поддержание оборудования в функциональном состоянии требует регулярных затрат на расходные материалы и комплектующие и иных эксплуатационных затрат; в некоторых случаях при производстве побочной продукции, такой, например, как серная кислота, значительные издержки могут возникать и в связи с необходимостью хранения и транспортировки агрессивного вещества. С другой стороны, низкая емкость российских рынков и территориальная удаленность от них никелевых предприятий не обеспечивают вывод «побочных» производств на экономически эффективный уровень и не смогут гарантировать устойчивое потребление продукции вновь вводимых производственных мощностей, а потенциал выхода на внешние рынки ограничен и малоперспективен с экономической точки зрения.
Таким образом, наибольшим потенциалом с точки зрения возмещения затрат, понесенных в связи с внедрением на предприятии новых природоохранных методов и технологий, обладают комплексные меры, увязывающие экологическую модернизацию производства с перенастройкой производственного процесса в целом, оптимизацией отдельных его звеньев и расширением номенклатуры выпускаемой продукции, в том числе с высокой добавленной стоимостью.
Раздел 6. Перспективные технологии при производстве никеля и кобальта 6.1 Технология двухзонной печи Ванюкова«Процесс плавки в жидкой ванне» (переименованный после смерти его создателя, профессора Андрея Владимировича Ванюкова, в «Процесс Ванюкова») является конкурентноспособной разновидностью существующих в мире автогенных процессов плавки сульфидного сырья, таких как взвешенная плавка Outokumpu, процессы Ausmelt и Isasmelt, кислородно -взвешенная плавка Inco, Mitsubishi, Noranda, Teniente и др .
Схематическое изображение однозонной печи Ванюкова представлено на рисунке 6.1.
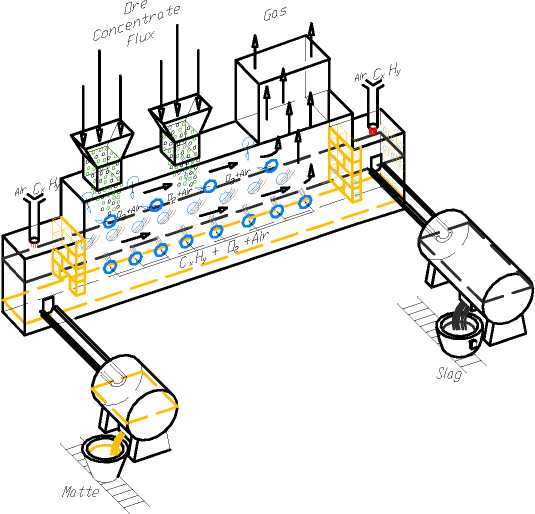
Рисунок 6.1 — Схематическое изображение однозонной печи Ванюкова
Однозонная печь состоит из плавильной камеры, аптейка, штейнового и шлакового сифонов. В плавильную камеру через отверстия в своде печи подается шихта, состоящая из концентрата (руды) и флюса. При необходимости в шихту может добавляться уголь с целью улучшения теплового баланса печи и восстановления магнетита. Через фурмы нижнего ряда, находящиеся в шлаковом слое печи, подается кислород-но-воздушная смесь. При необходимости, для поддержания теплового баланса печи, через фурмы нижнего ряда может дополнительно подаваться углеводородное топливо. В настоящее время в действующих печах Ванюкова в качестве такого топлива используется природный газ. В процессе взаимодействия шихты и дутья в надфурменной зоне образуется шлако-штейновая эмульсия. Она разделяется в подфурменной зоне на шлак и штейн, которые движутся в печи в противоположных направлениях. Из сифонов шлак и штейн поступают в миксеры, откуда они сливаются в ковши по мере требований дальнейшего производства. Отходящие концентрированные по SO2 газы дожигаются в плавильной камере с помощью воздушно-кислородной смеси, подаваемой через верхний ряд фурм, расположенных над расплавом шлака.
Дожигание газов производят в случае необходимости. Цель дожигания — не допустить попадания в газоходную систему газов с высокой концентрацией S2. Сифоны служат для отстаивания расплавов, после чего шлак и штейн по желобам перетекают в миксеры. Для поддержания температуры продуктов плавки в сифонах и миксерах используют горелки, работающие на газообразном или жидком углеводородном топливе (природный газ, пропан-бутан, мазут и пр.). В конструкции миксеров печей Ванюкова Балхашского горно-металлургического комбината вместо горелок используется электроподогрев с помощью графитированных электродов (площадь пода одного миксера — 50,5 м2, мощность трансформатора — 9 МВт).
Технология плавки сульфидных концентратов в печах Ванюкова имеет следующие достоинства:
- высокая удельная производительность печи ;
- возможность использования дутья с высокой концентрацией кислорода (до 95 %);
- достижение состояния, близкого к равновесию между шлаком и штейном, что обеспечивает высокое извлечение ценных компонентов;
- непрерывность процесса и поддержание постоянного уровня в печи шлака и штейна за счет использования сифонов.
Печь Ванюкова может быть размещена в действующих производственных помещениях, так как занимает небольшую площадь и не требует значительной высоты здания.
Процесс Ванюкова постоянно улучшается, как в направлении повышения технико-экономических показателей, так и в плане совершенствования конструкции металлургических агрегатов. Наиболее важным шагом в совершенствовании плавки Ванюкова в последние годы является разработка двухзонных печей Ванюкова, конструктивные разновидности которой разработаны в институтах МИСиС ([37], [38]) и «Гипроникель» ([39])- ([41]).
В 2004-2008 гг на комбинате «Южуралникель» ОАО «Стальная группа Мечел» была опробована промышленная двухзонная печь Ванюкова (площадь пода 26 м2) для плавки окисленных никелевых руд с получением штейна ([37], [38]). Положительный итог освоения новой технологии, проводившегося под научным руководством профессора МИСиС В. П. Быстрова, был окончательно подтвержден тестовыми испытаниями в 2008 году ([38]), показавшими преимущества данной технологии по сравнению с существующей на комбинате шахтной плавкой. Важным положительным моментом этих испытаний является также то, что в промышленном масштабе была показана возможность успешного использования печи Ванюкова для плавки окисленного сырья, что открывает перед этим процессом новые перспективы.
На комбинате «Североникель» ОАО «ГМК «Норильский Никель» в 2005 году была построена и в течение 2005-2006 гг эксплуатировалась опытно-промышленная двухзонная печь Ванюкова площадью пода 11,4 м2 и производительностью до 15 т/час по перерабатываемому сырью. Проект выполнен ООО «Институт Гипроникель». В процессе испытаний были успешно отработаны следующие технологии:
-
- переработка богатой сульфидной медной руды рудника «Октябрьский» Норильского комбината ОАО «ГМК «Норильский никель» (% масс.: Cu — 17,1; Ni — 3,1; Co — 0,079; Fe — 34,0; S — 26,5; SiO2-8,5) с получением богатых штейнов и отвальных шлаков ([39]);
-
- переработка никелевого сульфидного рудного концентрата ОАО «Кольская ГМК» (% масс.: Ni — 8,3; Cu — 4,6; Co — 0,25; Fe — 30,3; S — 20,5; SiO2-15,4; CaO — 1,6; Al2O3-1,3; MgO — 10,0) с получением богатых штейнов и отвальных шлаков ([41]);
-
- переработка медного никельсодержащего концентрата от разделения файн-штейна комбината «Североникель» ОАО «Кольская ГМК» (% масс.: Cu — 67,5; Ni — 3,8; Co — 0,24; Fe — 4,5; S — 21,2) с получением черновой меди и жидкотекучих никелевых шлаков ([40]).
На основании выполненных опытно-промышленных испытаний для промышленной реализации процесса переработки сульфидных концентратов с получением богатых штейнов и отвальных шлаков предложена двухзонная печь, схематически изображенная на рисунок 6.2.
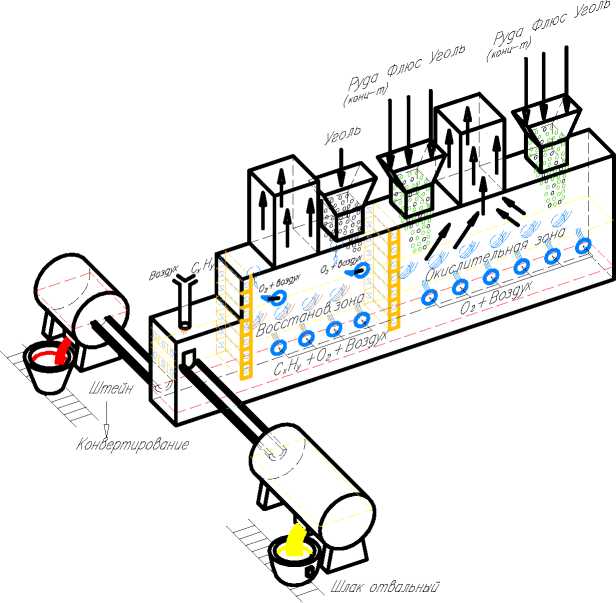
Рисунок 6.2 — Схематическое изображение двухзонной промышленной печи Ванюкова
Конструктивно двухзонная печь для плавки медных и медно-никелевых руд и концентратов состоит из окислительной зоны, восстановительной зоны и совмещенного сифона, предназначенного для выпуска как штейна, так и отвального шлака. Рабочие пространства зон печи разделены водоохлаждаемыми перегородками; системы га-зоудаления — раздельные. Концентрированные по SO2 газы окислительной зоны могут быть использованы для производства серной кислоты, элементной серы или жидкого диоксида серы. Газы восстановительной зоны, содержащие CO и Н2, дожигаются кислородно-воздушной смесью через специально установленные в верхнем ряду кессонов фурмы, очищаются от пыли и выбрасываются в атмосферу. Сифон печи оригинальной конструкции предусматривает возможность непрерывного выпуска шлака и штейна.
Процесс переработки сульфидного сырья в двухзонной печи Ванюкова может быть представлен следующим образом. В окислительную зону печи подаются совместно сульфидное сырье, флюс и уголь. Через фурмы подается кислородновоздушная смесь и газообразное (природный газ, пропан-бутан, генераторный газ) или жидкое (мазут, солярка) топливо. Использование газообразного (жидкого) топлива и/или угля необходимо в случае дефицита тепла, образующегося в результате окисления сульфидов. Шлак окислительной зоны поступает в восстановительную зону печи, где ведется его восстановление газовой смесью, образующейся в результате сжигания газообразного или жидкого топлива в условиях дефицита кислорода, и углем. Образующийся в процессе восстановления металлический сплав смешивается со штейном, полученным в зоне окисления, и выпускается через сифон из печи. Шлак восстановительной зоны также поступает в сифон, откуда происходит его непрерывный слив через порог, расположенный на уровне ~2200 мм от пода печи. С обеих сторон сифона расположены миксеры, где накапливаются конечные продукты плавки: штейн и отвальный шлак.
Основные преимущества двухзонных печей Ванюкова:
- возможность увеличения качества штейна по содержанию цветных металлов без роста их потерь со шлаком (как следствие обеднения последнего во второй зоне);
- перевод большего количества серы в концентрированные по SO2 газы , сниже -ние затрат на ее утилизацию;
- растворение образующейся при обеднении металлической фазы в штейне окислительной зоны, с сохранением сравнительно невысокой температуры плавления последнего. При проведении обеднения в отдельной печи с получением тугоплавкого металлического сплава необходимо либо поддерживать в ней высокую температуру, либо подавать в нее сульфидизатор и в дальнейшем утилизовать бедные по SO2 газы;
- высокая производительность процесса обеднения шлака , что в сочетании с вы -сокой производительностью окислительной плавки сульфидного сырья позволяет размещать два пирометаллургических передела на ограниченной площади.
Перспективность перехода от технологии обеднения шлаков в электропечах переменного тока или электроотстойниках (недостатки такого обеднения хорошо известны) к технологии барботажного обеднения шлаков подтверждается мировыми тенденциями в совершенствовании процесса обеднения шлаковых расплавов. В настоящее время одним из основных направлений в технологии обеднения шлаков является создание процессов, основанных на продувке шлаковых расплавов восстановительными газовыми смесями, образующимися при разложении жидкого или газообразного топлива, или продуктами их сжигания при недостатке кислорода.
В таблице 6.1 представлено сравнение результатов работы опытно -промышленной двухзонной ПВ с технологией плавки обожженных никелевых концентратов с повышенным содержанием MgO в рудно-термических печах.
Таблица 6.1 — Распределение цветных металлов в рудно-термической печи в сравнении с двухзонной печью Ванюкова
Технологический процесс |
Тип печи |
Содержание в штейне/шлаке, % |
Сумма ЦМ в штейне, % | ||
Си |
Ni |
Co |
S(Cu+Ni+Co) | ||
Переработка никелевых концентратов |
Руднотермическая плавка |
10,5/0,10 |
18,9/0,18 |
0,74/0,09 |
30,0 |
ДвухзоннаяПВ |
25,5/0,28 |
42,3/0,20 |
0,87/0,07 |
69,0 |
Видно, что при переработке никелевого сырья качество штейна увеличилось более чем в 2 раза; при этом заметное увеличение концентрации в отвальном шлаке наблюдается только для меди. Для никеля содержание осталось на том же уровне, а для кобальта наблюдается даже снижение потерь.
Таким образом, двузонная печь Ванюкова является не механическим сочетанием двух металлургических агрегатов, а единым технологическим комплексом, имеющим общую штейновую (металлическую ванну). Оригинальная конструкция печи, создающая крайне ограниченное взаимодействие между конечным продуктом плавки и обедненным шлаком, позволяет добиться высокого извлечения цветных и драгоценных металлов.
6.2 Усовершенствование технологии гидрометаллургического обогащения бедного никель-пирротинового концентратаВ мировой практике все медно-никелевые рудные концентраты, содержащие платиновые металлы, за исключением гидрометаллургического производства Надеждинского металлургического завода (ГМП НМЗ) ЗФ ПАО «ГМК «Норильский никель», перерабатываются по классической пирометаллургической технологии. Переработка рудных пентландит-пирротиновых концентратов в Норильске по автоклавной технологии связана с выделением на стадии обогащения относительно бедного продукта, переработка которого по пирометаллургической технологии не оправдана.
Используемая в настоящее время в ГМП НМЗ технология гидрометаллургического обогащения имеет потенциал для развития.
Применяемые для окисления пульпы пирротинового концентрата условия, с одной стороны, обеспечивают решение поставленной задачи — получение пригодного для пирометаллургической переработки сульфидного медно-никелевого концентрата, с другой — не позволяют снизить высокие потери с отвальными хвостами цветных и в особенности драгоценных металлов, что негативно сказывается на ее рентабельности. Этот факт, а также отсутствие в мире других подобных производств связаны с тем, что до настоящего момента не было готовых к промышленной реализации гидрометаллургических технологий, обеспечивающих низкие потери платиновых металлов, соизмеримые с достигаемыми на действующих пирометаллургических предприятиях.
Высокие потери ценных компонентов в действующей технологии гидрометаллургического обогащения во многом обусловлены свойствами формирующихся при автоклавном выщелачивании гидратных форм железа, обладающих развитой поверхностью и, соответственно, высокой сорбционной способностью по отношению к драгоценным металлам. Кроме того, оксиды железа формируют пленки на поверхности недоразложенных на АОВ сульфидов, что препятствует полноте их извлечения на стадии серо-сульфидной флотации. Еще одной причиной потерь ценных компонентов является использование в действующей технологии ПАВ — ЛСТ, что неизбежно при ведении процесса в режиме ВТВ. Отказ от использования ПАВ при АОВ возможен только в случае перехода на режим окисления при температурах ниже точки плавления серы (НТВ), но при этом необходимо изменить и другие параметры таким образом, чтобы не происходило снижение производительности оборудования.
С учетом всех этих обстоятельств в ООО «Институт Гипроникель» разрабатываются технологические приемы, позволяющие многократно снизить потери ценных компонентов, в том числе и платиновых металлов, при гидрометаллургической переработке никель-пирротинового сырья. В основе предложенных решений лежит создание условий, обеспечивающих формирование на стадии автоклавного окислительного выщелачивания крупнокристаллических частиц окисленных железистых фаз с пониженной по отношению к цветным и драгоценным металлам сорбционной способностью, например натроярозита (пат. RU № 2573306).
Результаты проведенных экспериментов, обзор научно-технической литературы и анализ действующей технологии гидрометаллургического обогащения показал , что разработанные ООО «Институт Гипроникель» технические решения весьма конкурентоспособны по сравнению как с действующим производством, так и с ближайшим аналогом — Activox-процессом (таблица 6.2). Более того, они показали свою эффективность для переработки концентратов широкого диапазона составов — от бедных по цветным и благородным металлам до весьма богатых (таблица 6.3).
Таблица 6.2 — Сравнение показателей действующей технологической схемы, Activox-процесса и перспективной технологии
Технология |
Извлечение в концентрат флотации, % | ||
Ni |
Cu |
SМПГ | |
Действующая |
94 |
91 |
52 |
Activox |
94 |
87 |
72 |
Перспективная |
98 |
93 |
93 |
Таблица 6.3 — Показатели извлечения цветных и драгоценных металлов по перспективной технологии
Состав сырья |
Извлечение в концентрат флотации,% | ||||||
Ni, % |
Cu, % |
SМПГ, г/т |
Pt+Pd+Rh, г/т |
Ni |
Cu |
SМПГ |
Pt+Pd+Rh |
0,7 |
0,05 |
2,1 |
1,8 |
98,2 |
68,3 |
82,3 |
86,3 |
1,1 |
0,20 |
4,0 |
3,8 |
98,2 |
94,2 |
88,5 |
92,5 |
1,3 |
0,20 |
4,3 |
4,1 |
98,2 |
93,2 |
93,2 |
95,7 |
8,7 |
0,40 |
26,5 |
26,2 |
99,2 |
93,0 |
94,2 |
94,5 |
3,4 |
7,40 |
33,7 |
33,3 |
97,7 |
98,8 |
95,3 |
96,1 |
3,9 |
2,80 |
38,2 |
37,8 |
94,9 |
96,9 |
96,9 |
97,2 |
При этом в зависимости от состава поступающего в переработку сырья возможна различная организация схемы переработки растворов автоклавного выщелачивания (рисунок 6.3). В обоих случаях обеспечиваются высокие показатели извлечения всех ценных компонентов.
богатые рудн ыо концентраты
рсагснть:
кислород или КВС
концентрат ЦМ
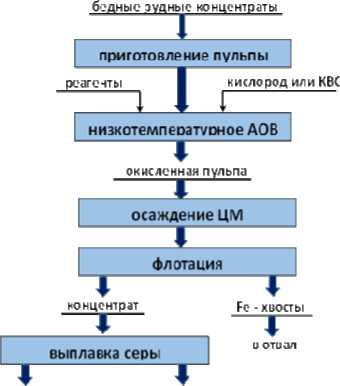

концентрат МПГ
сера товарная
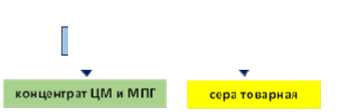
Рисунок 6.3 — Варианты организации технологических схем
для богатого (а) и бедного (б) сырья
Проведение промышленных испытаний новой технологии планируется на 2017 год.
6.3 Производство никеля электроэкстракцией и рафинированием ПНТПНа сегодняшний день в мировой практике получения товарного катодного никеля повсеместно используется процесс электроэкстракции из сульфатных или хлоридных растворов.
По сравнению с электрорафинированием черновых металлических или сульфидных анодов процесс получения никеля методом электроэкстракции имеет следующие преимущества:
- ликвидация затрат на производство промежуточных продуктов , а именно чер -новых анодов;
- ликвидация определяющихся наличием анодного скрапа оборотов;
- существенное упрощение обслуживания электролизных ванн (обработка ано -дов и скрапа, чистка ванн с выделением и переработкой шлама);
- возможности более полной механизации и внедрения дополнительных , более совершенных систем контроля процессов рафинирования;
- возможности использования более современного основного оборудования ;
- существенное сокращение незавершенного производства (срок растворения черновых анодов составляет приблизительно 30 суток, кроме того оно увеличивается за счет наличия оборотного скрапа).
В отечественной практике получения катодного никеля по состоянию на сего -дняшний день электроэкстракция имеет ограниченное применение, а хлорное растворение выступает как вспомогательный процесс для восполнения дефицита никеля и переработки оборотных полупродуктов. Однако в ближайшее время планируется полный перевод схемы производства катодного никеля на электроэкстракцию.
Перспективная технологическая схема включает в себя:
- последовательный окислительный и восстановительный обжиг никелевого концентрата флотации файнштейна с получением порошка никелевого трубчатых печей (ПНТП);
- хлорное выщелачивание ПНТП ;
- грубую медеочистку раствора ;
- экстракционную цинкоочистку ;
- гидролитическую железоочистку ;
- тонкую медеочистку ;
- двухстадиальную гидролитическую кобальтоочистку .
Очищенный богатый никелевый раствор разбавляется оборотным дехлорированным анолитом ванн электроэкстракции, объединяется с переливом католита из ванн электроэкстракции и в качестве католита питания направляется в напорные баки электролизного отделения для дальнейшей подачи в ванны электроэкстракции.
Первичные железистый и кобальтовый кеки подвергаются дальнейшей переработке с получением отвального железистого кека и катодного кобальта соответственно. Остаток хлорного растворения направляется на извлечение драгоценных металлов.
Принятая для развития рафинировочных мощностей ПАО «ГМК Норильский никель» концепция постепенного перехода от способа рафинирования черновых анодов к способу рафинирования ПНТП с использованием хлоридных сред решение обеспечивает постепенных переход к новой технологии с минимальными капитальными затратами и без остановки основного производства. Это объясняется близостью существующих и требуемых операций очистки никелевых растворов и возможностью использования действующего оборудования, включая основное оборудование очистных отделений и существующих электролизных ванн.
Дополнительный бонус может быть получен при организации обособленной переработки хлорным выщелачиванием магнитной фракции от разделения файнштейна.
Тогда эта коллектирующая в себя основную массу драгоценных металлов фракция перерабатывается хлорным выщелачиванием, минуя операции окислительного и восстановительного обжига. Кроме того, богатый драгоценными металлами остаток ее выщелачивания может быть переработан до концентратов драгоценных металлов по короткой цепочке. Тем самым сокращаются передельные затраты и общие потери драгоценных металлов.
Дополнительное использование экзотермических реакций хлорирования исходного сырья для подупарки растворов непосредственно на операции хлорирования открывает принципиальную возможность безреагентной экстракционной очистки от кобальта, которая становится целесообразной после разработки эффективного не гидролитического способа очистки никелевого раствора от свинца и марганца. Внедрение экстракционной очистки от кобальта позволит существенно сократить расход основного реагента — соды, одновременно значительно упростить новое кобальтовое производство, ликвидируя в нем основные головные переделы, и пропорционально сокращению расхода соды сократить количество направляемых на утилизацию солевых стоков.
Перечисленные мероприятия и потенциальные пути дальнейшего усовершенствования технологии иллюстрируют преимущества предлагаемого способа рафинирования никеля.
6.4 Производство никеля электроэкстракцией растворов выщелачивания никелевого концентрата от разделения файнштейнаДальнейшим развитием технологии производства никеля электроэкстракцией из растворов от выщелачивания промпродуктов переработки медно-никелевого файн-штейна российских предприятий является переход от рафинирования ПНТП (см. 6.3) к рафинированию никелевого концентрата флотации файнштейна. В этом случае дополнительно ликвидируются связанные с потерями затратные и экологически не совершенные переделы окислительного и восстановительного обжига. Присутствующая в никелевом концентрате сера не отгоняется в газовую фазу, а практически полностью сохраняется в остатке выщелачивания, переходя в элементарную.
Упрощенно процесс переработки никелевого концентрата методом хлорного выщелачивания можно представить состоящим из трех блоков: блока выщелачивания и медеочистки, блока получения продукционного никелевого раствора и блока электроэкстракции.
В свою очередь, блок выщелачивания и медеочистки состоит из трех стадий . На первой стадии проводят хлорное выщелачивание НК и оборотного медного кека, на второй стадии — очистку никелевого раствора от меди никелевым концентратом с получением оборотного медного кека, на третьей стадии — выведение меди в виде сульфидного медного продукта из технологической схемы для сохранения баланса по меди.
В результате процесса хлорного выщелачивания цветные металлы и железо пе -реходят в раствор, а в твердой фазе, содержащей до 85 % — 90 % элементной серы, концентрируются платиновые металлы. Пульпу после хлорного выщелачивания фильтруют, никелевый раствор направляют на выделение медного продукта из технологической схемы и на стадию медеочистки. Влажный кек после отмывки от хлор-иона направляют на получение концентрата платиновых металлов.
На стадии медеочистки раствора происходит гидротермальное осаждение меди никелевыми сульфидами и присутствующим в никелевом концентрате металлическим никелем.
Пульпу медеочистки фильтруют, никелевый раствор подают на контрольную фильтрацию, после чего его направляют на железоочистку. Влажный кек — на стадию приготовления пульпы ХВ.
Выделение меди из технологической схемы может быть организовано различными способами с получением металлизированного либо сульфидного медистого полупродукта.
Очистка никелевого раствора от примесей может быть также организована различно. Кроме очистки от меди, она включает в себя стадии гидролитической железо-очистки, экстракционную либо гидролитическую кобальтоочистку. В варианте сохранения гидролитической кобальтоочистки очистка от свинца и марганца сохраняется в кобальтовом производстве. Условия безреагентной экстракционной кобальтоочистки и ее преимущества описаны в 6.2.
Очищенный раствор поступает в электролизеры в качестве католита для производства товарного никеля.
По сравнению с процессом рафинирования ПНТП переработка никелевого концентрата флотации файнштейна сопряжена с рядом трудностей, главными из которых являются организация рациональной многостадийной очистки и необходимость переработки остатка хлорного выщелачивания на основе элементарной серы с получением концентрата драгметаллов.
Организация производства, аналогичного получению серы при переработке ни-кель-пирротинового концентрата, в данном случае представляется не самым лучшим решением ввиду громоздкости, создающей предпосылки к повышенным потерям платиновых металлов. В то время как фильтрация расплавленной серы представляется весьма перспективной и интересной. В настоящее время проводятся исследования по выбору наиболее эффективного варианта удаления серы из остатков хлорного выщелачивания сульфидных полупродуктов.
В варианте рафинирования никелевого концентрата , также как в варианте рафи -нирования ПНТП, сохраняется актуальность обособленной переработки металлизированной фракции файнштейна. В этом случае дополнительный экономический эффект возникает за счет сокращения количества операций и потерь в ходе переработки остатка выщелачивания металлизированной фракции до концентрата драгоценных металлов. Кроме того, в этом варианте остаток выщелачивания бедного драгоценными металлами никелевого концентрата может быть переработан в медном производстве.
6.5 Технология производства карбонильного никеля с использованием синтеза среднего давленияЗа рубежом синтез ТКН реализуют при атмосферном и среднем давлении. В отечественной металлургии карбонилирование осуществляют в колоннах высокого давления, карбонильное производство России не превышает 5600 т/год.
В таблице 6.4 проведено сравнение эффективности работы промышленных ре -акторов синтеза. На мировом рынке карбонильного никеля доминирующее положение занимает компания VALE, выпускающая до 104 000 т/год продукции, из них 54 400 т/год — по технологии синтеза среднего давления (Коппер-Клифф, Канада). Синтез ТКН осуществляется на трех горизонтально-вращающихся реакторах. Реакторы рассчитаны на рабочее давление 70,2 ати и температуру 175 °С. Диаметр реактора — 3,65 м, длина — 20,4 м. Реакторы работают в периодическом режиме: 28 ч синтез, 14 ч перезагрузка. Общее время одной операции — 42 ч. Выбранный режим обеспечивает равномерное потребление оксида углерода, так как в работе постоянно находятся два реактора, а третий перезагружается. Реакторы изготовлены из углеродистой стали, толщина стенки — 127 мм. Внутренний объем реакторов разделен на две камеры. В первой камере длиной 13,4 м происходит непосредственно карбонилирование сырья. Камера охлаждается водой. Вторая камера длиной 7 м, по-видимому, является пылеулавливающим устройством с установленными фильтрами.
Исходным сырьем для карбонилирования является материал, в основе которого находится магнитная фракция файнштейна, шихтуемая шламами электролиза и платиносодержащей вторичкой. Материал подвергается плавке в вертикальных конверторах с последующей грануляцией расплава. Гранулированный материал имеет состав %, мас.: Ni — 72,0; Cu — 18,0; Fe — 3,0; Co — 1,0; S — 5,0; С — <0,1; остальное примеси. Насыпная плотность исходного сырья — 4,0 т/м3. На одну операцию в каждый из реакторов загружается примерно 136 т сырья. Общий вес реактора с загрузкой — 500 т.
Твердые остатки синтеза обезвреживаются смесью азота и кислорода. Содержание кислорода в газовой смеси составляет 8-10 %, об. Химический состав остатков синтеза %, мас.: Ni — 7,0; Cu — 59,0; Fe — 8,0; Co — 4,0; S — 17,0. Извлечение никеля составляет не менее 95 %, железа — не более 30 %, Со — не свыше 1 %. Остатки синтеза поступают на дальнейшую переработку.
Таблица 6.4 — Сравнение эффективности работы промышленных реакторов синтеза в мировом производстве карбонила никеля и железа
174
Страна |
Производительность синтеза (т/год) |
Параметры синтеза |
Состав исходного сырья, % мас. |
Скорость циркуляции CO, нм3/т час |
Извлечение,% |
Продолжительность синтеза (час) |
Количество и тип реакторов | |||||||
Давление (ати) |
Температура (0С) |
Ni |
Fe |
Co |
Cu |
S |
Ni |
Fe |
Co | |||||
Синтез ТКН атмосферного давления | ||||||||||||||
Англия |
50 000 |
1 |
50 |
95 |
0,6 |
1,2 |
3,1 |
0,5 (+2) |
16 |
92 |
- |
- |
96 |
2 шт. горизонтально-вращающихся реакторов |
Китай |
1 500 |
1 |
50 |
93 |
1,2 |
2,0 |
3,5 |
0,2 (+2,5) |
нет данных |
120 |
количество - нет данных горизонталь-но-вращающийся | |||
Синтез ' |
"КН среднего давления | |||||||||||||
Канада |
54 400 |
70 |
180 |
72 |
3 |
1 |
18 |
5 |
77 |
96 |
30 |
1 |
28 |
3 шт. горизонтально-вращающихся реактора |
Синтез ' |
"КН высокого давления | |||||||||||||
Россия |
5 500 |
200 |
200 |
85 |
3,7 |
2,2 |
5,1 |
2,5 |
250 |
96 |
75 |
1 |
72 |
12 шт. стационарных колонн |
Синтез П |
КЖ среднего давления | |||||||||||||
Германия |
25 000 |
75 |
190 |
- |
93 |
нет данных |
58 |
количество - нет данных горизонталь-но-вращающийся | ||||||
Синтез Г |
КЖ высокого давления | |||||||||||||
Россия |
3 000 |
150 |
200 |
- |
95 |
- |
- |
- |
450 |
- |
70 |
- |
96 |
4 шт. стационарные колонны |
ИТС12-2016
Высокая производительность процесса синтеза ТКН достигается при использовании горизонтально-вращающихся реакторов. Причина, обуславливающая резкий рост скорости реакции синтеза во вращающихся реакторах по сравнению с карбонилированием в стационарных колоннах, заключается в организации эффективного отвода тепла реакции из движущегося слоя карбонилируемого сырья.
При этом избыток тепла в горизонтально-вращающихся реакторах утилизируется встроенными холодильниками, что намного эффективнее снятия тепла циркулирующим потоком моноксида углерода, как это осуществляется в колоннах высокого давления. Увеличение скорости циркуляции оксида углерода в синтезе высокого давления до 250 нм3/тч по сравнению со скоростью циркуляции в синтезе среднего давления 77 нм3/т ч не приводит к сокращению времени карбонилирования.
Продолжительность процесса при высоком давлении составляет 72 ч, что в
-
2,5 раза больше, чем при среднем. При этом условия карбонилирования при 250 ати более «жесткие», чем при 70 ати. Таким образом, для организации высокопроизводительного синтеза ТКН необходимо обеспечить интенсивный отвод тепла из зоны реакции. При движении и интенсивном перемешивании загруженного сырья во вращающихся реакторах коэффициент теплопередачи от встроенных холодильников значительно выше теплосъема циркулирующим газом через неподвижный слой материала. Съем тепла обеспечивает выигрыш в скорости синтеза в движущемся слое материала. В неподвижном слое карбонилируемого материала требуемый отвод тепла достигается при значительно более высоких скоростях циркуляции моноксида углерода, с чем связаны дополнительные энергетические затраты и значительные технические трудности в продувке больших газовых потоков.
В существующем в России карбонил-процессе высокого давления наиболее дорогостоящим и энергоемким переделом является синтез карбонила никеля. Анализ результатов промышленной эксплуатации карбонил-процесса показывает, что производство с использованием синтеза высокого давления не эффективно. Основными причинами, ограничивающими производительность синтеза высокого давления, являются:
-
- низкие скорости карбонилирования, обусловленные недостаточным отводом тепла реакции в колоннах синтеза;
-
- несовершенство операции по загрузке и разгрузке реакционных колонн;
-
- высокая стоимость оборудования на давление 150 кгс/см2;
-
- большие энергетические затраты на компримирование реакционного газа;
-
- значительные капиталовложения, в том числе на соблюдение экологической безопасности.
Одним из перспективных направлений увеличения производительности карбо-нил-процесса является переход на синтез карбонила никеля при средних давлениях реакционного газа до 70 кгс/см2 с использованием горизонтально-вращающихся реакторов. Такой переход позволит повысить производительность отделения синтеза на существующих промышленных площадях в результате:
- использования принципиально новой конструкции реактора синтеза , обеспечи -вающего высокую скорость извлечения никеля за счет утилизации тепла реакции, быструю загрузку исходного сырья и выгрузку твердых остатков синтеза;
- увеличения избирательности процесса карбонилирования при снижении давле -ния и сохранения железа в твердых остатках синтеза на 50 % — 70 %, кобальта — 98 % — 99 %.
Заключительные положения и рекомендацииОбзор научно-технической литературы и анализ работы действующих предприятий показал многообразие способов производства товарных никелевых продуктов, в том числе и различных форм рафинированного никеля. Каждый из способов включает в себя множество взаимосвязанных производств, состоящих из отдельных переделов, в свою очередь объединяющих последовательность отдельных операции.
Особенности сырья различных месторождений, экономические и инфраструктурные особенности региона обусловливают применение различных способов для переработки однотипного сырья. Практически не существует полностью совпадающих по способу и аппаратурному его оформлению рафинировочных предприятий.
Следует отметить, что настоящий справочник НДТ включает в себя только типовые многотоннажные способы производства и не упоминает отдельные уникальные или пилотные проекты, которые непрерывно создаются и эксплуатируются, как правило, ограниченное время.
Действующие производства никеля также непрерывно совершенствуются, что объясняется не столько разнообразием вовлекаемых в производство руд и концентратов, но и прежде всего конкуренцией производителей на мировом никелевом рынке.
Совершенствование действующих и создание новых способов производства никеля определяется существующим уровнем техники и требует значительных инвестиций, часто сопряженных с высокими рисками. При прочих равных условиях основные критерии успешной производственной деятельности имеют исключительно экономическую основу. Эти критерии, в свою очередь, являются интегральными характеристиками совокупности различных обычно разнонаправленных технологических факторов, в 176
том числе и факторов ресурсо- и энергоэффективности, а также экологической безопасности производства.
Мировая практика показывает, что любой соответствующий достигнутому уровню науки и техники способ производства никеля может быть доступен, но наилучшие способы производства оказываются совершенно различны и могут быть определены только с помощью учитывающих возможные риски экономических расчетов в привязке к конкретным условиям предполагаемого производства .
Справочник НДТ «Производство никеля и кобальта» подготовлен в соответствии с Поэтапным графиком создания в 2015-2017 гг. справочников наилучших доступных технологий, утвержденным распоряжением Правительства Российской Федерации от 31 октября 2014 г. № 2178-р, и правилами определения технологии в качестве наилучшей доступной технологии, а также разработки, актуализации и опубликования информационно-технических справочников по наилучшим доступным технологиям, утвержденными постановлением Правительства Российской Федерации от 23 декабря 2014 г. № 1458.
При подготовке настоящего справочника НДТ в максимально возможной степени были учтены положения окончательного проекта второй редакции справочника Европейского союза по наилучшим доступным технологиям для предприятий цветной металлургии (Best Available Techniques (BAT) Reference Document for the Non-Ferrous Metals Industries, final draft, October 2014), включая краткие описания (заключения) по НДТ.
Состав ТРГ 12 «Производство никеля и кобальта» утвержден приказом Росстан-
дарта от 4 марта 2016 г. № 240
Баканова Ирина Газимовна Булыгин Анатолий Николаевич
Бутовский Руслан Олегович Велюжинец Галина Анатольевна
Гончар Наталия Валерьевна Гордеев Алексей Иванович
Гришаев Сергей Иванович
Данченко Эдуард Викторович Доброхотова Мария Викторовна Дрижерукова Татьяна Александровна Дубровский Вадим Львович
Ермилов Виктор Ильич
Ерцева Любовь Николаевна
Заварин Александр Станиславович Затицкий Борис Эдуардович Зингалева Надежда Вячеславовна Икрянников Олег Валентинович
Илюхин Игорь Викторович
ЗФ ПАО "ГМК "Норильский никель"
ЗАО «Русская медная компания»
ФГБУ "ВНИИ Экология"
ЗФ ПАО "ГМК "Норильский никель"
ЗАО «Русская медная компания»
ЗАО «Русская медная компания»
Минпромторг России
ЗФ ПАО "ГМК "Норильский никель" ФГУП "ВНИИ СМТ"
АО "НИИ Атмосфера"
АО «Кольская ГМК»
ЗАО «Карабашмедь»
ООО "Институт Гипроникель"
ЗАО "Карабашмедь"
ООО "Институт Гипроникель"
ЗАО «Новгородский металлургический завод» Минпромторг России
ПАО "ГМК "Норильский никель"
Книсс Владимир Альбертович Король Юрий Александрович Котухов Сергей Борисович Крупнов Леонид Владимирович Курошев Илья Сергеевич Макаров Александр Александрович Макаров Юрий Александрович Машкович Константин Игоревич Попов Владимир Анатольевич Салтыков Павел Михайлович Сидоренко Александр Юрьевич Старых Роман Валерьевич Тюкин Александр Павлович Хан Сергей Алексеевич Цапах Сергей Леонидович Цымбулов Леонид Борисович Шабалин Антон Валерьевич Юдин Александр Борисович
ЗАО «Карабашмедь»
ЗАО «Русская медная компания»
ПАО "ГМК "Норильский никель"
ЗФ ПАО "ГМК "Норильский никель"
ФГУП "ВНИИ СМТ"
ЗАО ЭКАТ
ЗАО «Русская медная компания»
ПАО "ГМК "Норильский никель"
ООО "Институт Гипроникель"
ООО "Институт Гипроникель"
ЗАО «Кыштымский медеэлектролитный завод»
ООО "Институт Гипроникель"
АО «Кольская ГМК»
Минпромторг России
ООО "Институт Гипроникель"
ООО "Институт Гипроникель"
ЗАО «Кыштымский медеэлектролитный завод» ЗАО «Новгородский металлургический завод»
Наиболее активное участие в работе над справочником НДТ приняли следующие специалисты:
Бакамова Ирина Газимовна Бикетова Людмила Васильевна Велюжинец Галина Анатольевна Дубровский Вадим Львович Евграфова Александра Константиновна Ершов Сергей Дмитриевич Затицкий Борис Эдуардович Илюхин Игорь Викторович Калашникова Мария Игоревна Котухов Сергей Борисович Крупнов Леонид Владимирович Кузнецов Роман Андреевич Ласточкина Марина Андреевна Лисаков Юрий Николаевич Машкович Константин Игоревич Пак Александр Германович Попов Владимир Анатольевич Румянцев Денис Владимирович Тощев Дмитрий Анатольевич
ЗФ ОАО «ГМК «Норильский Никель» ООО «Институт Гипроникель»
ЗФ ОАО «ГМК «Норильский Никель» АО «Кольская ГМК»
ООО «Институт Гипроникель» ООО «Институт Гипроникель» ООО «Институт Гипроникель» ОАО «ГМК «Норильский никель» ООО «Институт Гипроникель» ОАО «ГМК «Норильский никель» ЗФ ОАО «ГМК «Норильский Никель» ООО «Институт Гипроникель» ООО «Институт Гипроникель» ООО «Институт Гипроникель» ОАО «ГМК «Норильский никель» ОАО «Уфалейникель»
ООО «Институт Гипроникель» ООО «Институт Гипроникель» ФГУП «ВНИИ СМТ», Руководитель секретариата ТРГ 12
В публичном обсуждении проекта настоящего справочника НДТ принимали участие следующие организации:
- ООО « Институт Гипроникель»;
- ЗФ ПАО « ГМК « Норильский Никель»;
- АО « Кольская ГМК»;
- Инновационный фонд Самарской области .
Всего было получено более 90 замечаний и комментариев, которые были рассмотрены ТРГ 12. По каждому из них вынесено решение о принятии или обоснованном отклонении.
Экспертиза проекта справочника НДТ была проведена профильным техническим комитетом по стандартизации ТК 113 «Наилучшие доступные технологии».
При оценке используемых на российских предприятиях по производству никеля и кобальта методов/технологий и соответствующих им технологических показателей необходимо было собрать информацию об используемых методах, а также данные о текущих показателях экологической результативности, ресурсо- и энергоэффективности. Для сбора информации о применяемых на промышленных предприятиях технологических процессах, оборудовании, об источниках загрязнения окружающей среды, технологических, технических и организационных мероприятиях, направленных на снижение загрязнения окружающей среды и повышение энергоэффективности и ресурсосбережения, а также соответствующих технологических показателях были подготовлены и направлены для заполнения производителям меди специальные анкеты для предприятий. В качестве основы для формирования анкет использовался ПНСТ 232014 «Наилучшие доступные технологии. Формат описания технологий» и краткие описания НДТ, включенные в проект Справочника ЕС по НДТ.
Технологические показатели НДТ определялись на основе результатов обработки данных, представленных предприятиями при анкетировании и по специальным дополнительным запросам. Учитывалась также информация, содержащаяся в окончательном проекте второй редакции Справочника ЕС по НДТ для предприятий цветной металлургии, в отдельных научно-исследовательских работах, а также в других российских и зарубежных материалах, рассматривавшихся ТРГ 12.
Проведенный анализ представленных данных и информации позволил также сформулировать рекомендации относительно направлений дальнейшей работы над настоящим справочником НДТ и над процессом внедрения НДТ. К ним прежде всего относятся следующие:
-
1) Предприятиям — производителям никеля рекомендуется целенаправленно накапливать информацию об уровнях эмиссий маркерных веществ, потреблении сырья и энергоресурсов, проведении модернизации основного и природоохранного оборудования, а также экономических аспектах внедрения НДТ.
-
2) Для оценки экологических характеристик методов, интегрированных в производственные процессы, может оказаться полезным сбор конкретных данных и информации об используемом сырье, объемах производства и удельных характеристиках
-
3) Для уточнения технологических показателей по выбросам металлов и их соединений необходима подготовка описаний и сбор детальных данных по конкретным методам предупреждения и снижения выбросов этих веществ и по соответствующим им показателям.
-
4) При проведении модернизации технологического и природоохранного оборудования на предприятиях приоритетное внимание следует уделять повышению эффективности методов и технологий улавливания диоксида серы, вторичным и третичным методам улавливания неорганизованных выбросов неорганической пыли.
ОКПД 2 |
Наименование продукции по ОК 034—2014 (ОКПД) |
Наименование вида деятельности по ОКВЭД 2 |
ОКВЭД 2 |
Производство металлургическое |
24 | ||
Производство основных драгоценных металлов и прочих цветных металлов, производство ядер-ного топлива |
24.4 | ||
Производство прочих цветных металлов |
24.45 | ||
Производство никеля |
24.45.1 | ||
24.45.1 |
Никель необработанный; промежуточные продукты металлургии никеля | ||
24.45.11 |
Никель необработанный | ||
24.45.11.000 |
Никель необработанный | ||
24.45.12 |
Штейн никелевый, агломераты оксидов никеля и прочие промежуточные продукты металлургии никеля | ||
24.45.12.110 |
Штейн никелевый | ||
24.45.12.120 |
Агломераты оксидов никеля | ||
24.45.12.130 |
Продукты металлургии никеля промежуточные прочие | ||
Производство кобальта |
24.45.6 |
ОКПД 2 |
Наименование продукции по ОК 034—2014 (ОКПД) |
Наименование вида деятельности по ОКВЭД 2 |
ОКВЭД 2 |
24.45.30.150 |
Кобальт и изделия из него, сплавы на основе кобальта, порошки | ||
24.45.30.151 |
Кобальт необработан ный | ||
24.45.30.152 |
Штейн кобальтовый | ||
24.45.30.153 |
Порошки кобальтовые |
Для атмосферного воздуха |
Для водных объектов |
Азота оксид и азота диоксид (суммарно) |
As |
Взвешенные вещества |
Pb |
Никель, оксид никеля (в пересчете на никель) |
Zn |
Свинец и его соединения, кроме тетраэтилсвинца, в пересчете на свинец |
Ni |
Мышьяк и его соединения, кроме водорода мышьяковистого |
Co |
взвешенные вещества |
Технологический показатель |
Единица измерения |
Диапазон/ значение |
Выбросы пыли и металлов от пирометаллургических процессов производства никеля и кобальта ( НДТ 12) | ||
Никель, оксид никеля (в пересчете на никель) |
мг/нм3 |
< 180,0 |
Свинец и его соединения, кроме тетраэтилсвинца, в пересчете на свинец |
мг/нм3 |
< 7,0 |
Мышьяк и его соединения, кроме водорода мышьяковистого |
мг/нм3 |
< 2,5 |
Степень утилизации диоксида серы (НДТ 13) | ||
Степень утилизации диоксида серы |
% |
90 - 95 |
Выбросы оксидов азота от пирометаллургических процессов (НДТ 15) | ||
Азота оксид и азота диоксид (суммарно) |
мг/нм3 |
< 250 |
Средний уровень концентраций загрязняющих веществ в прямых сбросах, образующихся при производстве никеля и кобальта, в принимающие водные объекты (НДТ 19) | ||
As |
мг/л |
< 0,2 |
Pb |
мг/л |
< 1,0 |
Zn |
мг/л |
< 1,0 |
Ni |
мг/л |
< 2,5 |
Co |
мг/л |
< 0,5 |
взвешенные вещества |
мг/л |
< 50 |
pH |
ед. |
6 - 10 |
Номер НДТ |
Наименование НДТ |
НДТ 1 |
Повышение общей результативности природоохранной деятельности |
НДТ 2 |
Повышение эффективности использования энергии |
НДТ 3 |
Обеспечение стабильности производственного процесса |
НДТ 4 |
Сокращение расхода реагентов за счет внедрения новых процессов |
НДТ 5 |
Предотвращение или уменьшение неорганизованных выбросов пыли |
НДТ 6 |
Предотвращение или уменьшение неорганизованных эмиссий в воздух и водные объекты |
НДТ 7 |
Уменьшение неорганизованных выбросов, образующихся при хранении сырья |
НДТ 8 |
Уменьшение неорганизованных эмиссий, образующихся при обработке и транспортировке сырья |
НДТ 9 |
Предупреждение или уменьшение неорганизованных выбросов |
НДТ 10 |
Уменьшение неорганизованных выбросов при реализации гидрометаллургических процессов |
НДТ 11 |
Сокращение выбросов пыли и металлов |
НДТ 12 |
Сокращение выбросов пыли (взвешенных веществ) и металлов от пирометаллургических процессов |
НДТ 13 |
Снижение выбросов SO2 |
НДТ 14 |
Снижение выброса в воздух кислых газов от гидрометаллургических операций |
НДТ 15 |
Снижение выброса в воздух NOx от пирометаллургических процессов |
НДТ 16 |
Уменьшение неорганизованных сбросов в водные объекты |
НДТ 17 |
Предотвращение загрязнения почвы и подземных вод при эксплуатации хвостохранилищ |
НДТ 18 |
Предотвращение загрязнения почвы и подземных вод электролитом при производстве никеля и кобальта |
НДТ 19 |
Предотвращение образования сточных вод |
Номер НДТ |
Наименование НДТ |
НДТ 20 |
Очистка сточных вод, образующихся при производстве никеля и кобальта |
НДТ 21 |
Уменьшение количества отходов, направляемых на утилизацию при производстве никеля и кобальта |
Основной тенденцией современной металлургии в области переработки высокосернистых концентратов является применение автогенных процессов. К наиболее распространенным относится технология и печь взвешенной плавки, разработанная и внедренная в производство в конце 1940-х годов фирмой Outokumpu для плавки медных концентратов. Начиная с 1960-х годов этот процесс начал свое победоносное шествие по миру и на сегодняшний день реализован на многих предприятиях медной и никелевой подотраслей.
Г.2 Основные технологические процессы, связанные с использованием энергииВ автогенных процессах большая часть потребности в тепле удовлетворяется за счет окисления железа и серы, содержащихся в концентрате, в результате чего расходы топлива или электричестве малы. Производительность печей взвешенной плавки по сырью (в пересчете на сухой вес) обычно составляет 100-150 т/час. В печах Outotec содержание кислорода в реакционном газе меняется от 30-40 об. % до 70 об. %; печи Inco (завод Copper Cliff) работают на кислородном дутье.
Г.3 Уровни потребленияИнформация об уровнях потребления энергии для основных технологических процессов приведена в разделе 1 (таблицы 1.20 и 1.21) и разделе 2 (таблица 2.34).
Г.4 Наилучшие доступные технологии, направленные на повышение энергоэффективности и оптимизацию и сокращение ресурсопотребленияНДТ 2. Повышение эффективности использования энергии: использование комбинации двух или более методов, приведенных в таблице ниже.
№ |
Метод/оборудование |
Применимость |
1 |
Система управления энергоэффективностью (например, в соответствии с требованиями ГОСТ Р ИСО 50001 1) или ISO 50001 1)) |
Общеприменимо |
2 |
Оптимальное размещение взаимосвязанных производств, переделов и отдельного оборудования, обеспечивающее минимизацию материальных потоков |
Общеприменимо при новом строительстве, изменении конфигурации существующих производств или реконструкции |
3 |
Использование избыточного тепла (например, пара, горячей воды или горячего воздуха), образующегося при реализации основных процессов |
Применимо для пирометаллургических процессов |
4 |
Регенеративные дожигающие устройства |
Применимо, когда требуется очистка выбросов от горючих загрязняющих веществ |
5 |
Подача на горелки воздуха, обогащенного кислородом, или чистого кислорода для уменьшения потребления энергии |
Применимо для пирометаллургических процессов |
6 |
Низкотемпературная сушка концентратов и влажного сырья перед плавкой |
Общеприменимо |
7 |
Теплоизоляция объектов, функционирующих при высоких температурах, например трубопроводов пара и горячей воды |
Общеприменимо |
№ |
Метод/оборудование |
Применимость |
8 |
Использование высокоэффективных электродвигателей, оборудованных частотными преобразователями, для таких устройств, как, например, вентиляторы |
Общеприменимо |
9 |
Использование горячих технологических газов от процессов плавления для нагревания подаваемых компонентов |
Применимо для пирометаллургических процессов |
10 |
Применение автогенных процессов плавки сырья |
Применимо для пирометаллургических процессов |
11 |
Использование тепла химических реакций для поддержания теплового баланса гидрометаллургических процессов |
Применимо при реализации окислительных процессов, сопровождающихся выделением тепла |
1) Соответствие системы менеджмента указанным стандартам не означает ее обязательную сертификацию. |
НТД 4 Сокращение расхода реагентов за счет внедрения новых процессов (таблица 4.3).
№ |
Метод/оборудование |
Применимость |
1 |
Использование сульфата натрия или сульфата кальция в качестве флюсующих добавок для улучшения физикохимических свойств шлаков и снижения потерь цветных металлов |
Применимо для пирометаллургических процессов |
2 |
Замена гидролитического способа выделения кобальта из никелевого раствора безреагентным экстракционным |
Применимо для хлоридных сред рафинирования ПНТП или иных полупродуктов, после разработки негидролитического способа очистки от свинца и марганца |
3 |
Утилизация солевого стока дробной выпаркой с выделением товарного сульфата натрия и оборотного хлорида натрия и производство хлора электролизом последнего взамен использования привозного хлора |
Применимо для установок очистки сточных вод от хлоридного рафинирования ПНТП или иных полупродуктов |
№ |
Метод/оборудование |
Применимость |
4 |
Использование известково-серного отвара в качестве осадителя тяжелых цветных металлов |
Применимо в гидрометаллургических производствах, сопровождающихся образованием и выделением элементарной серы |
5 |
Применение фильтрации расплавленной элементарной серы взамен автоклавной выплавки |
Применимо для гидрометаллургических процессов, сопровождающихся образованием элементарной серы при необходимости ее выделения |
Совершенствование действующих и создание новых способов производства никеля определяется существующим уровнем техники и требует значительных инвестиций, часто сопряженных с высокими рисками. При прочих равных условиях основные критерии успешной производственной деятельности имеют исключительно экономическую основу. Эти критерии, в свою очередь, являются интегральными характеристиками совокупности различных, обычно разнонаправленных технологических факторов, в том числе и факторов ресурсо- и энергоэффективности, а также экологической безопасности производства.
Собственный экономический потенциал природоохранных мероприятий, таких как, например, внедрение малоотходных технологий, производство побочной продукции и (или) полезное использование образующихся в основном производственном процессе отходов, в российских условиях следует признать скорее незначительным. С одной стороны , природоохранные технологии во многих случаях характеризуются высокой энергоемкостью, а поддержание оборудования в функциональном состоянии требует регулярных затрат на расходные материалы и комплектующие и иных эксплуатационных затрат; в некоторых случаях при производстве побочной продукции, такой, например, как серная кислота, значительные издержки могут возникать и в связи с необходимостью хранения и транспортировки агрессивного вещества. С другой стороны, низкая емкость российских рынков и территориальная удаленность от них никелевых предприятий не обеспечивают вывод «побочных» производств на экономически эффективный уровень и не смогут гарантировать устойчивое потребление продукции вновь вводимых производственных мощностей, а потенциал выхода на внешние рынки ограничен и малоперспективен с экономической точки зрения.
Таким образом, наибольшим потенциалом с точки зрения возмещения затрат, понесенных в связи с внедрением на предприятии новых природоохранных методов и технологий, обладают комплексные меры, увязывающие экологическую модернизацию производства с перенастройкой производственного процесса в целом, оптимизацией отдельных его звеньев и расширением номенклатуры выпускаемой продукции, в том числе с высокой добавленной стоимостью.
Можно выделить следующие перспективные технологии, направленные на повышение энергоэффективности и оптимизацию и сокращение ресурсопотребления:
- технология двухзонной печи Ванюкова ;
- усовершенствование технологии гидрометаллургического обогащения бедного никель-пирротинового концентрата;
- производство никеля электроэкстракцией рафинированием ПНТП;
- производство никеля электроэкстракцией растворов выщелачивания никелевого концентрата от разделения файнштейна;
- технология производства карбонильного никеля с использованием синтеза среднего давления.
Библиография-
1. № 7-ФЗ
-
2. ПНСТ 21—2014 Наилучшие доступные технологии. Структура информационно-технического справочника
-
3. ПНСТ 23—2014 Наилучшие доступные технологии. Формат описания технологий
-
4. ПНСТ 22—2014 Наилучшие доступные технологии. Термины и определения
-
5. Wood Mackenzie Ltd. Global Nickel Long-term Outlook Q1 2016, March 2016.
-
6. International Nickel Study Group. INSG October 2015 Meetings, Press Release, Lisbon, 7 October 2015.
-
7. Wood Mackenzie Ltd. Global Nickel Long-term Outlook Q1 2015, March 2015.
-
8. Cobalt Development Institute. Cobalt News, April 2016 , 16/2, 11 pp.
-
9. US Geological Survey. Mineral Commodities Summaries: Nickel, January 2016, 2 pp.
-
10. U. S. Geological Survey, MINERAL COMMODITY SUMMARIES 2016. 2016, 202 рр.
-
11. US Geological Survey. Mineral Commodities Summaries: Cobalt, January 2016, 2 pp.
-
12. Vale Inco Ltd. External Audit of Mineral Reserves, vol. 2, sections 1-6, 2010, 375 pp.
-
13. Blue Cube Quarterly. Nickel Processing at BCL in Botswana, 2016, First Edition, pp 3-4.
-
14. Glencore. Resources and Reserves as at 31 December 2015 Report, 63 pp.
-
15. Wardel Armstrong. NI 43-101 Technical Report on the Eagle Mine, Jily 2013, 275 pp.
-
16. BHP Billiton. Annual Report 2015, 324 pp.
-
17. Coffey Mining. Santa Rita Project, Brasil — Technical Report, 22nd March, 2011, 117 pp.
-
18. ПАО ГМК «Норильский никель». Годовой отчет 2014 г.
-
19. South32. Annual Report 2015, 240 pp.
-
20. Sherritt International. 2015 Annual Information Form, March 21, 2016, 108 pp.
-
21. Nickel Asia Corporation. Analysts Presentation, May 2015, 27 pp.
-
22. Состояние МСБ никеля Российской Федерации на 1 января 2012 г.
-
23. Методические рекомендации по применению Классификации запасов месторождений и прогнозных ресурсов твердых полезных ископаемых. Никелевые и кобальтовые руды. ФГУ ГКЗ, Москва, 2007 г.
-
24. F. Crundwell, M. Moats et al. Extractive Metallurgy of Nickel, Cobalt and PlatinumGroup Metals. Elsevier, 2011, 609 pp.
-
25. US Geological Survey. 2013 Minerals Yearbook: Cobalt, October 2015, 20 pp.
-
26. M.Elias (CSA Global). Nickel Laterites in SE Asia. Presentation at ‘Bali 2013' (East Asia: Geology, Exploration Technologies and Mines), May 27, 2013, 48 pp.
-
27. A.Warner, C.Diaz et al. World Nonferrous Smelter Survey Part IV: Nickel Sulfide. Journal of Metals, April 2007, pp 58-72.
-
28. The Journal of The South African Institute of Mining and Metallurgy, Vol. 106, 03.2008.
-
29. Samuel Engineering. Preliminary Economic Assessment NI 43-101 technical Report — Idaho Cobalt Project, April 29, 2015, 230 pp.
-
30. R. T. Jones, T. R. Curr (Mintek). Pyrometallurgy at mintek. Southern African Pyrometallurgy 2006, March 2006, pp. 127-150.
-
31. Golder Associates. An Independent Technical Report on the Material Assets of Katanga Mining Ltd, March 31, 2011, 340 pp.
-
32. Состояние МСБ никеля Российской Федерации на 1 января 2012 г.
-
33. Состояние МСБ никеля Российской Федерации на 1 января 2015 г.
-
34. Производство металлов за полярным кругом. Технологическое пособие. — под ред. Н. Г. Кайтмазова. — Норильск:Антей лимитед, 2007.
-
35. Резник И. Д., Ермаков Г. П., Шнеерсон Я. М. Никель: в 3 т. — М. : ООО «Наука и технологии», 2000. — 384 с.
-
36. Федеральный закон «Об охране окружающей среды» № 7-ФЗ.
-
37. А. Н. Федоров, А. А. Комков, В. Н. Бруэк и др. Освоение процесса Ванюкова для переработки окисленных никелевых руд на Южно-уральском никелевом комбинате // Цветные металлы. 2007. № 12. С. 33-37.
-
38. В. И. Костин. Опыт работы печи Ванюкова на ОАО «Комбинат Южуралникель» // Цветные металлы. 2008. № 11. С. 45-48.
-
39. M. V. Knyazev, A. G. Ryabko, L. B. Tsymbulov at all. Two-Zone Vaniukov Furnace: New Potential Copper and Nickel Production // Proc. of the Sohn International Symposium, San Diego, USA, August 27-31, 2006, Vol. 8, P. 327-334.
-
40. L. B. Tsymbulov, M. V. Knyazev, L.Sh. Tsemekhman at all. Pilot testing of a process treatment of Ni-containing copper concentrate after high-grade matte separation resulting in blister copper production in two-zone Vaniukov furnace // Proceedings of the sixth international Copper-Cobre Conference, The Carlos Diaz Symposium on Pyrometallurgy, Toronto, Ontario, Canada, August 25- 30, 2007, Vol. III (Bookl), P. 397-409.
-
41. Л. Б. Цымбулов, М. В. Князев, Л. Ш. Цемехман и др. Опытно-промышленные испытания технологии брикетированного медно-никелевого концентрата в двухзонной печи Ванюкова // Цветные металлы — 2008. — № 6. — С. 30-36.
194
Виды продукции: ЛК — ломаные катоды; РК — резаные катоды; ПГ — «пуговицы»; СЛ — слитки.
Регистрация на ЛБМ не продлена.
Следует отметить, что оценки USGS по добыче кобальта в разных странах не отличаются единообразным подходом. Так, например, «горная» добыча кобальта в Австралии включает содержание кобальта в латеритовой никелевой руде плюс содержание кобальта в никелевых концентратах; по Канаде, России — это оценка содержания кобальта в концентратах от переработки медно-никелевых сульфидных руд; по Кубе — это вообще расчетное значение, полученное на основе сообщенных данных по содержанию кобальта в произведенных никелькобальтовых смешанных сульфидах и оценки содержания кобальта в аммиачном растворе выщелачивания и т. д. ([25]).
Как будет показано ниже, получаемый при гидрометаллургическом обогащении на этом производстве продукт также перерабатывается до файнштейна.
На заводе Ravensthorpe используется сочетание высокотемпературного автоклавного сернокислотного выщелачивания с атмосферным, а на MurrinMurrin — с кучным выщелачиванием.
По данным на 2016 год, на единственном никельрафинировочном предприятии России — комбинате Североникель АО «Кольская ГМК» до сих пор используется устаревшая технологическая схема получения катодного никеля методом электрорафинирования металлических анодов, однако от этой технологии в настоящее время отказываются, постепенно переходя на технологию хлорного выщелачивания никелевого порошка трубчатых печей с получением никеля электроэкстракцией.
В середине ХХ века никельсодержащий пирротиновый концентрат месторождений Sudbery (Канада) также перерабатывали. Его обжигали, восстанавливали и выщелачивали аммиачными растворами для извлечения никеля. Полученный кек направлялся на пирометаллургическую переработку с получением гематитовых окатышей для черной металлургии.
После закрытия Никелевого завода в Норильске в 2016 году в России и никелевого завода Томпсон в Канаде в 2018 г. в эксплуатации останутся только два никелевых плавильных завода (Печенганикель компании «Норильский никель» и завод в г. Садбери компании Glencore), работающие по этой технологии. Заметим, что в январе 2016 года Glencore получила отсрочку на 10 лет для своего плавильного завода по части выполнения новых стандартов Канады по выбросам в атмосферу.
Следует отметь, что в таблице приведено содержание цветных металлов в шлаке после флотации. Однако утверждение не теряет силы, поскольку при флотации шлаков содержание драгоценных и цветных металлов снижается почти пропорционально, всего примерно в два раза.
На медных заводах эксплуатируется 44 печи.
См . [34], [35]
МИНИСТЕРСТВО ПРОМЫШЛЕННОСТИ И ТОРГОВЛИ РОССИЙСКОЙ ФЕДЕРАЦИИ
ФЕДЕРАЛЬНОЕ АГЕНТСТВО ПО ТЕХНИЧЕСКОМУ РЕГУЛИРОВАНИЮ И МЕТРОЛОГИИ (Госстандарт)
ПРИКАЗ
1890
15 декабря 2016 г.
Москва
Об утверждении информационно-технического справочника по наилучшим доступным технологиям «Производство никеля и кобальта»
В соответствии с постановлением Правительства Российской Федерации от 23 декабря 2014 г. № 1458 «О порядке определения технологии в качестве наилучшей доступной технологии, а также разработки, актуализации и опубликования информационно-технических справочников по наилучшим доступным технологиям» приказываю:
-
1. Утвердить для добровольного применения информационнотехнический справочник по наилучшим доступным технологиям ИТС 12-2016 «Производство никеля и кобальта» с датой введения в действие 1 июля 2017 г.
Введен впервые.
-
2. Закрепить утвержденный информационно-технический справочник по наилучшим доступным технологиям ИТС 12-2016 «Производство никеля и кобальта» за Управлением технического регулирования и стандартизации.
-
3. Управлению технического регулирования и стандартизации обеспечить опубликование информационно-технического справочника по наилучшим доступным технологиям ИТС 12-2016 «Производство никеля и кобальта» на официальном сайте Федерального агентства по техническому регулированию и метрологии в информационно-телекоммуникационной сети «Интернет».
Руководитель
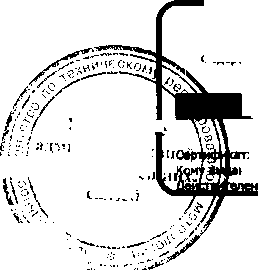
: 146337FB000300019EF1 н: Абрамов Алексей Владимирович
Подлинник электронного документа, подписанного ЭП, хранится о системе электронного документооборота Федеральное агентство по техническому регулированию и метрологии.
А.В. Абрамов
VnpHR.K'HF
■ ИФНКЛ ■ ! Ji I
ЯГ?
т? и
V"! р LUO J (I